- お役立ち記事
- Emergency response manual for purchasing departments to reduce material supply risks
Emergency response manual for purchasing departments to reduce material supply risks
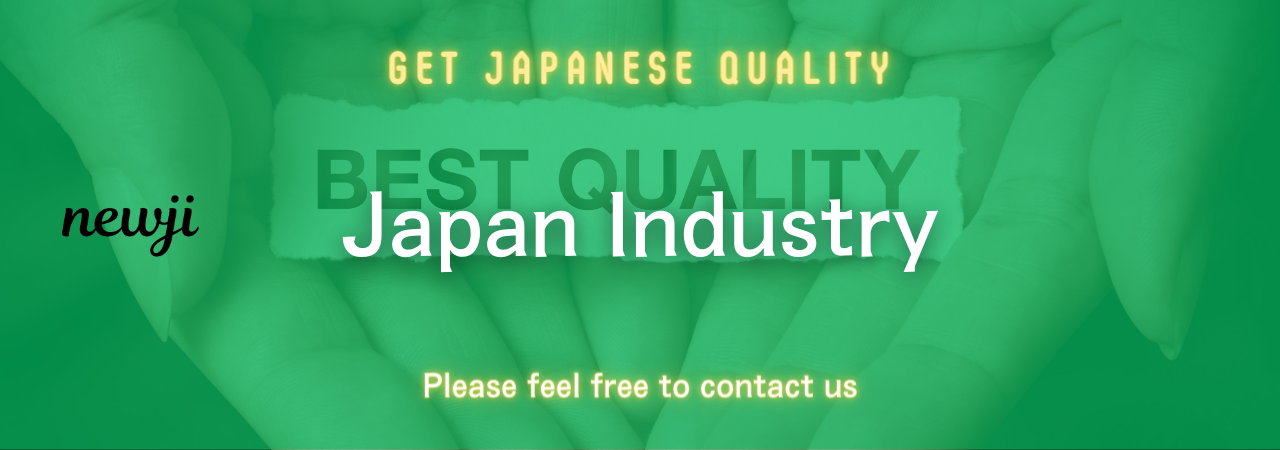
目次
Understanding Material Supply Risks
In today’s fast-paced business environment, supply chain challenges are an inevitable occurrence that can impact the purchasing department significantly.
Material supply risks can arise from several sources, such as natural disasters, geopolitical issues, transportation disruptions, and supplier inefficiencies.
These risks can lead to increased costs, production delays, or even a full halt in manufacturing.
It is crucial for purchasing departments to anticipate these potential threats and have a robust emergency response plan in place to mitigate risks associated with material supply.
Proactively managing these situations can keep your business operations running smoothly and ensure long-term success.
Identifying Potential Supply Chain Risks
To effectively reduce material supply risks, it is important, first and foremost, to identify and understand the various risks that your business might face.
Supplier Risks
The purchasing department relies heavily on suppliers for materials.
Therefore, it is essential to assess the reliability and stability of these suppliers.
Supplier risks can include poor financial health, low quality of products, or sudden shutdowns.
To mitigate these risks, companies should diversify their supplier base and establish solid relationships with multiple vendors.
Economic and Environmental Risks
Economic factors such as inflation, currency fluctuations, and trade restrictions greatly affect material costs and availability.
Additionally, environmental risks like natural disasters or climate change can disrupt supply routes and availability.
Purchasing departments need to stay informed about global economic trends and environmental changes to anticipate any impacts on material sourcing.
Logistical Risks
Logistical challenges can stem from transportation issues, such as damaged infrastructure, labor strikes, or political instability in transit regions.
Companies should work with reliable logistics service providers and continuously monitor transport channels to preemptively address any disruptions.
Developing an Emergency Response Plan
Having identified the potential risks, the next crucial step is creating a comprehensive emergency response plan for the purchasing department.
Risk Assessment and Prioritization
Begin by evaluating the likelihood and potential impact of each identified risk.
Prioritize the risks based on their severity and likelihood of occurrence.
This structured approach helps in allocating resources effectively to areas that need immediate attention.
Supplier Diversification
Establish relationships with multiple suppliers for each essential material.
This strategy, known as supplier diversification, ensures that you have alternate sources ready in case any single supplier runs into issues.
Regularly assess and update your supplier list and develop contingency contracts to enable quick shifts in the supplier network.
Inventory Management
Adopt proactive inventory management practices to mitigate material shortages.
Implement safety stock levels for essential materials to cushion against potential disruptions.
Using advanced inventory management tools can facilitate accurate forecasting and help maintain an optimal balance between supply and demand.
Implementing Real-Time Monitoring Systems
Utilizing technology to keep track of supply chain activities can significantly reduce material supply risks.
Supply Chain Visibility Tools
Invest in supply chain visibility tools that provide real-time data tracking.
These tools allow purchasing departments to monitor the status and movement of materials through the supply chain.
Real-time alerts and notifications can help quickly identify any disruptions and enable prompt remedial actions.
Predictive Analytics
Embrace predictive analytics to anticipate potential supply chain disruptions before they occur.
By analyzing historical data and current market trends, predictive analytics can provide valuable insights and forecasts.
This information assists in making timely decisions and adjusting procurement strategies accordingly.
Strengthening Supplier Relationships
Building strong relationships with suppliers is vital in reducing material supply risks.
Regular Communication
Maintain open lines of communication with your suppliers.
Regular meetings and updates can help identify potential supplier issues early and foster a collaborative approach to problem-solving.
Transparency and trust are key elements in maintaining successful supplier partnerships.
Joint Risk Management
Work together with suppliers to identify and mitigate risks that may impact both parties.
This could involve joint planning sessions, shared risk assessments, and collaborative efforts to address potential problems.
Partnering in risk management creates a sense of shared responsibility and strengthens the overall supply chain.
Conclusion
An emergency response manual for purchasing departments is an essential tool in reducing material supply risks.
By understanding and identifying potential risks and developing a thorough response plan, purchasing departments can significantly mitigate the impact of disruptions.
Prioritizing supplier diversification, inventory management, and advanced monitoring systems will enhance operational readiness and resilience.
Strong supplier relationships and regular communication further fortify the supply chain against unforeseen challenges.
Incorporating these strategies into your emergency response manual will ensure your purchasing department is well-prepared to navigate through material supply risks effectively.
With these measures in place, your business can maintain stable operations regardless of external disruptions.
資料ダウンロード
QCD調達購買管理クラウド「newji」は、調達購買部門で必要なQCD管理全てを備えた、現場特化型兼クラウド型の今世紀最高の購買管理システムとなります。
ユーザー登録
調達購買業務の効率化だけでなく、システムを導入することで、コスト削減や製品・資材のステータス可視化のほか、属人化していた購買情報の共有化による内部不正防止や統制にも役立ちます。
NEWJI DX
製造業に特化したデジタルトランスフォーメーション(DX)の実現を目指す請負開発型のコンサルティングサービスです。AI、iPaaS、および先端の技術を駆使して、製造プロセスの効率化、業務効率化、チームワーク強化、コスト削減、品質向上を実現します。このサービスは、製造業の課題を深く理解し、それに対する最適なデジタルソリューションを提供することで、企業が持続的な成長とイノベーションを達成できるようサポートします。
オンライン講座
製造業、主に購買・調達部門にお勤めの方々に向けた情報を配信しております。
新任の方やベテランの方、管理職を対象とした幅広いコンテンツをご用意しております。
お問い合わせ
コストダウンが利益に直結する術だと理解していても、なかなか前に進めることができない状況。そんな時は、newjiのコストダウン自動化機能で大きく利益貢献しよう!
(Β版非公開)