- お役立ち記事
- Lead time reduction methods that the purchasing department should adjust for short delivery projects
Lead time reduction methods that the purchasing department should adjust for short delivery projects
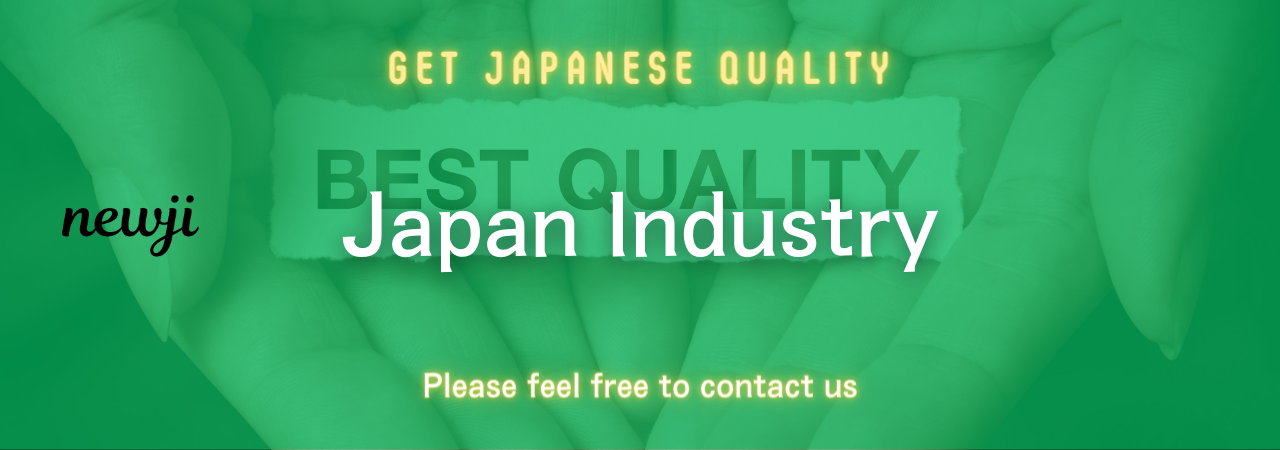
目次
Understanding Lead Time Reduction
The term “lead time” refers to the period between the initiation of a project order and its completion or delivery.
In the context of purchasing departments, reducing lead time is crucial for efficiently managing short delivery projects.
When companies maintain lower lead times, they can respond more rapidly to market demands, adjust to unforeseen changes, and enhance customer satisfaction.
Shortening lead times requires strategic planning and adjusting various processes within the purchasing cycle.
By focusing on key elements such as supplier relations, inventory control, and process optimization, companies can effectively reduce lead times and improve overall efficiency.
Why Lead Time Reduction Matters
Reducing lead times in purchasing is essential for several reasons.
First, it allows companies to become more agile, enabling faster responses to customer orders and market changes.
This agility can become a significant competitive advantage, allowing a business to capture new opportunities more swiftly than its competitors.
Second, minimizing lead times increases efficiency and reduces costs.
When lead times are lengthy, it often results in excess inventory, warehousing costs, and may also include a higher risk of obsolescence.
Streamlining processes and reducing lead times can alleviate these issues, leading to better resource management and cost-effective operations.
Lastly, shortened lead times directly impact customer satisfaction.
When businesses can deliver products faster and more efficiently, customers are likely to return for more purchases and recommend the brand to others.
Therefore, focusing on lead time reduction can yield significant benefits for the purchasing department and the business as a whole.
Methods for Reducing Lead Times
Purchasing departments aiming to reduce lead times must consider various strategies.
Below are key methods that have proven effective in achieving this goal:
1. Strengthen Supplier Relationships
Building and maintaining strong relationships with suppliers is paramount to reducing lead times.
Collaborative relationships can enhance communication, ensure better negotiation terms, and result in faster deliveries.
Actively engage suppliers to discuss lead time requirements, and consider entering strategic partnerships or long-term contracts to foster loyalty and mutual benefit.
2. Diversify Supplier Base
Relying on a single supplier can create bottlenecks and delays.
To mitigate this risk, consider diversifying the supplier base.
Having multiple suppliers for a single product or component allows flexibility in sourcing and ensures that purchasing departments are not caught off guard if one supplier fails to meet delivery deadlines.
3. Implement Inventory Management Techniques
Effective inventory management is integral to reducing lead times.
Techniques such as Just-In-Time (JIT) inventory can help decrease storage costs and improve cash flow.
Additionally, using inventory management software can optimize stock levels, predict demand more accurately, and automate reordering processes to prevent stockouts or overstock situations.
4. Optimize Order Processing
Streamlining internal order processing is critical to reducing lead times.
Evaluate current purchasing procedures and identify bottlenecks or inefficiencies.
Implement automated systems to handle routine tasks such as order placements and invoicing, freeing up staff to focus on more strategic activities.
Regularly review and adjust processes to ensure continuous improvement.
5. Improve Demand Forecasting
Accurate demand forecasting is vital for reducing lead times.
Using advanced analytics and historical data, businesses can predict product demand and adjust their procurement plans accordingly.
Improved forecasting allows purchasing departments to anticipate needs, reduce emergency orders, and maintain optimal stock levels.
Challenges in Reducing Lead Times
Despite the benefits, lead time reduction can present challenges that need careful consideration.
One common challenge is supplier resistance to change.
Suppliers who are used to traditional processes may be reluctant to adapt to new technologies or expedite deliveries frequently.
To overcome this, purchasing departments must employ effective change management strategies and incentives to encourage supplier cooperation.
Another challenge is the high investment required for technology solutions.
Automation and advanced inventory management systems can be costly, and not all organizations might have the budget to implement them immediately.
However, it’s usually beneficial in the long term, so departments should consider phased implementations or explore software-as-a-service (SaaS) options to mitigate initial costs.
Lastly, internal opposition to change can hinder lead time reduction efforts.
Staff may resist adopting new processes or using new technology if they believe existing methods are sufficient.
To address this, provide thorough training and communicate the benefits of lead time reduction to staff to gain their support and involvement.
Conclusion
Reducing lead times in purchasing departments is not only beneficial for meeting short delivery project requirements, but it’s also a strategic advantage for businesses.
By fostering strong supplier relationships, optimizing inventory management, improving demand forecasting, and utilizing technology, organizations can significantly reduce lead times.
While challenges exist, addressing them with targeted strategies and clear communication can help in making lead time reduction a reality.
In turn, businesses can enjoy increased efficiency, reduced costs, and enhanced customer satisfaction—ultimately leading to sustained success in a competitive market.
資料ダウンロード
QCD調達購買管理クラウド「newji」は、調達購買部門で必要なQCD管理全てを備えた、現場特化型兼クラウド型の今世紀最高の購買管理システムとなります。
ユーザー登録
調達購買業務の効率化だけでなく、システムを導入することで、コスト削減や製品・資材のステータス可視化のほか、属人化していた購買情報の共有化による内部不正防止や統制にも役立ちます。
NEWJI DX
製造業に特化したデジタルトランスフォーメーション(DX)の実現を目指す請負開発型のコンサルティングサービスです。AI、iPaaS、および先端の技術を駆使して、製造プロセスの効率化、業務効率化、チームワーク強化、コスト削減、品質向上を実現します。このサービスは、製造業の課題を深く理解し、それに対する最適なデジタルソリューションを提供することで、企業が持続的な成長とイノベーションを達成できるようサポートします。
オンライン講座
製造業、主に購買・調達部門にお勤めの方々に向けた情報を配信しております。
新任の方やベテランの方、管理職を対象とした幅広いコンテンツをご用意しております。
お問い合わせ
コストダウンが利益に直結する術だと理解していても、なかなか前に進めることができない状況。そんな時は、newjiのコストダウン自動化機能で大きく利益貢献しよう!
(Β版非公開)