- お役立ち記事
- New materials traceability tool for purchasing departments to consider implementing
New materials traceability tool for purchasing departments to consider implementing
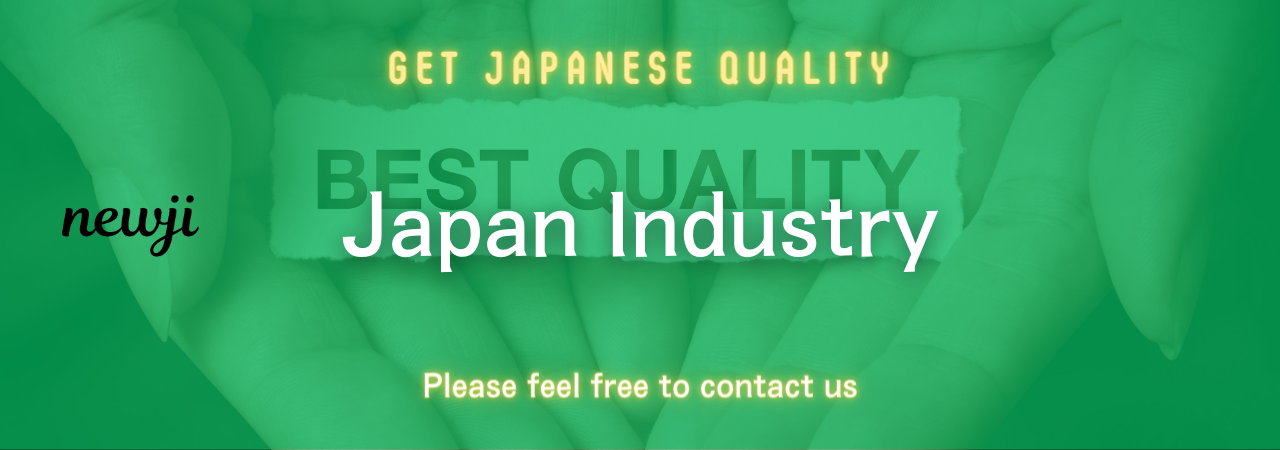
目次
Understanding Materials Traceability
Materials traceability is becoming an increasingly important aspect for businesses, especially those involved in manufacturing, construction, and other industries where quality and compliance are critical.
Traceability refers to the ability to track every piece of material or component through every stage of production and supply chain, from its origin to its final destination.
For purchasing departments, effective traceability means having the capacity to access detailed information about the materials that they acquire.
This can include information on the source of the materials, the processes they have undergone, and their compliance status with relevant standards and regulations.
Implementing a robust traceability tool can greatly benefit a purchasing department.
This article explores why traceability is crucial and how a new materials traceability tool can enhance efficiency, compliance, and transparency in procurement processes.
The Importance of Materials Traceability for Purchasing Departments
One of the primary advantages of having a solid materials traceability system is ensuring product quality and safety.
By being able to trace materials back to their source, purchasing departments can ensure that they are obtaining the highest-quality components.
This reduces the risk of defects and non-compliance, which can lead to costly recalls or legal issues.
Traceability also plays a significant role in sustainability and ethical sourcing.
With growing environmental concerns and increasing pressure on companies to be transparent about their supply chains, a strong traceability tool helps in verifying that suppliers adhere to sustainable practices.
This commitment not only enhances the company’s image but also aligns it with global sustainability goals.
Moreover, in highly regulated industries such as pharmaceuticals, aerospace, and food, traceability is not just advantageous—it is a necessity.
Regulatory bodies require stringent documentation to verify the quality and origin of materials.
A materials traceability tool provides the necessary documentation, ensuring compliance with all regulations and avoiding potential penalties.
Challenges in Implementing Materials Traceability
Despite its benefits, there are challenges associated with implementing a materials traceability tool.
One major hurdle is the complexity of supply chains.
With multiple suppliers, each having their own network of sub-suppliers, it can be difficult to maintain a clear line of sight on all materials.
Data management is another challenge.
Effective traceability requires accurate, up-to-date information, which means data collection and management systems must be robust and reliable.
Purchasing departments need to ensure that data is consistently and accurately recorded at each stage of the supply chain.
Furthermore, there is often resistance to change within organizations.
Employees accustomed to traditional procurement processes may be hesitant to adopt new systems and practices.
To overcome this, companies must invest in training and change management strategies to ensure a smooth transition.
Features to Look for in a Materials Traceability Tool
When selecting a materials traceability tool, it is crucial to look for features that will cater to the specific needs of the purchasing department.
Automation capabilities are key.
A tool that can automate data collection and analysis reduces the time and effort required for manual tracking, allowing staff to focus on more strategic tasks.
Integration is another important feature.
The traceability tool should seamlessly integrate with existing systems such as ERP and inventory management software.
This ensures a smooth flow of information across different departments and improves overall efficiency.
Additionally, the tool should provide comprehensive reporting capabilities.
Purchasing departments must be able to generate detailed reports that demonstrate compliance, track the flow of materials, and identify potential issues or bottlenecks in the supply chain.
User-friendliness cannot be overlooked.
A traceability tool should be intuitive and easy to use so that all team members can quickly adapt to it without a steep learning curve.
Steps to Implement a Materials Traceability Tool
Implementing a new traceability tool involves several key steps to ensure success.
Firstly, it is essential to set clear objectives.
The purchasing department should determine what they aim to achieve with the new tool, whether it’s enhancing quality assurance, ensuring compliance, or improving supply chain transparency.
Next, evaluating different traceability tools is crucial.
Purchasing departments should consider the features, scalability, and compatibility of the tool with their existing systems.
Vendor reputation and after-sales support are also important factors to consider.
Once a tool is selected, the next step is customization.
The traceability system should be tailored to meet the specific needs and processes of the company.
This may involve configuring the software, setting up user access levels, and defining workflows.
Training is a critical component of the implementation process.
All users should be adequately trained to ensure they are comfortable using the new system.
Ongoing support and refresher courses can help maintain proficiency and address any challenges that arise over time.
Finally, monitoring and optimization should not be overlooked.
Once the tool is in place, the purchasing department should continuously monitor its performance and make necessary adjustments.
Feedback from users can provide valuable insights into areas for improvement.
Conclusion
A materials traceability tool is an invaluable asset for purchasing departments committed to maintaining high standards of quality, compliance, and sustainability.
While there are challenges associated with its implementation, the benefits far outweigh the difficulties.
By carefully selecting and strategically implementing a traceability tool, purchasing departments can enhance their operations, reduce risks, and contribute to the overall success of their organizations.
資料ダウンロード
QCD調達購買管理クラウド「newji」は、調達購買部門で必要なQCD管理全てを備えた、現場特化型兼クラウド型の今世紀最高の購買管理システムとなります。
ユーザー登録
調達購買業務の効率化だけでなく、システムを導入することで、コスト削減や製品・資材のステータス可視化のほか、属人化していた購買情報の共有化による内部不正防止や統制にも役立ちます。
NEWJI DX
製造業に特化したデジタルトランスフォーメーション(DX)の実現を目指す請負開発型のコンサルティングサービスです。AI、iPaaS、および先端の技術を駆使して、製造プロセスの効率化、業務効率化、チームワーク強化、コスト削減、品質向上を実現します。このサービスは、製造業の課題を深く理解し、それに対する最適なデジタルソリューションを提供することで、企業が持続的な成長とイノベーションを達成できるようサポートします。
オンライン講座
製造業、主に購買・調達部門にお勤めの方々に向けた情報を配信しております。
新任の方やベテランの方、管理職を対象とした幅広いコンテンツをご用意しております。
お問い合わせ
コストダウンが利益に直結する術だと理解していても、なかなか前に進めることができない状況。そんな時は、newjiのコストダウン自動化機能で大きく利益貢献しよう!
(Β版非公開)