- お役立ち記事
- Examples of distributed procurement risks that purchasing departments should avoid in multi-location procurement
Examples of distributed procurement risks that purchasing departments should avoid in multi-location procurement
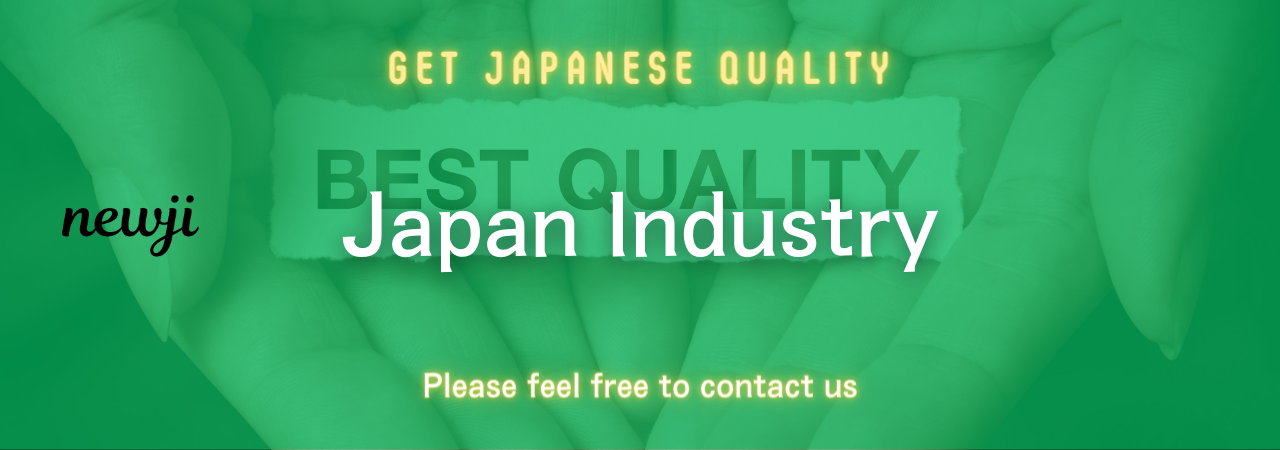
目次
Understanding Distributed Procurement Risks
In the intricate world of procurement, the move toward distributed or multi-location procurement is becoming increasingly common.
This strategy allows companies to source materials from various locations, enhancing their ability to manage supply chains more effectively.
However, this approach comes with its own set of risks that the purchasing department should be vigilant about.
Understanding these risks is crucial for any organization looking to optimize their procurement processes while avoiding potential pitfalls.
Communication Barriers
One of the most significant challenges in multi-location procurement is overcoming communication barriers.
Different regions may speak various languages and have different cultural norms that can impede effective communication.
This can lead to misunderstandings, errors, and even delays in procurement processes.
Purchasing departments must ensure that clear channels of communication are established and that teams are equipped with the necessary tools to bridge these barriers.
Utilizing professional translators or language training can help in mitigating this risk effectively.
The Role of Technology
Leveraging technology is a game-changer in addressing communication issues.
Tools such as cloud-based platforms and real-time messaging apps can facilitate better communication between teams spread across different locations.
Having a centralized platform where all procurement activities and communications are logged can help in eliminating the confusion and keeping everyone informed.
Moreover, technology can help in monitoring procurement processes to ensure timely updates and identify any potential delays.
Supply Chain Disruptions
With suppliers spread across multiple locations, the risk of supply chain disruptions increases.
Natural disasters, political unrest, or economic fluctuations in one location can severely impact the entire procurement chain.
Purchasing departments must develop contingency plans and maintain flexibility to adapt to unforeseen changes.
Diversifying suppliers and locations can mitigate the impact of these disruptions and provide the department with alternative options.
Building Strong Supplier Relationships
Forming strong relationships with suppliers is vital in mitigating supply chain risks.
Regular communication and negotiating favorable terms can create loyalty and stability.
It’s essential to understand each supplier’s capacity and reliability and to have backup suppliers to turn to if necessary.
Moreover, keeping abreast of the political and economic climate in supplier regions can provide early warnings of potential issues.
Logistical Challenges
Transporting goods across multiple locations comes with its logistical challenges.
Shipping delays, customs issues, and unexpected costs can arise, disrupting the supply timeline.
To navigate these hurdles, purchasing departments must have a robust logistics plan in place.
This includes understanding international shipping laws, tariffs, and ensuring compliance with all regulations.
Optimizing Transportation Routes
Efficiently optimizing transportation routes can reduce shipping times and costs.
Utilizing logistics software that offers route optimization and tracking features can manage shipments more efficiently.
Additionally, working closely with logistics providers to understand the best practices and current trends in transportation can significantly alleviate logistical challenges.
Collaborating with experienced third-party logistics companies can also offer valuable insights and solutions.
Quality Control Issues
Ensuring consistent product quality across different locations can be daunting.
With varying manufacturing standards and practices, the risk of receiving materials that don’t meet quality expectations increases.
This can lead to wasted resources, increased costs, and delay in production schedules.
Implementing Stringent Quality Checks
A robust system for monitoring and maintaining quality standards at every stage of procurement is essential.
Purchasing departments should implement stringent quality checks and audits across different suppliers.
This can involve setting clear quality benchmarks, conducting regular inspections, and using quality management software to track compliance.
Supplier vetting and performance monitoring can also ensure that only the most reliable suppliers are engaged.
Legal and Regulatory Compliance
Different regions have varying legal requirements and regulations that must be adhered to in procurement activities.
Non-compliance can lead to legal penalties and operational disruptions.
Purchasing departments must ensure that they fully understand the laws and regulations in each location they operate.
This includes labor laws, environmental regulations, and trade restrictions.
Engaging Legal Experts
Hiring legal experts with knowledge of international trade law can ensure that all procurement activities comply with local and international regulations.
Regular training for the purchasing team on regulatory compliance can also be beneficial.
Keeping documentation up to date and maintaining transparency in all procurement activities will help avoid legal pitfalls.
Cost Management Challenges
Multi-location procurement often results in inflated costs due to shipping, duties, and currency fluctuations.
Effective cost management strategies are vital to maintain profitability.
Purchasing departments must ensure that their budgeting includes all possible overheads related to distributed procurement.
Negotiating Better Terms
Negotiating better payment terms and volume discounts with suppliers can help reduce costs.
Every contract should be carefully reviewed to ensure no hidden costs are overlooked.
Moreover, using technology to track expenses and budget accurately will provide clearer visibility into potential cost overruns and savings opportunities.
Conclusion
In the landscape of multi-location procurement, recognizing and managing these risks is critical for purchasing departments.
By implementing effective communication strategies, planning for supply chain disruptions, optimizing logistics, ensuring quality control, maintaining compliance, and managing costs, organizations can mitigate the risks associated with distributed procurement.
Staying vigilant and adaptable will enable purchasing departments to thrive, leveraging the benefits of a decentralized approach to procurement while avoiding common pitfalls.
資料ダウンロード
QCD調達購買管理クラウド「newji」は、調達購買部門で必要なQCD管理全てを備えた、現場特化型兼クラウド型の今世紀最高の購買管理システムとなります。
ユーザー登録
調達購買業務の効率化だけでなく、システムを導入することで、コスト削減や製品・資材のステータス可視化のほか、属人化していた購買情報の共有化による内部不正防止や統制にも役立ちます。
NEWJI DX
製造業に特化したデジタルトランスフォーメーション(DX)の実現を目指す請負開発型のコンサルティングサービスです。AI、iPaaS、および先端の技術を駆使して、製造プロセスの効率化、業務効率化、チームワーク強化、コスト削減、品質向上を実現します。このサービスは、製造業の課題を深く理解し、それに対する最適なデジタルソリューションを提供することで、企業が持続的な成長とイノベーションを達成できるようサポートします。
オンライン講座
製造業、主に購買・調達部門にお勤めの方々に向けた情報を配信しております。
新任の方やベテランの方、管理職を対象とした幅広いコンテンツをご用意しております。
お問い合わせ
コストダウンが利益に直結する術だと理解していても、なかなか前に進めることができない状況。そんな時は、newjiのコストダウン自動化機能で大きく利益貢献しよう!
(Β版非公開)