- お役立ち記事
- What factors should purchasing departments consider when reviewing supplier selection criteria?
What factors should purchasing departments consider when reviewing supplier selection criteria?
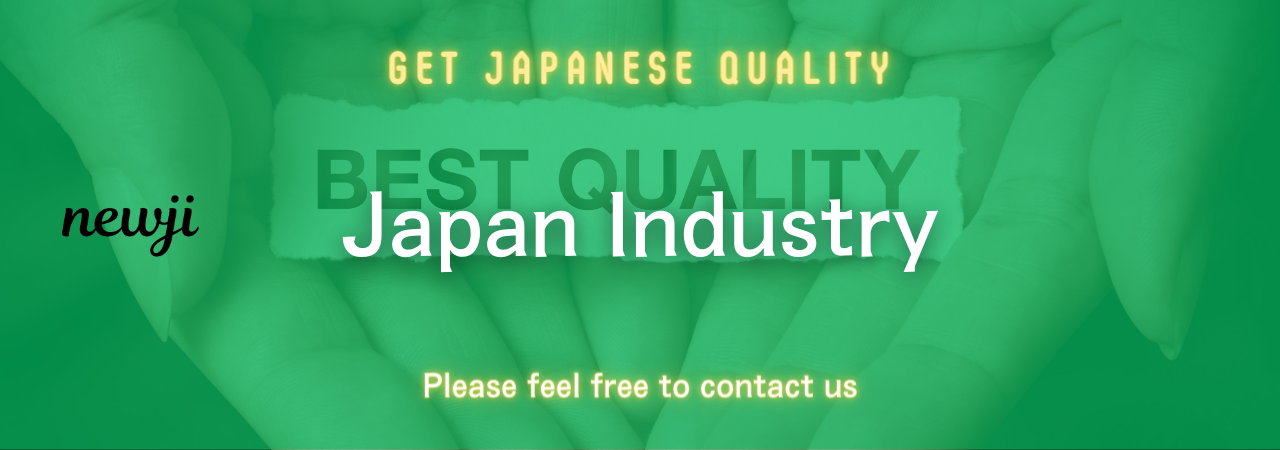
目次
Understanding Supplier Selection
Purchasing departments play a critical role in an organization’s supply chain management process.
They are responsible for acquiring goods and services that are necessary for day-to-day operations.
When selecting suppliers, these departments need to ensure that the suppliers align with the company’s goals and objectives.
Supplier selection is not just about getting the lowest price but involves evaluating a range of factors that can impact the overall health and efficiency of the supply chain.
Criteria for Supplier Selection
There are numerous factors that purchasing departments must consider when reviewing supplier selection criteria.
These criteria help ensure that the selected supplier can meet the organization’s needs both now and in the future.
Here are some key factors that purchasing departments typically evaluate:
1. Price and Cost Considerations
While getting the best price is crucial, it’s important to consider the total cost of ownership.
This includes the purchase price, shipping, handling, and storage costs.
Sometimes, a supplier with a slightly higher price might offer lower transportation or packaging costs, which could lead to overall savings.
It is also essential to evaluate the potential for cost savings through bulk purchasing or long-term agreements.
2. Quality of Goods and Services
The quality of the goods or services provided by a supplier is paramount.
Poor-quality materials can lead to production delays, increased waste, and customer dissatisfaction.
Purchasing departments should look for suppliers that have stringent quality control measures in place.
Certificates of quality and past performance reviews can be helpful in evaluating this factor.
3. Reliability and Performance
Reliability refers to a supplier’s ability to deliver goods and services consistently and on time.
Consistent late deliveries or incomplete shipments can disrupt an organization’s operations and lead to increased costs.
Performance history, such as past delivery records and the ability to meet order specifications, should be assessed.
4. Financial Stability
A supplier’s financial health is a crucial consideration.
A financially unstable supplier may struggle to deliver consistently or may go out of business suddenly.
Purchasing departments should review financial statements and credit ratings to assess potential risks.
5. Capacity and Capability
Can the supplier handle large orders if the business scales up?
Suppliers should have the capacity to meet future increases in demand without compromising on quality or delivery times.
Capability involves the supplier’s ability to provide custom solutions or adapt to changes in requirement specifications.
Advanced Factors to Evaluate
In addition to the basic criteria, purchasing departments often need to consider more advanced factors that can influence their choice of suppliers:
1. Technological Compatibility
In an increasingly digital world, technological compatibility between suppliers and purchasing departments can significantly ease the procurement process.
Suppliers who use modern technologies, like electronic data interchange (EDI), can streamline the order process, reduce errors, and improve transactional efficiency.
2. Sustainability and Ethical Practices
Given the growing importance of corporate social responsibility, selecting suppliers with sustainable and ethical practices is becoming more important.
Organizations seek suppliers who adhere to environmental regulations and maintain fair labor practices.
Sustainability credentials and third-party certifications can provide assurance in this area.
3. Supplier’s Reputation and Track Record
Reputation can oftentimes be a predictor of future performance.
Suppliers with a strong reputation often have established processes and standards in place.
Checking reviews, customer testimonials, and case studies can provide insights into a supplier’s reputation and performance history.
4. Strategic Fit and Relationship
Developing a strong relationship with a supplier can be a valuable advantage.
Suppliers that align with the strategic goals of your organization, and are willing to engage in joint initiatives, provide an added benefit.
Collaborative partnerships can lead to better communication, enhanced product development, and mutually beneficial growth.
The Selection Process
Selection of the right supplier is a structured process, and it should involve input from multiple stakeholders within the organization.
These might include end-users, finance teams, quality assurance, and logistics.
A common approach involves the creation of a supplier evaluation scorecard.
This tool helps in objectively comparing suppliers against set criteria and supports decision-making by providing a quantifiable assessment.
Once potential suppliers have been evaluated, it may be beneficial to conduct site visits or trial runs.
This helps in verifying the supplier’s capabilities, quality control measures, and working conditions.
Conclusion
The purchasing department plays a vital role in ensuring an efficient and reliable supply chain.
Choosing the right supplier involves looking beyond just costs, to a comprehensive evaluation of quality, reliability, capacity, and ethical practices, among other factors.
Ultimately, the goal is to forge partnerships with suppliers that not only meet the immediate needs but also support long-term strategic goals.
With the right suppliers, organizations can improve product quality, reduce costs, and enhance customer satisfaction, maintaining a competitive edge in the marketplace.
資料ダウンロード
QCD調達購買管理クラウド「newji」は、調達購買部門で必要なQCD管理全てを備えた、現場特化型兼クラウド型の今世紀最高の購買管理システムとなります。
ユーザー登録
調達購買業務の効率化だけでなく、システムを導入することで、コスト削減や製品・資材のステータス可視化のほか、属人化していた購買情報の共有化による内部不正防止や統制にも役立ちます。
NEWJI DX
製造業に特化したデジタルトランスフォーメーション(DX)の実現を目指す請負開発型のコンサルティングサービスです。AI、iPaaS、および先端の技術を駆使して、製造プロセスの効率化、業務効率化、チームワーク強化、コスト削減、品質向上を実現します。このサービスは、製造業の課題を深く理解し、それに対する最適なデジタルソリューションを提供することで、企業が持続的な成長とイノベーションを達成できるようサポートします。
オンライン講座
製造業、主に購買・調達部門にお勤めの方々に向けた情報を配信しております。
新任の方やベテランの方、管理職を対象とした幅広いコンテンツをご用意しております。
お問い合わせ
コストダウンが利益に直結する術だと理解していても、なかなか前に進めることができない状況。そんな時は、newjiのコストダウン自動化機能で大きく利益貢献しよう!
(Β版非公開)