- お役立ち記事
- How purchasing can help eliminate supply chain bottlenecks
How purchasing can help eliminate supply chain bottlenecks
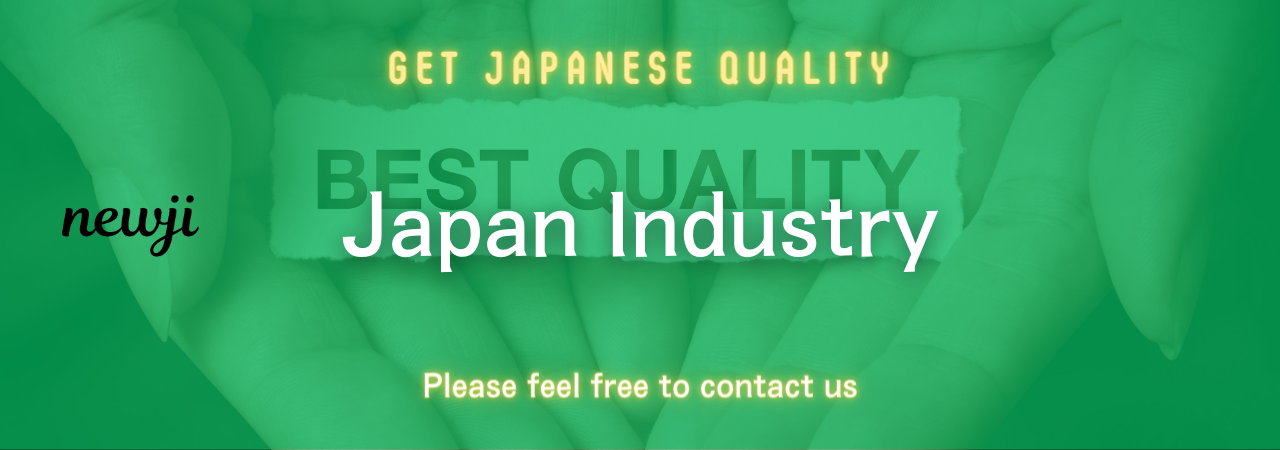
目次
Understanding Supply Chain Bottlenecks
Supply chain bottlenecks are points of congestion in the production or distribution process that can slow down or halt operations.
These bottlenecks can occur due to various issues, such as limited raw material availability, manufacturing delays, or transportation inefficiencies.
When bottlenecks arise, they can lead to delayed deliveries, increased costs, and a negative impact on customer satisfaction and businesses strive to find effective solutions to manage and reduce these disruptions.
The Role of Purchasing in the Supply Chain
Purchasing plays a critical role in the efficiency of a supply chain.
It involves the strategic sourcing and procurement of goods and services needed by an organization.
A well-managed purchasing process ensures that the necessary materials and components are available at the right time, in the right quantity, and at the right cost.
By fostering strong relationships with suppliers and streamlining internal processes, purchasing departments can significantly influence the reduction of supply chain bottlenecks.
Effective Supplier Relationships
Strong supplier relationships are essential for a smooth supply chain.
By establishing open lines of communication and developing partnerships with suppliers, purchasing managers can ensure a more reliable flow of goods.
Good relationships allow for better coordination and quicker responses to changing demands or unexpected disruptions.
Purchasing teams can negotiate favorable terms and foster collaborations that result in improved lead times and reduced bottlenecks.
Strategic Sourcing and Procurement
Strategic sourcing involves identifying and prioritizing the best suppliers based on factors like cost, reliability, and quality.
By carefully selecting suppliers who align with the company’s goals, purchasing managers can significantly mitigate supply chain risks.
Prioritizing quality and dependability in procurement helps avoid delays caused by poor-quality materials or unreliable deliveries.
This proactive approach ensures that goods are sourced in a manner that minimizes potential disruptions.
Leveraging Technology and Data
Technology and data play a crucial role in modern supply chain management.
Purchasing departments can take advantage of advanced software solutions that provide real-time visibility into inventory levels, supplier performance, and market trends.
By using data analytics, companies can make informed purchasing decisions that anticipate demand fluctuations and optimize stock levels.
This reduces the risk of bottlenecks caused by sudden shortages or overstocks.
Automation and Process Improvements
Automation can streamline the purchasing process, reducing manual errors and increasing efficiency.
By automating routine tasks such as order processing and invoice management, purchasing teams can focus on strategic activities that add value.
Automation also accelerates the procurement cycle, allowing for faster responses to supply chain disruptions and reducing the impact of potential bottlenecks.
Predictive Analytics and Demand Forecasting
Predictive analytics tools enable companies to forecast future demand with greater accuracy.
By analyzing historical data and market trends, purchasing departments can adjust their procurement strategies to anticipate changes in demand.
This foresight allows for proactive measures, such as adjusting order quantities or securing backup suppliers, thus preventing potential bottlenecks before they occur.
Adaptability and Risk Management
The ability to adapt quickly to changing conditions is essential in minimizing supply chain disruptions.
Purchasing teams that embrace flexibility in their processes can respond more effectively to unexpected challenges.
By diversifying suppliers and maintaining backup plans, companies can reduce the impact of supplier failures or geographical disruptions.
Risk management strategies such as supplier audits and contingency planning are critical components of a resilient supply chain.
Supplier Diversification
Relying on a single supplier can be risky.
By diversifying the supplier base, purchasing departments mitigate the risk of disruptions caused by supplier-specific issues.
Having alternative sources for critical materials ensures that production can continue even if one supplier faces challenges.
Supplier diversification also encourages competition, which can lead to more favorable pricing and service terms.
Contingency Planning
Contingency planning involves preparing for unforeseen events such as natural disasters, political instability, or sudden market shifts.
By developing contingency plans, purchasing teams can ensure that there are measures in place to maintain operations during a crisis.
These plans might include stockpiling critical materials, identifying alternative transportation routes, or setting up emergency contracts with additional suppliers.
Such preparations help mitigate the impact of disruptions on the overall supply chain.
Conclusion
Purchasing is a vital function in the effort to eliminate supply chain bottlenecks.
Through effective supplier relationships, strategic sourcing, and leveraging technology, purchasing departments can significantly enhance the flow of goods and reduce disruptions.
By increasing adaptability and focusing on risk management, companies can build a resilient supply chain that withstands unexpected challenges.
A proactive and strategic approach to purchasing is key to minimizing bottlenecks and ensuring smooth and efficient operations.
資料ダウンロード
QCD調達購買管理クラウド「newji」は、調達購買部門で必要なQCD管理全てを備えた、現場特化型兼クラウド型の今世紀最高の購買管理システムとなります。
ユーザー登録
調達購買業務の効率化だけでなく、システムを導入することで、コスト削減や製品・資材のステータス可視化のほか、属人化していた購買情報の共有化による内部不正防止や統制にも役立ちます。
NEWJI DX
製造業に特化したデジタルトランスフォーメーション(DX)の実現を目指す請負開発型のコンサルティングサービスです。AI、iPaaS、および先端の技術を駆使して、製造プロセスの効率化、業務効率化、チームワーク強化、コスト削減、品質向上を実現します。このサービスは、製造業の課題を深く理解し、それに対する最適なデジタルソリューションを提供することで、企業が持続的な成長とイノベーションを達成できるようサポートします。
オンライン講座
製造業、主に購買・調達部門にお勤めの方々に向けた情報を配信しております。
新任の方やベテランの方、管理職を対象とした幅広いコンテンツをご用意しております。
お問い合わせ
コストダウンが利益に直結する術だと理解していても、なかなか前に進めることができない状況。そんな時は、newjiのコストダウン自動化機能で大きく利益貢献しよう!
(Β版非公開)