- お役立ち記事
- A must-see for the purchasing department! Achieving quality improvement by strengthening cooperation between buyers and engineers
A must-see for the purchasing department! Achieving quality improvement by strengthening cooperation between buyers and engineers
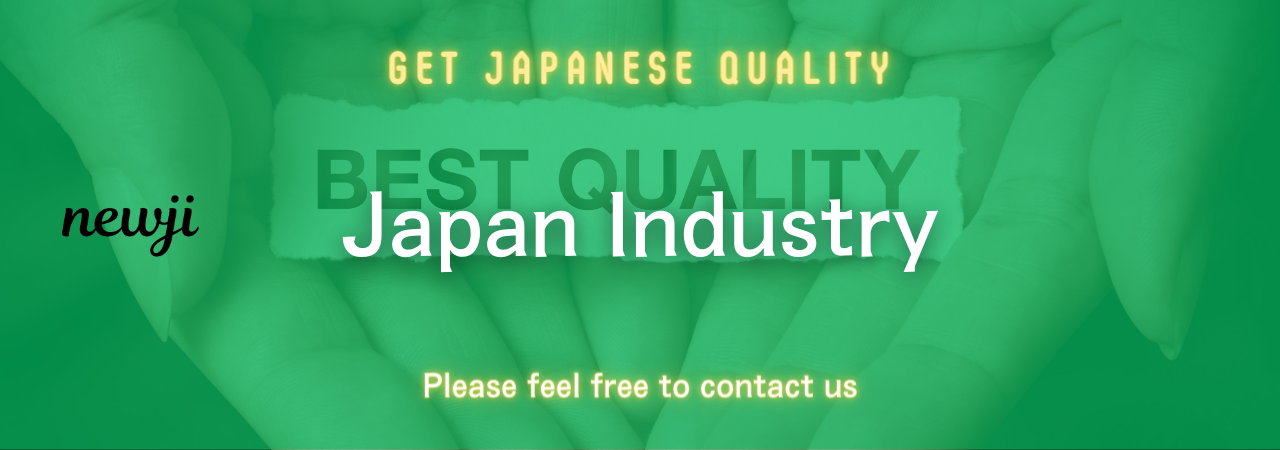
目次
The Importance of Collaboration Between Buyers and Engineers
The purchasing department plays a crucial role in any company, especially when it comes to ensuring the acquisition of quality materials and components at the right cost.
In many industries, achieving quality improvement is a top priority, and one effective way to achieve this is by strengthening the collaboration between buyers and engineers.
Both groups bring unique expertise to the table, and when they work together effectively, they can significantly enhance product quality and optimize the procurement process.
Understanding the Roles of Buyers and Engineers
Buyers, or procurement specialists, are responsible for sourcing, negotiating, and managing suppliers.
They focus on obtaining the best materials and parts to meet budgetary constraints and project deadlines.
On the other hand, engineers design and develop products, ensuring that they meet technical specifications and performance standards.
Their primary goal is to create high-quality products that are efficient, safe, and reliable.
While buyers concentrate on cost and terms, engineers emphasize functional and technical attributes.
These differing priorities sometimes lead to a gap in communication and understanding, which can adversely affect quality outcomes.
Benefits of Close Collaboration
Collaboration between buyers and engineers can result in numerous benefits:
1. **Quality Assurance:** By working together, buyers and engineers can ensure that purchased components meet design requirements and quality standards.
This collaboration can prevent defects and reduce rework, leading to more reliable products.
2. **Cost Efficiency:** Engineers can help buyers understand the importance of certain specifications, meaning buyers can make informed decisions that balance cost with quality, potentially reducing unnecessary expenses.
3. **Innovation and Problem Solving:** Collaborative efforts often lead to creative solutions to complex challenges.
Buyers and engineers can brainstorm together, leveraging each other’s insights to innovate and overcome obstacles.
4. **Improved Communication:** When buyers and engineers collaborate, they develop better communication habits, reducing misunderstandings that can delay projects.
5. **Supplier Relationships:** Buyers, with engineers’ input, can develop stricter standards and expectations for suppliers, leading to improved supplier performance and reliability.
Strategies to Strengthen Cooperation
Improving collaboration between buyers and engineers involves implementing several strategies:
1. **Regular Meetings:** Establish regular meetings between buyers and engineers to discuss ongoing projects, material specifications, and any challenges.
This keeps everyone on the same page and fosters a teamwork mindset.
2. **Cross-training Programs:** Allow buyers to understand engineering principles and vice versa.
This can help each party appreciate the other’s challenges and capabilities, leading to more effective problem-solving.
3. **Collaborative Tools:** Implement collaborative software tools that allow buyers and engineers to share information seamlessly.
These tools can track project status, supply chain details, and quality control measures in real time.
4. **Shared Goals and KPIs:** Define shared performance metrics and goals that both teams work towards.
This alignment encourages joint accountability for achieving quality and efficiency objectives.
5. **Incentive Structures:** Create incentive programs that reward teamwork and successful collaborative projects.
Recognizing the combined efforts of buyers and engineers can motivate continued cooperation.
Case Studies and Examples
Several companies across various industries have successfully improved quality through enhanced collaboration between purchasing and engineering teams.
For example, an automotive manufacturer might establish cross-functional teams to work on new model development.
By including buyers and engineers from the start, they can ensure that all parts meet the necessary specifications while maintaining cost efficiency.
In the electronics industry, a company might hold joint workshops where buyers learn about the technical intricacies of new product designs.
Such initiatives enable buyers to source more appropriate components and negotiate better terms with suppliers based on a deeper technical understanding.
Overcoming Challenges
Despite the clear benefits, fostering collaboration between buyers and engineers can present challenges:
1. **Cultural Differences:** The two departments may have distinct cultures and ways of working.
Bridging these differences requires deliberate effort and a willingness to adopt new perspectives.
2. **Conflict Resolution:** Disagreements about priorities and specifications can arise.
Having a structured conflict resolution process can help maintain positive and productive working relationships.
3. **Resource Allocation:** Both departments may feel strained for time and resources.
Allocating dedicated time and resources to foster collaboration is crucial for long-term success.
Conclusion
The purchasing department and engineering team, when working closely together, are formidable allies in the quest for quality improvement.
By integrating their distinct expertise, companies can achieve superior product quality, foster innovation, and maintain competitive costs in their supply chain.
Creating an environment that encourages and facilitates this cooperation is vital for sustained success and should be a strategic priority for any forward-thinking organization.
資料ダウンロード
QCD調達購買管理クラウド「newji」は、調達購買部門で必要なQCD管理全てを備えた、現場特化型兼クラウド型の今世紀最高の購買管理システムとなります。
ユーザー登録
調達購買業務の効率化だけでなく、システムを導入することで、コスト削減や製品・資材のステータス可視化のほか、属人化していた購買情報の共有化による内部不正防止や統制にも役立ちます。
NEWJI DX
製造業に特化したデジタルトランスフォーメーション(DX)の実現を目指す請負開発型のコンサルティングサービスです。AI、iPaaS、および先端の技術を駆使して、製造プロセスの効率化、業務効率化、チームワーク強化、コスト削減、品質向上を実現します。このサービスは、製造業の課題を深く理解し、それに対する最適なデジタルソリューションを提供することで、企業が持続的な成長とイノベーションを達成できるようサポートします。
オンライン講座
製造業、主に購買・調達部門にお勤めの方々に向けた情報を配信しております。
新任の方やベテランの方、管理職を対象とした幅広いコンテンツをご用意しております。
お問い合わせ
コストダウンが利益に直結する術だと理解していても、なかなか前に進めることができない状況。そんな時は、newjiのコストダウン自動化機能で大きく利益貢献しよう!
(Β版非公開)