- お役立ち記事
- Establishment of quality standards for purchasing departments and support measures for supplier employees
Establishment of quality standards for purchasing departments and support measures for supplier employees
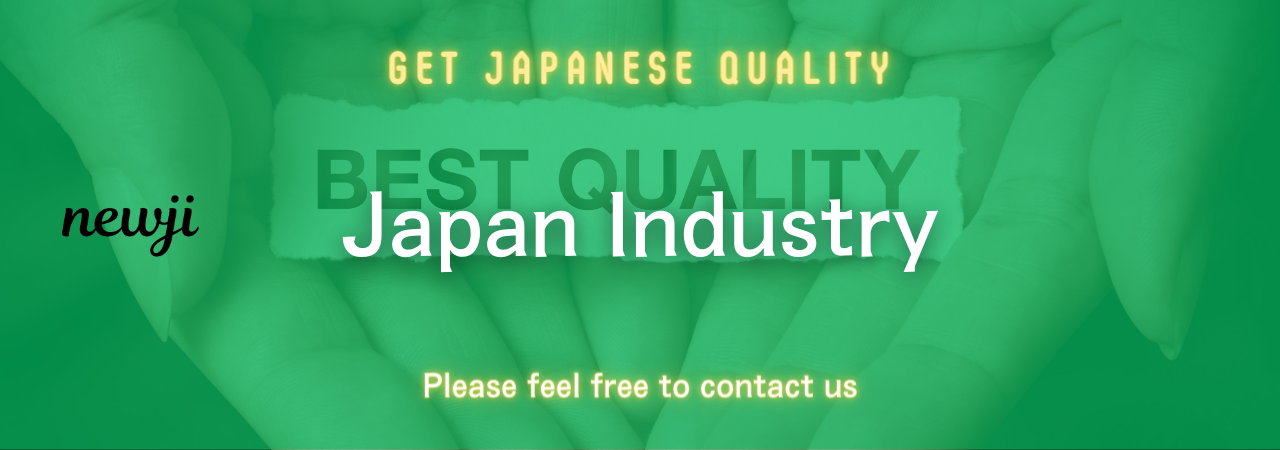
目次
Why Quality Standards Are Essential for Purchasing Departments
In today’s competitive marketplace, the purchasing department plays a crucial role in ensuring that businesses receive high-quality products and services.
This department is responsible for selecting suppliers, negotiating contracts, and ultimately ensuring that the organization gets the best value for its money.
With the increasing complexity of global supply chains, it has become more important than ever for purchasing departments to establish clear quality standards.
Quality standards help to minimize risks associated with purchasing, such as receiving defective goods or encountering unreliable suppliers.
They provide a benchmark for evaluating suppliers and ensuring that they meet the required levels of quality and service.
By implementing quality standards, companies can streamline their procurement processes, improve supplier relationships, and achieve better overall efficiency.
Key Components of Quality Standards
When establishing quality standards for purchasing departments, several key components need to be considered.
These components help ensure that the standards are comprehensive and cover all aspects of the purchasing process.
1. Supplier Evaluation
One of the first steps in establishing quality standards is creating a robust supplier evaluation process.
This process should assess suppliers based on several criteria, including reliability, product quality, service levels, and financial stability.
By conducting thorough evaluations, purchasing departments can identify suppliers who consistently meet or exceed expectations.
This helps reduce risks associated with poor supplier performance and ensures that only the best suppliers are selected for business partnerships.
2. Contract Management
Contracts play a vital role in ensuring clarity and setting expectations between businesses and their suppliers.
Quality standards should include guidelines for drafting, reviewing, and managing contracts effectively.
These guidelines help ensure that both parties clearly understand their responsibilities and obligations.
They also provide a framework for addressing potential disputes, ensuring that issues can be resolved quickly and amicably.
3. Performance Monitoring
Ongoing performance monitoring is essential to ensure that suppliers continue to meet quality standards after the initial evaluation.
Purchasing departments should establish clear metrics and performance indicators to regularly assess supplier performance.
This proactive approach allows companies to address any shortcomings early and maintain strong supplier relationships.
Regular feedback to suppliers can also encourage continuous improvement and innovation in their processes.
4. Risk Management
Quality standards should include risk management strategies to identify and mitigate potential supply chain disruptions.
These strategies may involve diversifying suppliers, conducting regular audits, and developing contingency plans.
By incorporating risk management into their quality standards, businesses can protect themselves from unexpected events and maintain a reliable supply chain.
Supporting Supplier Employees
While quality standards are crucial for purchasing departments, it is equally important to support supplier employees in meeting these standards.
After all, a supplier’s ability to deliver quality products and services depends largely on the competence and motivation of its workforce.
1. Training and Development
Investing in the training and development of supplier employees is a key strategy for ensuring quality.
By providing access to relevant education and skill-building opportunities, suppliers can equip their workforce with the knowledge needed to meet quality standards.
Training programs can cover a range of topics, including industry best practices, advanced technologies, and quality control techniques.
A well-trained workforce is more capable of adapting to changing requirements and maintaining high standards.
2. Fair Labor Practices
Supporting fair labor practices is vital for fostering a positive working environment among supplier employees.
Purchasing departments should prioritize partnerships with suppliers that adhere to ethical labor practices and provide fair wages and safe working conditions.
Ensuring fair treatment of employees not only helps suppliers meet quality standards but also strengthens the overall supplier relationship.
Happy and motivated employees are more likely to contribute positively to the manufacturing process, leading to higher quality products.
3. Collaboration and Communication
Strong collaboration and communication between purchasing departments and suppliers can facilitate the implementation of quality standards.
Regular meetings, feedback sessions, and joint problem-solving efforts can help align both parties towards common goals.
Open communication fosters transparency and trust, allowing potential issues to be addressed quickly.
It also provides a platform for suppliers to voice their concerns and seek support, ensuring that both parties work towards continuous improvement.
Conclusion
In conclusion, establishing quality standards for purchasing departments is essential for maintaining high levels of product and service quality.
A structured approach to supplier evaluation, contract management, performance monitoring, and risk management can streamline the purchasing process and enhance supplier relationships.
Supporting supplier employees through training, fair labor practices, and effective communication is equally crucial for achieving these quality standards.
By investing in supplier partnerships and ensuring that employees are motivated and skilled, businesses can safeguard the integrity of their supply chain and maintain a competitive edge.
Implementing these strategies empowers purchasing departments to drive quality, efficiency, and value throughout the organization.
資料ダウンロード
QCD調達購買管理クラウド「newji」は、調達購買部門で必要なQCD管理全てを備えた、現場特化型兼クラウド型の今世紀最高の購買管理システムとなります。
ユーザー登録
調達購買業務の効率化だけでなく、システムを導入することで、コスト削減や製品・資材のステータス可視化のほか、属人化していた購買情報の共有化による内部不正防止や統制にも役立ちます。
NEWJI DX
製造業に特化したデジタルトランスフォーメーション(DX)の実現を目指す請負開発型のコンサルティングサービスです。AI、iPaaS、および先端の技術を駆使して、製造プロセスの効率化、業務効率化、チームワーク強化、コスト削減、品質向上を実現します。このサービスは、製造業の課題を深く理解し、それに対する最適なデジタルソリューションを提供することで、企業が持続的な成長とイノベーションを達成できるようサポートします。
オンライン講座
製造業、主に購買・調達部門にお勤めの方々に向けた情報を配信しております。
新任の方やベテランの方、管理職を対象とした幅広いコンテンツをご用意しております。
お問い合わせ
コストダウンが利益に直結する術だと理解していても、なかなか前に進めることができない状況。そんな時は、newjiのコストダウン自動化機能で大きく利益貢献しよう!
(Β版非公開)