- お役立ち記事
- Standardization process for complex procurement conditions faced by purchasing departments
Standardization process for complex procurement conditions faced by purchasing departments
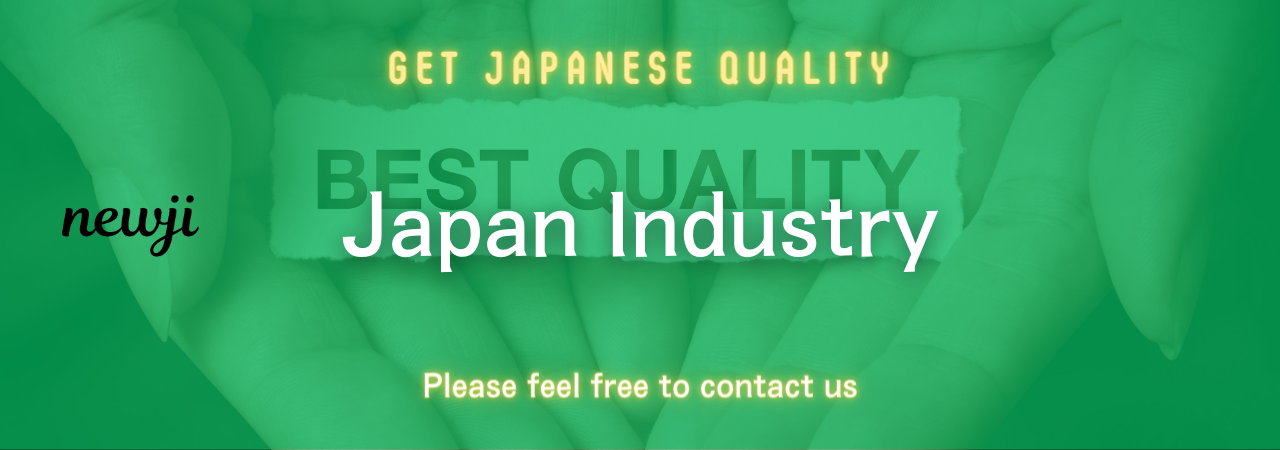
目次
Understanding the Importance of Standardization in Procurement
Purchasing departments often face complex procurement conditions, which can be challenging to manage effectively.
Standardization is a critical aspect of procurement that helps streamline these conditions, making the purchasing process more efficient and manageable.
By implementing standardization, companies can achieve consistency, reduce errors, and optimize their procurement strategies.
Procurement involves acquiring goods and services, requiring stringent processes to ensure quality and cost-effectiveness.
Without standardization, a purchasing department might encounter issues such as inconsistent supplier performance, varied product quality, and difficulty in managing contracts.
Challenges of Complex Procurement Conditions
Complex procurement conditions can arise from a range of factors, including diverse supplier bases, regulatory requirements, and fluctuating market demands.
Purchasing departments must navigate these challenges while adhering to company policies and maintaining compliance with legal and regulatory standards.
One common challenge is managing multiple suppliers, each with their own terms and conditions.
This diversity can lead to discrepancies in supplier performance and product delivery, making it difficult to maintain a consistent standard.
Moreover, regulatory requirements can vary significantly across regions, complicating compliance efforts for companies operating in multiple jurisdictions.
Fluctuating market demand also presents a challenge, as purchasing departments must adjust procurement strategies rapidly to meet changing needs.
Without standardization, these adjustments can lead to inefficiencies and increased costs.
Benefits of the Standardization Process
Standardization offers numerous benefits to purchasing departments facing complex procurement conditions.
Implementing standardized procedures ensures consistency across all operations, enabling more effective management of suppliers and contracts.
This process also simplifies compliance with regulatory requirements, reducing the risk of penalties and legal issues.
By adopting a standardized approach, companies can streamline communication with suppliers, fostering better relationships and improving negotiation outcomes.
Standardization also enables better data collection and analysis, providing valuable insights into procurement performance and identifying areas for improvement.
Cost reduction is another significant benefit of standardization.
By minimizing errors and inefficiencies, purchasing departments can achieve savings in terms of time, resources, and money.
Steps for Implementing Standardization
Implementing standardization in procurement involves several key steps that purchasing departments can follow to achieve optimal results.
1. **Identify Key Areas for Standardization**: Begin by identifying areas within the procurement process that would benefit most from standardization.
This could include supplier selection, contract management, or quality assurance processes.
2. **Develop Standard Procedures**: Once key areas are identified, develop clear and consistent procedures for each process.
These procedures should be documented and made accessible to all relevant staff members.
3. **Train Staff and Suppliers**: Ensure that all staff members are adequately trained in the new standardized procedures.
Additionally, communicate these standards to suppliers, so they understand the company’s expectations.
4. **Implement Technology Solutions**: Utilize technology solutions, such as procurement software, to support standardized procedures.
These tools can automate processes, improve data accuracy, and facilitate better communication.
5. **Monitor and Review**: Regularly monitor the effectiveness of standardized procedures and make necessary adjustments.
Reviewing performance metrics can help identify opportunities for further improvement and ensure continued alignment with company goals.
Overcoming Resistance to Standardization
Despite the clear benefits, some purchasing departments may resist standardization efforts due to perceived limitations or fear of change.
To overcome this resistance, it’s essential to communicate the advantages of standardization clearly and involve all stakeholders in the process.
Engaging stakeholders from various departments and encouraging their input can foster a sense of ownership and commitment to the standardization process.
Demonstrating measurable improvements, such as cost savings or enhanced supplier performance, can also help gain support for the initiative.
Real-World Examples of Successful Standardization
Many companies have successfully implemented standardization in their procurement processes, reaping significant benefits.
For example, a multinational corporation might standardize its supplier evaluation process, ensuring consistent criteria across all regions.
This approach can lead to improved supplier quality and reliability, as well as enhanced compliance with global standards.
Another example could be a company that standardizes its contract management procedures, utilizing procurement software to automate tasks and maintain a central repository of contract information.
This enables easier access to relevant data, reduces administrative burden, and improves contract compliance.
Conclusion
In conclusion, the standardization process is an essential strategy for managing complex procurement conditions faced by purchasing departments.
Through standardization, companies can achieve consistency, reduce errors, and optimize their procurement processes.
By following a structured approach and involving all stakeholders, businesses can overcome resistance and successfully implement standardized procedures.
Ultimately, standardization not only enhances procurement efficiency but also contributes to a company’s overall competitiveness and bottom line.
資料ダウンロード
QCD調達購買管理クラウド「newji」は、調達購買部門で必要なQCD管理全てを備えた、現場特化型兼クラウド型の今世紀最高の購買管理システムとなります。
ユーザー登録
調達購買業務の効率化だけでなく、システムを導入することで、コスト削減や製品・資材のステータス可視化のほか、属人化していた購買情報の共有化による内部不正防止や統制にも役立ちます。
NEWJI DX
製造業に特化したデジタルトランスフォーメーション(DX)の実現を目指す請負開発型のコンサルティングサービスです。AI、iPaaS、および先端の技術を駆使して、製造プロセスの効率化、業務効率化、チームワーク強化、コスト削減、品質向上を実現します。このサービスは、製造業の課題を深く理解し、それに対する最適なデジタルソリューションを提供することで、企業が持続的な成長とイノベーションを達成できるようサポートします。
オンライン講座
製造業、主に購買・調達部門にお勤めの方々に向けた情報を配信しております。
新任の方やベテランの方、管理職を対象とした幅広いコンテンツをご用意しております。
お問い合わせ
コストダウンが利益に直結する術だと理解していても、なかなか前に進めることができない状況。そんな時は、newjiのコストダウン自動化機能で大きく利益貢献しよう!
(Β版非公開)