- お役立ち記事
- New evaluation criteria to help purchasing departments strengthen supplier management
New evaluation criteria to help purchasing departments strengthen supplier management
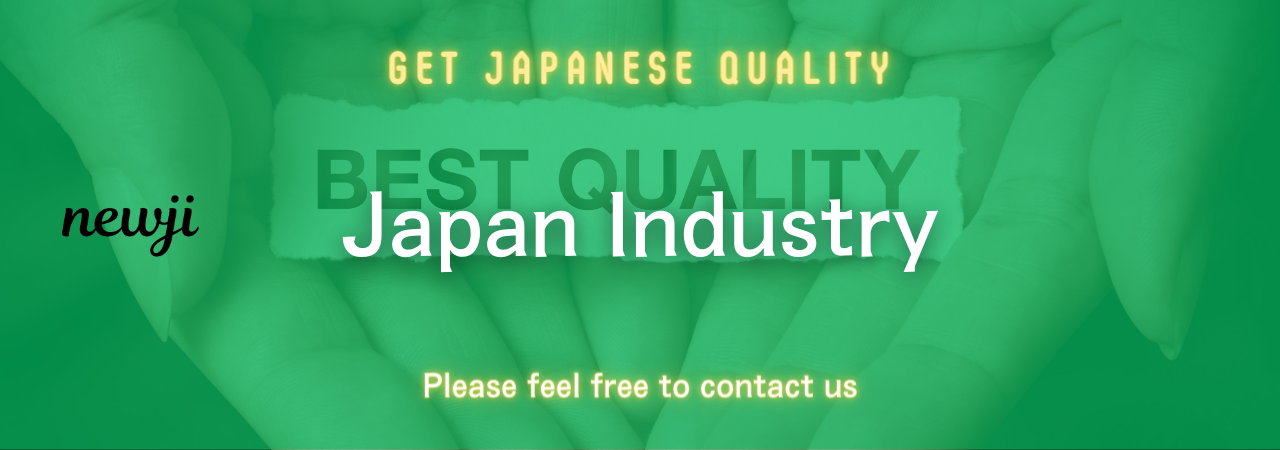
目次
Understanding the Importance of Supplier Management
Supplier management plays a crucial role in the success of any business.
A purchasing department’s ability to effectively evaluate and manage suppliers can directly impact the organization’s performance, efficiency, and profitability.
Having reliable suppliers ensures a consistent supply of quality goods and services, which is vital for maintaining operations and meeting customer demands.
Efficient supplier management involves more than just finding the lowest price.
It requires a comprehensive approach to evaluating suppliers based on various factors, including product quality, delivery performance, compliance with regulations, and financial stability.
By implementing new evaluation criteria, purchasing departments can enhance their supplier management processes and ensure long-term success.
Why New Evaluation Criteria are Needed
The business landscape is constantly evolving, with globalization and technological advancements reshaping the way companies operate.
These changes necessitate the need for updated evaluation criteria to address new challenges and opportunities in supplier management.
Traditional methods of supplier evaluation may no longer be sufficient, as they might not take into account emerging trends, such as sustainability and digital transformation.
Developing new evaluation criteria helps purchasing departments identify and select suppliers that align with the organization’s strategic goals.
It allows them to build more resilient supply chains, enhance collaboration, and mitigate risks associated with supplier performance and compliance.
Key Components of New Evaluation Criteria
When designing new evaluation criteria for supplier management, it’s essential to consider several key components that can provide a comprehensive overview of a supplier’s capabilities.
These components include:
1. Quality Assurance
Ensuring the quality of products and services is one of the primary functions of a purchasing department.
Supplier evaluation should include a thorough assessment of the supplier’s quality management systems, certifications, and track record in delivering high-quality goods.
This helps businesses avoid potential disruptions and additional costs related to defective products.
2. Financial Stability
Assessing a supplier’s financial health is crucial to ensuring continuous operations.
Financial instability can result in supply chain disruptions, delayed deliveries, or even the supplier going out of business.
Evaluate financial statements, credit ratings, and market reputation to gauge a supplier’s financial viability.
3. Delivery Performance
Timely delivery is a critical aspect of supplier performance.
Evaluate a supplier’s track record in meeting delivery deadlines and their capacity to handle fluctuating demand.
Consider their logistics capabilities and infrastructure, and whether they have contingency plans in place to address potential disruptions.
4. Compliance and Risk Management
As regulatory and compliance requirements become more complex, it’s essential to assess a supplier’s adherence to industry standards and regulations.
This includes evaluating their environmental policies, safety practices, and labor standards.
Implementing risk management measures helps mitigate potential legal and reputational risks associated with non-compliant suppliers.
5. Innovation and Adaptability
In a rapidly evolving market, suppliers should demonstrate a commitment to innovation and adaptability.
Assess their ability to embrace new technologies, improve processes, and respond quickly to market changes.
This can help businesses stay competitive and optimize their supply chains.
6. Corporate Social Responsibility
Increasingly, companies are focusing on sustainability and ethical practices within their supply chains.
Evaluate a supplier’s commitment to corporate social responsibility (CSR) by considering their sustainability initiatives, ethical sourcing, and community engagement efforts.
Benefits of Implementing New Evaluation Criteria
By adopting new evaluation criteria, purchasing departments can enjoy several benefits:
1. Improved Supplier Relationships
Enhanced evaluation processes foster better communication and transparency between businesses and suppliers.
This results in stronger partnerships, more effective collaboration, and mutually beneficial outcomes.
2. Greater Efficiency and Cost Savings
Identifying high-performing suppliers enables purchasing departments to make informed decisions that enhance efficiency and reduce costs.
Reliable suppliers minimize the risk of disruptions, ensure quality, and provide value for money.
3. Enhanced Risk Management
Comprehensive supplier evaluation reduces the risk of supply chain disruptions and ensures compliance with regulations.
By proactively addressing potential issues, businesses can safeguard their operations and protect their reputation.
4. Improved Sustainability
Emphasizing sustainability in supplier evaluation supports environmental and social responsibility goals.
This enhances a company’s reputation and meets the increasing demand for sustainable practices from consumers and stakeholders.
Conclusion
In an ever-changing business environment, updating supplier evaluation criteria is essential for purchasing departments to effectively manage their supply base.
By considering factors such as quality assurance, financial stability, delivery performance, compliance, innovation, and corporate social responsibility, businesses can build resilient supply chains and achieve long-term success.
Implementing these new criteria allows organizations to foster stronger supplier relationships, improve efficiency, and contribute to a more sustainable future.
資料ダウンロード
QCD調達購買管理クラウド「newji」は、調達購買部門で必要なQCD管理全てを備えた、現場特化型兼クラウド型の今世紀最高の購買管理システムとなります。
ユーザー登録
調達購買業務の効率化だけでなく、システムを導入することで、コスト削減や製品・資材のステータス可視化のほか、属人化していた購買情報の共有化による内部不正防止や統制にも役立ちます。
NEWJI DX
製造業に特化したデジタルトランスフォーメーション(DX)の実現を目指す請負開発型のコンサルティングサービスです。AI、iPaaS、および先端の技術を駆使して、製造プロセスの効率化、業務効率化、チームワーク強化、コスト削減、品質向上を実現します。このサービスは、製造業の課題を深く理解し、それに対する最適なデジタルソリューションを提供することで、企業が持続的な成長とイノベーションを達成できるようサポートします。
オンライン講座
製造業、主に購買・調達部門にお勤めの方々に向けた情報を配信しております。
新任の方やベテランの方、管理職を対象とした幅広いコンテンツをご用意しております。
お問い合わせ
コストダウンが利益に直結する術だと理解していても、なかなか前に進めることができない状況。そんな時は、newjiのコストダウン自動化機能で大きく利益貢献しよう!
(Β版非公開)