- お役立ち記事
- Supplier Performance Evaluation Checklist Every Purchasing Manager Should Know
Supplier Performance Evaluation Checklist Every Purchasing Manager Should Know
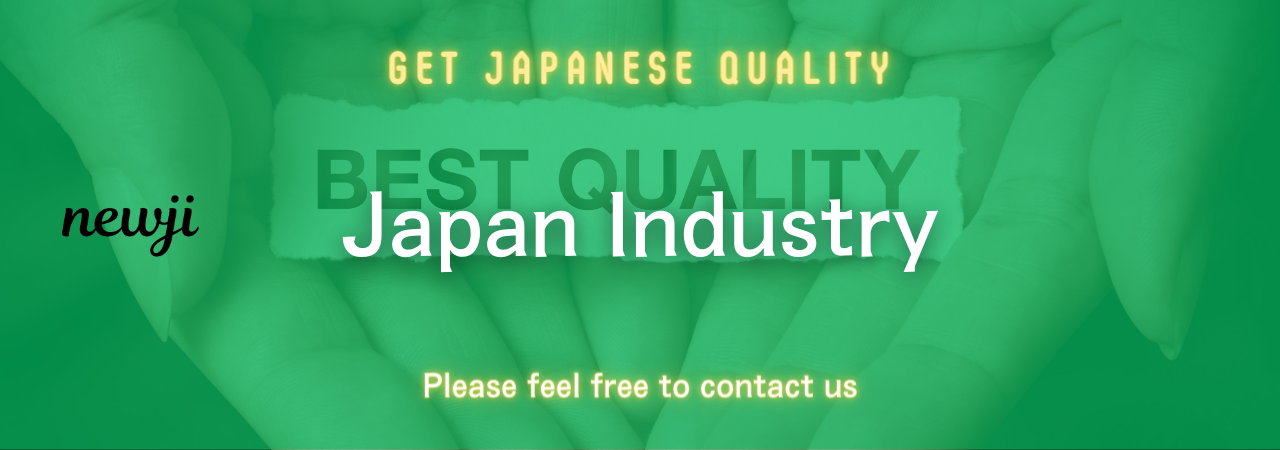
目次
Understanding Supplier Performance Evaluation
When you’re a purchasing manager, choosing the right suppliers is crucial for ensuring smooth operations and maintaining your company’s reputation.
But how do you know if your suppliers are doing their job effectively?
The answer lies in conducting a supplier performance evaluation.
This process helps you assess various aspects of their performance to make informed decisions about continuing or modifying your business relationship with them.
Key Areas to Evaluate in Supplier Performance
Evaluating supplier performance involves several critical factors.
By understanding these areas, you can establish a comprehensive checklist for assessing your suppliers.
Quality of Products or Services
The quality of goods or services delivered by a supplier is paramount.
Subpar quality can lead to production delays, increased costs, and customer dissatisfaction.
Consider setting clear quality standards and regularly comparing the supplier’s output against them to ensure compliance.
Timeliness and Delivery
Timely delivery is crucial for meeting production schedules and customer demands.
Evaluate how consistently suppliers meet agreed delivery times and how they handle unexpected delays.
This insight can reveal whether a supplier can adapt to your business’s needs.
Cost Competitiveness
While cost isn’t the only factor, it plays a significant role in supplier evaluation.
Assess whether the supplier prices align with market rates and whether they offer cost-effective solutions.
Negotiating favorable terms can benefit your company’s bottom line.
Communication and Responsiveness
Effective communication is essential for a strong supplier relationship.
Evaluate how promptly and clearly suppliers communicate any changes or issues.
Responsive suppliers help you stay informed and resolve problems swiftly, minimizing disruptions.
Flexibility and Adaptability
In an ever-changing business environment, the ability of suppliers to adapt is vital.
Analyze whether a supplier can handle variations in demand, introduce new technology or methods, and adjust to market trends.
A flexible supplier can support your company’s growth and evolution.
Compliance and Risk Management
Suppliers must comply with relevant regulations and standards to minimize legal and reputational risks.
Ensure that your suppliers adhere to industry regulations and possess certifications required for your industry.
Additionally, consider how they manage risks like supply chain disruptions or environmental impact.
Innovation and Improvement
Suppliers that actively seek improvements and innovations can add significant value to your business.
Assess whether they invest in research and development, introduce cutting-edge technology, or offer suggestions for process optimization.
Creating a Supplier Performance Evaluation Checklist
Developing a thorough checklist ensures a structured evaluation process.
Here’s how to create one:
Step 1: Define Evaluation Criteria
Identify the key performance indicators (KPIs) that align with your business objectives.
Consider criteria like quality, delivery, cost, communication, flexibility, compliance, and innovation.
Each KPI should have clear metrics for assessment.
Step 2: Establish Evaluation Frequency
Decide how often you will evaluate your suppliers.
This can depend on the nature of your industry, the criticality of the supplied goods or services, and resource availability.
Regular evaluations enable you to track improvements and address issues promptly.
Step 3: Gather Data
Collect data from relevant sources such as purchase orders, delivery records, quality inspections, and customer feedback.
In some cases, you may request performance reports from suppliers to gain additional insight.
Step 4: Score and Analyze
Assign scores to each KPI based on the collected data.
You can use a simple rating system or a more complex weighted scoring model to accommodate varying priorities.
Analyze the scores to identify trends, strengths, and weaknesses.
Step 5: Provide Feedback and Establish Action Plans
Communicate evaluation results to suppliers, highlighting areas of excellence and those requiring improvement.
Work collaboratively to develop action plans for enhancing performance, setting realistic goals, and monitoring progress.
Benefits of Conducting Supplier Performance Evaluations
Supplier performance evaluations offer several advantages that support your business’s strategic goals:
Improved Supplier Relationships
Regular evaluations help foster open communication, trust, and collaboration.
Suppliers are more likely to be proactive in addressing issues and meeting your company’s expectations.
Enhanced Quality and Efficiency
By identifying areas for improvement, suppliers can focus on delivering better quality and timely services.
This contributes to smoother operations and increased customer satisfaction.
Cost Management
Evaluations help identify suppliers who offer competitive pricing while maintaining high standards.
This allows you to make informed decisions about cost management and sourcing strategies.
Risk Mitigation
By ensuring suppliers comply with regulations and manage risks effectively, you reduce potential disruptions and liabilities.
This proactive approach protects your company’s reputation and continuity.
Strategic Sourcing Decisions
Evaluations provide insights that guide strategic sourcing decisions, allowing you to align supplier selection with long-term business objectives.
Conclusion
Supplier performance evaluations are a vital tool for purchasing managers.
By systematically assessing quality, delivery, cost, communication, flexibility, compliance, and innovation, you can make informed decisions about supplier partnerships.
Creating a detailed checklist and conducting regular evaluations not only improves supplier relationships but also enhances overall business performance.
Implementing these practices ensures your supply chain remains strong, flexible, and capable of supporting your company’s growth.
資料ダウンロード
QCD調達購買管理クラウド「newji」は、調達購買部門で必要なQCD管理全てを備えた、現場特化型兼クラウド型の今世紀最高の購買管理システムとなります。
ユーザー登録
調達購買業務の効率化だけでなく、システムを導入することで、コスト削減や製品・資材のステータス可視化のほか、属人化していた購買情報の共有化による内部不正防止や統制にも役立ちます。
NEWJI DX
製造業に特化したデジタルトランスフォーメーション(DX)の実現を目指す請負開発型のコンサルティングサービスです。AI、iPaaS、および先端の技術を駆使して、製造プロセスの効率化、業務効率化、チームワーク強化、コスト削減、品質向上を実現します。このサービスは、製造業の課題を深く理解し、それに対する最適なデジタルソリューションを提供することで、企業が持続的な成長とイノベーションを達成できるようサポートします。
オンライン講座
製造業、主に購買・調達部門にお勤めの方々に向けた情報を配信しております。
新任の方やベテランの方、管理職を対象とした幅広いコンテンツをご用意しております。
お問い合わせ
コストダウンが利益に直結する術だと理解していても、なかなか前に進めることができない状況。そんな時は、newjiのコストダウン自動化機能で大きく利益貢献しよう!
(Β版非公開)