- お役立ち記事
- Examples of distributed supply chain construction that are attracting attention in global purchasing departments
Examples of distributed supply chain construction that are attracting attention in global purchasing departments
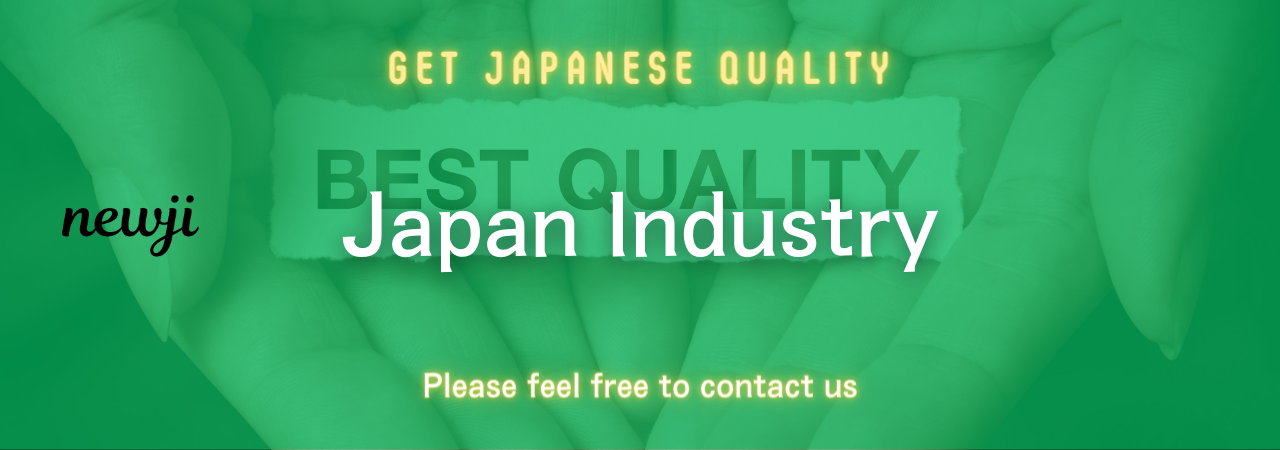
目次
Introduction to Distributed Supply Chains
In today’s rapidly changing global economy, businesses are exploring innovative ways to enhance their supply chains.
One such method that has garnered significant attention is the construction of distributed supply chains.
But what exactly does this term mean, and why is it becoming so popular?
A distributed supply chain refers to a network where the production of goods and services is spread out over multiple locations.
This approach contrasts with traditional, centralized supply chains where production is concentrated in a single location.
By distributing production, companies aim to increase efficiency, reduce risks, and respond more flexibly to market demands.
The Driving Forces Behind Distributed Supply Chains
The push towards distributed supply chains has been driven by several key factors.
Firstly, technological advancements have enabled seamless communication and coordination across diverse geographical locations.
With digital tools, companies can efficiently manage logistics and ensure smooth operations, irrespective of where production occurs.
Secondly, the global nature of commerce has prompted companies to cater to diverse markets.
By having production sites closer to key markets, businesses can respond quickly to local demands.
This localization also helps in mitigating potential disruptions, such as those caused by geopolitical tensions or natural disasters.
Another driving force is the increasing importance of sustainability.
Distributed supply chains allow companies to minimize their carbon footprint by reducing the distance goods need to travel.
This approach not only aligns with global sustainability goals but also improves a company’s brand image.
Benefits of Distributed Supply Chains
The adoption of distributed supply chains offers several benefits to global purchasing departments.
One major advantage is risk reduction.
By diversifying production locations, companies can avoid the pitfalls of concentrating all operations in a single area, making them more resilient to unexpected disruptions.
Another benefit is cost efficiency.
While setting up multiple production sites may initially seem costly, it can lead to savings in the long run.
Transport costs can be significantly reduced when products are manufactured closer to the end consumer.
Additionally, companies can take advantage of regional cost variations in labor and materials.
Flexibility and scalability are also enhanced in distributed supply chains.
As market demands fluctuate, companies can quickly adjust production levels across different locations.
This adaptability ensures that businesses remain competitive and can capture new opportunities as they arise.
Global Examples of Distributed Supply Chains
Several global companies have successfully transitioned to distributed supply chains, showcasing their potential.
Let’s look at some notable examples:
Toyota’s Global Production Network
Toyota, a leader in the automotive industry, has implemented a highly effective distributed supply chain.
By establishing production facilities in various regions, Toyota ensures that its vehicles are tailored to local market preferences.
This approach not only improves customer satisfaction but also reduces delivery times and costs.
Apple’s Strategic Manufacturing Approach
Apple’s supply chain strategy incorporates elements of distribution, with production spread across multiple countries.
By leveraging a global network of suppliers and manufacturers, Apple can maintain high production standards while benefiting from regional expertise and resources.
Zara and Rapid Response to Fashion Trends
The Spanish fashion retailer Zara uses a distributed supply chain to its advantage by producing a majority of its products in close proximity to its key markets.
This strategy allows Zara to quickly respond to changing fashion trends and maintain a competitive edge in the fast-paced fashion industry.
Challenges in Implementing Distributed Supply Chains
Despite the numerous benefits, constructing a distributed supply chain is not without its challenges.
One major hurdle is coordinating operations across multiple locations.
Ensuring consistency in quality and standards requires robust management systems and continuous monitoring.
Additionally, companies must navigate varying regulatory environments.
Different countries have unique compliance requirements, and businesses need to be aware of these regulations to avoid legal complications.
There is also the challenge of cultural differences.
Working across diverse regions involves understanding and managing cultural nuances, which can impact communication and collaboration.
Best Practices for Building a Distributed Supply Chain
For global purchasing departments looking to adopt a distributed supply chain, certain best practices can guide their efforts.
Firstly, leveraging technology is essential.
Investing in digital tools that facilitate communication, inventory management, and data analysis can greatly enhance operational efficiency.
Secondly, building strong relationships with local partners is crucial.
By collaborating with regional suppliers, companies can gain insights into local markets and strengthen their supply chain resilience.
It’s also important to develop contingency plans.
Preparedness for potential disruptions ensures that companies can maintain operations without significant setbacks.
Lastly, continuous evaluation and optimization of the supply chain are vital.
By regularly assessing performance, businesses can identify areas for improvement and adjust their strategies accordingly.
Conclusion
The adoption of distributed supply chains offers substantial benefits for global purchasing departments, from increased flexibility and resilience to cost efficiencies and sustainability improvements.
As companies continue to navigate the complexities of the global market, distributed supply chains provide a valuable framework to enhance their operations and meet the challenges of the modern economy.
Incorporating this approach requires careful planning, robust management, and a willingness to adapt, but those who successfully implement it can achieve significant competitive advantages.
資料ダウンロード
QCD調達購買管理クラウド「newji」は、調達購買部門で必要なQCD管理全てを備えた、現場特化型兼クラウド型の今世紀最高の購買管理システムとなります。
ユーザー登録
調達購買業務の効率化だけでなく、システムを導入することで、コスト削減や製品・資材のステータス可視化のほか、属人化していた購買情報の共有化による内部不正防止や統制にも役立ちます。
NEWJI DX
製造業に特化したデジタルトランスフォーメーション(DX)の実現を目指す請負開発型のコンサルティングサービスです。AI、iPaaS、および先端の技術を駆使して、製造プロセスの効率化、業務効率化、チームワーク強化、コスト削減、品質向上を実現します。このサービスは、製造業の課題を深く理解し、それに対する最適なデジタルソリューションを提供することで、企業が持続的な成長とイノベーションを達成できるようサポートします。
オンライン講座
製造業、主に購買・調達部門にお勤めの方々に向けた情報を配信しております。
新任の方やベテランの方、管理職を対象とした幅広いコンテンツをご用意しております。
お問い合わせ
コストダウンが利益に直結する術だと理解していても、なかなか前に進めることができない状況。そんな時は、newjiのコストダウン自動化機能で大きく利益貢献しよう!
(Β版非公開)