- お役立ち記事
- Coordination process between manufacturing sites and suppliers led by the purchasing department
Coordination process between manufacturing sites and suppliers led by the purchasing department
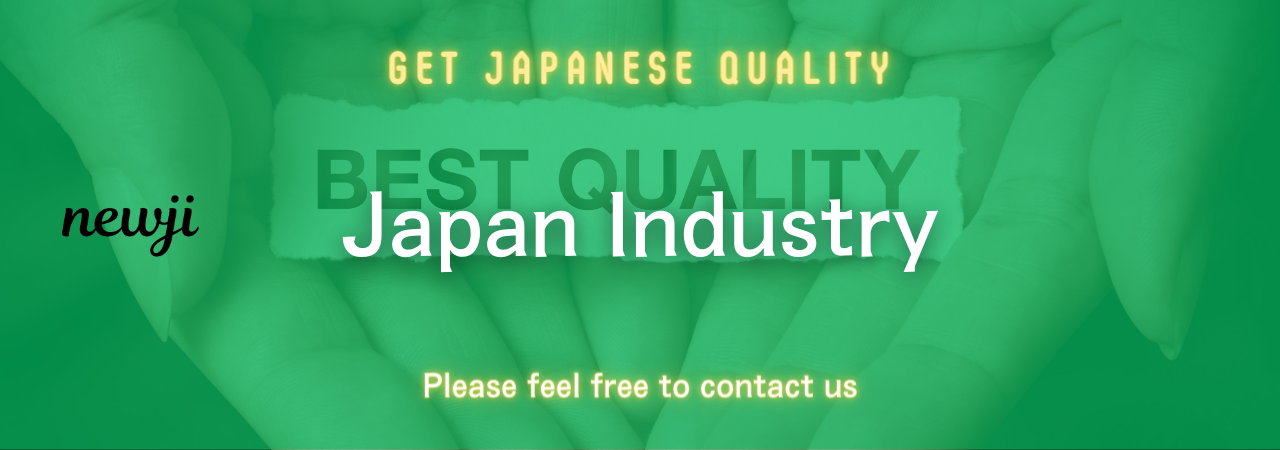
目次
Understanding the Coordination Process
In the world of manufacturing, seamless coordination between production sites and suppliers is crucial for efficiency and success.
The purchasing department plays a pivotal role in facilitating this coordination process.
This department acts as a bridge, ensuring that the needs of the manufacturing sites are met while also maintaining strong relationships with suppliers.
A well-structured coordination process helps prevent delays and ensures the delivery of quality products.
The Role of the Purchasing Department
The purchasing department is often considered the heart of the coordination process between manufacturing sites and suppliers.
Their main responsibility is to procure the right materials at the right time and at the right price.
This does not just involve buying materials but also strategizing and planning to ensure smooth operations.
Key functions of the purchasing department include:
Negotiating Contracts and Prices
One of the primary tasks of the purchasing department is to negotiate contracts and prices with suppliers.
This involves not only securing materials at a competitive price but also ensuring that the quality meets the standards required by the manufacturing sites.
Negotiations can be complex and require a deep understanding of market dynamics, supply chain logistics, and supplier capabilities.
Building Strong Supplier Relationships
Healthy and long-term relationships with reliable suppliers are vital for the smooth operation of manufacturing sites.
The purchasing department is responsible for nurturing these relationships through regular communication and collaboration.
This helps in building trust, which can lead to better terms, more efficient delivery schedules, and improved quality control.
Monitoring Supplier Performance
To ensure the reliability and consistency of supplies, the purchasing department monitors supplier performance closely.
This includes tracking delivery times, checking the quality of delivered goods, and ensuring that suppliers adhere to contractual agreements.
Feedback from manufacturing sites is crucial in assessing whether suppliers are meeting expectations.
Forecasting and Planning
Accurate forecasting and meticulous planning are essential tasks of the purchasing department.
They must anticipate future needs based on production schedules, historical data, and market trends.
Effective planning helps in avoiding stockouts, overstocking, and can significantly reduce costs.
Challenges in Coordination
While the purchasing department plays a vital role in the coordination process, there are several challenges that can arise:
Supply Chain Disruptions
Events such as natural disasters, political changes, or pandemics can disrupt supply chains.
The purchasing department must be agile and prepared with contingency plans to minimize the impact of such disruptions on manufacturing operations.
Communication Gaps
Miscommunications between the purchasing department, manufacturing sites, and suppliers can lead to delays, incorrect orders, or quality issues.
Implementing effective communication channels and systems is essential for smooth operations.
Cost Management
Balancing cost control with quality assurance is an ongoing challenge.
The purchasing department must constantly analyze ways to reduce costs without compromising on the quality and reliability of supplies.
Strategies for Effective Coordination
To enhance the coordination process between manufacturing sites and suppliers, certain strategies can be implemented:
Implementing Technology
Using technology such as Enterprise Resource Planning (ERP) systems can greatly improve coordination.
These systems provide real-time data, streamline procurement processes, and improve communication across all parties involved.
Enhancing Communication
Regular meetings, updates, and feedback sessions between the purchasing department, manufacturing sites, and suppliers can significantly reduce communication gaps.
Clear and transparent communication ensures everyone is on the same page and reduces the risk of misunderstandings.
Fostering Collaborative Partnerships
Viewing suppliers as partners rather than just vendors encourages collaboration and innovation.
The purchasing department can facilitate collaborative initiatives that drive mutual benefits, such as joint cost-saving projects or quality improvement plans.
Continuous Evaluation and Improvement
The coordination process should be regularly reviewed and improved.
Feedback from all stakeholders should be gathered and analyzed to identify areas for improvement.
This continuous evaluation helps in adapting strategies that meet the evolving needs of manufacturing sites and suppliers.
Conclusion
The coordination process between manufacturing sites and suppliers is a complex but crucial task, primarily driven by the purchasing department.
By understanding their roles, tackling challenges proactively, and implementing effective strategies, manufacturing operations can run smoothly and efficiently.
Ensuring the right materials are available at the right time allows production sites to meet their targets, maintain product quality, and satisfy customer demands.
資料ダウンロード
QCD調達購買管理クラウド「newji」は、調達購買部門で必要なQCD管理全てを備えた、現場特化型兼クラウド型の今世紀最高の購買管理システムとなります。
ユーザー登録
調達購買業務の効率化だけでなく、システムを導入することで、コスト削減や製品・資材のステータス可視化のほか、属人化していた購買情報の共有化による内部不正防止や統制にも役立ちます。
NEWJI DX
製造業に特化したデジタルトランスフォーメーション(DX)の実現を目指す請負開発型のコンサルティングサービスです。AI、iPaaS、および先端の技術を駆使して、製造プロセスの効率化、業務効率化、チームワーク強化、コスト削減、品質向上を実現します。このサービスは、製造業の課題を深く理解し、それに対する最適なデジタルソリューションを提供することで、企業が持続的な成長とイノベーションを達成できるようサポートします。
オンライン講座
製造業、主に購買・調達部門にお勤めの方々に向けた情報を配信しております。
新任の方やベテランの方、管理職を対象とした幅広いコンテンツをご用意しております。
お問い合わせ
コストダウンが利益に直結する術だと理解していても、なかなか前に進めることができない状況。そんな時は、newjiのコストダウン自動化機能で大きく利益貢献しよう!
(Β版非公開)