- お役立ち記事
- How to strengthen collaboration between manufacturing processes and procurement plans from the perspective of the purchasing department
How to strengthen collaboration between manufacturing processes and procurement plans from the perspective of the purchasing department
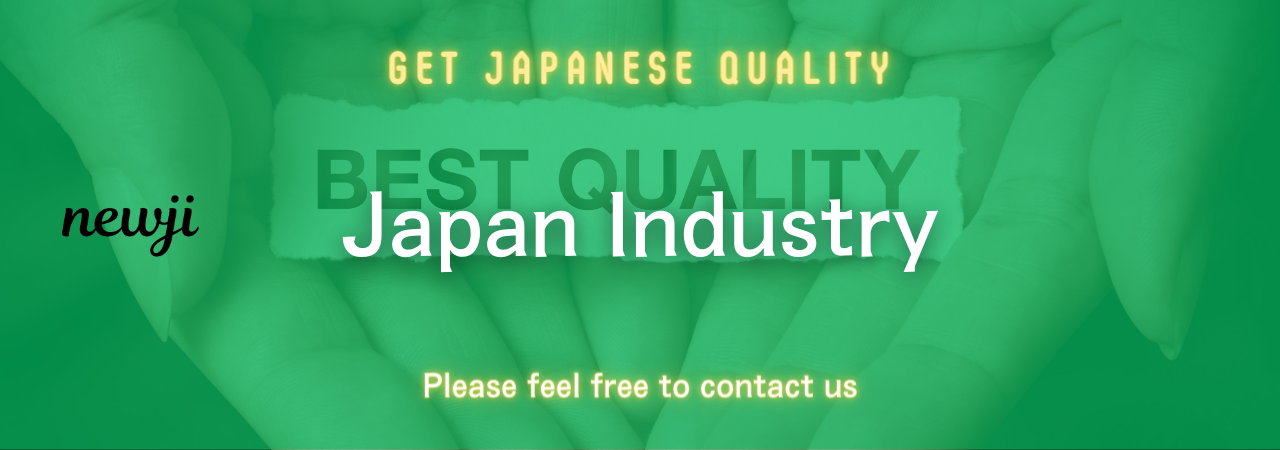
目次
Understanding the Importance of Collaboration
In the fast-paced world of manufacturing, collaboration between different departments is crucial to ensure seamless operations.
One of the most significant collaborations needed is between manufacturing processes and procurement plans, with the purchasing department often at the center.
Understanding the importance of this synergy is the first step toward strengthening it.
The purchasing department holds a pivotal role because it is responsible for securing the materials needed for production.
It ensures that quality materials are acquired timely and within budget.
When there is a discord between what the manufacturing team requires and what procurement plans provide, it can result in production delays, increased costs, and unsatisfied customers.
For a successful collaboration, it’s essential for the purchasing department to have complete visibility into manufacturing schedules and forecasted demands.
This allows them to plan procurement activities more accurately, minimizing the risks of overstocking or stockouts.
Setting Clear Communication Channels
To foster effective collaboration, establishing clear communication channels between the purchasing department and manufacturing teams is crucial.
Regular meetings and updates can help align procurement plans with manufacturing needs.
These meetings can be platforms for discussing current production requirements, future materials needed, and adjustments to procurement strategies based on production forecasts.
Utilizing technology, such as integrated communication tools and collaboration software, can also streamline the exchange of information.
Such platforms can provide real-time updates on inventory levels, production schedules, and procurement status, enabling teams to make informed and timely decisions.
Effective communication channels help ensure that any issues or changes in production plans are promptly addressed, allowing procurement teams to adapt their strategies quickly and efficiently.
Leveraging Technology for Better Alignment
Incorporating advanced technologies can significantly enhance the collaboration between manufacturing processes and procurement plans.
Enterprise Resource Planning (ERP) systems, for example, can provide a centralized database where all departments can access relevant information.
Having immediate access to this data allows the purchasing department to forecast the materials needed accurately and plan procurement activities accordingly.
Another valuable technology is Supply Chain Management (SCM) software, which provides tools for inventory management, supplier management, and demand forecasting.
These technologies can help the purchasing department to visualize the entire supply chain, assess potential risks, and adjust their strategies in response to any changes in production demands.
Deploying such technology ensures that all stakeholders are working from the same data, reducing misunderstandings and enhancing collaboration.
Building Strategic Supplier Partnerships
Strong relationships with suppliers are vital for improving collaboration between manufacturing processes and procurement plans.
Having a reliable network of suppliers who understand the production requirements can facilitate more efficient procurement processes.
To build these relationships, the purchasing department should focus on open communication, sharing long-term production plans and needs with their suppliers.
Such transparency can help suppliers adjust their operations to meet these demands more effectively.
Negotiating favorable agreements that allow flexibility, such as volume discounts and priority delivery, can also be beneficial.
These strategic relationships can provide the procurement team with more reliable sources of materials, reducing the likelihood of disruptions in the manufacturing process.
Implementing Cross-Departmental Training
To bridge any gaps between manufacturing and procurement, implementing cross-departmental training can be incredibly beneficial.
This training involves providing the purchasing team with insights into the manufacturing processes and vice versa.
Understanding the specific needs and challenges faced by each department can lead to more empathetic collaboration and problem-solving.
Such training can involve workshops or rotational programs where team members spend time in different departments.
This exposure can help both teams appreciate the interconnectedness of their roles and the importance of their collaboration.
Furthermore, this approach can foster a culture of continuous improvement and innovation, as team members can bring fresh insights back to their departments.
Evaluating and Refining Procurement Strategies
To ensure the collaboration remains effective, evaluating and refining procurement strategies regularly is crucial.
The purchasing department should continuously assess their strategies against key performance indicators such as lead times, quality of materials received, and inventory levels.
Feedback from the manufacturing team should be solicited regularly to identify any areas for improvement.
Use this feedback to modify procurement processes, enhancing adaptability to fluctuating production requirements.
Refining procurement strategies based on actual performance and production demand ensures the purchasing department’s actions are aligned with the overall manufacturing goals.
Creating a Collaborative Culture
Cultivating a culture of collaboration throughout the organization is essential for strengthening the connection between manufacturing and procurement.
Encouraging openness and mutual respect among team members can build a more cohesive work environment.
Executives and managers should lead by example, promoting collaboration through their actions and policies.
Recognizing and rewarding team efforts that successfully integrate manufacturing and procurement processes can also motivate employees to strive for continued improvement and collaboration.
Incorporating team-building activities and cross-functional projects can further reinforce a sense of unity and teamwork among departments.
The Path Forward
Strengthening the collaboration between manufacturing processes and procurement plans from the purchasing department’s perspective requires intentional strategies and a commitment to the organizational goals.
By focusing on clear communication, leveraging technology, building strong supplier relationships, implementing cross-departmental training, refining procurement strategies, and fostering a collaborative culture, companies can enhance their efficiency and competitiveness in the market.
This investment in collaboration not only supports the seamless operation of manufacturing processes but also plays a crucial role in meeting customer expectations, reducing costs, and increasing overall productivity.
As these departments work more cohesively, the company can achieve its production goals more effectively, ensuring continued success in the industry.
資料ダウンロード
QCD調達購買管理クラウド「newji」は、調達購買部門で必要なQCD管理全てを備えた、現場特化型兼クラウド型の今世紀最高の購買管理システムとなります。
ユーザー登録
調達購買業務の効率化だけでなく、システムを導入することで、コスト削減や製品・資材のステータス可視化のほか、属人化していた購買情報の共有化による内部不正防止や統制にも役立ちます。
NEWJI DX
製造業に特化したデジタルトランスフォーメーション(DX)の実現を目指す請負開発型のコンサルティングサービスです。AI、iPaaS、および先端の技術を駆使して、製造プロセスの効率化、業務効率化、チームワーク強化、コスト削減、品質向上を実現します。このサービスは、製造業の課題を深く理解し、それに対する最適なデジタルソリューションを提供することで、企業が持続的な成長とイノベーションを達成できるようサポートします。
オンライン講座
製造業、主に購買・調達部門にお勤めの方々に向けた情報を配信しております。
新任の方やベテランの方、管理職を対象とした幅広いコンテンツをご用意しております。
お問い合わせ
コストダウンが利益に直結する術だと理解していても、なかなか前に進めることができない状況。そんな時は、newjiのコストダウン自動化機能で大きく利益貢献しよう!
(Β版非公開)