- お役立ち記事
- “Revolutionizing Factory Layout: Unveiling the Secrets of Japanese Manufacturing Success”
“Revolutionizing Factory Layout: Unveiling the Secrets of Japanese Manufacturing Success”
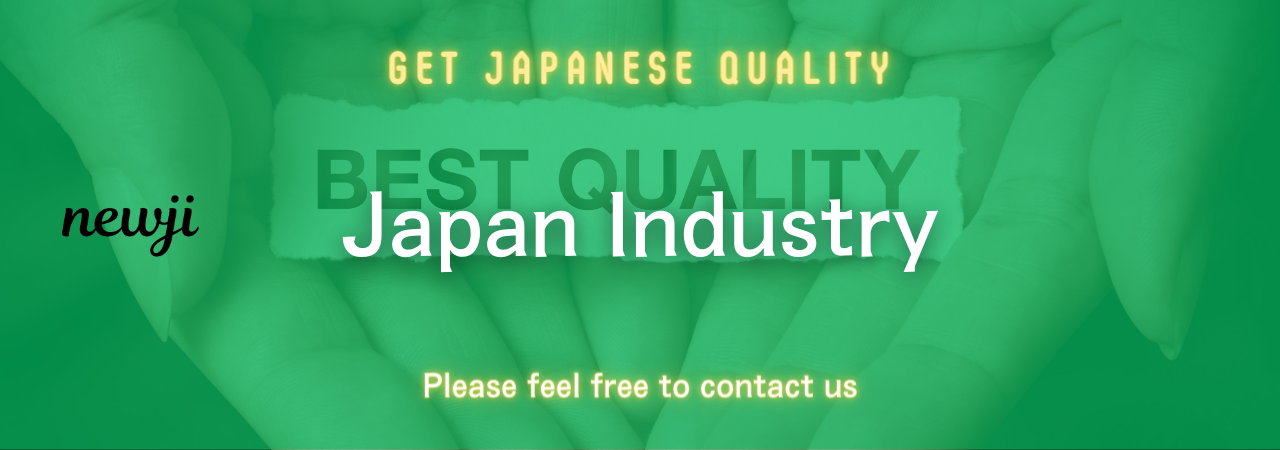
目次
Introduction to Japanese Manufacturing Success
Japanese manufacturing has long been admired for its efficiency, quality, and innovation.
Central to this success is the strategic layout of factories.
A well-designed factory layout is crucial for optimizing workflows, reducing waste, and enhancing productivity.
This article explores the secrets behind Japanese factory layouts and how they revolutionize manufacturing processes.
Through procurement and purchasing insights, we delve into best practices, supplier negotiations, and market conditions that contribute to Japan’s manufacturing prowess.
The Fundamentals of Factory Layout Design
A factory layout refers to the arrangement of machinery, equipment, and workstations within a manufacturing facility.
The primary goal is to create an efficient workflow that minimizes waste and maximizes productivity.
Japanese manufacturing emphasizes the importance of layout in achieving these objectives.
Several key principles guide the design of an effective factory layout.
Lean Manufacturing Principles
Lean manufacturing is at the heart of Japanese factory design.
It focuses on eliminating waste (muda) and optimizing processes.
By streamlining workflows, factories can achieve higher efficiency and lower costs.
Key elements include just-in-time production, continuous improvement (kaizen), and respect for people.
Flexibility and Adaptability
Japanese factory layouts are designed to be flexible and adaptable to changing production needs.
This allows manufacturers to swiftly respond to market demands and technological advancements.
Modular designs and multi-functional workstations are common features.
Flexibility also supports customization and small-batch production without significant downtime.
Flow Efficiency
Ensuring smooth material flow is essential in Japanese manufacturing.
Factory layouts aim to reduce bottlenecks and ensure that materials move seamlessly from one stage to the next.
This involves strategic placement of equipment and workers to facilitate efficient movement.
Effective flow reduces lead times and enhances overall production speed.
Advantages of Japanese Factory Layouts
Japanese factory layouts offer numerous benefits that contribute to their manufacturing success.
Understanding these advantages can help other businesses implement similar strategies.
Enhanced Productivity
Optimized layouts lead to higher productivity levels.
Efficient workflows mean less time is wasted, and resources are utilized effectively.
This results in increased output without the need for additional resources.
Improved Quality Control
Japanese manufacturing places a strong emphasis on quality.
Well-designed layouts facilitate better monitoring and control of production processes.
This ensures that quality standards are consistently met and maintained.
Cost Efficiency
By minimizing waste and optimizing resource use, Japanese factory layouts help reduce operational costs.
Efficient layouts mean lower energy consumption, reduced material waste, and fewer delays.
These cost savings contribute to competitive pricing and higher profit margins.
Employee Satisfaction and Engagement
A thoughtful factory layout can enhance the working environment for employees.
Ergonomic designs and efficient workflows reduce physical strain and improve job satisfaction.
Happy and engaged employees are more productive and contribute positively to the workplace culture.
Challenges and Disadvantages
While Japanese factory layouts offer many benefits, there are also challenges and potential drawbacks.
Initial Investment
Implementing a highly efficient factory layout often requires significant upfront investment.
Costly machinery, advanced technology, and specialized training can be barriers for some companies.
However, the long-term benefits typically outweigh the initial expenses.
Complexity in Design
Creating an optimal layout involves detailed planning and expertise.
The complexity of designing a layout that meets all efficiency and flexibility requirements can be daunting.
Mistakes in the design phase can lead to inefficiencies and increased costs.
Resistance to Change
Introducing new layouts and processes may face resistance from employees accustomed to existing systems.
Change management is crucial to ensure smooth transitions and buy-in from the workforce.
Dependency on Suppliers
Efficient layouts often rely on just-in-time procurement, making manufacturers vulnerable to supplier disruptions.
Maintaining strong supplier relationships and contingency plans is essential to mitigate this risk.
Supplier Negotiation Techniques in Japanese Manufacturing
Successful procurement and purchasing are integral to Japanese factory layouts.
Negotiating effectively with suppliers ensures timely delivery of quality materials and components.
Japanese manufacturing employs several negotiation techniques that contribute to their success.
Building Long-Term Relationships
Japanese companies prioritize long-term relationships with suppliers.
Trust and mutual respect are foundational elements in these partnerships.
Long-term relationships lead to better cooperation, reliability, and collaboration on quality improvements.
Collaborative Problem Solving
Rather than adopting an adversarial approach, Japanese manufacturers engage in collaborative problem solving with suppliers.
This approach fosters a sense of partnership and shared responsibility for resolving issues.
Collaborative solutions enhance efficiency and quality across the supply chain.
Mutual Benefits
Negotiations focus on creating win-win scenarios where both parties benefit.
This ensures sustained partnerships and encourages suppliers to invest in improving their capabilities.
Mutual benefits lead to more stable and reliable supply chains.
Quality Emphasis
Japanese manufacturers maintain high standards for quality and communicate these expectations clearly to suppliers.
Negotiations often include agreements on quality metrics, inspection processes, and continuous improvement plans.
This focus on quality ensures that suppliers align with the manufacturer’s standards.
Market Conditions and Their Impact
Understanding market conditions is vital for effective procurement and purchasing strategies.
Japanese manufacturers are adept at navigating varying market dynamics to maintain their competitive edge.
Supply Chain Resilience
Market volatility can disrupt supply chains, impacting factory operations.
Japanese manufacturers build resilience by diversifying suppliers and maintaining strategic inventories.
This approach helps mitigate risks associated with market fluctuations and ensures continuity.
Technological Advancements
Staying abreast of technological advancements is crucial in a competitive market.
Japanese manufacturers invest in automation, robotics, and digital technologies to enhance efficiency.
Adapting to new technologies allows for continuous improvement and innovation in factory layouts.
Globalization and Localization
Global market expansion requires manufacturers to adapt to different regional demands and regulations.
Japanese factories often incorporate localization strategies to cater to specific markets while maintaining global standards.
Balancing globalization and localization ensures broader market reach and compliance with local requirements.
Economic and Political Factors
Economic stability and favorable political climates support manufacturing operations.
Japanese manufacturers monitor economic indicators and political developments to make informed procurement decisions.
Proactive strategies help navigate challenges such as trade tariffs, currency fluctuations, and regulatory changes.
Best Practices in Japanese Factory Layouts
Adopting best practices from Japanese manufacturing can significantly enhance factory efficiency and productivity.
Here are some key strategies to consider.
5S Methodology
The 5S methodology (Sort, Set in order, Shine, Standardize, Sustain) is a cornerstone of Japanese factory layout design.
It emphasizes organization, cleanliness, and standardization to create a disciplined and efficient workspace.
Implementing 5S leads to improved workflows and reduced waste.
Kanban Systems
Kanban is a visual scheduling system that manages production processes.
It helps in maintaining just-in-time inventory levels, reducing excess stock and minimizing storage space.
Kanban systems enhance communication and coordination within the production line.
Cellular Manufacturing
Cellular manufacturing organizes workstations into cells based on product families.
This setup facilitates smoother workflows, reduces movement, and enhances specialization.
Cells promote teamwork and improve overall production efficiency.
Jidoka (Automation with a Human Touch)
Jidoka integrates automation with human oversight to ensure quality and efficiency.
Machines are designed to detect defects and halt production, allowing workers to address issues promptly.
This approach prevents the propagation of defects and maintains high quality standards.
Continuous Improvement (Kaizen)
Kaizen, or continuous improvement, is ingrained in Japanese manufacturing culture.
Employees at all levels are encouraged to identify and implement improvements.
This fosters a culture of innovation and constant enhancement of processes.
Implementing Japanese Layout Strategies in Your Factory
Adopting Japanese factory layout strategies requires careful planning and execution.
Here are steps to effectively implement these practices in your manufacturing facility.
Assess Current Layout and Processes
Begin by evaluating your existing factory layout and workflows.
Identify areas of waste, inefficiency, and bottlenecks.
Conduct a thorough analysis to understand the strengths and weaknesses of your current setup.
Define Objectives and Goals
Clearly outline the objectives you aim to achieve with the new layout.
Common goals include increasing productivity, reducing waste, enhancing quality, and improving employee satisfaction.
Setting specific, measurable goals helps guide the design process.
Involve Stakeholders
Engage employees, managers, and other stakeholders in the layout planning process.
Their insights and feedback are invaluable for identifying practical solutions and ensuring buy-in.
Collaborative planning fosters a sense of ownership and commitment to the new layout.
Design the Layout Based on Lean Principles
Incorporate lean manufacturing principles into the layout design.
Focus on eliminating waste, optimizing workflows, and ensuring smooth material flow.
Consider implementing 5S, Kanban, and cellular manufacturing as part of the design.
Invest in Training and Development
Provide training to employees on the new layout and processes.
Educate them on lean principles, quality control, and continuous improvement techniques.
Well-trained staff are essential for the successful implementation and maintenance of the new layout.
Monitor and Adjust
Continuously monitor the performance of the new layout.
Use key performance indicators (KPIs) to assess productivity, quality, and efficiency.
Be prepared to make adjustments based on feedback and performance data to ensure ongoing improvement.
Case Studies of Japanese Manufacturing Layouts
Examining successful implementations of Japanese factory layouts provides valuable insights.
Here are a few notable case studies.
Toyota Production System (TPS)
The Toyota Production System is a benchmark for lean manufacturing.
TPS emphasizes just-in-time production, jidoka, and continuous improvement.
Its factory layout is designed to minimize waste, enhance flow, and ensure quality.
The success of TPS has inspired manufacturers worldwide to adopt similar strategies.
Panasonic’s Flexible Manufacturing
Panasonic employs flexible manufacturing layouts to adapt to varying product demands.
Their factories utilize modular workstations and advanced automation.
This flexibility allows Panasonic to efficiently produce a diverse range of electronic products while maintaining high quality.
Sony’s Lean Factory
Sony’s lean factory focuses on eliminating waste and optimizing processes.
Their layout incorporates cellular manufacturing and kanban systems to ensure efficient workflows.
Continuous improvement is a core aspect, with employees encouraged to suggest and implement enhancements.
The Role of Technology in Modern Factory Layouts
Advancements in technology play a crucial role in enhancing factory layouts.
Japanese manufacturers leverage cutting-edge technologies to maintain their competitive edge.
Automation and Robotics
Automation and robotics streamline production processes, reducing human error and increasing precision.
Robots handle repetitive and hazardous tasks, allowing workers to focus on more complex activities.
Integrating automation into the layout enhances efficiency and safety.
Internet of Things (IoT)
IoT connects machines and devices, enabling real-time monitoring and data analysis.
Factories can track production metrics, identify issues early, and optimize workflows.
IoT enhances visibility and control over the entire manufacturing process.
Artificial Intelligence (AI) and Machine Learning
AI and machine learning facilitate predictive maintenance and quality control.
They analyze data to forecast equipment failures and optimize maintenance schedules.
AI-driven insights help in making informed decisions to improve factory operations.
Digital Twin Technology
Digital twin technology creates virtual replicas of factory layouts and processes.
This allows for simulations and testing of layout changes before implementation.
Digital twins aid in identifying potential improvements and ensuring smooth transitions.
Future Trends in Factory Layouts
As technology and market dynamics evolve, factory layouts must adapt to stay competitive.
Japanese manufacturers are at the forefront of embracing future trends.
Sustainable Manufacturing
Sustainability is becoming increasingly important in manufacturing.
Future factory layouts will prioritize energy efficiency, waste reduction, and the use of eco-friendly materials.
Sustainable practices not only benefit the environment but also enhance brand reputation and compliance with regulations.
Smart Factories
Smart factories integrate advanced technologies like AI, IoT, and robotics to create highly automated and interconnected manufacturing environments.
These factories are capable of self-optimization, adaptability, and real-time decision-making.
Smart factory layouts enhance flexibility and responsiveness to changing market demands.
Human-Centric Design
Future layouts will focus more on human-centric design, ensuring that factory environments are safe, comfortable, and conducive to productivity.
Ergonomic workstations, collaborative spaces, and healthy work environments will become standard features.
Human-centric designs improve employee satisfaction and performance.
Global Collaboration
As manufacturing becomes more global, factory layouts will need to accommodate collaboration across different regions and cultures.
Integrated communication systems and standardized processes will facilitate seamless global operations.
Global collaboration enhances innovation and efficiency in factory layouts.
Conclusion
Japanese manufacturing success is deeply rooted in the strategic design of their factory layouts.
By embracing lean principles, fostering strong supplier relationships, leveraging advanced technologies, and continuously striving for improvement, Japanese manufacturers have set a benchmark in the industry.
Implementing these strategies can revolutionize factory layouts, leading to enhanced productivity, quality, and competitiveness.
Businesses worldwide can learn from Japanese practices to achieve sustainable manufacturing excellence.
資料ダウンロード
QCD調達購買管理クラウド「newji」は、調達購買部門で必要なQCD管理全てを備えた、現場特化型兼クラウド型の今世紀最高の購買管理システムとなります。
ユーザー登録
調達購買業務の効率化だけでなく、システムを導入することで、コスト削減や製品・資材のステータス可視化のほか、属人化していた購買情報の共有化による内部不正防止や統制にも役立ちます。
NEWJI DX
製造業に特化したデジタルトランスフォーメーション(DX)の実現を目指す請負開発型のコンサルティングサービスです。AI、iPaaS、および先端の技術を駆使して、製造プロセスの効率化、業務効率化、チームワーク強化、コスト削減、品質向上を実現します。このサービスは、製造業の課題を深く理解し、それに対する最適なデジタルソリューションを提供することで、企業が持続的な成長とイノベーションを達成できるようサポートします。
オンライン講座
製造業、主に購買・調達部門にお勤めの方々に向けた情報を配信しております。
新任の方やベテランの方、管理職を対象とした幅広いコンテンツをご用意しております。
お問い合わせ
コストダウンが利益に直結する術だと理解していても、なかなか前に進めることができない状況。そんな時は、newjiのコストダウン自動化機能で大きく利益貢献しよう!
(Β版非公開)