- お役立ち記事
- “Revolutionizing Japanese Manufacturing: The Pivotal Role of Digital Design”
“Revolutionizing Japanese Manufacturing: The Pivotal Role of Digital Design”
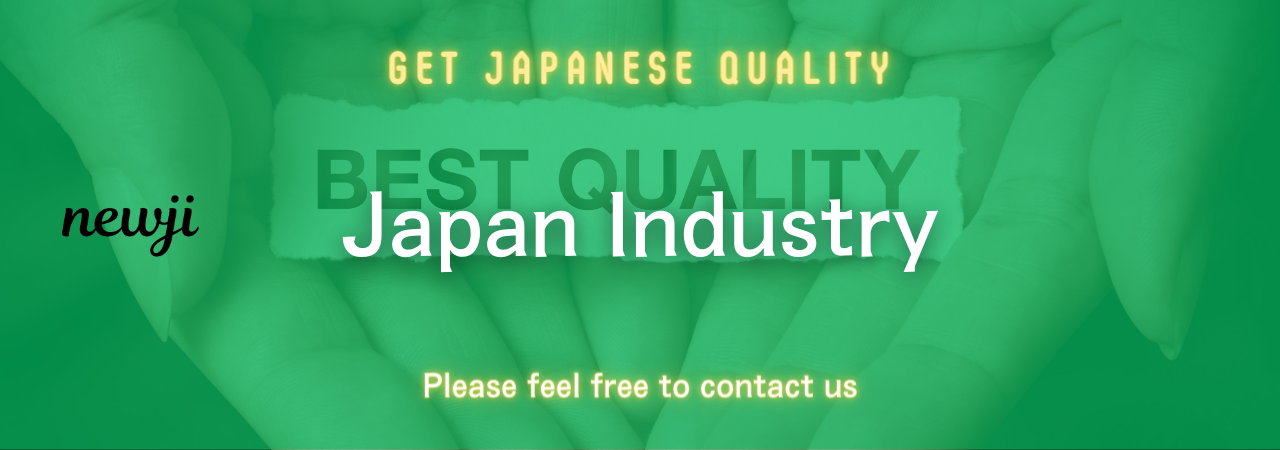
目次
Introduction to the Transformation of Japanese Manufacturing
Japanese manufacturing has long been synonymous with precision, efficiency, and quality. Over the past few decades, the industry has undergone significant transformations, adapting to global market demands and technological advancements. At the forefront of this revolution is digital design, a pivotal element that has redefined traditional manufacturing processes. This article explores the integral role of digital design in revolutionizing Japanese manufacturing, delving into its practical applications, advantages and disadvantages, supplier negotiation techniques, market conditions, and best practices from the perspective of procurement and purchasing professionals.
The Evolution of Digital Design in Manufacturing
Digital design refers to the use of computer-based tools and technologies to create, modify, analyze, and optimize manufacturing processes and products. In the context of Japanese manufacturing, digital design has evolved from simple computer-aided design (CAD) systems to more sophisticated platforms that integrate various aspects of production, supply chain management, and quality control.
From CAD to Comprehensive Digital Ecosystems
Initially, CAD systems were primarily used for drafting and designing individual components. However, the integration of Computer-Aided Manufacturing (CAM) and Computer-Aided Engineering (CAE) has allowed manufacturers to simulate and optimize production processes virtually. This evolution has led to the development of comprehensive digital ecosystems that encompass everything from design and prototyping to production and distribution.
The Role of Industry 4.0 and IoT
Industry 4.0, characterized by the integration of cyber-physical systems, the Internet of Things (IoT), and cloud computing, has further propelled digital design in manufacturing. In Japan, the adoption of these technologies has enabled real-time data collection, predictive maintenance, and enhanced automation, leading to more responsive and flexible manufacturing systems.
Advantages of Digital Design in Japanese Manufacturing
The incorporation of digital design into Japanese manufacturing processes offers numerous benefits that enhance both efficiency and competitiveness.
Enhanced Precision and Quality Control
Digital design tools enable manufacturers to achieve higher precision in product design and production. Advanced simulations and modeling allow for the detection and correction of potential defects early in the design phase, reducing errors and improving the overall quality of the final product.
Increased Flexibility and Customization
With digital design, manufacturers can easily modify designs to meet specific customer requirements without significant retooling or delays. This flexibility facilitates mass customization, allowing companies to cater to diverse market needs while maintaining efficiency.
Improved Collaboration and Communication
Digital platforms facilitate better collaboration among different departments and with external partners. Shared digital models and data ensure that all stakeholders have access to the latest information, reducing miscommunication and streamlining the decision-making process.
Cost Efficiency and Resource Optimization
By simulating production processes and optimizing designs digitally, manufacturers can identify the most cost-effective materials and methods. This leads to reduced waste, lower production costs, and more efficient use of resources.
Disadvantages and Challenges of Implementing Digital Design
Despite its numerous advantages, the implementation of digital design in Japanese manufacturing is not without challenges.
High Initial Investment
Adopting advanced digital design tools requires significant upfront investment in software, hardware, and training. For smaller manufacturers, this can be a substantial barrier to entry.
Integration with Legacy Systems
Many Japanese manufacturers operate with legacy systems that may not be compatible with modern digital design tools. Integrating new technologies with existing infrastructure can be complex and time-consuming.
Cybersecurity Risks
As manufacturing processes become more digitized and connected, the risk of cyberattacks increases. Protecting sensitive design data and maintaining the integrity of manufacturing systems is a critical concern.
Skill Gaps and Training Needs
The transition to digital design requires new skills and competencies. Ensuring that employees are adequately trained to use digital tools effectively is essential for successful implementation.
Supplier Negotiation Techniques in the Digital Era
In the realm of procurement and purchasing, digital design has transformed supplier relationships and negotiation strategies. Japanese manufacturers often rely on long-term partnerships with suppliers, emphasizing quality and reliability. Digital design plays a crucial role in these relationships by enhancing transparency and collaboration.
Leveraging Digital Platforms for Transparency
Digital design tools facilitate real-time sharing of design specifications, production schedules, and quality standards with suppliers. This transparency helps in building trust and ensures that suppliers are aligned with the manufacturer’s expectations.
Data-Driven Negotiations
Access to comprehensive data allows procurement professionals to make informed decisions during negotiations. Analyzing production costs, lead times, and quality metrics enables more effective bargaining and contract negotiations.
Collaborative Design and Development
Engaging suppliers early in the design process fosters collaboration and innovation. Joint development initiatives can lead to improved product features and better alignment of production capabilities with design requirements.
Performance-Based Contracts
Digital design facilitates the establishment of performance-based contracts that tie supplier compensation to specific quality and delivery metrics. This approach incentivizes suppliers to maintain high standards and meet performance targets consistently.
Market Conditions Influencing Digital Design Adoption
The adoption of digital design in Japanese manufacturing is influenced by various market conditions that shape the industry’s direction.
Global Competition
Japanese manufacturers face intense competition from global players, particularly from countries with rapidly advancing manufacturing technologies. To maintain their competitive edge, Japanese companies must continuously innovate and adopt cutting-edge digital design tools.
Demand for Customization
The increasing demand for customized products requires manufacturers to adopt flexible and responsive design and production processes. Digital design enables rapid adjustments to product specifications, meeting diverse customer needs efficiently.
Supply Chain Complexity
Global supply chains are becoming more complex, with multiple suppliers and partners across different regions. Digital design helps in managing this complexity by providing a centralized platform for design data and facilitating seamless collaboration among supply chain partners.
Sustainability and Environmental Regulations
Growing emphasis on sustainability and stringent environmental regulations compel manufacturers to optimize resource usage and minimize waste. Digital design tools assist in creating more sustainable products and efficient production processes, aligning with environmental standards.
Best Practices for Implementing Digital Design in Manufacturing
Successful implementation of digital design in Japanese manufacturing requires adherence to best practices that address both technical and organizational aspects.
Comprehensive Planning and Strategy
Developing a clear digital transformation strategy is crucial. This involves assessing current capabilities, identifying goals, and outlining the steps needed to integrate digital design tools effectively.
Employee Training and Development
Investing in training programs ensures that employees are proficient in using digital design tools. Continuous learning initiatives help in keeping the workforce updated with the latest technologies and methodologies.
Integration with Existing Systems
Seamless integration of digital design tools with existing manufacturing systems enhances overall efficiency. Utilizing middleware and APIs can facilitate communication between different software platforms, ensuring data consistency and reducing operational silos.
Emphasizing Cybersecurity
Implementing robust cybersecurity measures is essential to protect sensitive design data and safeguard manufacturing systems from potential threats. Regular security audits and updates help in maintaining a secure digital environment.
Fostering Collaborative Culture
Encouraging collaboration across departments and with external partners enhances the effectiveness of digital design initiatives. A culture that values open communication and teamwork supports the successful adoption of digital tools.
Continuous Improvement and Feedback Loops
Establishing feedback mechanisms allows for the continuous refinement of digital design processes. Regularly evaluating performance and incorporating feedback from stakeholders helps in optimizing workflows and achieving better outcomes.
The Future of Digital Design in Japanese Manufacturing
As technology continues to advance, digital design will play an increasingly critical role in shaping the future of Japanese manufacturing. Emerging trends and innovations are set to further enhance the capabilities of digital design, driving efficiency, innovation, and competitiveness.
Artificial Intelligence and Machine Learning
AI and machine learning are poised to revolutionize digital design by enabling predictive analytics, automated design optimization, and intelligent decision-making. These technologies can help manufacturers anticipate market trends, optimize resource allocation, and improve product innovation.
Virtual and Augmented Reality
Virtual and augmented reality technologies offer immersive design experiences, allowing manufacturers to visualize and interact with products in a virtual environment. This enhances the design process, facilitates better collaboration, and reduces the time and cost associated with physical prototyping.
Additive Manufacturing and 3D Printing
Additive manufacturing, particularly 3D printing, complements digital design by enabling the rapid production of complex components directly from digital models. This reduces lead times, minimizes material waste, and allows for greater design flexibility.
Blockchain for Supply Chain Transparency
Blockchain technology can enhance supply chain transparency and traceability, integrating seamlessly with digital design tools. This ensures the authenticity of design data, secures transaction records, and facilitates trust among supply chain partners.
Sustainable and Eco-Friendly Design
The focus on sustainability will drive the adoption of digital design practices that prioritize eco-friendly materials and processes. Digital tools can aid in designing products that are easier to recycle, consume less energy, and have a lower environmental impact.
Case Studies: Successful Implementation of Digital Design in Japanese Manufacturing
Examining real-world examples of Japanese manufacturers that have successfully integrated digital design into their operations provides valuable insights and best practices.
Case Study 1: Toyota Motor Corporation
Toyota has been a pioneer in adopting digital design and Industry 4.0 technologies. By integrating digital design tools with their Toyota Production System (TPS), the company has achieved remarkable efficiency and quality in their manufacturing processes. Digital twins, a virtual replica of physical products and processes, enable Toyota to simulate and optimize production workflows, reducing downtime and enhancing productivity.
Case Study 2: Panasonic Corporation
Panasonic utilizes advanced digital design tools to innovate its consumer electronics and automotive components. By leveraging AI-driven design optimization and collaborative platforms, Panasonic has improved product quality and accelerated time-to-market. The company’s focus on digital integration has also strengthened its supplier relationships, ensuring consistent quality and reliability.
Case Study 3: Hitachi Aerospace
Hitachi Aerospace employs digital design and additive manufacturing to produce complex aerospace components. The use of 3D printing allows for the creation of lightweight and intricate parts that meet stringent aerospace standards. Digital design has enabled Hitachi to enhance the performance and durability of its products while reducing material costs and production times.
Conclusion: Embracing Digital Design for Future Growth
Digital design stands as a transformative force in Japanese manufacturing, driving innovation, efficiency, and competitiveness. By embracing digital design tools and best practices, Japanese manufacturers can navigate the complexities of the modern market, meet evolving customer demands, and maintain their reputation for quality and precision. While challenges such as high initial investments and cybersecurity risks exist, the benefits of enhanced precision, flexibility, and collaboration make digital design an indispensable element of contemporary manufacturing strategies. As technologies continue to advance, the pivotal role of digital design will only grow, cementing its place at the heart of Japan’s manufacturing excellence.
資料ダウンロード
QCD調達購買管理クラウド「newji」は、調達購買部門で必要なQCD管理全てを備えた、現場特化型兼クラウド型の今世紀最高の購買管理システムとなります。
ユーザー登録
調達購買業務の効率化だけでなく、システムを導入することで、コスト削減や製品・資材のステータス可視化のほか、属人化していた購買情報の共有化による内部不正防止や統制にも役立ちます。
NEWJI DX
製造業に特化したデジタルトランスフォーメーション(DX)の実現を目指す請負開発型のコンサルティングサービスです。AI、iPaaS、および先端の技術を駆使して、製造プロセスの効率化、業務効率化、チームワーク強化、コスト削減、品質向上を実現します。このサービスは、製造業の課題を深く理解し、それに対する最適なデジタルソリューションを提供することで、企業が持続的な成長とイノベーションを達成できるようサポートします。
オンライン講座
製造業、主に購買・調達部門にお勤めの方々に向けた情報を配信しております。
新任の方やベテランの方、管理職を対象とした幅広いコンテンツをご用意しております。
お問い合わせ
コストダウンが利益に直結する術だと理解していても、なかなか前に進めることができない状況。そんな時は、newjiのコストダウン自動化機能で大きく利益貢献しよう!
(Β版非公開)