- お役立ち記事
- Revolutionizing Japanese Manufacturing: The Impact of Metropolitan Area Networks on Smart Factories
Revolutionizing Japanese Manufacturing: The Impact of Metropolitan Area Networks on Smart Factories
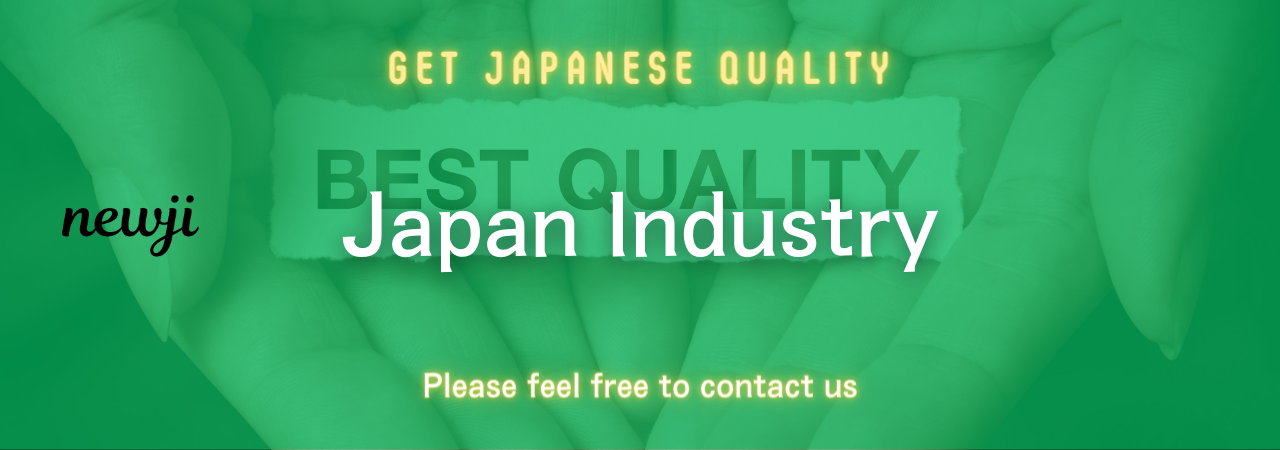
目次
The Evolution of Metropolitan Area Networks in Japanese Manufacturing
Metropolitan Area Networks (MANs) have become a cornerstone in the transformation of Japanese manufacturing.
Initially designed to facilitate communication within urban areas, MANs have evolved to support the complex demands of modern smart factories.
The integration of MANs into manufacturing processes signifies a shift towards more connected and efficient production environments.
This evolution reflects Japan’s commitment to maintaining its competitive edge in the global manufacturing sector.
Impact of MANs on Smart Factories
Enhanced Connectivity and Data Exchange
MANs provide robust connectivity solutions that enable seamless data exchange across various departments within a factory.
This connectivity ensures that information flows smoothly from the production floor to management, facilitating real-time decision-making processes.
The ability to share data instantaneously enhances collaboration and coordination, leading to more synchronized manufacturing operations.
Real-Time Monitoring and Control
With MANs, smart factories can implement real-time monitoring systems that track machinery performance and production metrics.
This real-time data allows for immediate identification of issues, minimizing downtime and maintaining steady production levels.
Furthermore, remote control capabilities enabled by MANs ensure that factory operations can be managed efficiently, even from distant locations.
Integration of IoT Devices
The Internet of Things (IoT) plays a significant role in modern manufacturing, and MANs facilitate the integration of IoT devices into production systems.
Connected sensors and devices collect valuable data that can be analyzed to optimize manufacturing processes.
This integration leads to predictive maintenance, reduced waste, and enhanced product quality, all of which contribute to the overall efficiency of smart factories.
Advantages of Implementing MANs in Manufacturing
Improved Operational Efficiency
MANs streamline communication channels, reducing delays and bottlenecks in manufacturing processes.
Efficient data flow ensures that operations are well-coordinated, leading to smoother workflows and increased productivity.
The automation capabilities supported by MANs further enhance operational efficiency by minimizing manual interventions.
Enhanced Quality Control
With real-time data monitoring, manufacturers can maintain stringent quality control measures.
Any deviations from quality standards can be detected and addressed promptly, ensuring that the final products meet the desired specifications.
This proactive approach to quality control reduces the incidence of defects and enhances customer satisfaction.
Cost Savings and Resource Optimization
The efficiency gains from implementing MANs translate into significant cost savings.
Optimized resource allocation ensures that materials and labor are utilized effectively, reducing unnecessary expenditures.
Additionally, predictive maintenance minimizes equipment downtime, further contributing to cost reduction and overall profitability.
Challenges and Disadvantages
High Initial Investment
Implementing MANs requires substantial upfront investments in infrastructure, technology, and training.
For many manufacturers, especially small and medium-sized enterprises, the financial burden can be a significant barrier to adoption.
However, the long-term benefits often justify the initial costs, leading to sustainable growth and competitiveness.
Cybersecurity Concerns
As MANs increase connectivity, they also expose factories to potential cyber threats.
Protecting sensitive manufacturing data and ensuring the integrity of production systems is paramount.
Manufacturers must invest in robust cybersecurity measures to safeguard their operations against cyber-attacks and data breaches.
Complexity of Integration
Integrating MANs into existing manufacturing systems can be complex and challenging.
Compatibility issues with legacy equipment and the need for specialized expertise can complicate the implementation process.
Careful planning and phased integration strategies are essential to address these challenges effectively.
Procurement and Purchasing in the Era of MANs
The adoption of MANs significantly impacts procurement and purchasing strategies within manufacturing firms.
Sourcing the necessary components and technologies for MAN implementation requires a strategic approach to supplier selection and management.
Procurement teams must evaluate suppliers based on their ability to provide reliable, high-quality MAN solutions that align with the factory’s specific needs.
Supplier Negotiation Techniques
Building strong relationships with suppliers is crucial for successful MAN implementations.
Negotiation should focus on securing favorable terms, including competitive pricing, timely delivery, and ongoing support.
Leveraging technological advantages, such as bundling services or integrating advanced features, can also enhance negotiation outcomes and foster long-term partnerships.
Market Conditions Influenced by MANs
The implementation of MANs reshapes the manufacturing market by introducing advanced connectivity and automation capabilities.
Manufacturers equipped with MANs gain a competitive edge through enhanced efficiency and product quality, distinguishing themselves in the marketplace.
Moreover, the demand for advanced manufacturing solutions drives innovation and technological advancements, fostering a dynamic and evolving market landscape.
Best Practices for Implementing MANs in Smart Factories
Strategic Planning
Successful MAN implementation begins with comprehensive strategic planning that aligns with the factory’s long-term objectives.
This involves assessing current infrastructure, identifying areas for improvement, and outlining clear goals for connectivity and automation enhancements.
Employee Training and Development
Investing in employee training ensures that the workforce is equipped to operate and maintain MAN-integrated systems.
Training programs should focus on technical skills, data analysis, and cybersecurity awareness to maximize the benefits of MANs.
Continuous Monitoring and Optimization
Ongoing monitoring of MAN performance allows for the identification of potential issues and the optimization of network configurations.
Regular assessments and updates ensure that the MAN infrastructure remains robust, secure, and capable of supporting evolving manufacturing demands.
Future Trends and the Role of MANs
As technology continues to advance, MANs will play an increasingly vital role in the future of manufacturing.
Integration with artificial intelligence (AI) and machine learning will enable more sophisticated data analysis and predictive capabilities.
The expansion of 5G networks will further enhance connectivity speeds and reliability, supporting the growing number of connected devices within smart factories.
Additionally, sustainability initiatives will drive the development of green manufacturing practices, with MANs facilitating energy-efficient operations and resource management.
Conclusion
Metropolitan Area Networks have revolutionized Japanese manufacturing by enabling the development of smart factories characterized by enhanced connectivity, efficiency, and quality control.
While the implementation of MANs presents challenges such as high initial costs and cybersecurity risks, the long-term benefits of improved operational efficiency and competitive advantage are substantial.
By adopting best practices in strategic planning, supplier negotiation, and continuous optimization, manufacturers can successfully integrate MANs into their operations.
Looking ahead, the continued evolution of MAN technology will further transform manufacturing processes, ensuring that Japanese manufacturers remain at the forefront of innovation and global competitiveness.
資料ダウンロード
QCD調達購買管理クラウド「newji」は、調達購買部門で必要なQCD管理全てを備えた、現場特化型兼クラウド型の今世紀最高の購買管理システムとなります。
ユーザー登録
調達購買業務の効率化だけでなく、システムを導入することで、コスト削減や製品・資材のステータス可視化のほか、属人化していた購買情報の共有化による内部不正防止や統制にも役立ちます。
NEWJI DX
製造業に特化したデジタルトランスフォーメーション(DX)の実現を目指す請負開発型のコンサルティングサービスです。AI、iPaaS、および先端の技術を駆使して、製造プロセスの効率化、業務効率化、チームワーク強化、コスト削減、品質向上を実現します。このサービスは、製造業の課題を深く理解し、それに対する最適なデジタルソリューションを提供することで、企業が持続的な成長とイノベーションを達成できるようサポートします。
オンライン講座
製造業、主に購買・調達部門にお勤めの方々に向けた情報を配信しております。
新任の方やベテランの方、管理職を対象とした幅広いコンテンツをご用意しております。
お問い合わせ
コストダウンが利益に直結する術だと理解していても、なかなか前に進めることができない状況。そんな時は、newjiのコストダウン自動化機能で大きく利益貢献しよう!
(Β版非公開)