- お役立ち記事
- Inventory management and supplier collaboration methods to ensure stability of material supply
Inventory management and supplier collaboration methods to ensure stability of material supply
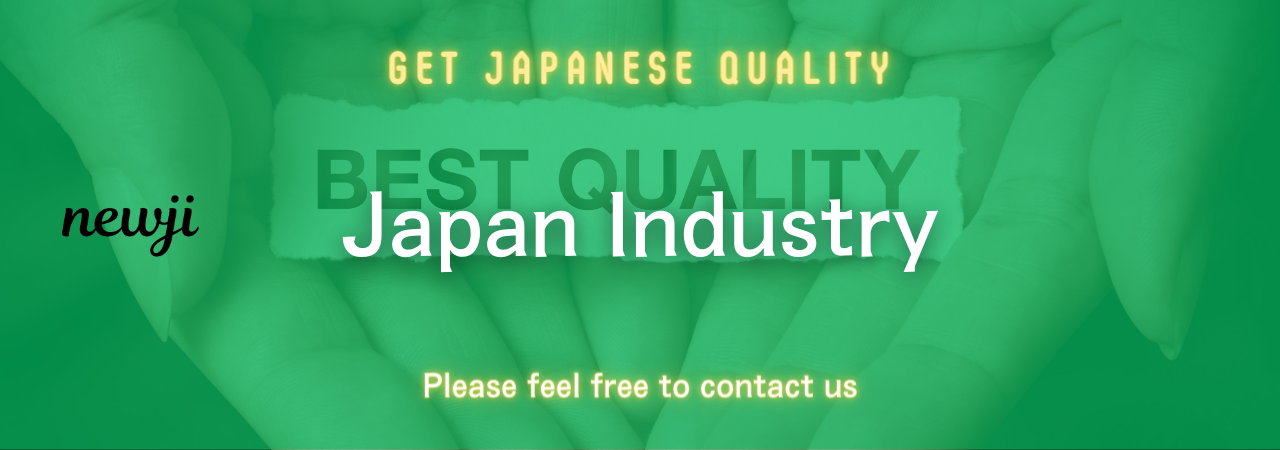
目次
Understanding Inventory Management
Inventory management is a crucial aspect of any business that deals with physical goods.
It involves the supervision of non-capitalized assets, or inventory, and stock items.
For companies, effective inventory management can mean the difference between thriving markets and lost sales.
Proper management involves balancing the costs of inventory with the benefits of having enough goods available for customers.
Businesses use inventory management to optimize their supply chain and enhance operational efficiency.
The main goal is to ensure that there is always enough stock to meet customer demands without overstocking, which can lead to high holding costs.
Too much inventory ties up company cash that could otherwise be invested back into the business.
On the other hand, too little inventory can lead to missed sales opportunities and unhappy customers.
The Role of Technology in Inventory Management
The development of technology has significantly improved the methods used for inventory management.
Modern systems allow businesses to keep track of stock amounts, predict ordering schedules, and identify trends that can help to optimize inventory levels.
Many businesses now leverage inventory management software that provides real-time data analytics to offer insights into stock levels, supply chain efficiency, and sales trends.
These systems often incorporate barcode scanning, radio-frequency identification (RFID), and automated ordering systems to minimize manual errors and streamline processes.
Moreover, technology helps in connecting inventory systems with e-commerce platforms, thus ensuring accurate stock levels are displayed to online customers.
This alignment of physical inventories with online interfaces is critical in multichannel retail environments.
Importance of Supplier Collaboration
Supplier collaboration is another key component in maintaining steady material supply.
By working closely with suppliers, businesses can ensure they receive the quality and quantity of goods needed on time.
Strong supplier relationships can lead to numerous benefits such as better pricing, priority customer service, and reliable supply chains.
Suppliers that are well-integrated into a business’s processes are more likely to go the extra mile during critical supply shortages, thereby minimizing the risk of stockouts.
Regular communication with suppliers allows businesses to negotiate terms that could include bulk discounts, dedicated production lines, or customized shipping options.
Moreover, during times of tight supply, strong collaboration means businesses can potentially influence how limited supplies are allocated.
Creating a Collaborative Supplier Environment
Building strong relational ties with suppliers requires effort and strategy from both parties involved.
It starts with open and honest communication to ensure that expectations for delivery timelines, quality standards, and pricing are understood and agreed upon.
Establishing a partnership rather than just a transactional relationship ensures mutual benefits.
Involving suppliers in planning processes can also add value, such as incorporating their insights into demand forecasting or capacity planning.
Using technology, platforms can be set up to enable better interaction between business and supplier.
Platforms that enable real-time data sharing can improve transparency, quickly highlight potential supply issues, and allow both parties to plan accordingly.
Periodic review meetings can help assess the performance of suppliers, with the chance to implement improvements based on feedback.
Such meetings can also be an avenue to discuss future plans and innovations, strengthening the partnership for mutual growth.
Strategies to Ensure Stability of Material Supply
Ensuring stability in material supply is essential for maintaining smooth business operations and customer satisfaction.
Demand Forecasting and Planning
Demand forecasting is key in predicting the amount of product that will be sold, allowing companies to plan their inventory accordingly.
Forecasting tools utilize historical data, market trends, and statistical algorithms to project customer demand.
Accurate demand planning ensures the right amount of stock is ordered and available, reducing the likelihood of both overstocking and stockouts.
Maintaining Safety Stock
Safety stock acts as a buffer in the event of unexpected disruptions in the supply chain or surges in demand.
By assessing the variability of their supply chain and demand patterns, businesses can set an optimal level for safety stock that minimizes risk without tying up excessive capital.
Supplier Diversification
Relying solely on a single supplier can be risky.
Therefore, it is smart to have a range of suppliers that can be relied upon to provide materials.
Diversifying suppliers ensures that if one supplier runs into difficulty, the business can lean on others to meet its supply needs.
Diversifying also fosters competitive pricing and can encourage suppliers to maintain high standards.
Implementing Just-In-Time (JIT) Inventory
This inventory strategy involves ordering inventory only as needed for production or sale.
It minimizes holding costs and reduces waste.
While this method works best with reliable suppliers and predictive delivery systems, it can lead to substantial savings if executed correctly.
Building Resilient Supply Chains
Developing a resilient supply chain involves understanding supply chain risks, evaluating possible scenarios, and identifying mitigation strategies.
Regular risk assessments and the implementation of contingency plans can prepare businesses for disruptive events.
This resilience planning ensures that the supply chain can recover quickly from unforeseen occurrences such as natural disasters or geopolitical tensions.
Conclusion
In summary, effective inventory management and strategic supplier collaboration are key to maintaining a stable supply of materials.
By embracing technology, planning accurately, and fostering strong supplier ties, businesses can create resilient operations that withstand uncertainty and meet customer demands.
It is essential for businesses to continuously review and improve upon these systems to stay competitive in a dynamic market environment.
資料ダウンロード
QCD調達購買管理クラウド「newji」は、調達購買部門で必要なQCD管理全てを備えた、現場特化型兼クラウド型の今世紀最高の購買管理システムとなります。
ユーザー登録
調達購買業務の効率化だけでなく、システムを導入することで、コスト削減や製品・資材のステータス可視化のほか、属人化していた購買情報の共有化による内部不正防止や統制にも役立ちます。
NEWJI DX
製造業に特化したデジタルトランスフォーメーション(DX)の実現を目指す請負開発型のコンサルティングサービスです。AI、iPaaS、および先端の技術を駆使して、製造プロセスの効率化、業務効率化、チームワーク強化、コスト削減、品質向上を実現します。このサービスは、製造業の課題を深く理解し、それに対する最適なデジタルソリューションを提供することで、企業が持続的な成長とイノベーションを達成できるようサポートします。
オンライン講座
製造業、主に購買・調達部門にお勤めの方々に向けた情報を配信しております。
新任の方やベテランの方、管理職を対象とした幅広いコンテンツをご用意しております。
お問い合わせ
コストダウンが利益に直結する術だと理解していても、なかなか前に進めることができない状況。そんな時は、newjiのコストダウン自動化機能で大きく利益貢献しよう!
(Β版非公開)