- お役立ち記事
- How to successfully implement quality control at subcontractors led by the purchasing department
How to successfully implement quality control at subcontractors led by the purchasing department
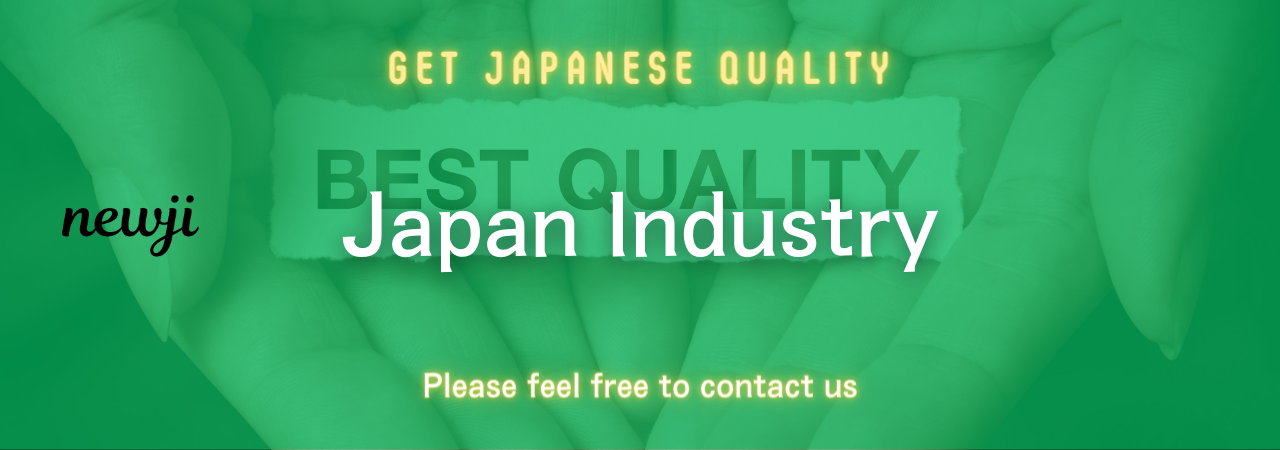
目次
Understanding the Role of the Purchasing Department
The purchasing department plays a crucial role in the overall operations of a company.
It is responsible for acquiring goods and services that the company needs to produce its products or deliver its services.
However, the responsibilities of the purchasing department extend beyond just buying products at the lowest price.
Ensuring the quality of these products is equally important.
This is where quality control at subcontractors becomes a key aspect of their responsibilities.
The Importance of Quality Control at Subcontractors
Quality control is vital because it directly affects the end product offered by a company.
When a purchasing department sources materials or components from subcontractors, the final product is only as good as the components it consists of.
If any piece of the puzzle is of inferior quality, it can lead to product failures, customer dissatisfaction, and loss of revenue.
Therefore, implementing effective quality control measures at subcontractors helps maintain the integrity of the company’s brand and ensures customer satisfaction.
Steps to Implement Quality Control at Subcontractors
1. Select Reliable Subcontractors
The first step in implementing quality control is to select subcontractors with a solid reputation for delivering high-quality products.
Conduct thorough research to understand their capabilities and track records.
Check their certifications and previous customer reviews.
It might also help to perform site visits to understand their manufacturing processes firsthand.
2. Define Quality Standards Clearly
Once you’ve selected a subcontractor, it’s crucial to communicate your company’s quality standards clearly and precisely.
Develop a comprehensive checklist that outlines all quality criteria—dimensions, performance characteristics, durability, and safety requirements.
Ensure that there is zero ambiguity in these standards to avoid any potential misunderstandings.
3. Establish a Quality Control Plan
Develop a quality control plan that details how quality will be monitored and ensured.
This plan should include key performance indicators (KPIs), inspection schedules, testing methods, and responsibilities.
Involve your subcontractor in the planning to gain their input and ensure that everyone is on the same page.
4. Regularly Monitor and Audit
Conduct regular inspections and audits at the subcontractor’s site to ensure compliance with the set quality standards.
These can be scheduled or random to ensure constant compliance.
Use these audits to address any non-conformances and share findings and expectations with the subcontractors for improvements.
5. Implement a Feedback Loop
Create a feedback mechanism that allows you and your subcontractor to communicate openly about quality concerns.
Regular meetings can be scheduled to discuss any issues, share observations, and brainstorm solutions.
A feedback loop is crucial in teaching and learning from each other to improve quality continuously.
Tools and Techniques for Effective Quality Control
Data Analysis and Reporting Tools
Leverage technological tools for data analysis and reporting.
Quality control software can help keep track of the quality levels of products received and provide insights into trends or recurring issues.
Use these insights for continuous improvement and corrective actions.
Supplier Performance Ratings
Develop and maintain supplier scorecards to evaluate subcontractor performance.
These ratings should be based on delivery times, product quality, communication, and compliance with standards.
Regularly review these performance ratings with subcontractors to motivate them to improve or maintain high standards.
Training and Development
Offer training and development programs focused on quality control for your subcontractors.
Whether it involves teaching specific testing methods or general quality management principles, training can raise awareness and equip subcontractors with the necessary skills.
By investing in their development, you foster a partnership that values quality improvement.
Challenges in Implementing Quality Control
Despite best efforts, there can be several challenges in maintaining quality control at subcontractors.
Cultural differences, language barriers, and geographical distances can complicate the process of implementing and maintaining quality standards.
Different regulations and standards in various countries can also pose challenges when dealing with international subcontractors.
Furthermore, there might be resistance from subcontractors due to cost-related concerns.
Ensuring meticulous quality control can increase their operational costs, which they might be reluctant to adopt without incentives or cost-sharing arrangements.
Conclusion
Quality control at subcontractors isn’t solely the subcontractor’s responsibility.
It requires active participation from the purchasing department to be successful.
By selecting the right subcontractors, establishing a clear quality control framework, and using appropriate tools and techniques, companies can ensure that products sourced from subcontractors meet their stringent quality requirements.
Overcoming challenges with a well-thought-out strategy and continuous improvement mindset is vital for robust quality control.
Ultimately, fostering a strong, collaborative relationship with subcontractors centered on quality leads to high-quality end products and customer satisfaction.
資料ダウンロード
QCD調達購買管理クラウド「newji」は、調達購買部門で必要なQCD管理全てを備えた、現場特化型兼クラウド型の今世紀最高の購買管理システムとなります。
ユーザー登録
調達購買業務の効率化だけでなく、システムを導入することで、コスト削減や製品・資材のステータス可視化のほか、属人化していた購買情報の共有化による内部不正防止や統制にも役立ちます。
NEWJI DX
製造業に特化したデジタルトランスフォーメーション(DX)の実現を目指す請負開発型のコンサルティングサービスです。AI、iPaaS、および先端の技術を駆使して、製造プロセスの効率化、業務効率化、チームワーク強化、コスト削減、品質向上を実現します。このサービスは、製造業の課題を深く理解し、それに対する最適なデジタルソリューションを提供することで、企業が持続的な成長とイノベーションを達成できるようサポートします。
オンライン講座
製造業、主に購買・調達部門にお勤めの方々に向けた情報を配信しております。
新任の方やベテランの方、管理職を対象とした幅広いコンテンツをご用意しております。
お問い合わせ
コストダウンが利益に直結する術だと理解していても、なかなか前に進めることができない状況。そんな時は、newjiのコストダウン自動化機能で大きく利益貢献しよう!
(Β版非公開)