- お役立ち記事
- A method to shorten global procurement lead times proposed by the purchasing department
A method to shorten global procurement lead times proposed by the purchasing department
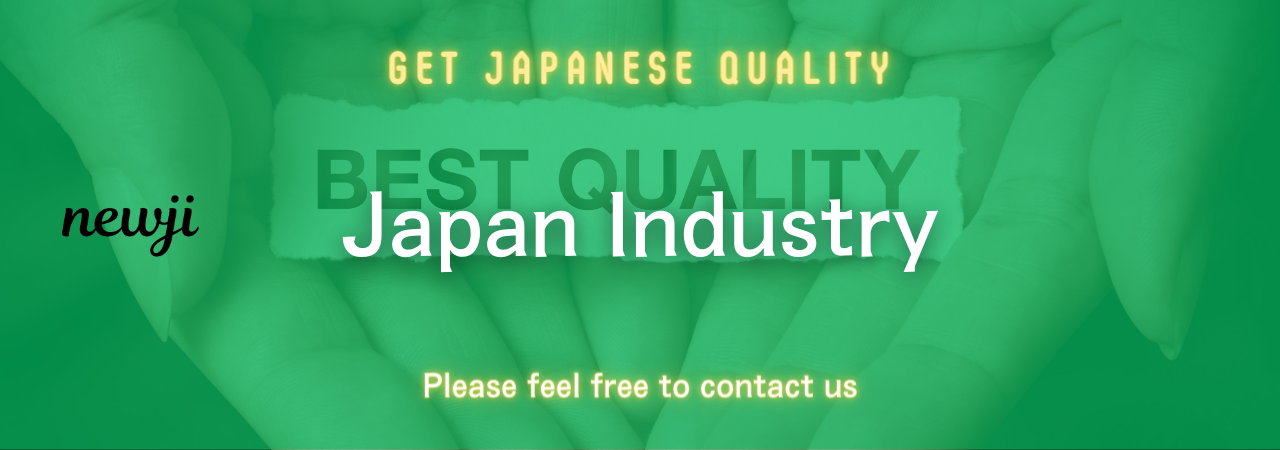
目次
Introduction to Global Procurement
In today’s interconnected world, businesses rely heavily on global procurement to source products and materials.
This practice involves purchasing goods and services from suppliers around the world, allowing companies to benefit from a more extensive selection of products and potentially reduced costs.
However, one of the primary challenges faced by organizations is managing the lead times associated with global procurement.
Long lead times can result in delays, increased costs, and a reduction in a company’s ability to respond swiftly to market changes.
To tackle this issue, the purchasing department has proposed a method to shorten these lead times effectively.
Understanding Lead Times in Procurement
Lead time is the period between placing an order and receiving the shipment.
There are several factors contributing to lead times in global procurement, such as geographical distances, supplier manufacturing cycles, shipping durations, customs clearance, and logistics delays.
Minimizing these lead times is crucial for enhancing supply chain efficiency and maintaining competitiveness.
Key Steps to Shorten Lead Times
The purchasing department has outlined a series of strategic steps to help reduce lead times in global procurement.
By implementing these strategies, businesses can enhance their responsiveness and improve their overall supply chain performance.
1. Supplier Relationship Management
Building strong relationships with suppliers is a fundamental aspect of reducing lead times.
Organizations should prioritize communication and collaboration with their suppliers to ensure they understand the company’s needs and timelines.
By establishing a good rapport, companies can work more efficiently with suppliers to address any potential delays before they become a problem.
Regular performance reviews and feedback sessions can further help in maintaining these relationships and ensuring continuous improvement.
2. Strategic Supplier Selection
Selecting the right suppliers is crucial in minimizing lead times.
Businesses should evaluate potential suppliers based on their location, reliability, production capacity, and historical performance.
Choosing suppliers closer to the market can significantly reduce shipping times.
Moreover, a reliable supplier with a consistent track record is less likely to experience production delays, ensuring a smoother procurement process.
3. Implementation of Technology
The use of technology in procurement processes can significantly streamline lead times.
Automation tools and software solutions can enhance real-time communication, provide accurate tracking of shipments, and forecast demand more reliably.
E-procurement systems enable businesses to place orders more quickly and manage their inventories effectively.
By integrating these technologies, companies can reduce clerical errors and minimize time-consuming manual processes.
4. Demand Forecasting and Inventory Management
Accurate demand forecasting is vital for minimizing lead times.
By predicting demand trends, companies can plan their procurement schedules efficiently, reducing the need for last-minute orders with longer lead times.
Additionally, effective inventory management — such as maintaining safety stock — ensures that sudden spikes in demand do not negatively impact lead times.
5. Streamlining Logistics and Shipping
Investing in efficient logistics and shipping solutions is essential for reducing lead times.
Partnering with reliable logistics providers that offer rapid and consistent delivery services can make a significant difference.
Use of air freight, express shipping options, and consolidation services can further reduce transit times.
Optimizing routes, minimizing handling times, and ensuring proper documentation for customs clearance are also crucial for streamlining the logistics process.
6. Continuous Improvement and Monitoring
To maintain reduced lead times, it’s important for businesses to focus on continuous improvement.
By constantly monitoring supplier performance, logistical processes, and procurement practices, companies can identify areas for improvement and implement necessary changes.
Regular training for procurement teams will keep them updated with the latest industry practices and technologies, further benefiting the organization.
Conclusion
Shortening global procurement lead times presents both challenges and opportunities for businesses.
By implementing these strategies proposed by the purchasing department, organizations can enhance their supply chain efficiency, reduce costs, and improve their competitive edge.
The essence lies in a comprehensive approach that encompasses effective supplier management, strategic decision-making, use of technology, and constant evaluation and adaptation of procurement processes.
Ultimately, the goal is to create a more resilient, agile, and responsive supply chain that can meet the demands of an ever-evolving global market.
資料ダウンロード
QCD調達購買管理クラウド「newji」は、調達購買部門で必要なQCD管理全てを備えた、現場特化型兼クラウド型の今世紀最高の購買管理システムとなります。
ユーザー登録
調達購買業務の効率化だけでなく、システムを導入することで、コスト削減や製品・資材のステータス可視化のほか、属人化していた購買情報の共有化による内部不正防止や統制にも役立ちます。
NEWJI DX
製造業に特化したデジタルトランスフォーメーション(DX)の実現を目指す請負開発型のコンサルティングサービスです。AI、iPaaS、および先端の技術を駆使して、製造プロセスの効率化、業務効率化、チームワーク強化、コスト削減、品質向上を実現します。このサービスは、製造業の課題を深く理解し、それに対する最適なデジタルソリューションを提供することで、企業が持続的な成長とイノベーションを達成できるようサポートします。
オンライン講座
製造業、主に購買・調達部門にお勤めの方々に向けた情報を配信しております。
新任の方やベテランの方、管理職を対象とした幅広いコンテンツをご用意しております。
お問い合わせ
コストダウンが利益に直結する術だと理解していても、なかなか前に進めることができない状況。そんな時は、newjiのコストダウン自動化機能で大きく利益貢献しよう!
(Β版非公開)