- お役立ち記事
- Measures to strengthen cooperation between production sites and suppliers supported by the purchasing department
Measures to strengthen cooperation between production sites and suppliers supported by the purchasing department
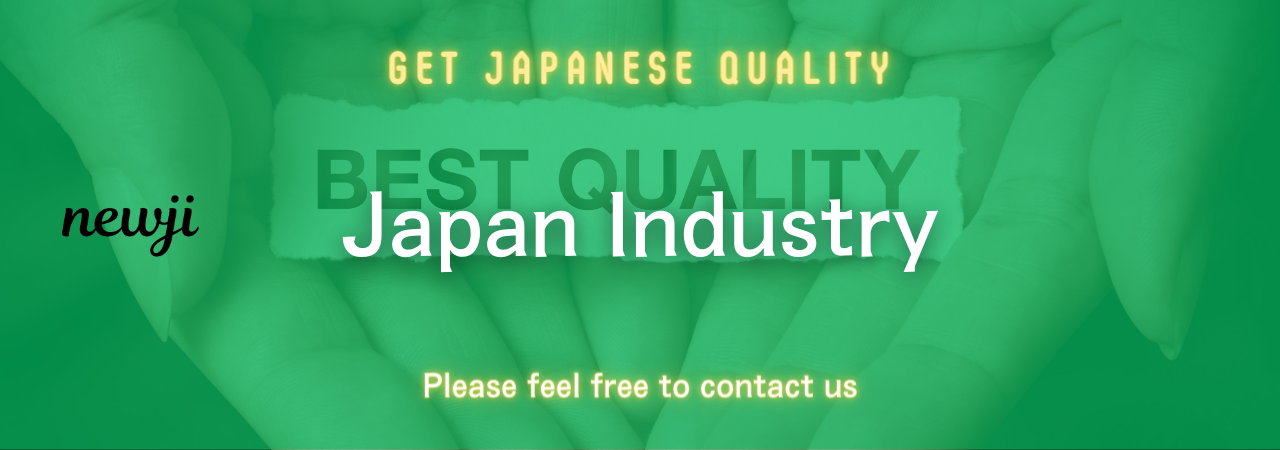
目次
Introduction
In today’s fast-paced industrial environment, the synergy between production sites and suppliers under the guidance of the purchasing department is critical.
This relationship forms the backbone of successful operations, ensuring that resources flow smoothly and products meet market demands efficiently.
Strengthening this cooperation is paramount for businesses striving to improve efficiency, reduce costs, and boost overall productivity.
In this article, we will explore measures to enhance this collaboration and the role of the purchasing department in facilitating a seamless connection.
Understanding the Role of the Purchasing Department
The purchasing department serves as a vital link between production sites and suppliers.
They are responsible for sourcing materials at competitive prices, ensuring that the quality meets company standards, and maintaining relationships with suppliers.
Their role involves not just procurement but also strategic planning and communication.
By coordinating with both production and supply chain teams, the purchasing department ensures that there is a systematic flow of goods and services, which is crucial to maintaining a smooth production cycle.
Efficient purchasing strategies can significantly reduce downtime, enhance product quality, and ensure timely delivery to customers.
Effective Communication Strategies
Open Channels of Communication
An essential component of strengthening cooperation is fostering open communication.
Production sites and suppliers must communicate regularly to ensure alignment on goals, timelines, and expectations.
The purchasing department can facilitate regular meetings and updates to ensure that all parties are informed and engaged.
Utilizing Technology for Better Communication
Leveraging technology can enhance communication between production and suppliers.
Tools like supply chain management software, automated alerts, and digital collaboration platforms streamline information sharing and help address issues before they escalate.
These digital solutions enable real-time updates, making it easier to adapt to changes and maintain a consistent workflow.
Establishing Clear Objectives and Expectations
For a collaborative relationship to thrive, clear objectives and expectations must be set.
The purchasing department can act as a mediator, helping to define and communicate these parameters.
By setting measurable goals and defining quality standards, both production sites and suppliers will be aligned toward a common purpose.
Defining Quality Standards
Ensuring that suppliers understand the quality requirements of the production site is crucial.
The purchasing department should facilitate workshops or provide documentation detailing the specific material and product quality expected.
This step minimizes the risk of misunderstandings and reduces the occurrence of defective materials disrupting production.
Agreeing on Delivery Schedules
Timely delivery is critical in a production environment.
By working closely with suppliers, the purchasing department can devise realistic delivery schedules that account for lead times and potential disruptions.
Having a buffer in place for emergencies and ensuring that both parties agree to these schedules can significantly enhance coordination.
Building Long-Term Relationships with Suppliers
Long-term relationships between production sites and suppliers foster trust and reliability, leading to better cooperation and mutual benefits.
Selecting the Right Suppliers
The purchasing department should conduct thorough assessments when selecting suppliers.
This involves evaluating their reliability, financial stability, quality of materials, and alignment with company values.
Choosing the right partners is fundamental to ensuring a consistent supply chain.
Fostering a Partnership Approach
A collaborative approach generates value for both production sites and suppliers.
By treating suppliers as partners rather than mere providers, organizations can work towards common goals.
Regular feedback, performance reviews, and joint problem-solving activities can strengthen this partnership.
Continuous Improvement and Adaptability
In a dynamic market, continuous improvement and adaptability are critical to success.
The purchasing department plays a key role in driving these aspects within cooperation.
Implementing Continuous Improvement Processes
Encouraging a culture of continuous improvement ensures that processes remain efficient and effective.
Regularly reviewing performance metrics and conducting audits can identify areas for improvement.
The purchasing department can lead initiatives to optimize procurement strategies and enhance supply chain efficiency.
Adapting to Market Changes
The business environment is ever-changing, requiring organizations to adapt quickly.
By staying informed about market trends and fluctuations, the purchasing department can anticipate changes in supply and demand.
This preparedness allows for timely adjustments to procurement strategies, ensuring that production sites remain unaffected by external pressures.
Conclusion
The seamless cooperation between production sites and suppliers, supported by the purchasing department, is essential for operational success.
By enhancing communication, setting clear objectives, cultivating long-term relationships, and fostering continuous improvement, organizations can significantly improve this collaboration.
The purchasing department is central to these efforts, guiding both sides towards shared goals and ensuring that the partnership remains productive and mutually beneficial.
In an ever-evolving industrial landscape, these measures will empower businesses to navigate challenges and seize opportunities effectively.
資料ダウンロード
QCD調達購買管理クラウド「newji」は、調達購買部門で必要なQCD管理全てを備えた、現場特化型兼クラウド型の今世紀最高の購買管理システムとなります。
ユーザー登録
調達購買業務の効率化だけでなく、システムを導入することで、コスト削減や製品・資材のステータス可視化のほか、属人化していた購買情報の共有化による内部不正防止や統制にも役立ちます。
NEWJI DX
製造業に特化したデジタルトランスフォーメーション(DX)の実現を目指す請負開発型のコンサルティングサービスです。AI、iPaaS、および先端の技術を駆使して、製造プロセスの効率化、業務効率化、チームワーク強化、コスト削減、品質向上を実現します。このサービスは、製造業の課題を深く理解し、それに対する最適なデジタルソリューションを提供することで、企業が持続的な成長とイノベーションを達成できるようサポートします。
オンライン講座
製造業、主に購買・調達部門にお勤めの方々に向けた情報を配信しております。
新任の方やベテランの方、管理職を対象とした幅広いコンテンツをご用意しております。
お問い合わせ
コストダウンが利益に直結する術だと理解していても、なかなか前に進めることができない状況。そんな時は、newjiのコストダウン自動化機能で大きく利益貢献しよう!
(Β版非公開)