- お役立ち記事
- Multiple procurement risk distribution model recommended by purchasing department
Multiple procurement risk distribution model recommended by purchasing department
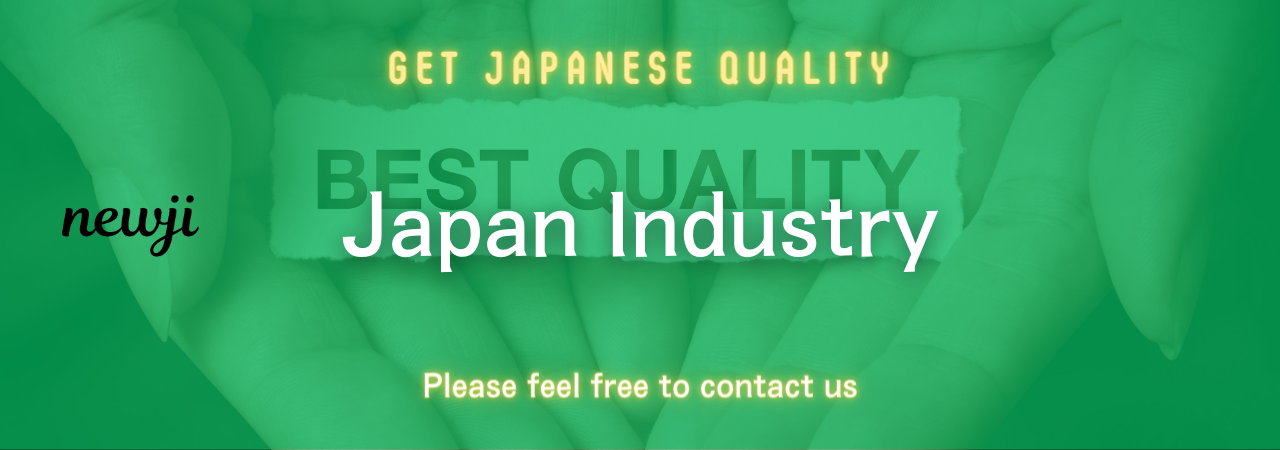
目次
Understanding Procurement Risk
Procurement risk refers to the potential challenges and uncertainties that can arise during the process of acquiring goods and services for your business.
These risks can affect an organization’s ability to obtain the best products at competitive prices, secure stable supply chains, and maintain profitability.
Risks in procurement can include supplier failure, price volatility, regulatory changes, and logistical issues.
Effectively managing these risks is crucial for any purchasing department to ensure smooth operations and consistent supply.
Why a Risk Distribution Model is Important
A risk distribution model plays a vital role in the procurement process by helping organizations anticipate, assess, and mitigate potential risks.
This model allows businesses to identify areas of vulnerability and distribute risks across different suppliers and categories.
By doing so, companies can avoid placing too much dependency on a single supplier or geographic region, which can lead to significant disruptions if issues arise.
A well-structured risk distribution model also aids in making informed procurement decisions, optimizing resource allocation, and improving overall business resilience.
The Concept of Multiple Procurement Risk Distribution
The multiple procurement risk distribution model is a strategic approach that spreads risks amongst various sources and supply channels.
This model encourages diversification in sourcing, procurement strategies, and supplier selection to minimize the impact of potential risks.
By distributing procurement risks, companies reduce the likelihood of supply chain disruptions, safeguard against price fluctuations, and increase their adaptability to unforeseen circumstances.
This approach ensures that even if one supplier fails or a particular region faces challenges, the organization can continue its operations smoothly.
Key Components of the Model
Successful implementation of a multiple procurement risk distribution model involves several key components.
1. **Supplier Diversification**: Engage multiple suppliers from different regions to avoid dependency on a single source.
This provides a buffer against supplier-specific risks, such as production delays or financial instability.
2. **Category Management**: Group similar items into distinct categories and manage them according to their unique risk profiles.
This approach allows for more focused risk management and tailored procurement strategies.
3. **Contractual Agreements**: Create flexible and comprehensive contracts that allow for adaptability in case of unexpected changes in the market or supply chain dynamics.
4. **Risk Assessment and Monitoring**: Continuously assess and monitor potential risks throughout the supply chain.
Use data analytics and risk management tools to identify trends and anticipate disruptions before they occur.
Implementing the Model in Your Organization
To successfully implement a multiple procurement risk distribution model, purchasing departments must follow a structured process.
Step 1: Risk Identification
Begin by identifying potential risks in your procurement process.
Consider factors such as geopolitical events, market volatility, supplier financial health, and regulatory changes.
Step 2: Supplier and Market Analysis
Conduct a thorough analysis of current and potential suppliers, including their locations, capabilities, and reliability.
Explore market trends to understand the broader context of your procurement environment.
Step 3: Strategic Sourcing
Develop a strategic sourcing plan that diversifies your supplier base.
Aim to balance cost efficiency with risk reduction by seeking suppliers in different regions and with varying specialties.
Step 4: Contract Management
Draft contracts that include clauses for flexibility and contingency plans.
Ensure that your contracts protect your business interests while allowing room for adaptation to changing circumstances.
Step 5: Ongoing Monitoring and Evaluation
Establish a system for ongoing risk monitoring and evaluation.
Regularly review supplier performance, market conditions, and any changes in the regulatory environment.
Adjust your procurement strategies as needed to maintain an optimal balance of risk and reward.
Benefits of the Multiple Procurement Risk Distribution Model
By implementing a multiple procurement risk distribution model, organizations can enjoy several significant benefits.
1. **Increased Resilience**: Diversified sourcing strategies increase your business’s ability to withstand supply chain disruptions and market fluctuations.
2. **Cost Optimization**: Balancing costs against potential risks allows businesses to make more strategic purchasing decisions, ultimately leading to cost savings.
3. **Improved Supplier Relationships**: Engaging with a broader range of suppliers fosters innovation and competitive pricing, while reducing reliance on any single entity.
4. **Enhanced Flexibility**: A diversified procurement approach enables organizations to adapt quickly to changing market conditions and shifting consumer demands.
Challenges in Implementing the Model
While the multiple procurement risk distribution model offers clear benefits, it also comes with challenges.
Businesses may face difficulties in managing relationships with numerous suppliers, requiring more complex coordination and communication efforts.
Additionally, the initial analysis and establishment of a diversified supplier base can be resource-intensive.
Companies must strike a balance between diversity and manageability to avoid overcomplicating their procurement processes.
Conclusion
Incorporating a multiple procurement risk distribution model is a strategic approach that can greatly benefit purchasing departments.
By spreading risks across suppliers, regions, and categories, organizations can enhance resilience, optimize costs, and adapt to an ever-changing market landscape.
While implementation presents challenges, the long-term advantages far outweigh the initial hurdles.
Purchasing departments should prioritize the development and execution of such a model to secure a sustainable and robust supply chain.
資料ダウンロード
QCD調達購買管理クラウド「newji」は、調達購買部門で必要なQCD管理全てを備えた、現場特化型兼クラウド型の今世紀最高の購買管理システムとなります。
ユーザー登録
調達購買業務の効率化だけでなく、システムを導入することで、コスト削減や製品・資材のステータス可視化のほか、属人化していた購買情報の共有化による内部不正防止や統制にも役立ちます。
NEWJI DX
製造業に特化したデジタルトランスフォーメーション(DX)の実現を目指す請負開発型のコンサルティングサービスです。AI、iPaaS、および先端の技術を駆使して、製造プロセスの効率化、業務効率化、チームワーク強化、コスト削減、品質向上を実現します。このサービスは、製造業の課題を深く理解し、それに対する最適なデジタルソリューションを提供することで、企業が持続的な成長とイノベーションを達成できるようサポートします。
オンライン講座
製造業、主に購買・調達部門にお勤めの方々に向けた情報を配信しております。
新任の方やベテランの方、管理職を対象とした幅広いコンテンツをご用意しております。
お問い合わせ
コストダウンが利益に直結する術だと理解していても、なかなか前に進めることができない状況。そんな時は、newjiのコストダウン自動化機能で大きく利益貢献しよう!
(Β版非公開)