- お役立ち記事
- Best practices for supply chain response during disasters that purchasing departments should pay attention to
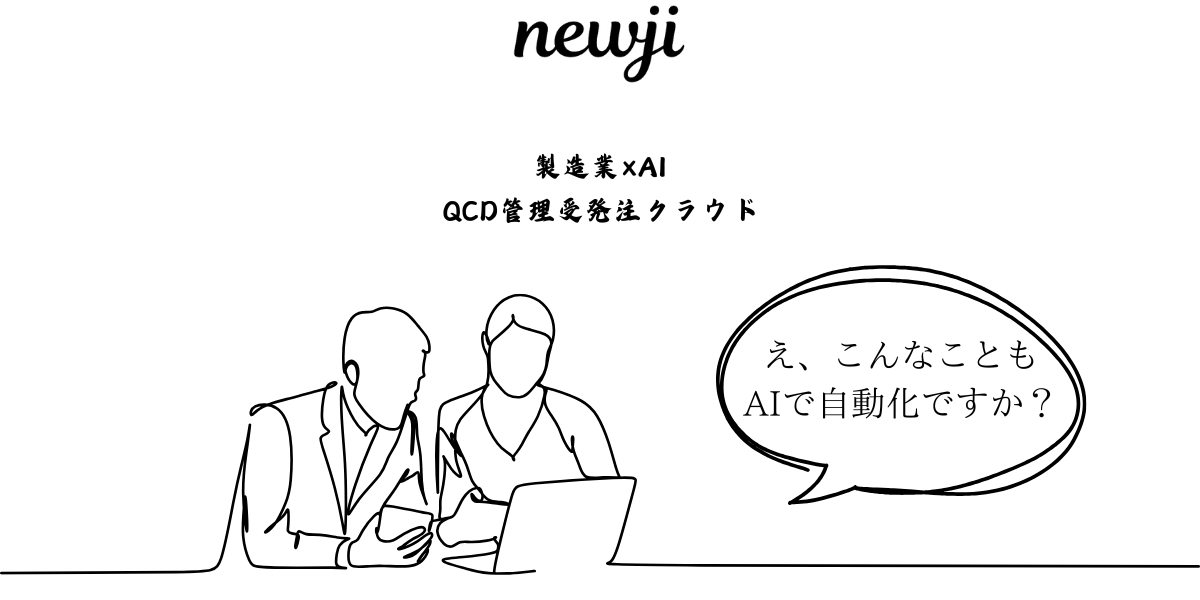
Best practices for supply chain response during disasters that purchasing departments should pay attention to
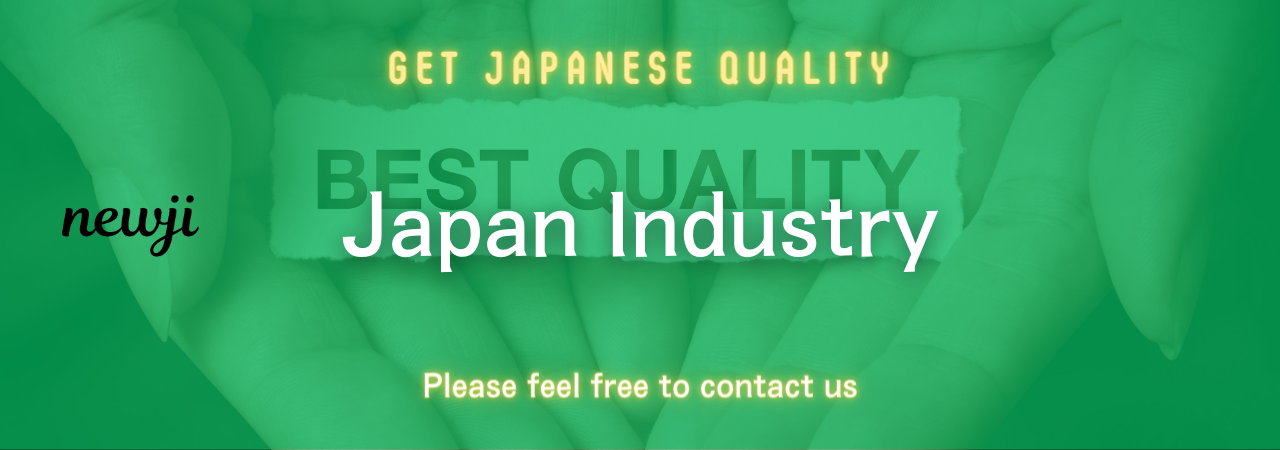
目次
Understanding Supply Chain Disruptions During Disasters
Supply chain disruptions during disasters can have a profound impact on businesses, affecting everything from production schedules to delivery timelines.
Natural disasters, such as hurricanes, earthquakes, and floods, tend to disrupt transportation networks and facilities.
Besides natural calamities, human-induced events like cyber-attacks or political unrest can also cripple supply chains.
Therefore, it’s vital for purchasing departments to develop comprehensive strategies to mitigate these risks.
Disasters can impact raw material availability, contract fulfillment, and overall logistics flow.
Understanding the potential risks and making provisions for alternate suppliers or routes can significantly cushion the blow.
For example, during the disruption caused by a hurricane, having pre-established relationships with suppliers from unaffected areas can help maintain the supply flow.
Importance of Communication and Coordination
Effective communication is key in managing supply chain responses during disasters.
Purchasing departments must establish well-coordinated communication lines with suppliers, logistics partners, and internal teams.
Real-time communication tools and platforms can offer visibility into the supply chain status, enabling quick decision-making.
During a disaster, it is crucial that all stakeholders are updated regularly on the status of operations.
From understanding which suppliers are functional to knowing which routes are viable, timely information can be the difference between success and failure.
A coordinated approach ensures that everyone involved in the supply chain is on the same page, thereby minimizing confusion and optimizing response efforts.
Risk Assessment and Management
Identifying potential risks before they occur is essential for effective disaster response.
Purchasing departments should conduct thorough risk assessments to understand vulnerabilities in their supply chains.
This involves evaluating supplier reliability, transportation risks, and geopolitical influences that could affect operations.
Risk management strategies might include diversifying supplier bases, maintaining safety stock, and utilizing technology to predict and manage risks.
Engaging in scenario planning and running disaster simulation exercises can prepare purchasing departments for real-world disruptions.
Planning for worst-case scenarios can guide timely responses and, ultimately, reduce the financial repercussions of a disaster.
Alternative Sourcing and Diversification
One of the best practices for responding to supply chain disruptions is through alternative sourcing and diversification.
Relying on a single supplier or region exposes businesses to greater risks if those areas are affected by disasters.
Diversifying the supplier base allows businesses to switch sources quickly if one is compromised.
Purchasing departments should develop a global supplier network that considers regional risks and capabilities.
Building strong relationships with multiple suppliers can also ensure better negotiation terms and enhance flexibility during crises.
A broad and diversified sourcing strategy acts as a buffer, minimizing the impact of disruptions on the supply chain.
Utilizing Technology and Data Analytics
Technology plays a crucial role in improving supply chain resilience.
Advanced data analytics can provide insights into supplier performance, logistics efficiency, and risk factors.
Cloud-based platforms and software applications offer real-time monitoring and advanced tracking capabilities.
IoT devices, blockchain, and AI can further streamline data collection and decision-making processes.
These technologies support predictive analysis, enabling proactive measures rather than reactive responses.
By leveraging technology, purchasing departments gain enhanced visibility and control over the supply chain, making it easier to adapt to unforeseen events.
Building Strong Supplier Relationships
Strong supplier relationships are essential for navigating disruptions effectively.
Collaborative partnerships lead to mutual trust, open communication, and increased support during crises.
Building such relationships involves understanding the suppliers’ strengths and limitations and working together towards a common goal.
Investing time and resources in supplier relationship management can reap long-term benefits.
During disasters, trusted suppliers are more likely to prioritize your needs, offer alternate solutions, and provide vital information for decision-making.
Therefore, nurturing these relationships is a best practice for strengthening disaster response capabilities.
The Role of Training and Education
Training and educating teams within the purchasing department can make a significant difference in disaster response efforts.
Staff should be well-versed in the company’s disaster response plan and know the procedures for communicating with suppliers and other stakeholders.
Training initiatives can include workshops, simulations, and scenario-based planning exercises.
Equipping teams with problem-solving skills and decision-making authority is equally important.
When disaster strikes, employees who understand processes and possess the relevant skills will make informed decisions that can mitigate risks effectively.
Conclusion: Proactive Measures are Key
Supply chain disruptions during disasters are inevitable.
However, adopting best practices such as risk management, communication, technological integration, and diversification can significantly mitigate the adverse effects.
Purchasing departments must take proactive measures, develop robust disaster recovery plans, and foster strong supplier relationships to enhance resilience.
The central idea is to anticipate potential problems and put solutions in place before they arise.
In doing so, businesses not only safeguard their interests but also ensure continuity in their operations.
In a world where uncertainties are part of business dynamics, these practices create a safety net that transforms vulnerability into a strategic advantage.
資料ダウンロード
QCD調達購買管理クラウド「newji」は、調達購買部門で必要なQCD管理全てを備えた、現場特化型兼クラウド型の今世紀最高の購買管理システムとなります。
ユーザー登録
調達購買業務の効率化だけでなく、システムを導入することで、コスト削減や製品・資材のステータス可視化のほか、属人化していた購買情報の共有化による内部不正防止や統制にも役立ちます。
NEWJI DX
製造業に特化したデジタルトランスフォーメーション(DX)の実現を目指す請負開発型のコンサルティングサービスです。AI、iPaaS、および先端の技術を駆使して、製造プロセスの効率化、業務効率化、チームワーク強化、コスト削減、品質向上を実現します。このサービスは、製造業の課題を深く理解し、それに対する最適なデジタルソリューションを提供することで、企業が持続的な成長とイノベーションを達成できるようサポートします。
オンライン講座
製造業、主に購買・調達部門にお勤めの方々に向けた情報を配信しております。
新任の方やベテランの方、管理職を対象とした幅広いコンテンツをご用意しております。
お問い合わせ
コストダウンが利益に直結する術だと理解していても、なかなか前に進めることができない状況。そんな時は、newjiのコストダウン自動化機能で大きく利益貢献しよう!
(Β版非公開)