- お役立ち記事
- Revolutionizing Japanese Manufacturing: The Role of Adhesive Detection in Quality Assurance
Revolutionizing Japanese Manufacturing: The Role of Adhesive Detection in Quality Assurance
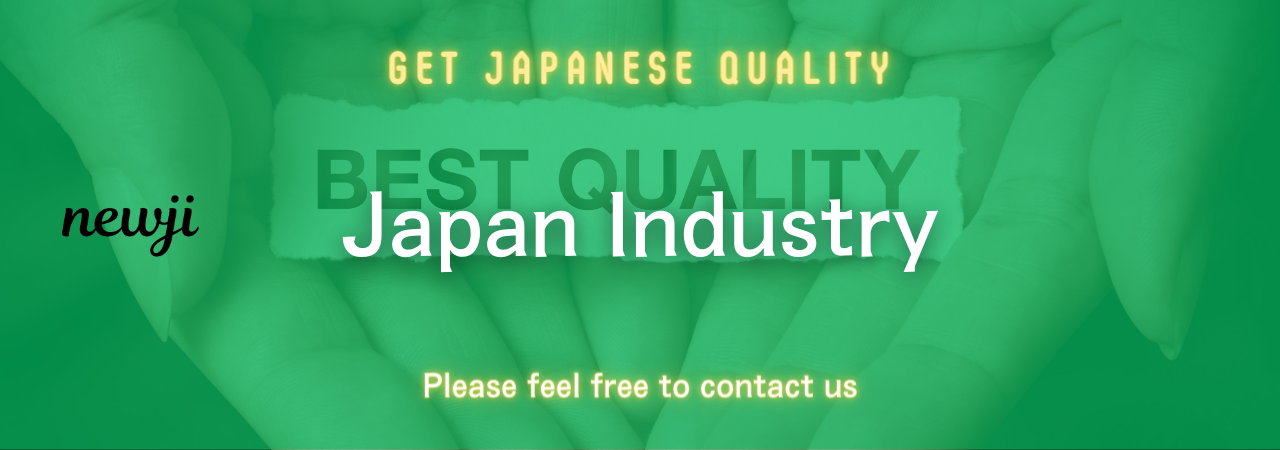
目次
Introduction to Adhesive Detection in Japanese Manufacturing
Japanese manufacturing is renowned worldwide for its precision, quality, and efficiency. One of the key factors contributing to this reputation is the meticulous approach to quality assurance, particularly in the application and detection of adhesives. Adhesive detection plays a pivotal role in ensuring that products meet stringent quality standards, thereby minimizing defects and enhancing overall reliability. This article delves into the role of adhesive detection in revolutionizing Japanese manufacturing, exploring its impact from a procurement and purchasing perspective, discussing advantages and disadvantages, supplier negotiation techniques, market conditions, and best practices.
The Importance of Adhesive Detection in Quality Assurance
Adhesives are integral components in various manufacturing processes, from electronics assembly to automotive production. The correct application and detection of adhesives are critical to product integrity and performance. In Japanese manufacturing, where quality is paramount, adhesive detection systems ensure that bonds are strong, consistent, and free from defects such as air bubbles, uneven distribution, or insufficient bonding. Effective adhesive detection not only enhances product quality but also reduces waste, lowers production costs, and improves overall manufacturing efficiency.
Advantages of Integrating Adhesive Detection Systems
Enhanced Product Quality
One of the primary advantages of implementing adhesive detection systems is the significant improvement in product quality. By accurately detecting and analyzing adhesive application, manufacturers can ensure that each product meets the required standards. This consistency reduces the likelihood of product failures, enhances durability, and increases customer satisfaction.
Cost Reduction
Adhesive detection helps in minimizing material wastage by ensuring precise application. By detecting excess or insufficient adhesive usage, manufacturers can optimize their adhesive consumption, leading to substantial cost savings. Additionally, early detection of defects reduces the need for costly rework and repairs.
Increased Efficiency
Automated adhesive detection systems streamline the production process by providing real-time feedback and monitoring. This automation reduces manual inspection efforts, accelerates production cycles, and allows for rapid adjustments, thereby increasing overall manufacturing efficiency.
Compliance with Industry Standards
Japanese manufacturing often adheres to rigorous industry standards and regulations. Adhesive detection systems help ensure compliance by maintaining consistent quality levels and providing documented evidence of quality control measures. This compliance is crucial for maintaining certifications and meeting customer expectations.
Challenges and Disadvantages of Adhesive Detection
High Initial Investment
The implementation of adhesive detection systems requires a significant initial investment in equipment, technology, and training. For smaller manufacturers or those with tight budgets, the upfront costs can be a barrier to adoption.
Technical Complexity
Adhesive detection involves sophisticated technology and requires specialized knowledge to operate effectively. Manufacturers may face challenges in training staff, maintaining the systems, and integrating them seamlessly into existing production lines.
Maintenance and Downtime
Like any technological system, adhesive detection equipment requires regular maintenance to function optimally. Unscheduled downtimes due to technical issues can disrupt production schedules and negate some of the efficiency gains offered by the systems.
Adaptability to Different Adhesive Types
Different adhesive types have varying properties and application requirements. Adhesive detection systems must be adaptable to handle these differences, which can complicate the setup and calibration processes.
Supplier Negotiation Techniques for Adhesive Detection Systems
Understanding Market Conditions
Before entering negotiations, it is crucial to have a thorough understanding of the current market conditions for adhesive detection systems. This includes knowledge of the leading suppliers, technological advancements, pricing trends, and availability. Staying informed about market dynamics empowers buyers to negotiate more effectively.
Building Strong Supplier Relationships
Establishing and maintaining strong relationships with suppliers can lead to better terms, preferential pricing, and more reliable support. Engaging in open communication, demonstrating loyalty, and fostering mutual trust are essential strategies for building these relationships.
Requesting Detailed Proposals
When negotiating with suppliers, request detailed proposals that outline not only the cost of the adhesive detection systems but also the associated services such as installation, training, and maintenance. Comparing comprehensive proposals ensures a more informed decision-making process.
Leveraging Volume Discounts
If your manufacturing operations require multiple adhesive detection systems or if you plan to scale your production, leverage the potential for volume discounts during negotiations. Suppliers are often willing to offer better pricing for larger orders, providing cost savings for your company.
Evaluating Total Cost of Ownership
Beyond the initial purchase price, consider the total cost of ownership, including installation, maintenance, training, and potential downtime costs. Negotiating terms that minimize these ongoing expenses can result in significant long-term savings.
Exploring Financing Options
In cases where upfront costs are prohibitive, explore financing options offered by suppliers. Flexible payment terms, leasing options, or installment plans can make the acquisition of adhesive detection systems more manageable financially.
Market Conditions for Adhesive Detection in Japan
Technological Advancements
The market for adhesive detection in Japan is characterized by rapid technological advancements. Innovations such as machine learning algorithms, advanced imaging techniques, and integration with Industry 4.0 platforms are enhancing the capabilities and accuracy of adhesive detection systems.
Competitive Landscape
The Japanese market features a mix of domestic and international suppliers offering a range of adhesive detection solutions. Competition drives innovation, improves product offerings, and often results in more competitive pricing, benefiting manufacturers seeking the best solutions for their needs.
Regulatory Environment
Japan’s stringent regulatory environment ensures that adhesive detection systems meet high standards of quality and safety. Manufacturers must navigate these regulations to ensure compliance, which can influence supplier selection and system specifications.
Demand for Quality Assurance
The high demand for quality assurance in Japanese manufacturing sectors such as automotive, electronics, and aerospace fuels the growth of the adhesive detection market. Manufacturers’ commitment to excellence drives the adoption of advanced detection systems to maintain their competitive edge.
Best Practices for Implementing Adhesive Detection Systems
Comprehensive Needs Assessment
Before selecting an adhesive detection system, conduct a comprehensive needs assessment to understand the specific requirements of your manufacturing processes. Consider factors such as adhesive types, application methods, detection accuracy, and integration capabilities with existing systems.
Choosing the Right Technology
Select adhesive detection technology that aligns with your production needs. Options include optical inspection, infrared spectroscopy, ultrasonic testing, and machine vision systems. Evaluating the strengths and limitations of each technology ensures the selection of the most suitable solution.
Integration with Existing Systems
Ensure that the adhesive detection system can be seamlessly integrated with your current manufacturing infrastructure. Compatibility with existing equipment, data management systems, and workflow processes is essential for maximizing efficiency and minimizing disruptions.
Training and Skill Development
Invest in comprehensive training programs for staff to effectively operate and maintain adhesive detection systems. Skilled personnel can leverage the full potential of the technology, troubleshoot issues promptly, and contribute to continuous quality improvement.
Regular Maintenance and Calibration
Implement a schedule for regular maintenance and calibration of adhesive detection systems to ensure consistent performance and accuracy. Proactive upkeep minimizes downtime, extends the lifespan of equipment, and maintains high detection standards.
Data Analysis and Continuous Improvement
Utilize the data generated by adhesive detection systems for ongoing analysis and quality improvement initiatives. Identifying trends, common defects, and areas for enhancement enables manufacturers to refine processes, reduce variability, and achieve higher quality outcomes.
Collaboration with Suppliers
Maintain open lines of communication with adhesive detection system suppliers to stay informed about the latest technological advancements, updates, and best practices. Collaborating with suppliers can lead to customized solutions and support that align with your specific manufacturing needs.
The Role of Procurement and Purchasing in Adhesive Detection
Strategic Sourcing
Procurement plays a critical role in sourcing the right adhesive detection systems. Strategic sourcing involves identifying reliable suppliers, evaluating their offerings, and selecting solutions that provide the best value in terms of quality, cost, and performance.
Vendor Management
Effective vendor management ensures that suppliers meet their commitments regarding delivery schedules, product quality, and support services. Building strong partnerships with vendors enhances collaboration and facilitates smoother implementation of adhesive detection systems.
Risk Management
Procurement professionals must assess and mitigate risks associated with the acquisition of adhesive detection systems. This includes evaluating supplier reliability, ensuring compliance with regulatory standards, and planning for contingencies in case of system failures or supplier issues.
Negotiation and Contracting
Negotiating favorable terms and conditions is essential to securing the best possible deals for adhesive detection systems. Procurement teams must focus on aspects such as pricing, warranties, service agreements, and delivery timelines to ensure that contracts align with organizational goals and budgets.
Cost-Benefit Analysis
Conducting a thorough cost-benefit analysis helps in making informed purchasing decisions. Evaluating the potential return on investment, considering both tangible and intangible benefits, ensures that the expenditure on adhesive detection systems is justified and aligned with business objectives.
Future Trends in Adhesive Detection and Quality Assurance
Integration with Industry 4.0
The integration of adhesive detection systems with Industry 4.0 technologies, such as the Internet of Things (IoT) and artificial intelligence (AI), is transforming quality assurance processes. Smart detection systems can communicate with other manufacturing equipment, analyze data in real-time, and facilitate predictive maintenance.
Advancements in Machine Learning
Machine learning algorithms are enhancing the capabilities of adhesive detection systems by enabling them to learn and adapt to varying conditions. These advancements improve detection accuracy, reduce false positives, and allow systems to handle more complex adhesive application scenarios.
Sustainability and Eco-Friendly Adhesives
As sustainability becomes increasingly important, the demand for eco-friendly adhesives is rising. Adhesive detection systems are evolving to accommodate these new materials, ensuring that manufacturers can maintain quality standards while adopting environmentally responsible practices.
Remote Monitoring and Cloud Integration
Remote monitoring capabilities and cloud integration are becoming standard features in adhesive detection systems. These technologies allow for centralized data management, remote troubleshooting, and enhanced collaboration across different manufacturing sites.
Customization and Flexibility
Manufacturers are seeking adhesive detection systems that offer greater customization and flexibility to meet specific production needs. The ability to tailor detection parameters, integrate with diverse production lines, and adapt to different adhesive types is driving demand for more versatile solutions.
Case Studies: Successful Implementation of Adhesive Detection in Japanese Manufacturing
Automotive Industry
A leading Japanese automotive manufacturer implemented advanced adhesive detection systems to improve the quality of component assembly. By integrating machine vision technology, the company achieved a 25% reduction in adhesive-related defects, resulting in significant cost savings and enhanced vehicle reliability.
Electronics Manufacturing
In the electronics sector, precision is crucial. A major electronics manufacturer adopted infrared spectroscopy-based adhesive detection to ensure the accurate placement of components on circuit boards. This implementation reduced production errors by 30% and increased overall production efficiency.
Aerospace Components
An aerospace parts manufacturer integrated ultrasonic adhesive detection systems to meet stringent industry standards. The enhanced detection capabilities ensured that all bonds met required specifications, leading to improved product safety and compliance with international regulations.
Conclusion
Adhesive detection plays a transformative role in Japanese manufacturing by ensuring high-quality standards, enhancing efficiency, and reducing costs. From a procurement and purchasing perspective, selecting the right adhesive detection systems involves strategic sourcing, effective vendor management, and thorough cost-benefit analysis. While there are challenges associated with the implementation, the advantages far outweigh the disadvantages, making adhesive detection a critical component of quality assurance in manufacturing.
As technology continues to advance, the integration of adhesive detection with Industry 4.0, machine learning, and sustainable practices will further revolutionize manufacturing processes. By adopting best practices and staying abreast of market trends, Japanese manufacturers can maintain their competitive edge, uphold their reputation for excellence, and continue to deliver superior products to the global market.
Investing in adhesive detection is not just a quality control measure; it is a strategic decision that aligns with the broader goals of efficiency, reliability, and innovation. As Japanese manufacturing continues to evolve, the role of adhesive detection will undoubtedly grow, solidifying its importance in the landscape of global manufacturing excellence.
資料ダウンロード
QCD調達購買管理クラウド「newji」は、調達購買部門で必要なQCD管理全てを備えた、現場特化型兼クラウド型の今世紀最高の購買管理システムとなります。
ユーザー登録
調達購買業務の効率化だけでなく、システムを導入することで、コスト削減や製品・資材のステータス可視化のほか、属人化していた購買情報の共有化による内部不正防止や統制にも役立ちます。
NEWJI DX
製造業に特化したデジタルトランスフォーメーション(DX)の実現を目指す請負開発型のコンサルティングサービスです。AI、iPaaS、および先端の技術を駆使して、製造プロセスの効率化、業務効率化、チームワーク強化、コスト削減、品質向上を実現します。このサービスは、製造業の課題を深く理解し、それに対する最適なデジタルソリューションを提供することで、企業が持続的な成長とイノベーションを達成できるようサポートします。
オンライン講座
製造業、主に購買・調達部門にお勤めの方々に向けた情報を配信しております。
新任の方やベテランの方、管理職を対象とした幅広いコンテンツをご用意しております。
お問い合わせ
コストダウンが利益に直結する術だと理解していても、なかなか前に進めることができない状況。そんな時は、newjiのコストダウン自動化機能で大きく利益貢献しよう!
(Β版非公開)