- お役立ち記事
- Examples of successful manufacturing cost reduction initiatives supported by purchasing departments
Examples of successful manufacturing cost reduction initiatives supported by purchasing departments
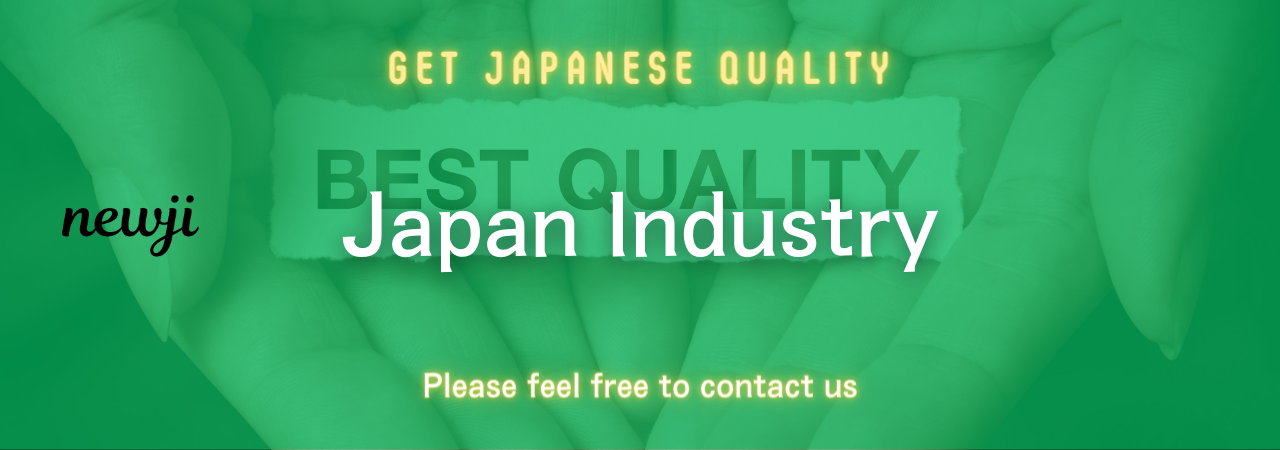
目次
The Role of Purchasing Departments in Cost Reduction
Purchasing departments play a crucial role in reducing manufacturing costs.
They are at the forefront of negotiating better prices, managing supplier relationships, and optimizing procurement processes.
By focusing on these key areas, purchasing departments have the potential to significantly lower costs, thus enhancing the overall profitability of the company.
Negotiating Better Prices
One of the most effective ways purchasing departments can reduce costs is through negotiation.
They work tirelessly to secure better prices for materials and supplies.
This involves understanding market prices, competitor activities, and potential alternative suppliers.
A purchasing team might, for example, leverage the company’s buying power by bundling purchases across different departments to gain volume discounts.
They may also lock in long-term contracts with suppliers to hedge against price volatility, ensuring stable prices over time.
Managing Supplier Relationships
Building strong relationships with suppliers is another strategy for reducing costs.
By nurturing these relationships, purchasing departments can secure favorable terms and conditions.
Consider a manufacturer that sources raw materials from multiple suppliers.
The purchasing department can work closely with these suppliers to identify cost-saving opportunities, such as reducing lead times or consolidating shipments to lower transportation costs.
Moreover, good supplier relationships can lead to collaborative efforts on product innovations or process improvements that further reduce costs.
Streamlining Procurement Processes
Efficiency in procurement processes can also yield significant cost savings.
The purchasing department can employ digital tools and technologies to automate routine tasks and improve procurement workflows.
For instance, implementing an e-procurement system can enhance visibility over the supply chain, reduce paperwork, and minimize human errors.
It allows the department to track spending efficiently and ensure compliance with procurement policies.
Automation can also speed up order processing, enabling the company to respond more quickly to market demands and reduce holding costs for inventory.
Case Studies of Successful Cost Reduction Initiatives
Case Study 1: Automotive Manufacturer
An automotive manufacturer successfully reduced its production costs by revamping its supplier selection process.
The purchasing department conducted a thorough review of all existing suppliers based on price, quality, and delivery performance.
Armed with this data, the team renegotiated contracts and chose to partner with suppliers who offered superior value.
As a result, the company managed to cut material costs by 10%, which translated into substantial savings on production expenses.
Case Study 2: Electronics Producer
An electronics producer faced high costs due to inefficient procurement processes.
The purchasing department decided to implement a cloud-based procurement system to address this challenge.
This digital solution automated the ordering process and provided real-time insights into supplier performance and inventory levels.
With improved data accuracy and process automation, the company reduced its procurement-related administrative costs by 15%.
Case Study 3: Food and Beverage Company
A food and beverage company sought to reduce manufacturing costs through strategic supplier partnerships.
The purchasing department focused on fostering long-term collaborations with key suppliers.
They worked together to develop ingredients that were not only cost-effective but also maintained product quality.
This collaborative approach enabled the company to reduce ingredient costs by 8%, ultimately leading to lower production expenses without compromising on taste or quality.
Challenges in Cost Reduction Efforts
While purchasing departments are instrumental in driving cost reduction initiatives, they often face challenges.
One common obstacle is resistance to change within the organization.
For example, departments accustomed to certain suppliers might be hesitant to switch, even when better options are available.
Overcoming this resistance requires effective communication and demonstrating the potential benefits of new suppliers or processes.
Another challenge is managing trade-offs between cost and quality.
Reducing costs should not come at the expense of the product’s quality or company reputation.
Purchasing teams must balance these factors carefully to ensure sustainable cost savings.
Best Practices for Successful Cost Reduction
To maximize the success of cost reduction efforts, purchasing departments should adhere to several best practices.
Firstly, adopting a strategic approach to procurement is essential.
Rather than focusing merely on cost-cutting, purchasing teams should aim for value creation.
This involves regular market analysis, strategic sourcing, and aligning procurement goals with the company’s overall business strategy.
Secondly, investing in technology can greatly enhance purchasing efficiency.
Modern procurement tools provide insights and analytics that can lead to more informed decision-making.
Finally, fostering a culture of continuous improvement is vital.
Encouraging employees to identify cost-saving opportunities and champion innovative ideas can lead to sustained reductions in manufacturing costs.
In conclusion, purchasing departments are key drivers of manufacturing cost reduction initiatives.
Through effective negotiation, strategic supplier relationships, and streamlined processes, they can unlock significant savings for their organizations.
Despite the challenges, by following best practices and leveraging technology, purchasing teams can achieve meaningful and lasting cost reductions, ultimately bolstering the financial health of their companies.
資料ダウンロード
QCD調達購買管理クラウド「newji」は、調達購買部門で必要なQCD管理全てを備えた、現場特化型兼クラウド型の今世紀最高の購買管理システムとなります。
ユーザー登録
調達購買業務の効率化だけでなく、システムを導入することで、コスト削減や製品・資材のステータス可視化のほか、属人化していた購買情報の共有化による内部不正防止や統制にも役立ちます。
NEWJI DX
製造業に特化したデジタルトランスフォーメーション(DX)の実現を目指す請負開発型のコンサルティングサービスです。AI、iPaaS、および先端の技術を駆使して、製造プロセスの効率化、業務効率化、チームワーク強化、コスト削減、品質向上を実現します。このサービスは、製造業の課題を深く理解し、それに対する最適なデジタルソリューションを提供することで、企業が持続的な成長とイノベーションを達成できるようサポートします。
オンライン講座
製造業、主に購買・調達部門にお勤めの方々に向けた情報を配信しております。
新任の方やベテランの方、管理職を対象とした幅広いコンテンツをご用意しております。
お問い合わせ
コストダウンが利益に直結する術だと理解していても、なかなか前に進めることができない状況。そんな時は、newjiのコストダウン自動化機能で大きく利益貢献しよう!
(Β版非公開)