- お役立ち記事
- Latest indicators for supplier evaluation recommended by purchasing departments
Latest indicators for supplier evaluation recommended by purchasing departments
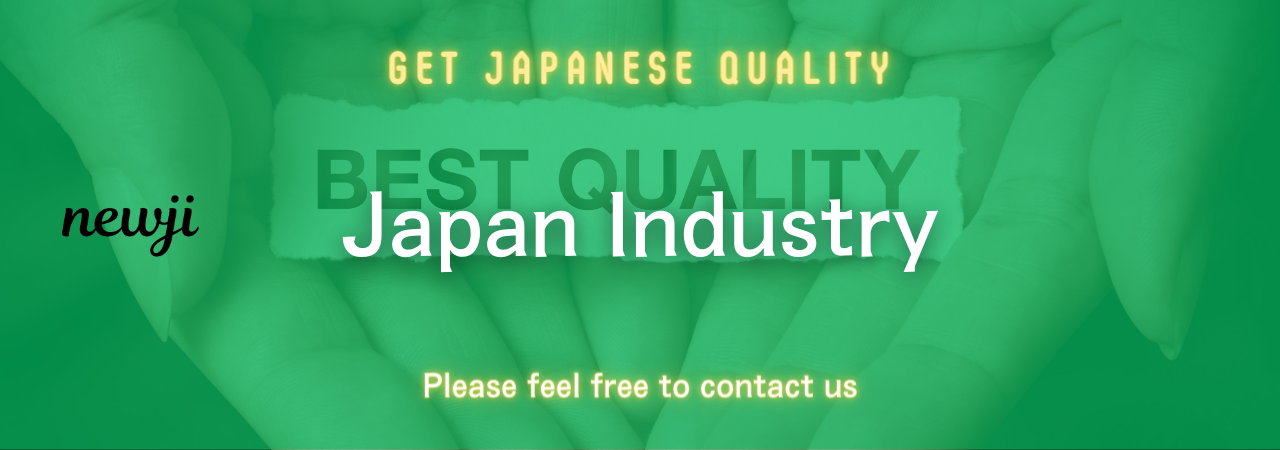
目次
Introduction to Supplier Evaluation
In today’s dynamic business environment, effective supplier evaluation is crucial for purchasing departments.
Selecting the right suppliers can significantly impact a company’s operational efficiency and overall success.
Evaluating suppliers involves assessing various aspects, including quality, reliability, and cost-effectiveness.
With the right indicators, purchasing departments can ensure they partner with suppliers who meet their company’s standards and requirements.
Why Supplier Evaluation Matters
Supplier evaluation is not just about finding a vendor who offers the best price.
It is about establishing a reliable supply chain that supports a company’s strategic goals.
A well-evaluated supplier often leads to better product quality, timely deliveries, and improved overall service.
Additionally, it helps mitigate risks associated with supply chain disruptions and enhances the purchasing department’s decision-making process.
Key Indicators for Supplier Evaluation
To effectively evaluate suppliers, purchasing departments should consider several key indicators.
These indicators cover various aspects of a supplier’s performance and align with the company’s standards.
1. Quality of Products and Services
The quality of products and services tops the list of evaluation criteria.
It is essential to assess whether the supplier consistently delivers high-quality products that meet the company’s specifications.
Purchasing departments should consider the supplier’s quality control processes and their ability to maintain quality over time.
High-quality products lead to customer satisfaction and reduce the need for costly returns or rework.
2. Reliability and Consistency
Reliability in fulfilling orders consistently is a crucial indicator for evaluating suppliers.
Purchasing departments should assess the supplier’s track record for on-time deliveries and adherence to commitments.
Reliable suppliers help maintain production schedules and avoid disruptions in the supply chain.
3. Cost Competitiveness
While cost is not the sole consideration, it remains a significant factor in supplier evaluation.
Purchasing departments should compare the supplier’s pricing with industry standards and competitor offerings.
Ensuring that the supplier provides value for money without compromising quality is key to cost competitiveness.
4. Financial Stability
Understanding a supplier’s financial stability is critical to ensuring long-term partnerships.
Financially stable suppliers are better positioned to invest in capacity, technology, and innovation.
Purchasing departments should review the supplier’s financial statements and assess their creditworthiness.
5. Compliance and Certifications
Adherence to industry standards and certifications is an important indicator of a supplier’s credibility.
Purchasing departments should verify if the supplier complies with relevant regulations, such as environmental and safety standards.
Certifications like ISO can provide assurance of the supplier’s commitment to maintaining high standards.
6. Communication and Responsiveness
Effective communication is essential for a successful supplier relationship.
Purchasing departments should evaluate the supplier’s responsiveness and willingness to address inquiries and issues promptly.
Transparent communication can prevent misunderstandings and build trust between the parties.
7. Innovation and Technological Capabilities
Suppliers that invest in innovation and technology can offer competitive advantages to purchasing departments.
Evaluating a supplier’s technological capabilities can help assess their potential to contribute to product development and process improvements.
Innovative suppliers are more likely to adapt to changing industry trends and demands.
Tools and Techniques for Supplier Evaluation
Purchasing departments can use various tools and techniques to assess suppliers based on the mentioned indicators.
1. Supplier Scorecards
Supplier scorecards are effective tools for evaluating supplier performance.
These scorecards typically include various metrics related to quality, delivery, cost, and service.
By assigning scores to each metric, purchasing departments can objectively compare different suppliers.
2. Regular Audits and Assessments
Conducting regular audits and assessments allows purchasing departments to maintain ongoing evaluations of suppliers.
These audits can identify areas for improvement and help ensure compliance with agreed terms.
Regular assessments also foster open dialogue and continuous improvement efforts.
3. Supplier Performance Reviews
Organizing periodic performance reviews with suppliers facilitates constructive discussions about their performance.
During these reviews, purchasing departments can share feedback and address any concerns or improvement opportunities.
Supplier performance reviews encourage accountability and strengthen the supplier-customer relationship.
Conclusion
Effective supplier evaluation is a critical component of the purchasing department’s strategic role within an organization.
By focusing on key indicators like quality, reliability, cost competitiveness, financial stability, compliance, communication, and innovation, companies can select the best partners for their needs.
Utilizing tools like scorecards, audits, and performance reviews ensures a comprehensive evaluation process.
Ultimately, the right supplier evaluation approach contributes to enhanced operational efficiency, reduced risks, and a stronger supply chain.
資料ダウンロード
QCD調達購買管理クラウド「newji」は、調達購買部門で必要なQCD管理全てを備えた、現場特化型兼クラウド型の今世紀最高の購買管理システムとなります。
ユーザー登録
調達購買業務の効率化だけでなく、システムを導入することで、コスト削減や製品・資材のステータス可視化のほか、属人化していた購買情報の共有化による内部不正防止や統制にも役立ちます。
NEWJI DX
製造業に特化したデジタルトランスフォーメーション(DX)の実現を目指す請負開発型のコンサルティングサービスです。AI、iPaaS、および先端の技術を駆使して、製造プロセスの効率化、業務効率化、チームワーク強化、コスト削減、品質向上を実現します。このサービスは、製造業の課題を深く理解し、それに対する最適なデジタルソリューションを提供することで、企業が持続的な成長とイノベーションを達成できるようサポートします。
オンライン講座
製造業、主に購買・調達部門にお勤めの方々に向けた情報を配信しております。
新任の方やベテランの方、管理職を対象とした幅広いコンテンツをご用意しております。
お問い合わせ
コストダウンが利益に直結する術だと理解していても、なかなか前に進めることができない状況。そんな時は、newjiのコストダウン自動化機能で大きく利益貢献しよう!
(Β版非公開)