- お役立ち記事
- Purchasing department process reform method to strengthen collaboration with production sites
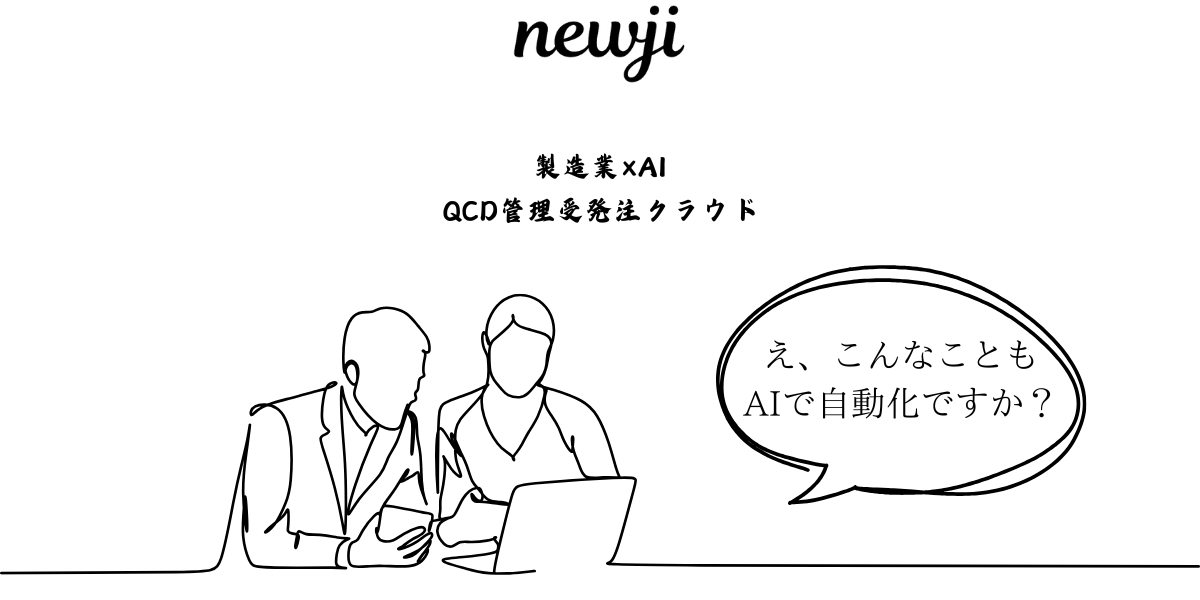
Purchasing department process reform method to strengthen collaboration with production sites
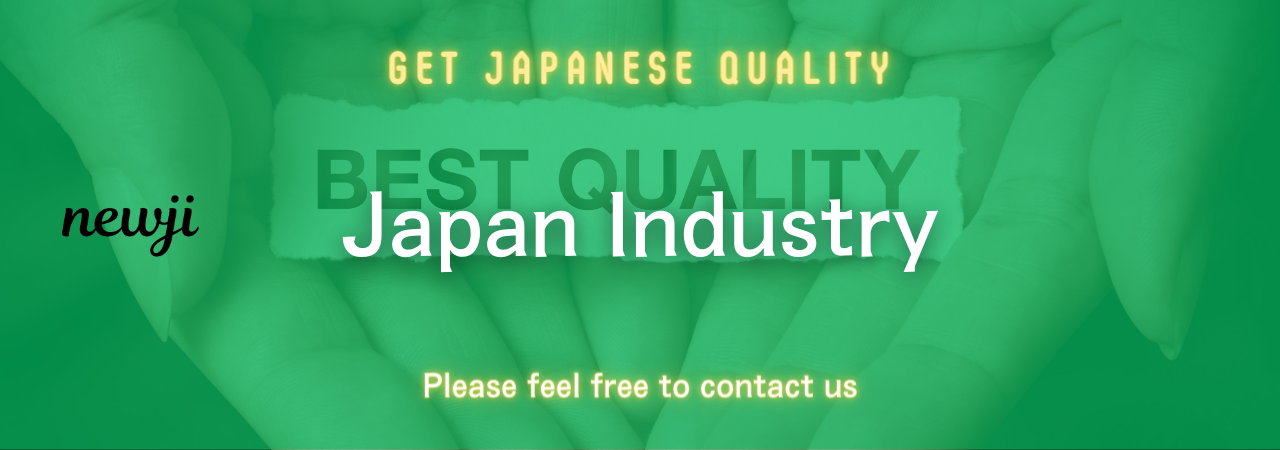
目次
Understanding the Role of the Purchasing Department
The purchasing department plays a pivotal role in any manufacturing company.
Their primary responsibility is to procure the materials necessary for production.
This involves researching suppliers, negotiating prices, and ensuring timely delivery of quality materials.
However, their role is much more than just buying.
They work to optimize costs, forecast demand, and ensure that production has what it needs to create finished products.
The Importance of Collaboration with Production Sites
Effective collaboration between the purchasing department and production sites is essential for seamless operations.
When these two units work harmoniously, it minimizes delays, reduces costs, and improves product quality.
Production sites rely on steady supplies to maintain their schedules, while the purchasing department counts on production forecasts to plan their procurement strategies.
Challenges Faced by the Purchasing Department
Despite the critical nature of their role, purchasing departments often face various challenges.
Poor communication with production sites can lead to overstocking or stockouts.
Misjudgments in material quality or supplier capacity can disrupt production.
To overcome these issues, a reform in their processes and a stronger collaboration strategy with production sites is necessary.
Aligning Goals and Objectives
The first step in reforming processes is aligning the goals and objectives of the purchasing department with those of the production sites.
Both teams should have a clear understanding of the company’s overall objectives.
This clarity ensures that all processes and initiatives support the bigger picture.
Regular meetings can be held to discuss targets, review performances, and ensure alignment.
Implementing Advanced Technology for Better Collaboration
In today’s digital age, technology offers solutions to many common collaboration challenges.
For purchasing departments, implementing advanced technologies can streamline processes and improve communication with production sites.
Adopting Integrated Software Systems
One way to strengthen collaboration is through the use of integrated software systems.
These systems allow real-time sharing of data between departments.
For instance, Enterprise Resource Planning (ERP) systems can provide updates on inventory levels, production forecasts, and more.
This transparency ensures that both purchasing and production are on the same page regarding what’s needed and what’s available.
Utilizing Data Analytics
Data analytics offers another avenue for improvement.
By analyzing purchasing data, departments can predict trends, identify inefficiencies, and make informed decisions.
Data-driven insights can lead to better forecasting of material requirements, thus ensuring materials are available precisely when needed by the production sites.
Building Strong Supplier Relationships
For the purchasing department, suppliers are key partners.
Building strong, reliable relationships with suppliers can lead to better terms, quicker response times, and overall improved service.
Regular Communication with Suppliers
Maintaining regular communication with suppliers is crucial.
By keeping them informed about future demands and needs, they can better prepare their resources.
This proactive approach helps avoid last-minute issues that might disrupt production schedules.
Supplier Performance Evaluation
Another aspect of strengthening supplier relationships is regular performance evaluations.
Assess suppliers on factors such as delivery timelines, quality of materials, and pricing flexibility.
Based on these evaluations, work to enhance relationships with high-performing suppliers while addressing issues with others.
Training and Development for Purchasing Staff
Investing in the continuous development of the purchasing team is vital for streamlining processes and improving collaboration with production sites.
Skill Enhancement Programs
Conducting regular training programs on negotiation, analytics, and communication can empower the purchasing staff.
A well-trained team can make informed decisions promptly and negotiate better terms with suppliers.
Cross-Departmental Workshops
Facilitating workshops that include both purchasing and production staff can improve understanding and cooperation.
These workshops can foster a culture of collaboration, enabling both departments to work towards common objectives more effectively.
Implementing Continuous Improvement Strategies
The process of process reform doesn’t end once initial changes are made; it’s ongoing.
Establishing continuous improvement strategies is essential for maintaining long-term success and collaboration.
Regular Process Audits
Conduct regular audits of the purchasing processes to identify any discrepancies or bottlenecks.
These audits can help in understanding areas that may need refinement or adjustment, ensuring that processes remain effective.
Feedback Mechanisms
Providing mechanisms for feedback from both the purchasing department and production sites is valuable.
This feedback can give insights into what’s working well and areas that might need more attention.
Incorporating this feedback into the strategies adopted helps in refining processes continually.
In conclusion, transforming the purchasing department’s processes to bolster collaboration with production sites involves a strategic approach.
By aligning goals, leveraging technology, nurturing supplier relationships, enhancing staff skills, and fostering a culture of continuous improvement, companies can achieve seamless operations that drive success.
Such reforms not only assure smooth production flow but also contribute significantly to improving the bottom line.
資料ダウンロード
QCD調達購買管理クラウド「newji」は、調達購買部門で必要なQCD管理全てを備えた、現場特化型兼クラウド型の今世紀最高の購買管理システムとなります。
ユーザー登録
調達購買業務の効率化だけでなく、システムを導入することで、コスト削減や製品・資材のステータス可視化のほか、属人化していた購買情報の共有化による内部不正防止や統制にも役立ちます。
NEWJI DX
製造業に特化したデジタルトランスフォーメーション(DX)の実現を目指す請負開発型のコンサルティングサービスです。AI、iPaaS、および先端の技術を駆使して、製造プロセスの効率化、業務効率化、チームワーク強化、コスト削減、品質向上を実現します。このサービスは、製造業の課題を深く理解し、それに対する最適なデジタルソリューションを提供することで、企業が持続的な成長とイノベーションを達成できるようサポートします。
オンライン講座
製造業、主に購買・調達部門にお勤めの方々に向けた情報を配信しております。
新任の方やベテランの方、管理職を対象とした幅広いコンテンツをご用意しております。
お問い合わせ
コストダウンが利益に直結する術だと理解していても、なかなか前に進めることができない状況。そんな時は、newjiのコストダウン自動化機能で大きく利益貢献しよう!
(Β版非公開)