- お役立ち記事
- Parts standardization and supply chain simplification strategy led by purchasing department
Parts standardization and supply chain simplification strategy led by purchasing department
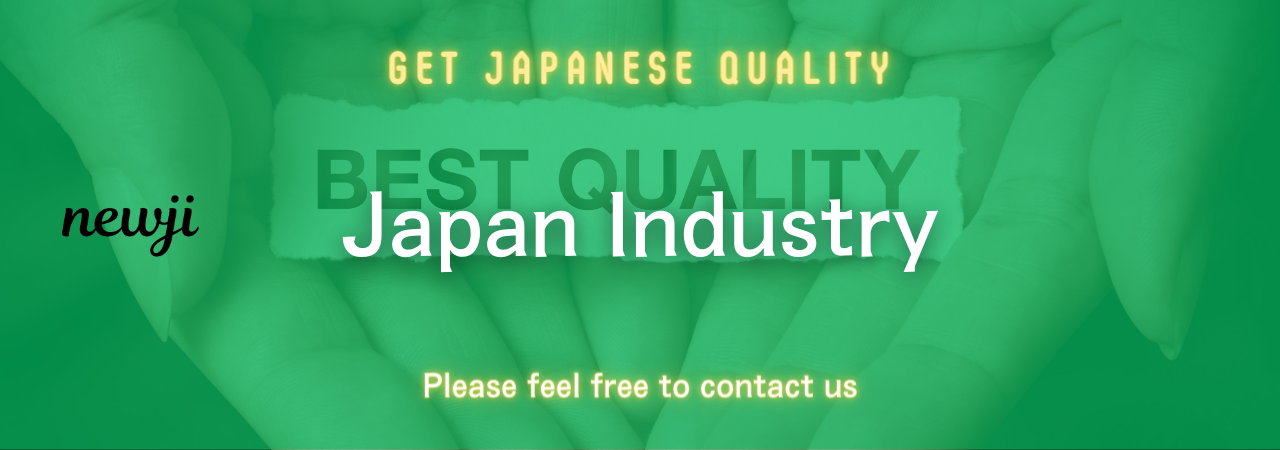
目次
Understanding Parts Standardization
Parts standardization is the process of using uniform components and specifications across various products and product lines.
It involves the procurement of interchangeable parts that can be used in multiple applications to streamline production, reduce costs, and simplify maintenance.
The purchasing department plays a critical role in ensuring that parts standardization is effectively implemented within an organization.
By working closely with engineering, manufacturing, and quality assurance teams, the purchasing department can identify opportunities for standardization and negotiate with suppliers to ensure the best terms possible.
Benefits of Parts Standardization
One of the main advantages of parts standardization is cost reduction.
By using standardized parts, companies can achieve economies of scale, as buying in bulk often leads to discount pricing.
This results in lower overall material costs.
Standardization also simplifies inventory management.
With fewer unique components to manage, the purchasing department can streamline inventory processes, reducing storage requirements and minimizing the risk of stockouts or overstock situations.
Moreover, parts standardization enhances quality and reliability.
Standardized parts mean more tested and proven components, leading to consistent performance and fewer quality issues.
This consistency can increase product reliability and reduce maintenance and warranty claims.
Supply Chain Simplification
Supply chain simplification is about making the process of getting products from suppliers to customers as efficient and cost-effective as possible.
By reducing the number of parts and suppliers, companies can significantly streamline their supply chain operations.
The purchasing department is integral to this process, acting as the liaison between the company and its suppliers.
Reducing Supplier Complexity
With parts standardization, the purchasing department can reduce supplier complexity by consolidating contracts with fewer suppliers.
Managing fewer supplier relationships simplifies the supply chain, leading to less administrative work and stronger partnerships with selected suppliers.
This focus can foster collaboration and innovation between the company and its suppliers, resulting in better service and more favorable terms.
Improved Demand Forecasting
Simplifying the supply chain through standardization helps in improving demand forecasting.
With fewer parts and a clearer understanding of production needs, companies can more accurately predict demand.
This forecasting leads to improved planning and allocation of resources, reducing costs associated with rush orders or excess inventory.
Enhanced Risk Management
A simplified supply chain also enhances risk management.
By relying on standardized parts and a select group of trusted suppliers, companies can mitigate the risks of supply disruptions.
Fewer variables and dependencies equate to fewer opportunities for unforeseen issues, leading to a more resilient supply chain.
The Role of the Purchasing Department
The purchasing department’s role in parts standardization and supply chain simplification cannot be overstated.
It requires a strategic approach to balance cost-saving initiatives with quality assurance and operational efficiency.
Collaboration and Communication
For successful implementation of a standardization strategy, the purchasing department must maintain strong communication with other departments within the organization.
Working with engineering ensures that standardized parts meet the technical specifications required for the products.
Collaboration with manufacturing guarantees these parts fit seamlessly into production processes.
Additionally, feedback from quality assurance helps ensure that standardized parts do not compromise product quality.
Supplier Relationship Management
The purchasing department is responsible for cultivating and maintaining relationships with suppliers.
Effective supplier relationship management is crucial in negotiating favorable terms for standardized parts, securing reliable deliveries, and fostering innovation.
Developing strong partnerships with suppliers can lead to improved products and significant competitive advantage.
Continuous Improvement
The purchasing department should constantly seek opportunities for improvement in parts standardization and supply chain operations.
Monitoring performance metrics, evaluating supplier performance, and exploring advancements in technology can help identify areas where further simplification and cost savings can be achieved.
By staying proactive, the department can adapt to changes in market conditions or organizational goals and continue to drive efficiencies in the supply chain.
Challenges and Considerations
While parts standardization and supply chain simplification offer numerous benefits, they are not without challenges.
Balancing Standardization with Innovation
One significant challenge is balancing standardization with the need for product innovation.
Standardized parts can sometimes limit design flexibility, potentially stifling creativity and innovation.
To overcome this, organizations need to ensure that their parts standardization strategy includes scope for customization and flexibility where necessary.
Managing Change
Implementing a parts standardization strategy often requires significant change management.
Employees across various departments need to be trained and aligned with new processes.
Overcoming resistance to change and ensuring buy-in at all levels of the organization is crucial for the success of the strategy.
Potential Supplier Resistance
Suppliers may resist standardization efforts if they fear losing business due to reduced part variation or consolidation of suppliers.
Open, transparent communication with suppliers about the benefits of long-term partnerships and potential opportunities for collaboration can help alleviate concerns.
Conclusion
The parts standardization and supply chain simplification strategy led by the purchasing department can significantly enhance operational efficiency, reduce costs, and deliver a competitive edge for organizations.
By fostering collaboration, managing supplier relationships, and continually seeking improvement, the purchasing department becomes a driving force for organizational success in today’s dynamic market.
However, it requires careful planning, implementation, and ongoing management to address the associated challenges and ensure the strategy yields the desired results.
資料ダウンロード
QCD調達購買管理クラウド「newji」は、調達購買部門で必要なQCD管理全てを備えた、現場特化型兼クラウド型の今世紀最高の購買管理システムとなります。
ユーザー登録
調達購買業務の効率化だけでなく、システムを導入することで、コスト削減や製品・資材のステータス可視化のほか、属人化していた購買情報の共有化による内部不正防止や統制にも役立ちます。
NEWJI DX
製造業に特化したデジタルトランスフォーメーション(DX)の実現を目指す請負開発型のコンサルティングサービスです。AI、iPaaS、および先端の技術を駆使して、製造プロセスの効率化、業務効率化、チームワーク強化、コスト削減、品質向上を実現します。このサービスは、製造業の課題を深く理解し、それに対する最適なデジタルソリューションを提供することで、企業が持続的な成長とイノベーションを達成できるようサポートします。
オンライン講座
製造業、主に購買・調達部門にお勤めの方々に向けた情報を配信しております。
新任の方やベテランの方、管理職を対象とした幅広いコンテンツをご用意しております。
お問い合わせ
コストダウンが利益に直結する術だと理解していても、なかなか前に進めることができない状況。そんな時は、newjiのコストダウン自動化機能で大きく利益貢献しよう!
(Β版非公開)