- お役立ち記事
- Specific example of annual planning for purchasing department for successful procurement strategy
Specific example of annual planning for purchasing department for successful procurement strategy
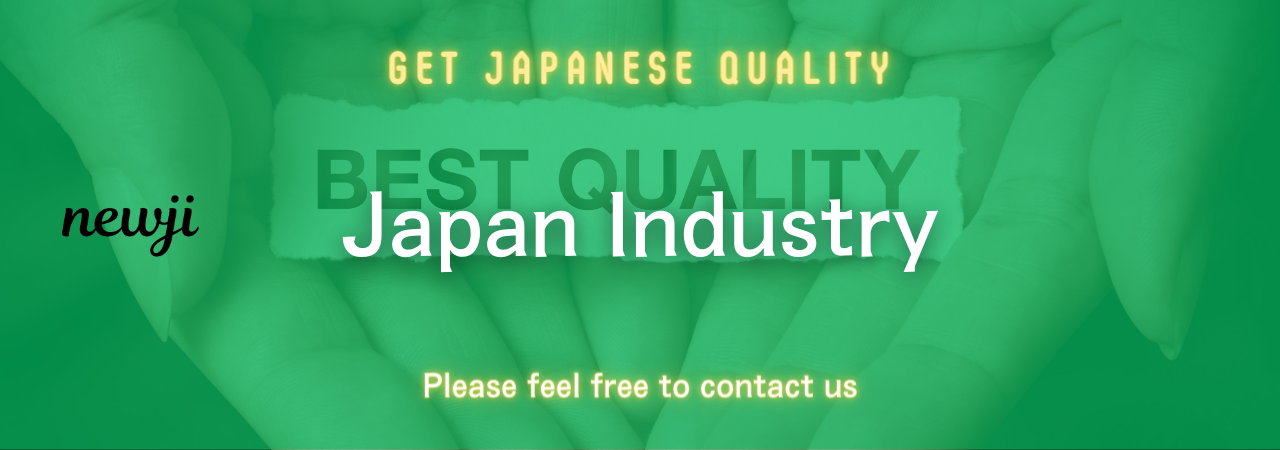
目次
Understanding the Importance of Annual Planning in Procurement
The purchasing department plays a crucial role in any organization.
Their primary responsibility is to ensure that the needed goods and services are procured efficiently and cost-effectively.
A well-planned purchasing strategy is essential for the smooth operation of the company and for maintaining financial health.
Annual planning in the purchasing department helps streamline procurement processes, forecast demand, and manage supplier relationships effectively.
Creating a clear and detailed annual plan enables purchasing managers to anticipate challenges, optimize resources, and achieve cost efficiencies.
By having a strategic approach to procurement, businesses can enhance their competitive edge and support long-term growth.
Key Components of an Annual Procurement Plan
An effective annual procurement plan should encompass several key components.
These elements help guide purchasing decisions and address potential challenges throughout the year.
1. Demand Forecasting
Accurate demand forecasting is fundamental for any procurement strategy.
By analyzing historical data and market trends, businesses can predict the quantities of products or services they’ll require over the coming year.
This information is crucial in preventing both overstocking and stockouts, which can lead to financial loss and operational disruptions.
Demand forecasting involves close collaboration between the purchasing department and other business units, such as sales and operations.
Regular reviews and updates to forecasts are necessary to address any unexpected changes in market conditions.
2. Budget Planning
A robust budget forms the backbone of a successful procurement strategy.
The purchasing department must work in tandem with the finance team to allocate appropriate funds for various procurement activities, taking into consideration the forecasted demand and expected market prices.
Budget planning allows organizations to prioritize spending, control costs, and avoid overspending.
It also aids in identifying opportunities for cost savings and negotiating better terms with suppliers.
3. Supplier Management
Maintaining strong relationships with suppliers is pivotal to ensuring a reliable supply chain.
The procurement plan should include strategies for selecting, evaluating, and maintaining a network of dependable suppliers.
This involves setting criteria for supplier selection, such as quality, delivery reliability, and cost competitiveness.
Supplier management also includes regular performance evaluations and fostering an open line of communication to address issues proactively.
Building long-term partnerships with key suppliers can lead to better negotiation outcomes and a more resilient supply chain.
4. Risk Management
Risks associated with procurement can have significant impacts on an organization.
An effective procurement plan identifies potential risks, such as supply chain disruptions, price volatility, and compliance issues, and outlines strategies to mitigate them.
Risk management strategies may involve diversifying the supplier base, implementing contingency plans, and continuously monitoring the external environment for emerging threats.
Regular risk assessments and updating of the procurement plan are necessary to adapt to changing conditions and maintain resilience against unforeseen challenges.
5. Performance Metrics
Setting clear performance metrics and KPIs (Key Performance Indicators) allows the purchasing department to measure the efficiency and effectiveness of their procurement activities.
These metrics may include cost savings achieved, procurement lead time, supplier performance, and inventory turnover rates.
Regularly reviewing these metrics helps identify areas for improvement and informs decision-making to enhance the procurement process.
Performance metrics also provide transparency and accountability within the purchasing department and the wider organization.
Implementing the Annual Procurement Plan
Once the annual procurement plan is in place, it is critical to ensure its implementation throughout the organization.
This involves communicating the plan to all relevant stakeholders, including procurement staff, suppliers, and finance teams.
Training and Development
Investing in the training and development of procurement staff is essential for successful plan implementation.
Employees should be well-versed in industry best practices, new technologies, and the organization’s procurement policies.
Regular training sessions and workshops can enhance the skills and knowledge of procurement teams, enabling them to execute the plan effectively.
Utilizing Technology
Leveraging technology can optimize the procurement process and enhance decision-making.
Procurement software solutions streamline activities such as purchase order management, supplier communication, and data analysis.
These tools provide real-time insights into spending trends and supplier performance, facilitating data-driven decisions.
Adopting e-procurement systems also reduces paperwork, minimizes errors, and ensures compliance with procurement policies.
Review and Adaptation
The annual procurement plan is not static; it requires ongoing review and adaptation to remain relevant in a dynamic business environment.
Regular evaluations of the plan’s effectiveness should be conducted, and adjustments made based on performance metrics and changes in the external environment.
Feedback from stakeholders and suppliers is valuable in identifying areas for improvement and ensuring alignment with organizational goals.
Flexibility and responsiveness are essential for adapting the procurement strategy to meet evolving business needs.
Conclusion
A specific example of an annual planning process for the purchasing department underlines the importance of a strategic approach to procurement.
By focusing on demand forecasting, budgeting, supplier management, risk management, and performance metrics, organizations can enhance their procurement efficiency and support their overall business objectives.
Implementing and adapting this plan requires collaboration, training, and the integration of technology to achieve desired outcomes.
A well-executed procurement strategy not only leads to cost savings and operational efficiency but also strengthens the organization’s ability to compete in the marketplace.
資料ダウンロード
QCD調達購買管理クラウド「newji」は、調達購買部門で必要なQCD管理全てを備えた、現場特化型兼クラウド型の今世紀最高の購買管理システムとなります。
ユーザー登録
調達購買業務の効率化だけでなく、システムを導入することで、コスト削減や製品・資材のステータス可視化のほか、属人化していた購買情報の共有化による内部不正防止や統制にも役立ちます。
NEWJI DX
製造業に特化したデジタルトランスフォーメーション(DX)の実現を目指す請負開発型のコンサルティングサービスです。AI、iPaaS、および先端の技術を駆使して、製造プロセスの効率化、業務効率化、チームワーク強化、コスト削減、品質向上を実現します。このサービスは、製造業の課題を深く理解し、それに対する最適なデジタルソリューションを提供することで、企業が持続的な成長とイノベーションを達成できるようサポートします。
オンライン講座
製造業、主に購買・調達部門にお勤めの方々に向けた情報を配信しております。
新任の方やベテランの方、管理職を対象とした幅広いコンテンツをご用意しております。
お問い合わせ
コストダウンが利益に直結する術だと理解していても、なかなか前に進めることができない状況。そんな時は、newjiのコストダウン自動化機能で大きく利益貢献しよう!
(Β版非公開)