- お役立ち記事
- Searching for solutions to logistics delay problems faced by purchasing departments
Searching for solutions to logistics delay problems faced by purchasing departments
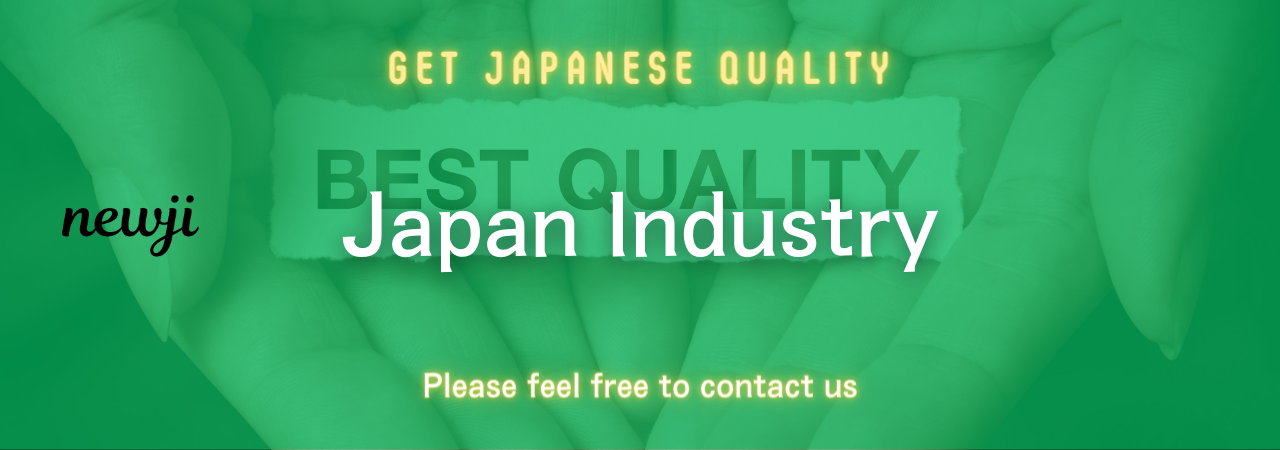
目次
Understanding Logistics Delays
Logistics delays can become significant obstacles for purchasing departments in any organization.
These delays disrupt supply chains, affect production schedules, and ultimately impact customer satisfaction.
To effectively address these challenges, it is crucial to understand the root causes of logistics delays.
By doing so, teams can develop strategies to mitigate disruptions and enhance efficiency.
For purchasing departments, managing logistics is a complex task that involves coordination with suppliers, transportation partners, and warehousing facilities.
It also includes taking into account international borders, regulations, and unexpected events such as weather conditions or political instability.
Thus, identifying the problem areas is the first step towards finding solutions.
Common Causes of Logistics Delays
Supplier Issues
Suppliers play a critical role in the supply chain.
Delays in supplier fulfillment can be attributed to various factors such as material shortages, production delays, or labor strikes.
These issues can lead to a ripple effect, hindering the timely delivery of goods.
Transportation Challenges
Transportation is another common source of delays.
Frequent problems include congestion at ports, limited cargo capacity, and unpredictable transit times.
Vehicle breakdowns and poor road conditions can also contribute to unforeseen delays.
Customs and Regulations
For international shipments, navigating customs and complying with regulations can be time-consuming.
Documents may require further scrutiny, or shipments can be delayed due to non-compliance with import/export regulations.
Managing these hurdles effectively is crucial for maintaining smooth operations.
Warehouse and Inventory Management
Inadequate warehouse or inventory management can cause significant slowdowns.
Delays may arise from inaccuracies in inventory records, inefficient packing processes, or lack of space for stock.
Proper inventory forecasting and efficient warehouse management are essential to prevent disruptions.
Strategies to Mitigate Logistics Delays
Enhancing Supplier Relationships
Fostering strong relationships with suppliers is vital for purchasing departments.
By maintaining open lines of communication, they can anticipate potential issues and collaboratively find solutions.
Long-term partnership agreements can ensure priority treatment during peak times or when unforeseen events occur.
Improving Transportation Efficiency
Investing in reliable transportation partners and optimizing routes can significantly reduce delays.
Utilizing technology, such as GPS tracking and real-time monitoring systems, helps in managing transit times and promptly addressing any arising issues.
Flexibility in choosing different modes of transport can further mitigate risks.
Streamlining Customs Processes
To reduce customs-related delays, organizations can work with customs brokers who are familiar with local regulations.
Ensuring that all documentation is accurate and complete before shipments is crucial.
Implementing software solutions that automate compliance checks can also save time and prevent errors.
Optimizing Warehouse Operations
Adopting advanced warehouse management systems can enhance inventory accuracy and streamline operations.
Techniques such as just-in-time inventory and cross-docking help reduce storage time and improve efficiency.
Regular audits and staff training ensure that best practices are followed consistently.
The Role of Technology in Addressing Logistics Delays
Technology offers a plethora of tools that can aid purchasing departments in managing logistics delays.
Using advanced analytics can help predict disruptions and enable proactive measures.
Simulation models can assess different scenarios, helping to develop effective contingency plans.
Digital platforms facilitate better coordination between different stakeholders across the supply chain.
Cloud-based systems provide real-time visibility, enabling quick decision-making and improving overall supply chain agility.
Moreover, leveraging automation in administrative tasks allows teams to focus on strategic problem-solving instead of mundane processes.
Emphasizing Collaboration and Communication
Effective communication is the cornerstone of addressing logistics delays.
Purchasing departments should establish a culture of collaboration with all supply chain partners.
Bringing together different teams to share insights and workflows promotes mutual understanding and accountability.
Regular meetings and reviews help in identifying potential bottlenecks and developing collective solutions.
Additionally, having clear communication protocols ensures that any arising issues are addressed promptly.
When everyone involved in the supply chain is on the same page, delays can be minimized, and efficiency will improve.
Preparing for the Future
As logistics become increasingly global and complex, purchasing departments must proactively prepare for future challenges.
Staying informed about industry developments and trends can help in adapting to emerging technologies and practices.
Investing in staff training and upskilling ensures that employees are equipped to handle evolving demands.
Furthermore, resiliency planning should be a priority, with robust contingency strategies in place for dealing with unexpected disruptions.
By focusing on continuous improvement and leveraging technology, organizations can achieve significant gains in efficiency and reliability.
In the quest for solutions to logistics delays, identifying core issues and implementing strategic measures can transform challenges into opportunities for growth and innovation.
資料ダウンロード
QCD調達購買管理クラウド「newji」は、調達購買部門で必要なQCD管理全てを備えた、現場特化型兼クラウド型の今世紀最高の購買管理システムとなります。
ユーザー登録
調達購買業務の効率化だけでなく、システムを導入することで、コスト削減や製品・資材のステータス可視化のほか、属人化していた購買情報の共有化による内部不正防止や統制にも役立ちます。
NEWJI DX
製造業に特化したデジタルトランスフォーメーション(DX)の実現を目指す請負開発型のコンサルティングサービスです。AI、iPaaS、および先端の技術を駆使して、製造プロセスの効率化、業務効率化、チームワーク強化、コスト削減、品質向上を実現します。このサービスは、製造業の課題を深く理解し、それに対する最適なデジタルソリューションを提供することで、企業が持続的な成長とイノベーションを達成できるようサポートします。
オンライン講座
製造業、主に購買・調達部門にお勤めの方々に向けた情報を配信しております。
新任の方やベテランの方、管理職を対象とした幅広いコンテンツをご用意しております。
お問い合わせ
コストダウンが利益に直結する術だと理解していても、なかなか前に進めることができない状況。そんな時は、newjiのコストダウン自動化機能で大きく利益貢献しよう!
(Β版非公開)