- お役立ち記事
- Benefits and risks of a purchasing department-led multi-supplier strategy
Benefits and risks of a purchasing department-led multi-supplier strategy
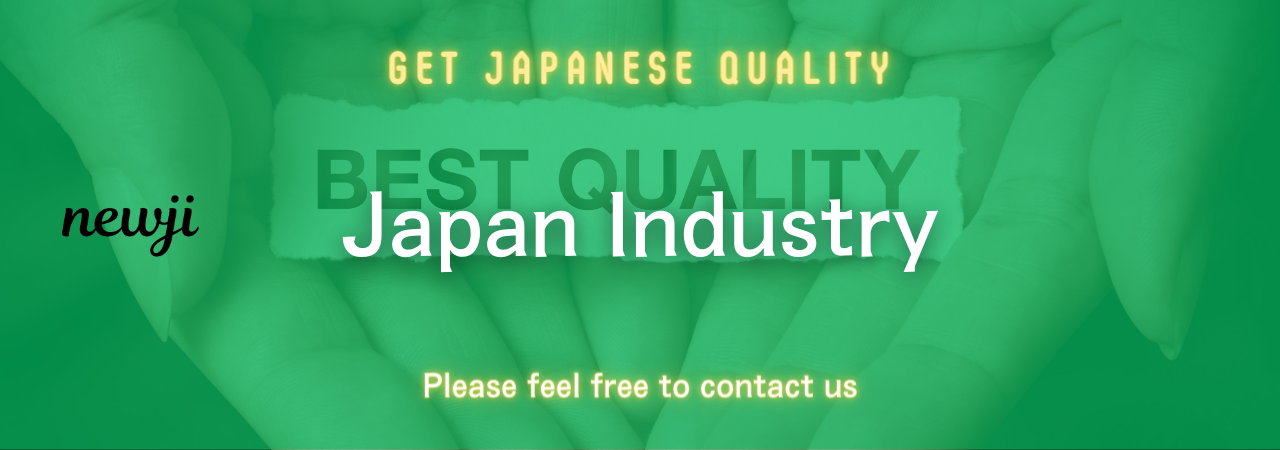
目次
Introduction to Multi-Supplier Strategy
In the world of procurement and supply chain management, a multi-supplier strategy is a widely adopted practice by many organizations.
This approach involves sourcing materials or services from multiple suppliers rather than relying on a single supplier.
The purchasing department often leads this strategy to ensure stability and versatility in the supply chain.
But what exactly are the benefits and risks associated with this strategy?
Let’s delve into the details.
Benefits of a Multi-Supplier Strategy
Increased Flexibility and Resilience
One of the primary benefits of a multi-supplier strategy is increased flexibility.
Having multiple suppliers means that if one supplier faces disruption, the company can still obtain goods or services from another supplier without significant delays.
This resilience is crucial for maintaining operations without interruptions, especially in industries where time-sensitive deliveries are critical.
Competitive Pricing
A multi-supplier strategy allows the purchasing department to leverage competitive pricing.
By sourcing from multiple suppliers, companies can encourage competition among suppliers to offer the best prices and terms.
This can lead to cost savings, improving the company’s overall profitability.
Risk Mitigation
Relying on a single supplier can expose a business to various risks, including supply disruptions, quality issues, or financial instability of the supplier.
With multiple suppliers, these risks are mitigated, providing a safety net that ensures continuity and quality control.
Access to Innovative Solutions
Working with different suppliers can expose a company to new technologies and innovations.
Each supplier may offer unique approaches or technologies that can enhance the supply chain or product offerings.
This diversity can be a significant advantage in staying competitive in the market.
Better Supplier Relationship Management
When the purchasing department manages relationships with multiple suppliers, they engage with diverse supplier networks.
This can lead to improved communication and stronger, more collaborative partnerships.
These robust relationships can result in better service levels and innovative collaboration.
Risks of a Multi-Supplier Strategy
Complexity in Management
With multiple suppliers, the complexity of managing procurement tasks increases significantly.
The purchasing department must allocate more resources to manage contracts, relationships, and communications across the supplier network.
This complexity can lead to inefficiencies if not managed effectively.
Supplier Quality Variability
Different suppliers may adhere to varying quality standards.
Maintaining consistent product or service quality can be challenging when dealing with multiple suppliers.
It requires ongoing monitoring and evaluation, adding to the workload of the purchasing department.
Increased Administrative Costs
With a multi-supplier approach, administrative tasks such as negotiation, contract management, and compliance checks increase.
These tasks require additional time and resources, potentially leading to higher operational costs for the purchasing department.
Negotiation Challenges
While competitive pricing is a benefit, negotiating with multiple suppliers can be a challenging and time-consuming process.
The purchasing department must strike a balance between competitive tension and maintaining good supplier relationships.
Potential for Inconsistencies
Inconsistent lead times or service levels from different suppliers can lead to operational inefficiencies.
These inconsistencies require additional coordination and planning to ensure that the supply chain operates smoothly.
Implementing a Multi-Supplier Strategy Successfully
Effective Supplier Evaluation
To mitigate the risks associated with a multi-supplier strategy, a thorough evaluation process for selecting suppliers is crucial.
The purchasing department must consider factors such as supplier reliability, quality, cost, and financial stability before entering into agreements.
Strong Communication Channels
Maintaining open and effective communication with all suppliers is vital.
Regular check-ins, performance reviews, and feedback sessions can help foster positive relationships and ensure alignment with the company’s objectives.
Clear Contract Management
Having clear and concise contracts with each supplier can prevent misunderstandings and ensure all parties are aware of their responsibilities and expectations.
The purchasing department should also regularly review and update contracts to reflect any changes in the business environment.
Leveraging Technology
Utilizing supply chain management software can simplify the management of multiple suppliers.
These tools provide real-time data and analytics, helping the purchasing department make informed decisions and optimize supplier interactions.
Conclusion
A purchasing department-led multi-supplier strategy offers significant benefits, such as increased flexibility, competitive pricing, and access to innovative solutions.
However, it also presents challenges in managing complexity, ensuring quality consistency, and controlling administrative costs.
For businesses looking to implement this strategy, careful planning, supplier evaluation, and effective communication are key to maximizing the benefits and minimizing the risks.
By balancing these elements, organizations can build a resilient and efficient supply chain for long-term success.
In a rapidly changing business environment, a well-managed multi-supplier strategy can be a cornerstone of a robust procurement strategy, helping companies navigate uncertainties and seize new opportunities.
資料ダウンロード
QCD調達購買管理クラウド「newji」は、調達購買部門で必要なQCD管理全てを備えた、現場特化型兼クラウド型の今世紀最高の購買管理システムとなります。
ユーザー登録
調達購買業務の効率化だけでなく、システムを導入することで、コスト削減や製品・資材のステータス可視化のほか、属人化していた購買情報の共有化による内部不正防止や統制にも役立ちます。
NEWJI DX
製造業に特化したデジタルトランスフォーメーション(DX)の実現を目指す請負開発型のコンサルティングサービスです。AI、iPaaS、および先端の技術を駆使して、製造プロセスの効率化、業務効率化、チームワーク強化、コスト削減、品質向上を実現します。このサービスは、製造業の課題を深く理解し、それに対する最適なデジタルソリューションを提供することで、企業が持続的な成長とイノベーションを達成できるようサポートします。
オンライン講座
製造業、主に購買・調達部門にお勤めの方々に向けた情報を配信しております。
新任の方やベテランの方、管理職を対象とした幅広いコンテンツをご用意しております。
お問い合わせ
コストダウンが利益に直結する術だと理解していても、なかなか前に進めることができない状況。そんな時は、newjiのコストダウン自動化機能で大きく利益貢献しよう!
(Β版非公開)