- お役立ち記事
- Unlocking Efficiency: Understanding “Production Lead Time” in Japanese Manufacturing
Unlocking Efficiency: Understanding “Production Lead Time” in Japanese Manufacturing
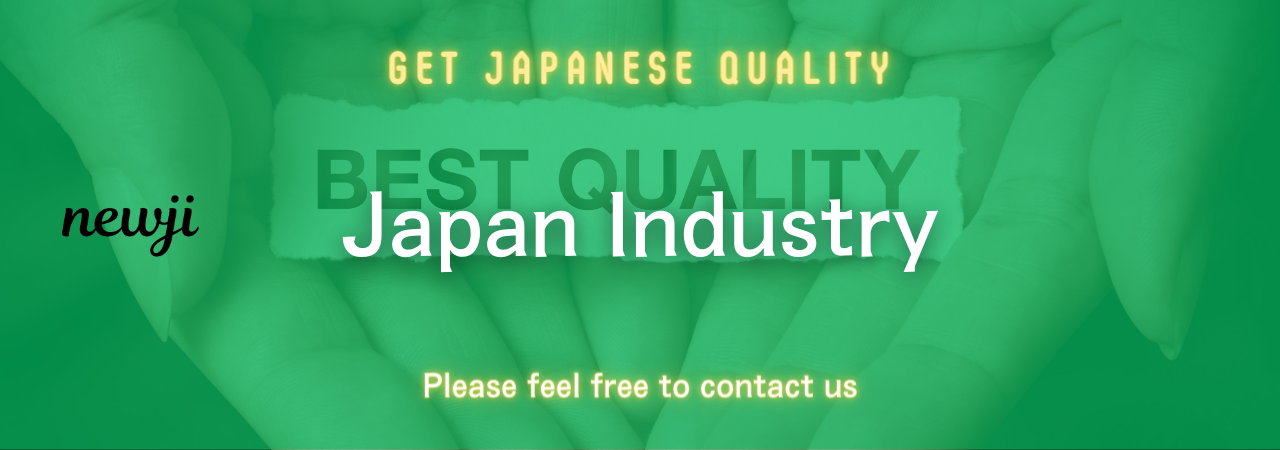
目次
Introduction to Production Lead Time in Japanese Manufacturing
Production lead time is a critical metric in manufacturing, representing the total time taken from the initiation of a production process to its completion. In Japanese manufacturing, the emphasis on efficiency and precision makes understanding and optimizing production lead time essential for maintaining competitive advantage.
The Importance of Production Lead Time
Production lead time directly impacts a company’s ability to respond to market demands, manage inventory levels, and maintain customer satisfaction. Shorter lead times enable quicker response to changes, reducing the risk of overstocking or stockouts. In the context of Japanese manufacturing, where quality and reliability are paramount, optimizing lead time ensures that products meet high standards without unnecessary delays.
Impact on Supply Chain Management
Efficient production lead time enhances supply chain management by improving synchronization between different stages of production and distribution. This synchronization minimizes delays, reduces costs, and ensures timely delivery of products to customers.
Customer Satisfaction and Market Responsiveness
Shorter production lead times allow companies to be more responsive to customer needs and market trends. This responsiveness is crucial in maintaining customer satisfaction and adapting to evolving market conditions.
Key Components of Production Lead Time
Understanding the various components that contribute to production lead time is essential for identifying areas of improvement. These components include:
Order Processing Time
This refers to the time taken from receiving an order to initiating production. Efficient order processing involves accurate order entry, validation, and scheduling.
Production Time
The actual manufacturing time required to produce the goods. This includes machine setup, processing, and assembly times, which are critical factors in determining overall lead time.
Quality Control and Inspection
Ensuring that products meet quality standards involves time-consuming inspection and testing processes. Balancing quality assurance with lead time is key to maintaining both efficiency and product reliability.
Material Procurement
The availability of raw materials and components can significantly impact production lead time. Efficient procurement processes ensure that materials are available when needed, preventing delays in production.
Logistics and Shipping
The time taken to transport finished goods to customers or distribution centers is another component of lead time. Efficient logistics planning and execution are essential for timely delivery.
Advantages of Optimizing Production Lead Time
Optimizing production lead time offers numerous benefits, particularly in the competitive landscape of Japanese manufacturing.
Increased Efficiency
Reducing lead time streamlines production processes, resulting in higher operational efficiency. This efficiency translates to lower production costs and improved profitability.
Enhanced Flexibility
Shorter lead times provide manufacturers with greater flexibility to adapt to changes in customer demand and market conditions. This adaptability is crucial for maintaining relevance in dynamic markets.
Improved Cash Flow
Efficient production lead times reduce the time between order receipt and payment, enhancing cash flow. Better cash flow management supports business growth and stability.
Competitive Advantage
Companies that can consistently deliver products faster than their competitors gain a significant market advantage. This advantage is particularly important in industries where speed to market is a key differentiator.
Challenges in Managing Production Lead Time
While optimizing production lead time offers numerous benefits, it also presents several challenges that manufacturers must address.
Complex Supply Chains
Managing lead time in complex supply chains with multiple suppliers and logistics partners requires careful coordination and communication. Disruptions at any point in the supply chain can significantly impact overall lead time.
Balancing Quality and Speed
Maintaining high-quality standards while reducing lead time can be challenging. Manufacturers must find the right balance to ensure that products are both timely and reliable.
Cost Constraints
Optimizing lead time often involves investments in technology, training, and process improvements. Balancing these costs with the potential benefits requires strategic planning and resource allocation.
Market Volatility
Fluctuating market conditions and unpredictable demand can complicate efforts to optimize lead time. Manufacturers must develop flexible strategies to handle such volatility effectively.
Best Practices for Reducing Production Lead Time
Implementing best practices can help Japanese manufacturers effectively reduce production lead time while maintaining quality and efficiency.
Lean Manufacturing Principles
Adopting lean manufacturing techniques focuses on eliminating waste, streamlining processes, and improving overall efficiency. Principles such as Just-In-Time (JIT) production ensure that materials and products are produced only as needed, reducing excess inventory and lead time.
Advanced Planning and Scheduling
Utilizing advanced planning and scheduling tools helps optimize production schedules, ensuring that resources are allocated efficiently and that production bottlenecks are minimized.
Automation and Technology Integration
Investing in automation and integrating advanced technologies such as IoT and AI can enhance production processes, reduce manual interventions, and accelerate lead times.
Supplier Collaboration
Building strong relationships with suppliers fosters better communication and coordination, ensuring timely delivery of materials and reducing delays in the supply chain.
Continuous Improvement Culture
Encouraging a culture of continuous improvement empowers employees to identify and implement process enhancements, contributing to ongoing reductions in lead time.
Supplier Negotiation Techniques
Effective supplier negotiation is crucial for managing production lead time. Establishing clear communication and mutually beneficial agreements ensures that suppliers meet delivery expectations.
Building Long-Term Partnerships
Developing long-term relationships with suppliers fosters trust and collaboration, making it easier to negotiate favorable terms and ensure reliable delivery schedules.
Clear Communication of Expectations
Clearly articulating lead time requirements and quality standards helps suppliers understand and meet your expectations, reducing the risk of delays and quality issues.
Incentive Structures
Implementing incentive structures, such as bonuses for early delivery or penalties for delays, motivates suppliers to prioritize your orders and adhere to agreed-upon lead times.
Flexible Contract Terms
Including flexible terms in contracts allows for adjustments in lead time requirements based on changing market conditions, providing both parties with the ability to adapt as needed.
Performance Monitoring
Regularly monitoring supplier performance against agreed-upon lead time metrics enables proactive identification of issues and fosters continuous improvement.
Market Conditions Affecting Production Lead Time
Understanding the broader market conditions that impact production lead time is essential for effective planning and management.
Global Supply Chain Disruptions
Events such as natural disasters, geopolitical tensions, and pandemics can disrupt global supply chains, leading to delays in material procurement and increased lead times.
Demand Fluctuations
Variations in customer demand, driven by seasonal trends or economic shifts, affect production schedules and can lead to changes in lead time requirements.
Technological Advancements
Rapid advancements in technology can both positively and negatively impact lead times. While new technologies can streamline production, they may also require time for integration and training.
Regulatory Changes
Changes in industry regulations and standards can necessitate adjustments in production processes, potentially affecting lead times as manufacturers adapt to new requirements.
Competitive Pressure
Intense competition forces manufacturers to continually seek ways to reduce lead times to stay ahead of rivals and meet customer expectations for faster delivery.
Case Studies: Successful Lead Time Reduction in Japanese Manufacturing
Examining real-world examples of Japanese manufacturers who have successfully reduced production lead time provides valuable insights into effective strategies and practices.
Toyota Production System
The Toyota Production System (TPS) exemplifies lean manufacturing principles, emphasizing waste reduction, continuous improvement, and just-in-time production. This approach has enabled Toyota to achieve remarkably short production lead times while maintaining high quality.
Panasonic’s Supply Chain Integration
Panasonic has integrated its supply chain processes through advanced information systems and close collaboration with suppliers. This integration has streamlined material procurement, reduced lead times, and enhanced overall supply chain efficiency.
Canon’s Automation Initiatives
Canon has invested heavily in automation and robotics, which has significantly reduced manual interventions in the production process. These investments have led to shorter lead times, higher precision, and increased production capacity.
Technological Innovations Driving Lead Time Reduction
Advancements in technology play a pivotal role in reducing production lead time. Japanese manufacturers are at the forefront of adopting innovative technologies to enhance efficiency and speed.
Internet of Things (IoT)
IoT technology enables real-time monitoring of production processes, facilitating timely decision-making and rapid response to potential issues that could cause delays.
Artificial Intelligence (AI) and Machine Learning
AI and machine learning algorithms optimize production schedules, predict maintenance needs, and enhance quality control, all of which contribute to reducing lead times.
Additive Manufacturing
3D printing and other additive manufacturing technologies allow for rapid prototyping and production, significantly shortening the time from design to finished product.
Advanced Robotics
Sophisticated robotics systems perform repetitive and precise tasks faster and more consistently than human workers, increasing production speed and reducing lead time.
Enterprise Resource Planning (ERP) Systems
Integrated ERP systems streamline information flow across departments, enhancing coordination and reducing delays in production processes.
Quality Control and Lead Time Optimization
Maintaining high-quality standards while optimizing lead time is a delicate balance. Japanese manufacturers excel in integrating quality control measures without compromising efficiency.
Statistical Process Control (SPC)
SPC techniques monitor and control production processes through statistical methods, ensuring consistent quality and preventing defects that could cause delays.
Total Quality Management (TQM)
TQM principles emphasize continuous improvement and employee involvement in quality initiatives, fostering a culture that prioritizes both quality and efficiency.
Automated Inspection Systems
Automated inspection technologies detect defects in real-time, reducing the need for rework and minimizing delays associated with quality issues.
Root Cause Analysis
Identifying and addressing the root causes of defects and production delays ensures that problems are resolved permanently, preventing recurrence and maintaining efficient lead times.
Workforce Training and Development
A skilled and knowledgeable workforce is essential for optimizing production lead time. Japanese manufacturers invest heavily in employee training and development to enhance productivity and efficiency.
Continuous Training Programs
Ongoing training programs ensure that employees are proficient in the latest manufacturing techniques and technologies, enabling them to work more efficiently and reduce lead times.
Cross-Training Employees
Cross-training employees in multiple roles increases workforce flexibility, allowing for better resource allocation and quicker responses to production demands.
Empowerment and Engagement
Empowering employees to identify and implement process improvements fosters a proactive culture focused on reducing lead time and enhancing overall efficiency.
Lean Certification
Providing lean manufacturing certifications to employees equips them with the skills needed to implement lean principles effectively, driving continuous improvements in lead time.
Inventory Management Strategies
Effective inventory management is crucial for reducing production lead time. Properly managed inventory ensures that materials are available when needed without excessive stock holding.
Just-In-Time (JIT) Inventory
JIT inventory management minimizes inventory levels by ensuring that materials arrive exactly when needed, reducing storage costs and lead times.
Kanban Systems
Kanban systems use visual signals to control inventory flow, ensuring that production processes receive the necessary materials without overstocking.
Safety Stock Optimization
Maintaining optimal safety stock levels balances the risk of stockouts with the costs of holding excess inventory, supporting consistent production lead times.
Demand Forecasting
Accurate demand forecasting helps align inventory levels with anticipated production needs, reducing the likelihood of delays due to material shortages.
Vendor-Managed Inventory (VMI)
VMI involves suppliers managing inventory levels based on demand data, ensuring timely replenishment and reducing lead times associated with procurement.
Conclusion
Understanding and optimizing production lead time is essential for Japanese manufacturers seeking to maintain efficiency, quality, and competitiveness in a dynamic global market. By implementing best practices in lean manufacturing, adopting advanced technologies, fostering strong supplier relationships, and investing in workforce development, manufacturers can effectively reduce lead times while upholding the high standards that Japanese manufacturing is renowned for. Balancing quality and speed, navigating market conditions, and continuously seeking improvement are key to unlocking sustained efficiency and success in the manufacturing sector.
資料ダウンロード
QCD調達購買管理クラウド「newji」は、調達購買部門で必要なQCD管理全てを備えた、現場特化型兼クラウド型の今世紀最高の購買管理システムとなります。
ユーザー登録
調達購買業務の効率化だけでなく、システムを導入することで、コスト削減や製品・資材のステータス可視化のほか、属人化していた購買情報の共有化による内部不正防止や統制にも役立ちます。
NEWJI DX
製造業に特化したデジタルトランスフォーメーション(DX)の実現を目指す請負開発型のコンサルティングサービスです。AI、iPaaS、および先端の技術を駆使して、製造プロセスの効率化、業務効率化、チームワーク強化、コスト削減、品質向上を実現します。このサービスは、製造業の課題を深く理解し、それに対する最適なデジタルソリューションを提供することで、企業が持続的な成長とイノベーションを達成できるようサポートします。
オンライン講座
製造業、主に購買・調達部門にお勤めの方々に向けた情報を配信しております。
新任の方やベテランの方、管理職を対象とした幅広いコンテンツをご用意しております。
お問い合わせ
コストダウンが利益に直結する術だと理解していても、なかなか前に進めることができない状況。そんな時は、newjiのコストダウン自動化機能で大きく利益貢献しよう!
(Β版非公開)