- お役立ち記事
- Specific implementation process for automating procurement operations in the purchasing department
Specific implementation process for automating procurement operations in the purchasing department
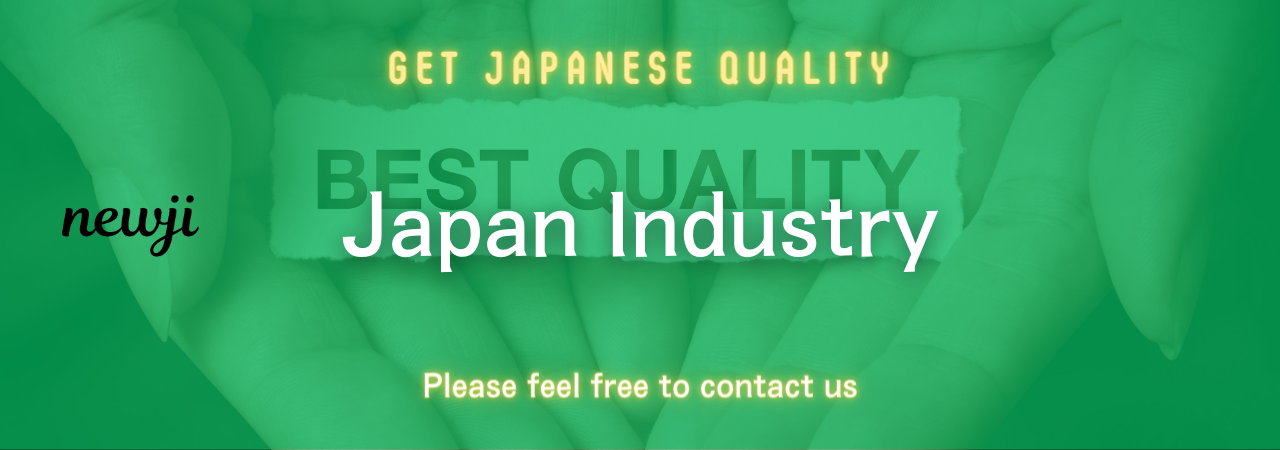
目次
Understanding the Basics of Procurement Automation
Procurement automation is a game-changer in the purchasing department, streamlining tasks that once required countless hours of manual labor.
At its core, it involves employing technology to handle repetitive and time-consuming activities such as order processing, invoice approvals, and supplier management.
The primary goal is to improve efficiency, reduce errors, and allow the team to focus on strategic tasks.
Before diving into the specifics of implementation, it’s essential to grasp the fundamentals of procurement automation.
The technology typically involves software solutions that integrate with existing systems, using data analytics and AI to optimize purchasing operations.
Common features include automated purchase requisitions, real-time analytics, and supplier collaboration portals.
As the first step, it’s important to assess the current state of procurement processes within your organization.
This involves identifying bottlenecks, inefficiencies, and tasks that consume significant resources.
By having a clear understanding of these elements, you can prioritize areas for improvement and measure potential benefits accurately.
Identifying Key Processes for Automation
The next step in implementing procurement automation is selecting which processes to automate.
Not every task will benefit from automation, so it’s critical to focus on those that will yield the most significant gains in efficiency.
Some of the key processes that are ripe for automation include:
Automated Purchase Requisitions
Manual purchase requisitions can be error-prone and inefficient.
Automating this step helps ensure that requisitions are submitted with all necessary details, approved quickly, and aligned with organizational policies.
Supplier Management
Supplier relationships are crucial for procurement success.
Automation can streamline onboarding processes, maintain up-to-date supplier data, and help with performance assessments.
This ensures suppliers meet the company’s requirements and contribute positively to the supply chain.
Invoice and Payment Automation
Processing invoices manually can lead to delays and errors.
Automating invoice approvals and payments can reduce these risks, ensure timely payments, and improve supplier relationships by avoiding late fees and building trust.
Choosing the Right Technology
After identifying the processes for automation, the next step is selecting the appropriate technology to implement these changes.
This involves researching various procurement software solutions in the market, taking into consideration factors such as:
Integration Capabilities
Ensure the chosen software can seamlessly integrate with your existing systems like ERP (Enterprise Resource Planning) and CRM (Customer Relationship Management).
This integration is crucial for maintaining data consistency and ensuring the smooth operation of business processes.
Scalability
Choose a solution that can scale with your business.
As your organization grows, your procurement needs will undoubtedly evolve.
Selecting scalable software ensures that your solution remains relevant and effective over time.
User-Friendliness
The effectiveness of any technology depends on its adoption by the team.
Selecting software with a user-friendly interface ensures that team members can quickly get up to speed and leverage the solution to its full potential.
Implementing the Automation Solution
With technology in place, the next phase involves implementation.
This step requires careful planning and execution to ensure a smooth transition from manual processes to automation.
Change Management
Implementing automation is not just about technology, but also about people.
Effective change management involves communicating the benefits of automation clearly to all stakeholders and providing the necessary training to ensure everyone is comfortable with the new system.
Pilot Testing
Before full-scale deployment, it’s advisable to conduct a pilot test.
This test helps identify any unforeseen issues and allows for adjustments without disrupting the entire procurement process.
Use the insights gained from the pilot to refine the system for an optimal rollout.
Full Deployment and Support
Once the pilot test has been successfully evaluated, proceed with full deployment.
Ensure there’s adequate support in place to address any questions or issues that may arise, thus easing the team into the new system effortlessly.
Measuring Success and Continuous Improvement
After implementation, it’s crucial to measure the success of procurement automation regularly.
This involves monitoring key performance indicators such as reduced cycle times, cost savings, and error rates.
Review these metrics periodically to ensure the automation solution is delivering the expected benefits.
Solicit feedback from the procurement team and suppliers to identify any areas for improvement or additional features that could be beneficial.
Continuous improvement should be the guiding principle.
As technologies advance, new features and capabilities will become available.
Keep abreast of these developments to continuously leverage technology in optimizing procurement processes.
Conclusion
The implementation of automation in procurement operations is a transformative step towards increased efficiency and effectiveness.
By understanding the basics, identifying key processes, choosing the right technology, and following an organized implementation plan, organizations can reap significant benefits.
With ongoing measurement and continuous improvement, the purchasing department can maintain a competitive edge and contribute to the organization’s overall success.
資料ダウンロード
QCD調達購買管理クラウド「newji」は、調達購買部門で必要なQCD管理全てを備えた、現場特化型兼クラウド型の今世紀最高の購買管理システムとなります。
ユーザー登録
調達購買業務の効率化だけでなく、システムを導入することで、コスト削減や製品・資材のステータス可視化のほか、属人化していた購買情報の共有化による内部不正防止や統制にも役立ちます。
NEWJI DX
製造業に特化したデジタルトランスフォーメーション(DX)の実現を目指す請負開発型のコンサルティングサービスです。AI、iPaaS、および先端の技術を駆使して、製造プロセスの効率化、業務効率化、チームワーク強化、コスト削減、品質向上を実現します。このサービスは、製造業の課題を深く理解し、それに対する最適なデジタルソリューションを提供することで、企業が持続的な成長とイノベーションを達成できるようサポートします。
オンライン講座
製造業、主に購買・調達部門にお勤めの方々に向けた情報を配信しております。
新任の方やベテランの方、管理職を対象とした幅広いコンテンツをご用意しております。
お問い合わせ
コストダウンが利益に直結する術だと理解していても、なかなか前に進めることができない状況。そんな時は、newjiのコストダウン自動化機能で大きく利益貢献しよう!
(Β版非公開)