- お役立ち記事
- Cost and risk optimization strategies for the manufacturing industry faced by the purchasing department
Cost and risk optimization strategies for the manufacturing industry faced by the purchasing department
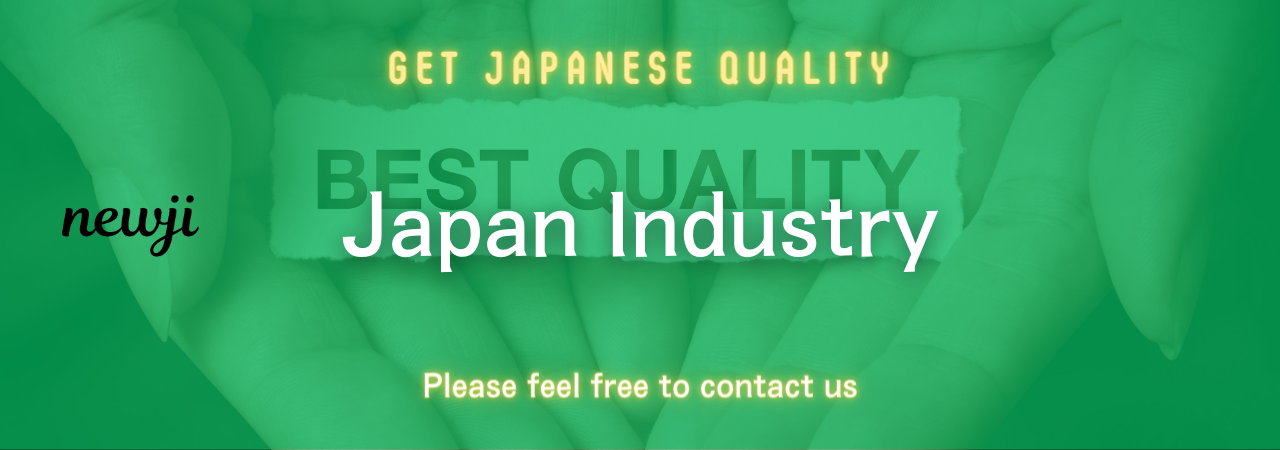
目次
Understanding Cost and Risk in Manufacturing
In the fast-paced world of manufacturing, the purchasing department plays a crucial role in determining the overall success of the company.
This department is tasked with finding the balance between cost and risk, which can be a daunting challenge.
The ultimate objective is to minimize costs while simultaneously reducing risks that could disrupt production or impact product quality.
Cost optimization involves finding ways to reduce expenses in the purchasing process.
This could include negotiating better prices with suppliers or finding alternative sources for raw materials.
On the other hand, risk optimization involves anticipating potential issues that could arise in the supply chain and finding strategies to mitigate these risks.
Analyzing Cost Drivers in Manufacturing
To achieve cost optimization, it is important to first identify the key cost drivers in your manufacturing process.
These typically include raw materials, production equipment, labor, logistics, and wastage.
1. **Raw materials**: The cost of raw materials can significantly impact overall production costs.
Monitoring market trends and establishing long-term contracts with suppliers can help in managing price fluctuations.
2. **Production equipment**: Investing in modern machinery might require a high initial cost, but it tends to lower operational costs over time.
Regular maintenance can also prevent expensive breakdowns.
3. **Labor**: Employing skilled labor is crucial, but so is managing labor efficiency.
This might mean providing additional training or using automation to reduce reliance on manual processes.
4. **Logistics**: Efficient logistics can minimize transportation costs.
Frequent evaluation of logistics partners and routes can uncover opportunities for savings.
5. **Wastage**: Reducing wastage in the production process can lower costs significantly.
Implementing lean manufacturing principles can be beneficial in achieving this.
Risk Management Strategies
Risks are inherent in any manufacturing process, but they can be managed or mitigated with strategic planning.
Building a Resilient Supply Chain
A resilient supply chain is one that can withstand disruptions without a significant impact on production.
To achieve this, the purchasing department can adopt several strategies:
1. **Supplier diversification**: Relying on a single supplier increases the risk of disruption if they experience issues.
Having multiple suppliers or dual sourcing for critical components can reduce this risk.
2. **Inventory management**: Keeping a buffer stock of essential materials can prevent halts in production in case of supplier delays.
However, this needs to be balanced with the costs associated with holding inventory.
3. **Supplier relationships**: Building strong relationships with suppliers can improve communication and collaboration, leading to faster problem-solving during crises.
Quality Assurance Procedures
Ensuring the quality of raw materials and components is vital to reduce risks related to product rework or recalls.
1. **Supplier evaluation**: Regular assessments of suppliers’ quality control processes can ensure they meet your standards.
Implementing a supplier scorecard can be an effective way to keep track.
2. **Incoming material inspections**: Conducting thorough inspections on incoming materials can catch defects early, preventing them from affecting the production line.
Financial Risk Management
Managing financial risks involves protecting the company against volatile market conditions that can affect pricing and availability.
1. **Contracts with cost escalation clauses**: When market prices increase significantly, having escalation clauses in contracts allows for adjustments in the agreed price, protecting both parties.
2. **Currency hedging**: For companies dealing with international suppliers, currency fluctuations can impact cost stability.
Currency hedging strategies can help mitigate this risk.
Utilizing Technology and Data Analytics
Advancements in technology have provided the manufacturing industry with tools to enhance both cost and risk optimization efforts.
Adopting Automation
Automation helps to increase production efficiency while reducing costs related to labor and material wastage.
Adopting robotics or AI-driven machines can lead to more consistent production quality and quicker turnaround times.
Leveraging Data Analytics
Data analytics can provide insights into purchasing patterns, supplier performance, and market trends.
Utilizing data effectively allows for better decision-making in areas such as:
1. **Demand forecasting**: Predicting future demand can help in making informed purchasing decisions and avoiding overstocking or stockouts.
2. **Supplier performance analysis**: Tracking supplier metrics over time can help identify trends that might indicate potential reliability issues.
Continuous Improvement and Collaboration
Cost and risk optimization is an ongoing process that needs continuous monitoring and improvement.
Encouraging a culture of collaboration between departments can further enhance these efforts.
Collaborative Planning
Working closely with production, logistics, and sales teams allows the purchasing department to tailor its strategies to align with company-wide goals.
Regular meetings to discuss challenges, opportunities, and upcoming demand changes foster a more cohesive approach.
Training and Development
Investing in the development of purchasing department employees ensures they remain up-to-date with the latest industry practices and technologies.
Continuous training on negotiation, contract management, and risk assessment is beneficial.
Conclusion
Balancing cost and risk optimization in the manufacturing industry is a complex task requiring a strategic, well-informed approach.
By understanding cost drivers, building a resilient supply chain, and leveraging technology, the purchasing department can significantly contribute to a company’s efficiency and success.
The key is maintaining a proactive, rather than reactive, stance and ensuring all efforts are aligned with the company’s overarching goals.
資料ダウンロード
QCD調達購買管理クラウド「newji」は、調達購買部門で必要なQCD管理全てを備えた、現場特化型兼クラウド型の今世紀最高の購買管理システムとなります。
ユーザー登録
調達購買業務の効率化だけでなく、システムを導入することで、コスト削減や製品・資材のステータス可視化のほか、属人化していた購買情報の共有化による内部不正防止や統制にも役立ちます。
NEWJI DX
製造業に特化したデジタルトランスフォーメーション(DX)の実現を目指す請負開発型のコンサルティングサービスです。AI、iPaaS、および先端の技術を駆使して、製造プロセスの効率化、業務効率化、チームワーク強化、コスト削減、品質向上を実現します。このサービスは、製造業の課題を深く理解し、それに対する最適なデジタルソリューションを提供することで、企業が持続的な成長とイノベーションを達成できるようサポートします。
オンライン講座
製造業、主に購買・調達部門にお勤めの方々に向けた情報を配信しております。
新任の方やベテランの方、管理職を対象とした幅広いコンテンツをご用意しております。
お問い合わせ
コストダウンが利益に直結する術だと理解していても、なかなか前に進めることができない状況。そんな時は、newjiのコストダウン自動化機能で大きく利益貢献しよう!
(Β版非公開)