- お役立ち記事
- A technique for balancing cost reduction and quality assurance that is important for purchasing departments
A technique for balancing cost reduction and quality assurance that is important for purchasing departments
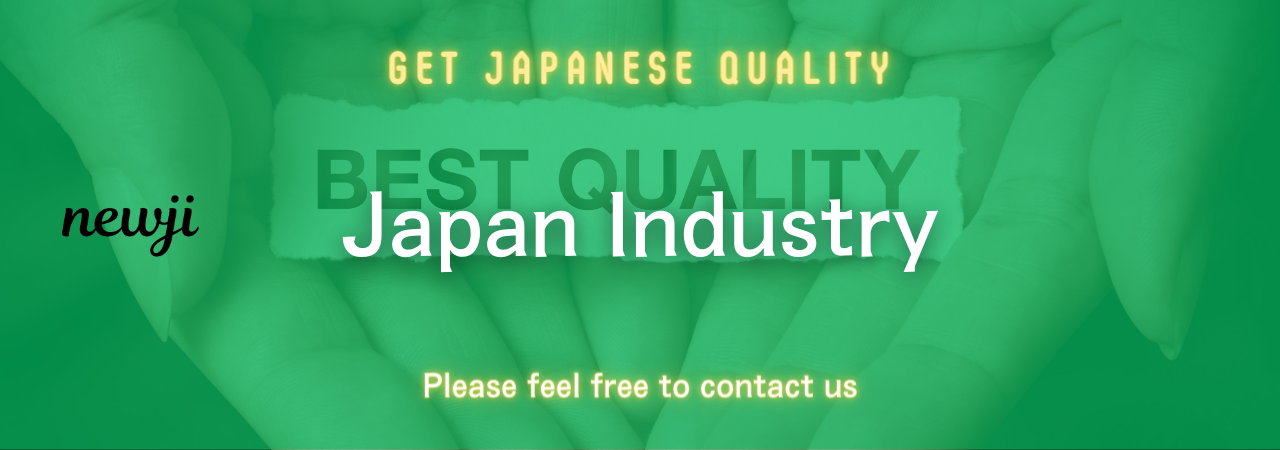
目次
Understanding Cost Reduction and Quality Assurance
In today’s competitive business environment, maintaining a balance between cost reduction and quality assurance is crucial for purchasing departments.
These two elements, while seemingly opposing, must work in harmony for the success and sustainability of any organization.
Cost reduction aims to decrease expenses and improve financial efficiency.
However, if not managed carefully, it can lead to compromised quality, which can affect customer satisfaction and damage a brand’s reputation.
On the other hand, quality assurance focuses on maintaining high standards within products or services.
While ensuring quality is essential, it can sometimes result in increased costs for the company.
Finding the right balance is key to procurement success and organizational growth.
The Importance of Balancing Cost and Quality
For purchasing departments, striking a balance between cost and quality has significant implications.
Businesses gain a competitive advantage when they manage to reduce costs without sacrificing quality.
This balance also affects the overall perception of the brand in the market.
Customers today expect value for money.
They are more informed and have higher standards regarding product quality.
If a company cuts costs but delivers inferior products, it risks losing customer loyalty and facing negative reviews.
Moreover, governmental regulations and industry standards often dictate minimum quality levels for products and services.
Failing to meet these can lead to legal challenges and fines, negating any short-term savings from prior cost reductions.
Strategies for Effective Cost Reduction
Analyze and Optimize the Supply Chain
The supply chain is one area where purchasing departments can find substantial cost-saving opportunities.
Start by analyzing the end-to-end process and identifying inefficiencies.
Negotiate better terms with suppliers, consider alternative materials, or simplify the logistics process.
Optimizing these aspects can lead to significant savings.
Leverage Technology
Utilizing advanced procurement technologies like data analytics, automation, and artificial intelligence can streamline processes and reduce errors.
Technology allows for better demand forecasting, more efficient inventory management, and improved supplier relationships.
These improvements can lead to cost reductions without adversely affecting quality.
Develop Strong Supplier Relationships
Building strong, long-term relationships with suppliers can result in favorable terms, such as discounts for bulk purchases or reduced shipping costs.
A good relationship with suppliers also fosters open communication, leading to better problem-solving and innovation.
Ensuring Quality Assurance
Define Clear Quality Standards
Establishing and communicating clear quality standards is crucial in ensuring all stakeholders understand what is expected.
These standards should align with industry norms and embed the company’s values and customer expectations.
Implement Regular Inspections
Regular inspections and audits help maintain high-quality standards.
These can be achieved through internal reviews or by hiring third-party quality assurance firms.
Inspections help identify issues early and prevent defects from reaching the end consumer.
Focus on Employee Training
Empowered employees are a vital component of quality assurance.
Investing in training and development ensures that staff understand both the importance of quality and the methods to maintain it.
Training programs can emphasize attention to detail and encourage proactive identification of quality issues.
Balancing Cost Reduction and Quality Assurance
To find the balance, purchasing departments should incorporate an integrated approach that considers both aspects during decision-making processes.
Adopt Total Cost of Ownership (TCO) Analysis
When evaluating options, consider the total cost of ownership rather than just the initial purchase price.
TCO includes costs related to maintenance, operations, and even disposal.
Often, a higher initial investment may lead to lower costs over time due to improved efficiency or durability.
Implement Continuous Improvement Practices
Practices like Lean and Six Sigma aim for efficiency and excellence.
These methodologies encourage constant evaluation and refinement of processes, ensuring both cost efficiency and quality.
By embedding these practices, organizations can adapt to changes and meet evolving demands efficiently.
Utilize Cross-Functional Teams
Collaboration across departments enhances cost-quality balance by incorporating diverse perspectives.
Cross-functional teams bring together expertise from different areas, fostering innovative solutions that take both costs and quality into account.
Conclusion
Balancing cost reduction and quality assurance is not an easy task.
However, it is essential for the long-term success of organizations.
By optimizing supply chains, leveraging technology, fostering supplier relationships, and maintaining high-quality standards, purchasing departments can achieve this balance.
An integrated approach incorporating total cost analysis, continuous improvement practices, and cross-functional collaboration ensures cost-effectiveness without sacrificing product quality.
This creates a sustainable competitive advantage in the market and crucially, retains customer trust and satisfaction.
For purchasing departments, mastering this balance is both a strategic necessity and a pathway to robust business growth.
資料ダウンロード
QCD調達購買管理クラウド「newji」は、調達購買部門で必要なQCD管理全てを備えた、現場特化型兼クラウド型の今世紀最高の購買管理システムとなります。
ユーザー登録
調達購買業務の効率化だけでなく、システムを導入することで、コスト削減や製品・資材のステータス可視化のほか、属人化していた購買情報の共有化による内部不正防止や統制にも役立ちます。
NEWJI DX
製造業に特化したデジタルトランスフォーメーション(DX)の実現を目指す請負開発型のコンサルティングサービスです。AI、iPaaS、および先端の技術を駆使して、製造プロセスの効率化、業務効率化、チームワーク強化、コスト削減、品質向上を実現します。このサービスは、製造業の課題を深く理解し、それに対する最適なデジタルソリューションを提供することで、企業が持続的な成長とイノベーションを達成できるようサポートします。
オンライン講座
製造業、主に購買・調達部門にお勤めの方々に向けた情報を配信しております。
新任の方やベテランの方、管理職を対象とした幅広いコンテンツをご用意しております。
お問い合わせ
コストダウンが利益に直結する術だと理解していても、なかなか前に進めることができない状況。そんな時は、newjiのコストダウン自動化機能で大きく利益貢献しよう!
(Β版非公開)