- お役立ち記事
- Steps for purchasing department to eliminate bottlenecks in procurement flow
Steps for purchasing department to eliminate bottlenecks in procurement flow
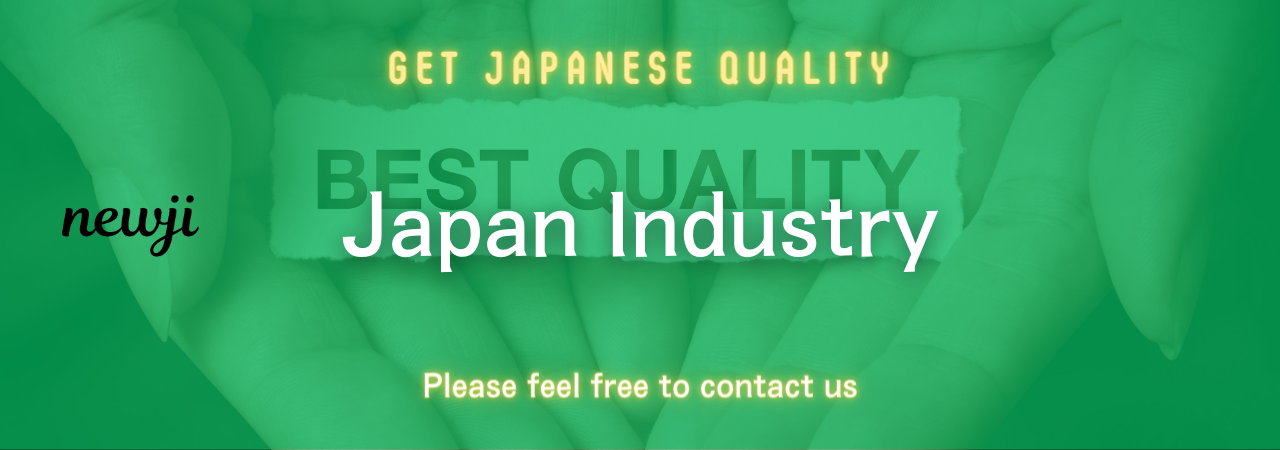
目次
Understanding Procurement Bottlenecks
In any business, smooth procurement processes are essential for maintaining steady production and minimizing operational costs.
However, bottlenecks in procurement can disrupt the flow and lead to delays and increased expenses.
Understanding where bottlenecks occur is the first step towards eliminating them and ensuring a seamless procurement process.
Bottlenecks in procurement often arise due to delays in supplier deliveries, inefficient internal processes, or inadequate communication between departments.
Recognizing these challenges is crucial for developing strategies that resolve these issues effectively.
A thorough investigation into the procurement flow will help identify specific problem areas that require attention.
Identifying the Root Causes
A comprehensive analysis is necessary to pinpoint the core issues causing procurement bottlenecks.
This involves gathering data on key metrics such as lead times, order processing times, and expenditure levels.
Analyzing these metrics will highlight trends and patterns that could be contributing to the slowdown.
Another key area to evaluate is supplier performance.
Reviewing supplier contracts, delivery timelines, and quality metrics can provide insights into potential inefficiencies in supplier relationships.
Additionally, internal processes should be scrutinized for opportunities to improve workflows and remove unnecessary steps.
Optimizing Supplier Relationships
One of the most effective ways to eliminate procurement bottlenecks is by optimizing relationships with suppliers.
Establishing strong partnerships with reliable suppliers ensures timely deliveries and high-quality materials, reducing disruptions in the procurement flow.
Start by evaluating current suppliers based on their performance history and reliability.
Consider negotiating terms to guarantee better delivery times or more favorable pricing structures.
Building long-term relationships with suppliers can lead to preferential treatment, such as priority in stock availability or expedited shipping options.
Implementing Supplier Performance Metrics
To maintain high standards, implement performance metrics for suppliers.
Metrics such as delivery accuracy, quality adherence, and communication responsiveness hold suppliers accountable and incentivize improved performance.
Regular reviews of supplier performance against these metrics will help highlight any areas in need of improvement.
For continuous improvement, consider organizing quarterly meetings with major suppliers.
These discussions can focus on setting mutually beneficial goals, addressing any concerns, and ensuring both parties are aligned in their objectives.
Streamlining Internal Processes
Another critical step is to streamline internal processes to reduce procurement bottlenecks.
Inefficient procedures can lead to delays in order processing, approvals, and inventory management.
Conduct a thorough review of existing procurement procedures and identify areas where automation or technology could enhance efficiency.
For instance, implementing a digital procurement system can offer real-time visibility into inventory levels, automate order processing, and simplify tracking.
Training and Development
Investing in the training and development of procurement staff is essential for maintaining a smooth procurement process.
Educating team members on best practices, the latest technology tools, and effective communication techniques fosters a more efficient and cohesive work environment.
Encourage collaboration and knowledge sharing among team members to promote skill enhancement and innovation.
Regular workshops or training sessions can be organized to update staff on new procurement strategies and industry developments.
Enhancing Communication and Collaboration
Effective communication is indispensable for eliminating procurement bottlenecks.
Ensure there are clear channels of communication between departments involved in the procurement process, such as finance, operations, and the procurement team itself.
Utilizing project management tools can help keep all parties informed about the status of orders, approvals, and deliveries.
These tools provide platforms for collaboration, ensuring everyone has access to the necessary information at any given time.
Cross-Functional Teams
Establishing cross-functional teams can further enhance collaboration between departments.
These teams bring together people from different functions to work on procurement projects, enabling faster decision-making and problem resolution.
Cross-functional teams can also help identify potential issues early in the process, allowing for quick adjustments before they escalate into more significant problems.
Regular team meetings and progress reviews encourage a more proactive approach to bottleneck elimination.
Leveraging Technology Solutions
Technology plays a vital role in eliminating bottlenecks in procurement.
Implementing integrated technology solutions can provide a more cohesive overview of the procurement process and highlight inefficiencies that need addressing.
Consider adopting an ERP (Enterprise Resource Planning) system that integrates various business processes, including procurement, finance, and inventory management.
This centralized approach allows for better control, monitoring, and planning of procurement activities.
Analytics and Reporting
Utilize analytics and reporting tools to gain deeper insights into the procurement flow.
These tools can reveal meaningful data trends related to order cycles, supplier performance, and cost management.
Advanced analytics can also help forecast demand and optimize inventory levels, ensuring procurement is both cost-effective and responsive to business needs.
Regularly reviewing analytics reports will assist in making informed decisions aimed at reducing bottlenecks and enhancing productivity.
Continuous Improvement and Feedback
Finally, prioritize continuous improvement and feedback within the procurement flow.
Encourage team members and suppliers to provide feedback on processes, suggesting improvements and reporting any issues they encounter.
Establish a culture of continuous improvement where innovation and adaptability are encouraged.
Regular audits and reviews of procurement processes will help identify new improvement opportunities and ensure existing solutions remain effective.
Implementing Feedback Loops
Create feedback loops that allow information to flow seamlessly between team members, departments, and suppliers.
This ongoing dialogue facilitates the identification of bottlenecks as they occur and accelerates the response in implementing timely solutions.
By fostering an environment of collaboration and innovation, businesses can eliminate bottlenecks in the procurement process, driving efficiency and ensuring reliable operations.
資料ダウンロード
QCD調達購買管理クラウド「newji」は、調達購買部門で必要なQCD管理全てを備えた、現場特化型兼クラウド型の今世紀最高の購買管理システムとなります。
ユーザー登録
調達購買業務の効率化だけでなく、システムを導入することで、コスト削減や製品・資材のステータス可視化のほか、属人化していた購買情報の共有化による内部不正防止や統制にも役立ちます。
NEWJI DX
製造業に特化したデジタルトランスフォーメーション(DX)の実現を目指す請負開発型のコンサルティングサービスです。AI、iPaaS、および先端の技術を駆使して、製造プロセスの効率化、業務効率化、チームワーク強化、コスト削減、品質向上を実現します。このサービスは、製造業の課題を深く理解し、それに対する最適なデジタルソリューションを提供することで、企業が持続的な成長とイノベーションを達成できるようサポートします。
オンライン講座
製造業、主に購買・調達部門にお勤めの方々に向けた情報を配信しております。
新任の方やベテランの方、管理職を対象とした幅広いコンテンツをご用意しております。
お問い合わせ
コストダウンが利益に直結する術だと理解していても、なかなか前に進めることができない状況。そんな時は、newjiのコストダウン自動化機能で大きく利益貢献しよう!
(Β版非公開)