- お役立ち記事
- A practical guide to shortening procurement lead times proposed by the purchasing department
A practical guide to shortening procurement lead times proposed by the purchasing department
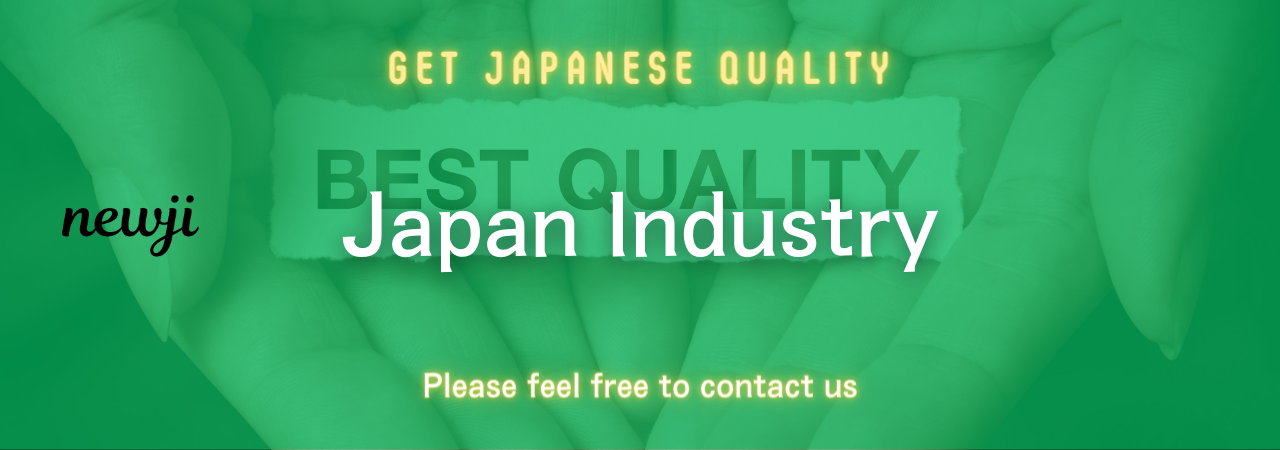
目次
Understanding Procurement Lead Times
Procurement lead time is the period between when an order is placed and when the goods or services are received.
It encompasses various stages like order processing, supplier response time, production schedules, and delivery schedules.
It’s a critical factor in supply chain management as it affects inventory levels, production planning, and customer satisfaction.
For purchasing departments, reducing procurement lead times is crucial.
It’s not just about getting materials on time.
It’s about being efficient, minimizing costs, and satisfying internal or external customers.
Identifying the Bottlenecks
The first step in shortening procurement lead times is identifying where delays occur.
Bottlenecks might be within your organization or with your suppliers.
Start by analyzing your procurement process.
Look for stages where time lags are happening.
Are purchase orders being delayed in approval? Is there a delay in communication with suppliers?
Having a clear understanding of where these bottlenecks are is essential.
You cannot fix what you do not see.
Once you have identified these areas, you can begin to design strategies to address them.
Internal Process Improvements
Improving internal processes is often where you will find the quickest wins.
Evaluate your purchase order cycle time.
Consider implementing an automated purchasing system if you’re still using a manual process.
Automation can drastically cut down on the time it takes to process orders.
Another area is supplier communication.
Ensure that communication is seamless by using updated technology like procurement software.
These platforms can facilitate instant messaging or automate reminders and follow-ups.
This reduces the back-and-forth that can happen with emails and phone calls.
Streamlining approval processes is another critical area.
Implementing a hierarchical approval system where only necessary individuals have decision-making power can significantly speed up the process.
Building Strong Supplier Relationships
Your suppliers are your partners in the procurement process.
The stronger your relationship with them, the smoother and faster your procurement activities will be.
Regular communication builds trust and can lead to preferential treatment regarding priority and pricing.
Conduct periodic supplier reviews to ensure they meet your timeline and quality expectations.
If a supplier consistently fails to deliver on time, it may be time to look for alternatives.
Having a diversified supplier list is also beneficial.
It enables you to pivot quickly if there’s a delay with one supplier.
It’s essential not to over-depend on a single source for critical materials.
Use of Technology
Utilizing advanced technology can significantly reduce procurement lead times.
Artificial Intelligence (AI) and Machine Learning (ML) can forecast inventory needs, reducing the lead time by preemptively ordering supplies based on demand trends.
Adopting Electronic Data Interchange (EDI) systems allows the purchasing department to facilitate faster exchanges of business documents with suppliers.
This reduces paperwork and speeds up the transaction times.
Consider establishing an online portal for real-time vendor interaction.
This promotes transparency and allows for progress tracking, query clarifications, and immediate issue resolution.
Inventory Management Strategies
Effective inventory management strategies can also shorten procurement lead times.
Maintaining optimal inventory levels ensures that you have enough stock to cover lead time periods.
Just-in-time (JIT) inventory is a management strategy whereby materials are only ordered as required for production.
While this reduces holding costs, it requires a very streamlined supply chain and reliable suppliers.
Safety stock is another strategy to consider.
This is extra inventory kept on hand to mitigate the risk of shortages.
However, the key is balancing safety stock to avoid excess holding costs.
Strategic Forecasting and Planning
Accurate demand forecasting is a long-term strategy to reduce procurement lead times.
The better you understand your needs, the more accurate your orders will be, and the less likely you are to face stockouts or production delays.
Incorporate historical sales data and market analysis to anticipate future requirements.
By planning, purchasing departments can negotiate better lead times with suppliers well in advance.
Develop a contingency plan.
Proactive risk management minimizes disruptions to your supply chain.
This includes identifying potential threats and having plans in place to address them swiftly.
Training and Development
Invest in the training and development of your procurement team.
Ensure they are aware of the latest procurement strategies and technologies.
A skilled team is more adept at managing processes efficiently, negotiating better, and troubleshooting any issues that may arise.
Encourage continued education in areas like supply chain management, negotiation tactics, and time management to enhance their effectiveness.
Conclusion
Shortening procurement lead times is a multifaceted challenge that involves improving internal processes, fostering strong supplier relationships, leveraging technology, and strategic planning.
By taking a holistic approach, purchasing departments can enhance their efficiency, reduce costs, and provide better service to their organizations.
Remember, each company’s procurement needs and processes are unique.
It’s essential to assess and tailor these strategies based on specific organizational requirements.
With careful planning and continuous improvement efforts, significant reductions in procurement lead times are achievable.
資料ダウンロード
QCD調達購買管理クラウド「newji」は、調達購買部門で必要なQCD管理全てを備えた、現場特化型兼クラウド型の今世紀最高の購買管理システムとなります。
ユーザー登録
調達購買業務の効率化だけでなく、システムを導入することで、コスト削減や製品・資材のステータス可視化のほか、属人化していた購買情報の共有化による内部不正防止や統制にも役立ちます。
NEWJI DX
製造業に特化したデジタルトランスフォーメーション(DX)の実現を目指す請負開発型のコンサルティングサービスです。AI、iPaaS、および先端の技術を駆使して、製造プロセスの効率化、業務効率化、チームワーク強化、コスト削減、品質向上を実現します。このサービスは、製造業の課題を深く理解し、それに対する最適なデジタルソリューションを提供することで、企業が持続的な成長とイノベーションを達成できるようサポートします。
オンライン講座
製造業、主に購買・調達部門にお勤めの方々に向けた情報を配信しております。
新任の方やベテランの方、管理職を対象とした幅広いコンテンツをご用意しております。
お問い合わせ
コストダウンが利益に直結する術だと理解していても、なかなか前に進めることができない状況。そんな時は、newjiのコストダウン自動化機能で大きく利益貢献しよう!
(Β版非公開)