- お役立ち記事
- Purchasing department solutions to eliminate bottlenecks in the procurement process
Purchasing department solutions to eliminate bottlenecks in the procurement process
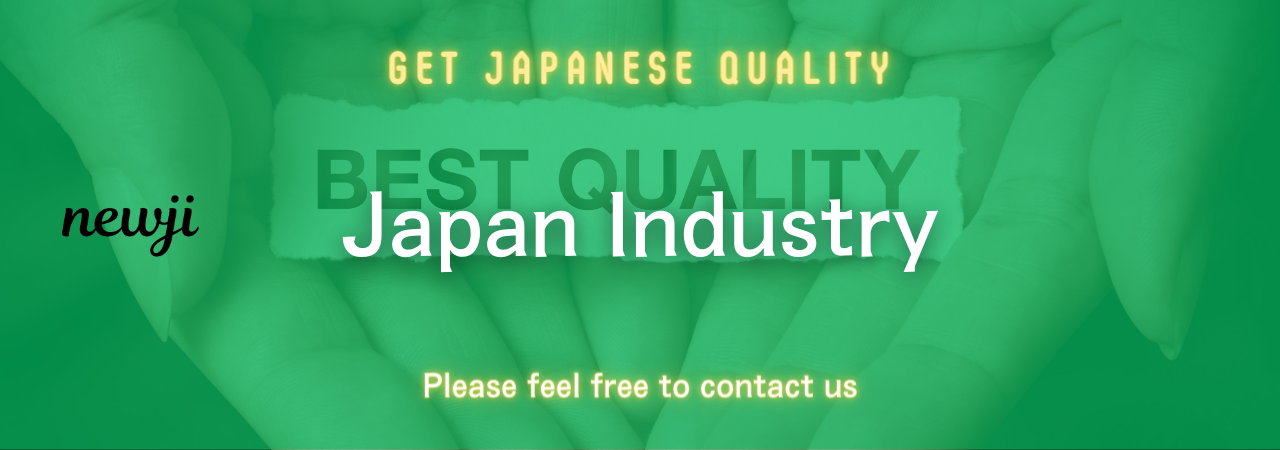
目次
Understanding Procurement Bottlenecks
Before diving into solutions, it’s crucial to understand what procurement bottlenecks are and how they impact the purchasing department.
A bottleneck in procurement occurs when there’s a hindrance or delay in the purchasing process, causing inefficiencies and potential losses for a company.
These bottlenecks can arise from a variety of sources, such as supplier issues, internal processes, or fluctuating market demands.
Identifying and addressing these obstacles is key to optimizing procurement operations and ensuring a smooth flow of goods and services.
Common Causes of Procurement Bottlenecks
Procurement bottlenecks can appear in different forms and are caused by various factors.
One major cause is limited supplier availability or capacity, which occurs when a supplier cannot meet the demand for products or services.
Internal factors, such as inadequate communication between departments or insufficient data management systems, can also cause significant delays.
Furthermore, inefficient manual processes can slow down procurement, as they often require excessive time and resources to complete tasks that could be automated.
Improving Supplier Relationships
A strong supplier relationship is vital in minimizing bottlenecks in the procurement process.
To enhance this relationship, companies should prioritize open and honest communication with their suppliers.
Regularly engaging in discussions about expectations, capacity, and potential challenges can help both parties prepare and adjust accordingly.
Additionally, diversifying the supplier base by working with multiple suppliers for the same product or service reduces the risk of relying too heavily on one supplier.
This not only enables flexibility during unforeseen circumstances but also fosters competitive pricing and higher quality.
Leveraging Technology for Procurement Efficiency
Incorporating technology into procurement processes is another effective way to eliminate bottlenecks.
Utilizing procurement software solutions can streamline operations by automating routine tasks like purchase order creation, invoice processing, and supplier management.
These software solutions often come with powerful data analytics tools that offer insights into procurement patterns and highlight areas for improvement.
Moreover, adopting cloud-based procurement systems enhances real-time collaboration, allowing team members and suppliers to access critical information on demand.
This connectivity ensures more accurate decision-making and faster response times, ultimately reducing delays.
Optimizing Internal Processes
Examining and refining internal processes is a key step in overcoming procurement bottlenecks.
Start by mapping out the entire procurement process to identify any stages that consistently experience delays.
Consider implementing a standardized approach by developing clear policies and procedures that guide each step of the procurement journey.
This helps to reduce ambiguity and ensures that employees understand their roles and responsibilities.
Additionally, regular training sessions can equip the purchasing team with the skills needed to navigate the procurement landscape effectively and efficiently.
Effective Demand Forecasting
Accurate demand forecasting is essential to preventing procurement bottlenecks caused by unexpected spikes in demand.
By analyzing historical data and market trends, companies can better anticipate future needs and adjust their procurement strategies accordingly.
Collaboration with sales and marketing teams also aids in understanding upcoming promotions or campaigns that may influence demand.
Investing in advanced forecasting tools can provide more precise predictions and allow businesses to plan their inventory and supplier engagements proactively.
This proactive approach minimizes the risk of stockouts and ensures the timely procurement of necessary goods and services.
Enhancing Communication and Collaboration
Internal communication breakdowns are a frequent contributor to procurement bottlenecks.
Ensuring seamless communication and collaboration within the purchasing department, as well as with other relevant departments such as finance and production, is crucial.
Implementing integrated communication platforms or project management tools can facilitate smoother interactions and information sharing.
Regular team meetings, both formal and informal, promote transparency and encourage the exchange of ideas, insights, and solutions.
Building a culture of collaboration empowers employees to work together towards the common goal of eliminating bottlenecks and achieving procurement efficiency.
Continuous Performance Monitoring
For ongoing success in managing procurement bottlenecks, continuous performance monitoring and improvement are crucial.
Establish relevant key performance indicators (KPIs) that align with the organization’s procurement goals and regularly assess the performance of both internal processes and supplier relationships.
Utilizing performance metrics helps identify areas of improvement and measure the effectiveness of implemented changes.
Moreover, seeking feedback from stakeholders, including suppliers, employees, and customers, can provide valuable insights and uncover potential issues that may not have been previously recognized.
With a commitment to continuous improvement, companies can stay agile and responsive to evolving market conditions and procurement challenges.
By understanding the causes of procurement bottlenecks and implementing these solutions, purchasing departments can enhance efficiency and maintain a competitive edge.
Prioritizing strong supplier relationships, leveraging technology, optimizing internal processes, and fostering a culture of communication and collaboration are key steps in eliminating bottlenecks.
As a result, businesses can enjoy a smoother procurement process, leading to timely deliveries, cost savings, and increased overall productivity.
資料ダウンロード
QCD調達購買管理クラウド「newji」は、調達購買部門で必要なQCD管理全てを備えた、現場特化型兼クラウド型の今世紀最高の購買管理システムとなります。
ユーザー登録
調達購買業務の効率化だけでなく、システムを導入することで、コスト削減や製品・資材のステータス可視化のほか、属人化していた購買情報の共有化による内部不正防止や統制にも役立ちます。
NEWJI DX
製造業に特化したデジタルトランスフォーメーション(DX)の実現を目指す請負開発型のコンサルティングサービスです。AI、iPaaS、および先端の技術を駆使して、製造プロセスの効率化、業務効率化、チームワーク強化、コスト削減、品質向上を実現します。このサービスは、製造業の課題を深く理解し、それに対する最適なデジタルソリューションを提供することで、企業が持続的な成長とイノベーションを達成できるようサポートします。
オンライン講座
製造業、主に購買・調達部門にお勤めの方々に向けた情報を配信しております。
新任の方やベテランの方、管理職を対象とした幅広いコンテンツをご用意しております。
お問い合わせ
コストダウンが利益に直結する術だと理解していても、なかなか前に進めることができない状況。そんな時は、newjiのコストダウン自動化機能で大きく利益貢献しよう!
(Β版非公開)