- お役立ち記事
- A new strategy to shorten lead times promoted by purchasing departments in manufacturing industries
A new strategy to shorten lead times promoted by purchasing departments in manufacturing industries
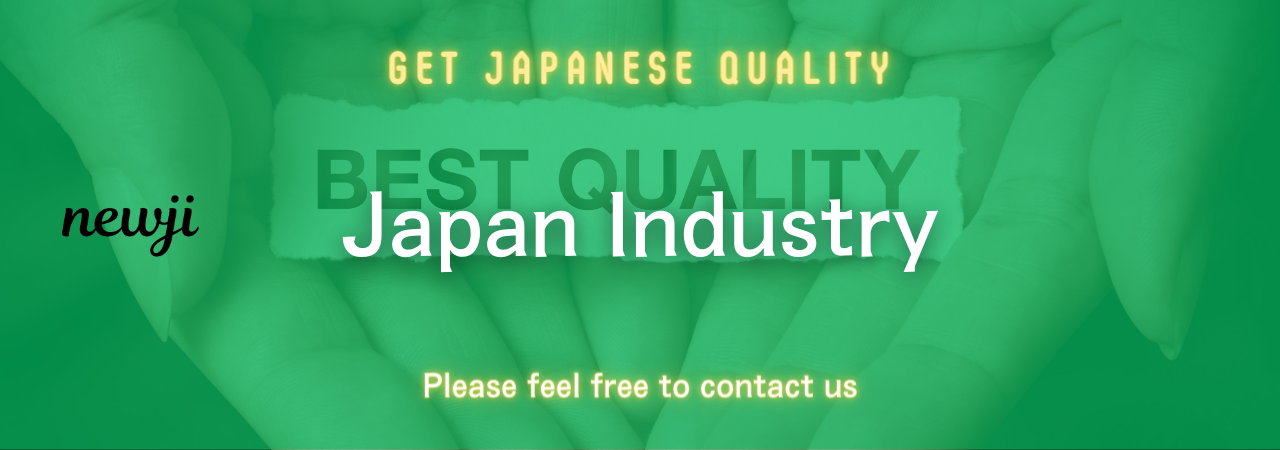
目次
Understanding Lead Times in Manufacturing
Lead time refers to the amount of time that elapses from the start of a particular process to its completion.
In the context of manufacturing, it includes sourcing raw materials, production, and delivery of the final product.
Reducing lead time is crucial as it enhances customer satisfaction, optimizes inventory levels, and improves overall efficiency.
The purchasing department plays a pivotal role in shortening these lead times as they are directly involved in sourcing and procurement.
The Role of the Purchasing Department
The purchasing department in manufacturing is responsible for procuring raw materials, components, and other goods essential for manufacturing processes.
Their role extends beyond mere procurement to encompass supplier management, negotiating contracts, and ensuring the timely delivery of materials.
By improving their strategies, purchasing departments can significantly reduce lead times, which in turn benefits the entire manufacturing operation.
Strategies for Reducing Lead Times
Supplier Relationships
Building strong, long-term relationships with suppliers is vital.
Such relationships often lead to better communication, favorable terms, and priority service.
By understanding the capacity and lead times of their suppliers, purchasing departments can plan more effectively.
Vendor Managed Inventory (VMI)
Implementing a Vendor Managed Inventory system can allow suppliers to monitor the buying company’s inventory.
VMI improves lead time by reducing the need for manual reordering and ensuring that the company always has necessary stock on hand.
This system relies on clear communication and technology to be effective.
Just-in-Time (JIT) Purchasing
Just-in-Time is an inventory strategy where materials are ordered and received as close as possible to when they are needed.
This reduces inventory costs and minimizes excess, which can drastically cut down lead times.
Success in JIT relies on efficient supply chain logistics and accurate demand forecasting.
Technology and Automation in Lead Time Reduction
The integration of modern technology into purchasing departments can significantly enhance their efficiency and effectiveness.
Automation tools streamline routine processes like purchase orders and invoice approvals, freeing staff to focus on strategic sourcing and supplier relationships.
Moreover, utilizing software solutions for demand forecasting can help in better managing lead times.
Data Analytics
Using data analytics, purchasing departments can better understand market trends, supplier performance, and internal processes.
This insight allows them to make informed decisions about inventory levels and reorder points, ultimately reducing lead times.
ERP Systems
Enterprise Resource Planning systems can automate various processes within the manufacturing supply chain.
By implementing a robust ERP system, manufacturers can synchronize production schedules and supply chain logistics, ensuring seamless operations.
Collaboration Across Departments
For purchasing departments to effectively reduce lead times, collaboration with other departments is crucial.
Operations, logistics, and sales teams must work in harmony to understand and meet customer demands.
Cross-departmental collaboration can lead to shared insights, better forecasting, and the ability to anticipate and resolve potential bottlenecks early.
Challenges and Solutions
Supply Chain Disruptions
Global supply chains are often vulnerable to disruptions from geopolitical tensions, natural disasters, or pandemics.
To mitigate these risks, it’s essential to diversify suppliers and establish contingency plans.
Flexible sourcing strategies, such as dual-sourcing, can also help alleviate dependencies on single suppliers.
Lead Time Variability
Lead time can vary due to several factors, including supplier delays and order quantities.
Implementing a robust lead time tracking mechanism can help purchasing departments monitor variability and adjust forecasts as needed.
Negotiating shorter lead times with key suppliers can also minimize variability.
The Future of Purchasing in Manufacturing
As manufacturing sectors evolve, the role of the purchasing department in reducing lead times will become increasingly significant.
New technologies such as AI, machine learning, and blockchain have the potential to revolutionize procurement processes.
These technologies enable greater transparency, efficiency, and responsiveness within supply chains.
Moreover, sustainability is likely to play a growing role in future purchasing strategies.
Sourcing materials responsibly and choosing environmentally conscious suppliers not only aligns with global sustainability goals but can also streamline operations by building a more resilient supply chain.
In conclusion, the purchasing department is central to reducing lead times in manufacturing industries.
By fostering strong supplier relationships, utilizing technology, and collaborating across departments, they can significantly enhance efficiency.
Embracing new strategies and technologies will help manufacturing businesses remain competitive and responsive to market demands.
資料ダウンロード
QCD調達購買管理クラウド「newji」は、調達購買部門で必要なQCD管理全てを備えた、現場特化型兼クラウド型の今世紀最高の購買管理システムとなります。
ユーザー登録
調達購買業務の効率化だけでなく、システムを導入することで、コスト削減や製品・資材のステータス可視化のほか、属人化していた購買情報の共有化による内部不正防止や統制にも役立ちます。
NEWJI DX
製造業に特化したデジタルトランスフォーメーション(DX)の実現を目指す請負開発型のコンサルティングサービスです。AI、iPaaS、および先端の技術を駆使して、製造プロセスの効率化、業務効率化、チームワーク強化、コスト削減、品質向上を実現します。このサービスは、製造業の課題を深く理解し、それに対する最適なデジタルソリューションを提供することで、企業が持続的な成長とイノベーションを達成できるようサポートします。
オンライン講座
製造業、主に購買・調達部門にお勤めの方々に向けた情報を配信しております。
新任の方やベテランの方、管理職を対象とした幅広いコンテンツをご用意しております。
お問い合わせ
コストダウンが利益に直結する術だと理解していても、なかなか前に進めることができない状況。そんな時は、newjiのコストダウン自動化機能で大きく利益貢献しよう!
(Β版非公開)