- お役立ち記事
- A multi-tier supplier management strategy for purchasing departments that increases manufacturing efficiency
A multi-tier supplier management strategy for purchasing departments that increases manufacturing efficiency
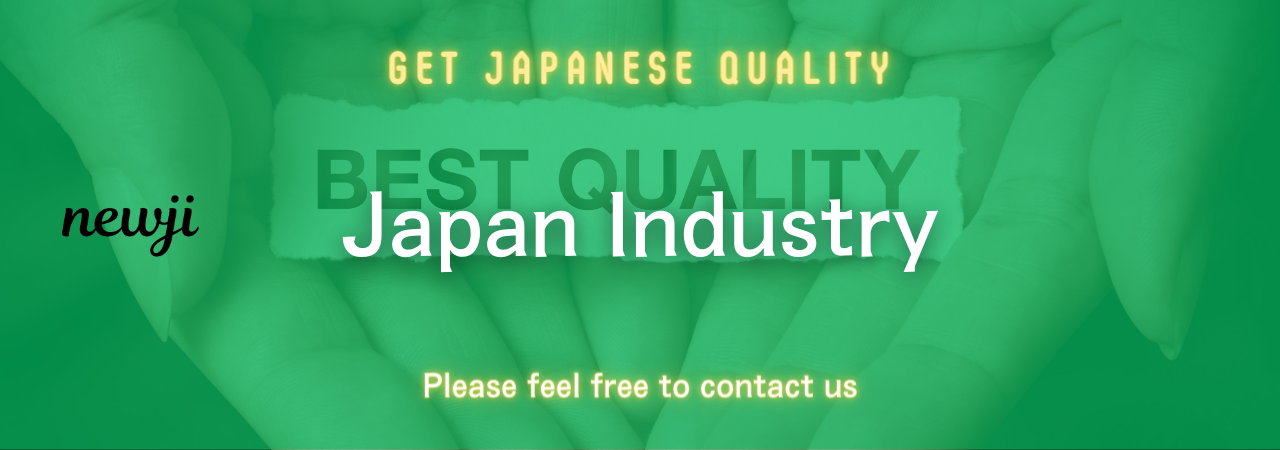
目次
Understanding Multi-Tier Supplier Management
In today’s complex manufacturing landscape, managing suppliers effectively has become more critical than ever.
A multi-tier supplier management strategy is a structured approach to overseeing interactions and relationships with suppliers at different levels.
This strategy goes beyond direct suppliers, reaching into the extended supply chain to optimize relationships with secondary and tertiary suppliers.
By incorporating this layered approach, purchasing departments can significantly enhance manufacturing efficiency.
A multi-tier strategy recognizes that each supplier tier plays a role in the final product’s quality, cost, and delivery.
Managing these tiers strategically helps in mitigating risks, optimizing costs, and improving overall agility in manufacturing.
It is a proactive approach that anticipates challenges and ensures better coordination across the supply chain.
The Importance of a Multi-Tier Supplier Strategy
Traditional supply chain management often focuses on direct suppliers, leaving secondary and tertiary suppliers without much oversight.
However, disruptions at any tier of the supply chain can affect the entire production line.
A multi-tier supplier management strategy addresses this by establishing a comprehensive view of the entire supply chain.
Integrating a multi-tier approach aids in detecting potential issues early in the supply chain.
For example, if a tertiary supplier faces a shortage of raw materials, this information can be communicated up the chain to allow for contingency planning.
This enhances the purchasing department’s ability to respond swiftly to changes, maintaining manufacturing efficiency regardless of disruptions.
Enhancing Collaboration and Transparency
Multi-tier supplier management fosters stronger collaboration and transparency among all parties involved.
By prioritizing communication across all supply chain levels, purchasing departments can build more resilient relationships.
Stakeholders can share information openly, which facilitates better coordination and alignment with production goals.
Transparency is critical for trust-building, ensuring each tier of the supply chain is adequately informed.
When suppliers understand their role in the broader context of manufacturing, they can adjust priorities and resources to meet collective objectives.
This holistic view of the supply chain creates a harmonious working environment conducive to efficiency and innovation.
Strategies for Effective Multi-Tier Supplier Management
Implementing a multi-tier supplier management strategy involves several key steps, each aimed at optimizing relationships and improving manufacturing outcomes.
Conducting a Comprehensive Supply Chain Analysis
The first step is to thoroughly map out the supply chain.
This involves identifying all suppliers at every tier and understanding their roles and relationships.
With this comprehensive analysis, purchasing departments can recognize critical paths and potential bottlenecks.
It also provides insight into dependency networks, helping to allocate resources more effectively.
Assessing Supplier Performance and Risks
Regularly assessing the performance of all suppliers is integral to maintaining efficiency.
Metrics such as delivery times, quality consistency, and pricing competitiveness should be evaluated.
Risk assessments should also be conducted to identify vulnerabilities within the supply chain.
By understanding performance metrics and risk factors, purchasing departments can prioritize suppliers that align with organizational goals.
Implementing Technology Solutions
Leveraging technology is a game-changer for multi-tier supplier management.
Supply chain management software can provide real-time data visibility, allowing for instant communication across all tiers.
Technological tools help in automating routine tasks, streamlining communication, and enhancing data accuracy.
By embracing digital solutions, purchasing departments can make data-driven decisions leading to improved efficiency.
The Benefits of a Multi-Tier Supplier Management Strategy
This approach to supplier management offers numerous advantages that contribute to increased manufacturing efficiency.
Improved Product Quality
With all tiers of suppliers working cohesively, the quality of materials used in production can be consistently monitored and improved.
This collaborative effort helps in reducing defects and enhancing the final product quality, meeting or exceeding customer expectations.
Cost Optimization
By having visibility into the entire supply chain, purchasing departments can identify cost-saving opportunities.
Competitive supplier pricing, optimal resource allocation, and minimizing waste contribute to a leaner, more cost-effective manufacturing process.
Increased Agility
A multi-tier strategy facilitates rapid responses to changes in the market or production demands.
This agility is essential in today’s fast-paced environment, where customer expectations and market conditions constantly evolve.
Purchasing departments can quickly adapt to fluctuations, ensuring a steady production flow.
Conclusion
A multi-tier supplier management strategy is essential for purchasing departments aiming to enhance manufacturing efficiency.
By understanding the intricacies of the supply chain and fostering collaboration amongst all suppliers, organizations can achieve greater resilience, cost savings, and product quality improvements.
This strategic approach empowers purchasing departments to mitigate risks effectively, respond to market changes swiftly, and maintain competitiveness in the manufacturing sector.
As businesses continue to evolve, a well-executed multi-tier supplier management strategy remains a pivotal factor in achieving operational excellence.
資料ダウンロード
QCD調達購買管理クラウド「newji」は、調達購買部門で必要なQCD管理全てを備えた、現場特化型兼クラウド型の今世紀最高の購買管理システムとなります。
ユーザー登録
調達購買業務の効率化だけでなく、システムを導入することで、コスト削減や製品・資材のステータス可視化のほか、属人化していた購買情報の共有化による内部不正防止や統制にも役立ちます。
NEWJI DX
製造業に特化したデジタルトランスフォーメーション(DX)の実現を目指す請負開発型のコンサルティングサービスです。AI、iPaaS、および先端の技術を駆使して、製造プロセスの効率化、業務効率化、チームワーク強化、コスト削減、品質向上を実現します。このサービスは、製造業の課題を深く理解し、それに対する最適なデジタルソリューションを提供することで、企業が持続的な成長とイノベーションを達成できるようサポートします。
オンライン講座
製造業、主に購買・調達部門にお勤めの方々に向けた情報を配信しております。
新任の方やベテランの方、管理職を対象とした幅広いコンテンツをご用意しております。
お問い合わせ
コストダウンが利益に直結する術だと理解していても、なかなか前に進めることができない状況。そんな時は、newjiのコストダウン自動化機能で大きく利益貢献しよう!
(Β版非公開)