- お役立ち記事
- How to optimize the supplier selection process for manufacturing purchasing departments
How to optimize the supplier selection process for manufacturing purchasing departments
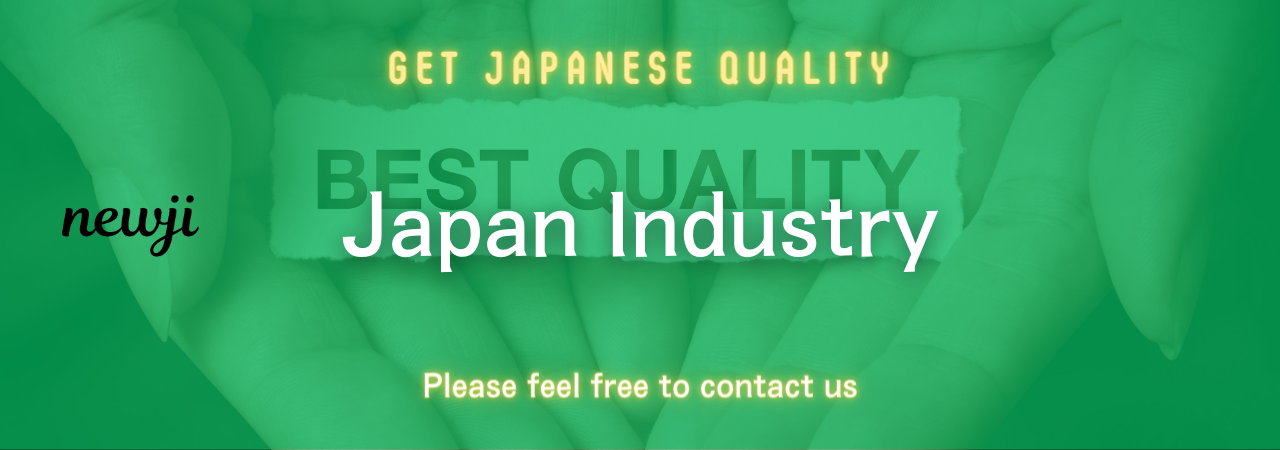
目次
Understanding the Supplier Selection Process
In manufacturing purchasing departments, selecting the right suppliers is crucial for ensuring quality and efficiency in production.
The supplier selection process involves identifying and evaluating potential suppliers and making decisions based on various factors like cost, quality, reliability, and service.
A well-optimized supplier selection process can help a manufacturing department reduce costs, improve product quality, and maintain smooth operations.
The Importance of Supplier Selection
Choosing the right supplier affects the overall performance of a manufacturing company.
A dependable supplier delivers high-quality materials consistently and on time, which leads to uninterrupted production schedules.
Proper supplier selection protects a company from unnecessary costs and losses due to poor quality products, delayed deliveries, or unmet contractual commitments.
Steps to Optimize the Supplier Selection Process
Manufacturers can optimize their supplier selection process by following several key steps.
1. Define Your Requirements
The first step in optimizing the supplier selection process involves clearly defining what your company needs.
This includes understanding the materials, products, and services required for production.
Create a comprehensive list of specifications, quality standards, and delivery expectations.
This helps in identifying suppliers who can meet these requirements efficiently.
2. Conduct Market Research
Once the requirements are defined, research potential suppliers in the market.
Look for suppliers with a good reputation and track record in the industry.
Utilize online resources, industry publications, and trade shows to compile a list of prospective suppliers.
Additionally, networking with industry professionals can provide valuable insights and recommendations.
3. Evaluate Supplier Capabilities
After identifying potential suppliers, the next step is to evaluate their capabilities.
Assess factors such as financial stability, production capacity, technology, quality management systems, and customer service.
Check if the supplier has the flexibility to adjust to changes in demand or specifications.
Reach out for references and reviews from existing or past clients to gain an insight into the supplier’s reliability.
4. Consider Total Cost of Ownership
Focusing solely on the price of materials can lead to overlooking other cost factors.
Evaluate the total cost of ownership (TCO), which includes additional costs such as logistics, storage, and potential risk costs associated with a supplier.
A supplier offering lower prices may incur higher costs in other areas like transportation or quality issues, impacting overall savings.
5. Prioritize Quality and Reliability
Quality and reliability should be top priorities during the supplier selection process.
Ensure that suppliers adhere to industry standards and quality certifications.
Request samples or trial runs to test product quality.
A reliable supplier should have consistent quality assurance processes and a strong commitment to maintaining high standards.
6. Analyze Communication and Support
Effective communication and robust support from a supplier can prevent misunderstandings and delays.
Assess how responsive and supportive a supplier is during the negotiation and evaluation phase.
A supplier who communicates transparently and provides excellent customer service will likely provide a more cooperative and productive partnership.
7. Develop a Long-Term Partnership
Creating and nurturing long-term relationships with suppliers can lead to mutually beneficial outcomes.
A strong partnership allows for better negotiation on prices, priority on service, and collaboration in product development.
Commitment and trust ensure that both parties strive to meet business goals consistently.
Tools and Techniques for Supplier Optimization
There are several tools and techniques available to optimize the supplier selection process.
Supplier Scorecard
A supplier scorecard is a useful tool for evaluating and comparing suppliers using defined criteria.
It includes critical performance indicators such as delivery times, quality standards, cost efficiencies, and service levels.
Using a scorecard makes it easier to quantify performance metrics and select suppliers who meet or exceed expectations.
Supplier Audits
Conducting regular supplier audits helps ensure compliance with contractual obligations and quality standards.
Audits provide an opportunity to verify a supplier’s capabilities and identify areas for improvement, ultimately leading to enhanced supplier performance.
Data and Analytics
Utilizing data and analytics enables better decision-making by providing insights into supplier performance trends and risk factors.
Manufacturing departments can use data-driven approaches to anticipate issues, manage risk, and refine supplier selection strategies.
Collaborative Planning
Engage in collaborative planning with suppliers to ensure a transparent and aligned relationship.
This includes shared forecasting, inventory management, and joint development projects.
Collaboration results in optimized production schedules and reduced risk of supply chain disruptions.
Conclusion
Optimizing the supplier selection process is essential for manufacturing purchasing departments striving for operational excellence.
By defining clear requirements, evaluating capabilities, and considering the total cost of ownership, departments can make informed decisions.
Investing in long-term partnerships and using tools like supplier scorecards and data analytics contribute to a successful supply chain.
By following these practices, manufacturing companies can ensure reliability, quality, efficiency, and a competitive edge in the industry.
資料ダウンロード
QCD調達購買管理クラウド「newji」は、調達購買部門で必要なQCD管理全てを備えた、現場特化型兼クラウド型の今世紀最高の購買管理システムとなります。
ユーザー登録
調達購買業務の効率化だけでなく、システムを導入することで、コスト削減や製品・資材のステータス可視化のほか、属人化していた購買情報の共有化による内部不正防止や統制にも役立ちます。
NEWJI DX
製造業に特化したデジタルトランスフォーメーション(DX)の実現を目指す請負開発型のコンサルティングサービスです。AI、iPaaS、および先端の技術を駆使して、製造プロセスの効率化、業務効率化、チームワーク強化、コスト削減、品質向上を実現します。このサービスは、製造業の課題を深く理解し、それに対する最適なデジタルソリューションを提供することで、企業が持続的な成長とイノベーションを達成できるようサポートします。
オンライン講座
製造業、主に購買・調達部門にお勤めの方々に向けた情報を配信しております。
新任の方やベテランの方、管理職を対象とした幅広いコンテンツをご用意しております。
お問い合わせ
コストダウンが利益に直結する術だと理解していても、なかなか前に進めることができない状況。そんな時は、newjiのコストダウン自動化機能で大きく利益貢献しよう!
(Β版非公開)