- お役立ち記事
- What tools can help purchasing departments manage supply chain disruption risks?
What tools can help purchasing departments manage supply chain disruption risks?
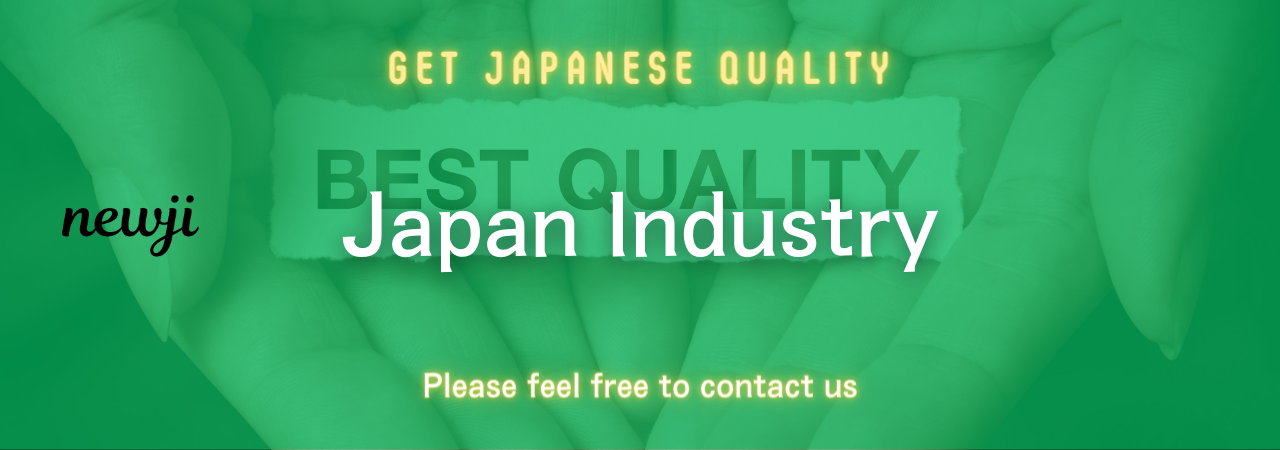
目次
Understanding Supply Chain Disruption Risks
Supply chain disruption risks have become a significant concern for purchasing departments worldwide.
These risks can stem from various factors, such as natural disasters, political instability, pandemics, or even cyber-attacks.
Any disruption can lead to delays, increased costs, and unhappy customers.
Therefore, managing these risks effectively is crucial to ensuring smooth operations and maintaining a competitive edge.
The Importance of Risk Management in Supply Chains
Risk management in supply chains involves identifying potential risks, evaluating their impact, and implementing strategies to mitigate them.
The goal is to minimize disruptions and ensure that the supply chain can continue to operate effectively, even when unexpected events occur.
Effective risk management can lead to better decision-making, improved supplier relationships, and increased resilience, ultimately protecting a company’s bottom line.
Identifying Potential Risks
The first step in managing supply chain disruption risks is to identify potential vulnerabilities within the supply chain.
This involves analyzing every aspect of the supply chain, from raw material sourcing to final product delivery.
Purchasing departments should consider factors such as supplier reliability, geopolitical issues, environmental factors, and technology dependencies.
Evaluating Risk Impact
Once potential risks are identified, it is essential to evaluate their impact on the supply chain.
This involves assessing the likelihood of each risk occurring and the potential consequences if it does.
Prioritizing risks based on their potential impact allows purchasing departments to focus their efforts and resources on the most critical areas.
Tools for Managing Supply Chain Disruption Risks
There are several tools and technologies available that can help purchasing departments manage supply chain disruption risks effectively.
These tools can provide valuable insights, streamline processes, and help mitigate potential threats.
Supply Chain Risk Management Software
Supply chain risk management software is specifically designed to identify, assess, and mitigate risks within the supply chain.
This software often includes features such as risk mapping, scenario analysis, and real-time monitoring.
By using this software, purchasing departments can gain a comprehensive view of their supply chain and proactively address potential disruptions.
Supplier Relationship Management Tools
Maintaining strong relationships with suppliers is crucial for managing supply chain risks.
Supplier relationship management tools can help purchasing departments monitor supplier performance, identify potential issues, and ensure compliance with contractual agreements.
These tools often include features such as supplier scorecards, communication portals, and performance tracking, which can help strengthen supplier relationships and improve collaboration.
Data Analytics and Predictive Analytics
Data analytics and predictive analytics tools can provide valuable insights into potential risks and disruptions within the supply chain.
By analyzing historical data and trends, these tools can help purchasing departments identify patterns and predict potential disruptions before they occur.
This proactive approach allows companies to implement mitigation strategies and avoid costly delays.
Inventory Management Systems
Effective inventory management is crucial for mitigating supply chain disruption risks.
Inventory management systems can help purchasing departments optimize inventory levels, reduce excess stock, and improve demand forecasting.
By maintaining optimal inventory levels, companies can ensure they have the necessary resources to continue operations, even if a disruption occurs.
Blockchain Technology
Blockchain technology offers several benefits for managing supply chain risks, such as increased transparency, traceability, and security.
By using blockchain, purchasing departments can ensure that all parties in the supply chain have access to accurate and up-to-date information.
This can help prevent fraud, reduce errors, and improve overall supply chain reliability.
Best Practices for Managing Supply Chain Disruption Risks
In addition to using the right tools and technologies, there are several best practices that purchasing departments can follow to manage supply chain disruption risks effectively.
Diversify Suppliers
Relying on a single supplier can increase the risk of disruptions.
It is essential to diversify suppliers and have backups ready to step in if necessary.
This approach can help ensure continuity and minimize the impact of disruptions.
Build Strong Relationships with Suppliers
Strong relationships with suppliers can lead to better communication, collaboration, and problem-solving.
Maintaining open lines of communication with suppliers can help address potential issues before they escalate and ensure a more resilient supply chain.
Continuously Monitor and Review Risks
Supply chain risks are constantly evolving, and it is crucial to continuously monitor and review them.
Regular risk assessments can help identify new risks and emerging threats, allowing purchasing departments to adjust their strategies accordingly.
Develop a Contingency Plan
A comprehensive contingency plan is essential for managing supply chain disruptions.
This plan should outline steps to take in case of a disruption, including communication protocols, resource allocation, and recovery strategies.
Having a well-defined plan in place can help companies respond quickly and effectively to unexpected events.
Conclusion
Managing supply chain disruption risks is a critical function of purchasing departments.
By understanding potential risks, using the right tools, and implementing best practices, companies can mitigate disruptions and ensure a resilient supply chain.
This proactive approach not only protects against financial losses but also enhances customer satisfaction and strengthens competitive advantage.
資料ダウンロード
QCD調達購買管理クラウド「newji」は、調達購買部門で必要なQCD管理全てを備えた、現場特化型兼クラウド型の今世紀最高の購買管理システムとなります。
ユーザー登録
調達購買業務の効率化だけでなく、システムを導入することで、コスト削減や製品・資材のステータス可視化のほか、属人化していた購買情報の共有化による内部不正防止や統制にも役立ちます。
NEWJI DX
製造業に特化したデジタルトランスフォーメーション(DX)の実現を目指す請負開発型のコンサルティングサービスです。AI、iPaaS、および先端の技術を駆使して、製造プロセスの効率化、業務効率化、チームワーク強化、コスト削減、品質向上を実現します。このサービスは、製造業の課題を深く理解し、それに対する最適なデジタルソリューションを提供することで、企業が持続的な成長とイノベーションを達成できるようサポートします。
オンライン講座
製造業、主に購買・調達部門にお勤めの方々に向けた情報を配信しております。
新任の方やベテランの方、管理職を対象とした幅広いコンテンツをご用意しております。
お問い合わせ
コストダウンが利益に直結する術だと理解していても、なかなか前に進めることができない状況。そんな時は、newjiのコストダウン自動化機能で大きく利益貢献しよう!
(Β版非公開)