- お役立ち記事
- Revolutionizing Japanese Manufacturing: The Rise of Multi-Joint Robots in Industry 4.0
Revolutionizing Japanese Manufacturing: The Rise of Multi-Joint Robots in Industry 4.0
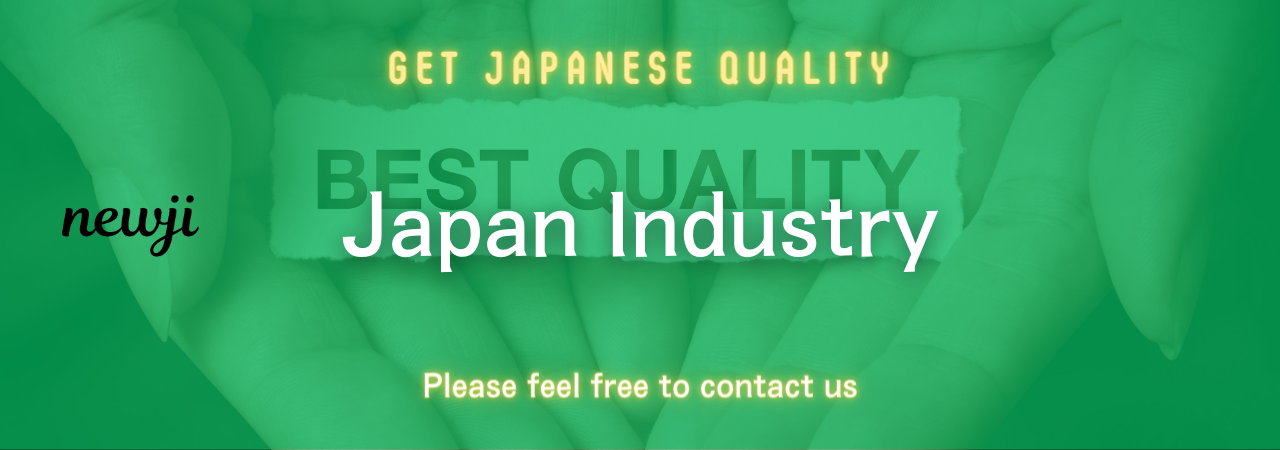
目次
Introduction to Industry 4.0 and Japanese Manufacturing
Industry 4.0 represents the fourth industrial revolution, characterized by the integration of digital technologies into manufacturing processes. This transformation emphasizes automation, data exchange, and advanced manufacturing techniques, creating “smart factories.” Japanese manufacturing, renowned for its precision and efficiency, is at the forefront of adopting Industry 4.0 technologies. Among these innovations, multi-joint robots have emerged as pivotal components in revolutionizing production lines, enhancing flexibility, and improving overall productivity.
The Evolution of Robotics in Japanese Manufacturing
Japanese manufacturing has a long history of embracing robotics to enhance production capabilities. From the early adoption of industrial robots in the automotive sector to the integration of advanced robotic systems in electronics and machinery, Japan has consistently led the way in robotic innovation. The shift towards multi-joint robots marks a significant advancement, enabling more complex and versatile operations within manufacturing environments.
Historical Milestones in Japanese Robotics
Japan’s journey with robotics began in the 1960s with the introduction of the Unimate robot in automotive assembly lines. Over the decades, companies like Fanuc, Yaskawa, and Kawasaki have been instrumental in developing state-of-the-art robotic solutions. The evolution from single-axis robots to multi-joint configurations has allowed for greater flexibility, precision, and integration into various manufacturing processes.
Benefits of Multi-Joint Robots
Multi-joint robots, also known as articulated robots, feature multiple rotary joints, allowing for a wide range of motion similar to the human arm. This design enables them to perform complex tasks with high precision. The benefits include:
– Enhanced flexibility in handling diverse tasks.
– Improved precision and repeatability.
– Ability to operate in limited spaces.
– Increased payload capacity and reach.
– Seamless integration with existing manufacturing systems.
Procurement and Purchasing of Multi-Joint Robots
Acquiring multi-joint robots involves strategic procurement and purchasing processes to ensure that manufacturing companies obtain the best technology at competitive prices. Japanese suppliers are highly regarded for their quality and innovation, making them preferred partners in this sector.
Advantages of Procuring from Japanese Suppliers
Japanese suppliers offer several advantages that make them attractive to international buyers:
– High-quality manufacturing standards.
– Cutting-edge technology and continuous innovation.
– Strong after-sales support and maintenance services.
– Customization capabilities to meet specific manufacturing needs.
– Reliable supply chains and timely delivery.
Challenges in Procuring Japanese Robotics
Despite the advantages, there are challenges associated with procuring multi-joint robots from Japanese suppliers:
– Higher initial investment costs.
– Language barriers and cultural differences.
– Navigating complex technical specifications.
– Potential longer lead times compared to local suppliers.
– Import regulations and tariffs.
Supplier Negotiation Techniques
Effective negotiation with Japanese suppliers is crucial to securing favorable terms and ensuring long-term partnerships. Understanding Japanese business etiquette and negotiation styles can significantly impact the outcomes.
Understanding Japanese Business Culture
Japanese business culture emphasizes respect, patience, and building long-term relationships. Key aspects include:
– Formal introductions and business card exchanges.
– Emphasis on consensus-building and group harmony.
– Indirect communication to maintain respect and avoid conflict.
– Punctuality and preparedness in meetings.
Negotiation Strategies
Implementing the following strategies can enhance negotiation outcomes:
– **Preparation:** Conduct thorough research on the supplier, their products, and market conditions.
– **Building Relationships:** Invest time in establishing trust and rapport before discussing business terms.
– **Clear Communication:** Ensure clarity in requirements and expectations to avoid misunderstandings.
– **Flexibility:** Be open to compromises and alternatives proposed by the supplier.
– **Long-Term Perspective:** Focus on creating mutually beneficial agreements that foster ongoing partnerships.
Key Negotiation Points
Critical areas to address during negotiations include:
– Pricing and payment terms.
– Delivery schedules and lead times.
– Warranty and maintenance services.
– Customization options and technical support.
– Terms for future upgrades and scalability.
Market Conditions for Multi-Joint Robots
The market for multi-joint robots in Japan is influenced by various factors, including technological advancements, industry demand, and global economic conditions. Understanding these dynamics is essential for effective procurement and strategic planning.
Technological Trends
Continuous advancements in robotics technology drive the market forward. Key trends include:
– Integration of artificial intelligence and machine learning for smarter operations.
– Development of collaborative robots (cobots) that work alongside humans.
– Enhanced sensor technologies for better precision and adaptability.
– Increased use of IoT for real-time monitoring and data analysis.
Industry Demand
Industries such as automotive, electronics, and semiconductor manufacturing are primary drivers of demand for multi-joint robots. The need for increased efficiency, higher production volumes, and improved product quality propels the adoption of advanced robotic systems.
Economic Factors
Economic conditions, including exchange rates, trade policies, and global supply chain dynamics, impact the market. Fluctuations in these factors can influence the cost and availability of multi-joint robots, affecting procurement decisions.
Best Practices in Procuring Multi-Joint Robots
Adhering to best practices ensures successful procurement of multi-joint robots, optimizing both cost and performance.
Comprehensive Needs Assessment
Begin by conducting a thorough analysis of your manufacturing processes to identify specific needs and objectives. Determine the tasks the robots will perform, required capabilities, and integration points within the existing infrastructure.
Supplier Evaluation and Selection
Evaluate potential suppliers based on:
– Technical expertise and product offerings.
– Reputation and track record in the industry.
– Quality certifications and compliance standards.
– Customer testimonials and case studies.
– Financial stability and support services.
Cost-Benefit Analysis
Perform a detailed cost-benefit analysis to assess the return on investment. Consider factors such as initial costs, operational savings, productivity gains, and potential for future scalability.
Customization and Integration
Ensure that the selected robots can be customized to meet your specific requirements. Effective integration with your existing systems and workflows is critical for maximizing efficiency and minimizing disruptions.
Training and Support
Invest in comprehensive training programs for your staff to operate and maintain the robots effectively. Reliable support services from the supplier can address technical issues promptly, ensuring minimal downtime.
Advantages of Multi-Joint Robots in Japanese Manufacturing
Integrating multi-joint robots into Japanese manufacturing systems offers numerous advantages that contribute to enhanced productivity and competitiveness.
Increased Flexibility
Multi-joint robots can perform a wide range of tasks, from assembly and welding to packaging and quality inspection. Their versatility allows manufacturers to adapt to changing production needs without significant reconfiguration of the production line.
Enhanced Precision and Quality
The high precision of multi-joint robots ensures consistent quality in manufacturing processes. This precision reduces defects, minimizes waste, and enhances the overall quality of the final products.
Improved Efficiency and Productivity
Robots can operate continuously without fatigue, leading to increased production rates and shorter cycle times. Automation of repetitive tasks allows human workers to focus on more complex and value-added activities, boosting overall productivity.
Cost Savings
Although the initial investment in multi-joint robots can be substantial, the long-term cost savings from reduced labor costs, minimized errors, and decreased material waste make them economically viable. Additionally, robots can operate in environments that may be hazardous for human workers, enhancing workplace safety.
Scalability and Future-Proofing
Multi-joint robots offer scalability, allowing manufacturers to expand their operations easily as demand grows. Their adaptability to new technologies ensures that manufacturing systems remain up-to-date with industry advancements.
Disadvantages and Challenges
While multi-joint robots offer significant benefits, there are also challenges and disadvantages to consider.
High Initial Investment
The cost of acquiring and implementing multi-joint robots can be substantial. This includes expenses related to purchasing the robots, integrating them into existing systems, and training staff.
Technical Complexity
The advanced technology of multi-joint robots requires a certain level of technical expertise for operation and maintenance. Manufacturers may need to invest in specialized training and ongoing technical support.
Potential Job Displacement
Automation of tasks traditionally performed by humans can lead to concerns about job displacement. It is essential to manage this transition thoughtfully, focusing on retraining and upskilling employees for new roles.
Maintenance and Downtime
Robots require regular maintenance to operate efficiently. Any downtime due to technical issues can disrupt production schedules and impact overall productivity.
Integration Challenges
Integrating multi-joint robots with existing manufacturing systems can be complex. Ensuring seamless communication and coordination between robots and other equipment is crucial for optimal performance.
Case Studies: Successful Implementation in Japanese Manufacturing
Examining real-world examples of successful multi-joint robot implementations in Japanese manufacturing can provide valuable insights into best practices and achievable outcomes.
Automotive Assembly Lines
Japanese automotive manufacturers have extensively adopted multi-joint robots for assembly tasks. These robots perform precise welding, painting, and component assembly, enhancing the speed and quality of vehicle production. The integration of robots has led to significant reductions in production time and improvements in product consistency.
Electronics Manufacturing
In the electronics sector, multi-joint robots are used for tasks such as circuit board assembly, component placement, and quality inspection. Their high precision and adaptability enable the manufacture of complex electronic devices with minimal defects, meeting stringent industry standards.
Semiconductor Fabrication
Semiconductor manufacturers utilize multi-joint robots for handling delicate materials and automating intricate fabrication processes. The robots’ ability to operate in cleanroom environments and perform precise movements ensures high yields and consistent product quality.
Future Prospects of Multi-Joint Robots in Japanese Industry
The future of multi-joint robots in Japanese manufacturing is promising, driven by ongoing technological advancements and evolving industry needs.
Advancements in Artificial Intelligence
Integration of AI and machine learning will enable multi-joint robots to perform more complex and adaptive tasks. AI-powered robots can learn from data, optimize performance, and make real-time decisions, further enhancing their efficiency and versatility.
Collaborative Robots (Cobots)
The development of cobots, which work alongside human workers, will expand the applications of multi-joint robots. Cobots can handle repetitive or physically demanding tasks, complementing human capabilities and improving overall workplace productivity.
Enhanced Human-Robot Interaction
Improved interfaces and communication protocols will facilitate better interaction between humans and robots. This will enable more intuitive control, easier programming, and more effective collaboration on the production floor.
Sustainability and Energy Efficiency
Future multi-joint robots will incorporate energy-efficient technologies and sustainable materials, aligning with global sustainability goals. This will reduce the environmental impact of manufacturing operations and contribute to greener production practices.
Conclusion
The rise of multi-joint robots is revolutionizing Japanese manufacturing, ushering in an era of increased automation, precision, and efficiency. As Industry 4.0 continues to evolve, the strategic procurement and integration of advanced robotic systems will be crucial for maintaining competitiveness and driving innovation. While challenges such as high initial costs and technical complexities exist, the long-term benefits of enhanced productivity, quality, and scalability make multi-joint robots a valuable investment for the future of manufacturing in Japan and beyond.
資料ダウンロード
QCD調達購買管理クラウド「newji」は、調達購買部門で必要なQCD管理全てを備えた、現場特化型兼クラウド型の今世紀最高の購買管理システムとなります。
ユーザー登録
調達購買業務の効率化だけでなく、システムを導入することで、コスト削減や製品・資材のステータス可視化のほか、属人化していた購買情報の共有化による内部不正防止や統制にも役立ちます。
NEWJI DX
製造業に特化したデジタルトランスフォーメーション(DX)の実現を目指す請負開発型のコンサルティングサービスです。AI、iPaaS、および先端の技術を駆使して、製造プロセスの効率化、業務効率化、チームワーク強化、コスト削減、品質向上を実現します。このサービスは、製造業の課題を深く理解し、それに対する最適なデジタルソリューションを提供することで、企業が持続的な成長とイノベーションを達成できるようサポートします。
オンライン講座
製造業、主に購買・調達部門にお勤めの方々に向けた情報を配信しております。
新任の方やベテランの方、管理職を対象とした幅広いコンテンツをご用意しております。
お問い合わせ
コストダウンが利益に直結する術だと理解していても、なかなか前に進めることができない状況。そんな時は、newjiのコストダウン自動化機能で大きく利益貢献しよう!
(Β版非公開)