- お役立ち記事
- Unlocking the Future of Automation: How Japan’s Force Sensors are Revolutionizing Global Manufacturing
Unlocking the Future of Automation: How Japan’s Force Sensors are Revolutionizing Global Manufacturing
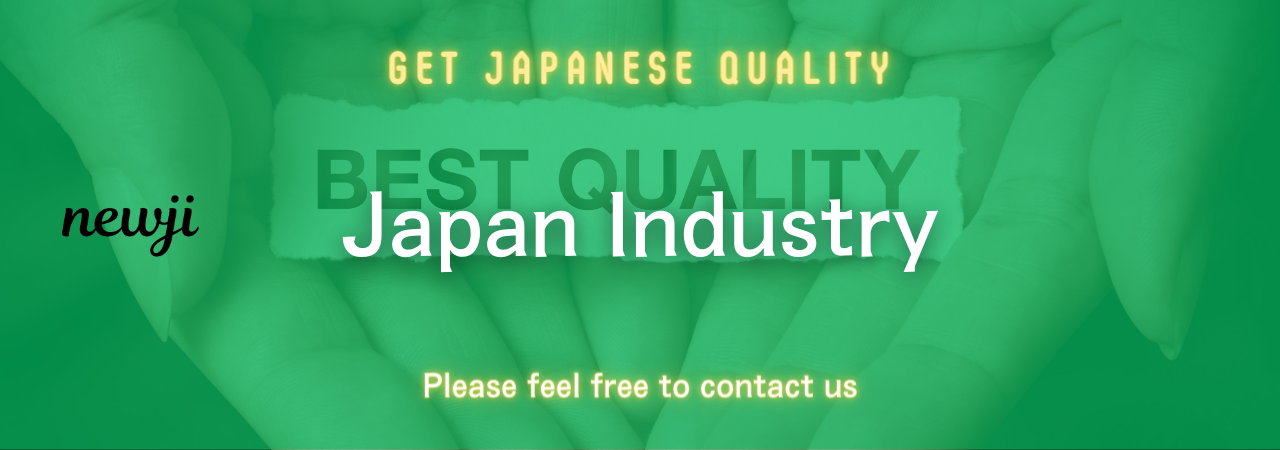
目次
Introduction to Japan’s Force Sensors in Automation
In the rapidly evolving landscape of global manufacturing, automation stands as a pivotal force driving efficiency and innovation. At the heart of this transformation are advanced technologies like force sensors, which play a crucial role in enhancing precision and reliability in production processes. Japan, renowned for its engineering excellence, has been at the forefront of developing cutting-edge force sensors. These devices are revolutionizing manufacturing across the globe by providing unparalleled accuracy and integration capabilities.
The Role of Force Sensors in Modern Manufacturing
Force sensors are integral components in automated systems, enabling machines to measure and respond to physical forces with high precision. They are essential in applications such as assembly lines, robotics, and quality control. By accurately detecting forces, these sensors ensure that products are manufactured to exact specifications, reducing errors and waste.
Enhancing Precision and Quality
Japanese force sensors are designed to deliver exceptional accuracy, which is critical in industries where precision is paramount. For instance, in automotive manufacturing, force sensors ensure that components are assembled with the exact amount of pressure, preventing defects and enhancing the overall quality of the vehicles. This level of precision not only improves product quality but also extends the lifespan of machinery by minimizing wear and tear.
Integration with Advanced Automation Systems
The seamless integration of force sensors with advanced automation systems is a hallmark of Japanese engineering. These sensors are compatible with various control systems and can be easily integrated into existing manufacturing setups. This flexibility allows manufacturers to upgrade their automation capabilities without overhauling their entire production lines, saving both time and resources.
Advantages of Partnering with Japanese Suppliers
Collaborating with Japanese suppliers offers numerous advantages for global manufacturers seeking to incorporate advanced force sensors into their operations.
Unmatched Quality and Reliability
Japanese suppliers are renowned for their commitment to quality and reliability. Their force sensors undergo rigorous testing and adhere to strict quality standards, ensuring consistent performance even in demanding environments. This reliability minimizes downtime and maintenance costs, providing a significant return on investment for manufacturers.
Innovative Technology and Continuous Improvement
Japan’s dedication to technological innovation drives the continuous improvement of force sensors. Suppliers invest heavily in research and development, resulting in sensors that incorporate the latest advancements in materials, electronics, and software. This forward-thinking approach ensures that manufacturers have access to state-of-the-art technologies that keep them competitive in the global market.
Strong After-Sales Support and Service
Japanese suppliers excel in providing comprehensive after-sales support and service. From installation and training to maintenance and troubleshooting, they offer extensive assistance to ensure that manufacturers can fully leverage the capabilities of their force sensors. This support is crucial for optimizing sensor performance and addressing any issues that may arise during operation.
Challenges and Considerations in Partnering with Japanese Suppliers
While partnering with Japanese suppliers offers significant benefits, there are also challenges that manufacturers must navigate.
Cultural and Communication Differences
Cultural and communication differences can pose challenges in establishing and maintaining partnerships with Japanese suppliers. Understanding and respecting Japanese business etiquette, such as formality and the importance of building trust, is essential for successful collaborations. Clear and consistent communication is also necessary to ensure that both parties have a mutual understanding of expectations and requirements.
Higher Initial Costs
Japanese force sensors may come with higher initial costs compared to alternatives from other regions. However, this investment is often justified by the superior quality, reliability, and long-term performance of the sensors. Manufacturers must weigh the upfront costs against the potential savings from reduced downtime, lower maintenance expenses, and enhanced product quality.
Lead Times and Supply Chain Considerations
Importing force sensors from Japan may involve longer lead times and complex supply chain logistics. Manufacturers need to plan their procurement processes carefully to account for shipping times, customs procedures, and potential delays. Building strong relationships with Japanese suppliers can help mitigate these challenges by ensuring priority in production and shipping schedules.
Supplier Negotiation Techniques
Effective negotiation with Japanese suppliers is crucial for securing favorable terms and fostering long-term partnerships.
Building Trust and Long-Term Relationships
Japanese business culture places a high value on trust and long-term relationships. Demonstrating commitment and reliability can enhance negotiation outcomes. Engaging in regular communication, honoring agreements, and showing respect for Japanese business practices can help build a strong foundation for successful negotiations.
Understanding Supplier Priorities
To negotiate effectively, it is important to understand the priorities and constraints of Japanese suppliers. Factors such as production capacity, lead times, and quality standards should be considered. By aligning your requests with the supplier’s capabilities and demonstrating how a partnership can be mutually beneficial, you can achieve more favorable negotiation results.
Leveraging Volume and Long-Term Contracts
Offering larger order volumes or committing to long-term contracts can provide leverage in negotiations. Japanese suppliers are often willing to offer discounts or better terms in exchange for guaranteed business over an extended period. Highlighting your company’s growth potential and long-term needs can strengthen your negotiating position.
Market Conditions and Trends
Understanding the current market conditions and trends in force sensor technology is essential for making informed procurement decisions.
Increasing Demand for Automation
The global push towards automation in manufacturing is driving the demand for advanced force sensors. Industries such as automotive, electronics, and medical devices are increasingly adopting automated processes to enhance efficiency and reduce costs. This trend presents opportunities for suppliers who can provide high-quality sensors that meet the evolving needs of manufacturers.
Advancements in Sensor Technology
Technological advancements are continuously enhancing the capabilities of force sensors. Innovations in materials, miniaturization, and smart sensor integration are enabling more accurate and versatile sensors. Staying abreast of these developments can help manufacturers select sensors that offer the best performance and future-proof their automation systems.
Sustainability and Environmental Considerations
Sustainability is becoming a key consideration in manufacturing. Suppliers that prioritize environmentally friendly practices and sustainable production methods are gaining a competitive edge. Japanese companies are increasingly incorporating eco-friendly technologies and materials into their force sensors, aligning with global sustainability goals and appealing to environmentally conscious manufacturers.
Best Practices in Procurement and Purchasing
Adopting best practices in procurement and purchasing can enhance the effectiveness of partnerships with Japanese force sensor suppliers.
Comprehensive Supplier Evaluation
Conducting a thorough evaluation of potential suppliers is essential. Assess factors such as financial stability, production capabilities, quality certifications, and customer references. A comprehensive evaluation ensures that you partner with suppliers who can consistently meet your quality and delivery requirements.
Clear Specification and Requirement Definition
Clearly defining your specifications and requirements helps prevent misunderstandings and ensures that suppliers can deliver products that meet your needs. Provide detailed information on the performance, durability, and integration aspects of the force sensors you require. Clear communication of expectations facilitates smoother procurement processes and reduces the risk of costly errors.
Establishing Strong Communication Channels
Maintaining open and effective communication with suppliers is crucial for successful partnerships. Utilize various communication channels such as regular meetings, reports, and digital collaboration tools to stay informed about order statuses, product updates, and potential issues. Strong communication fosters transparency and enables proactive problem-solving.
Implementing Quality Control Measures
Establishing robust quality control measures ensures that the force sensors received from suppliers meet your standards. Implementing inspection protocols, conducting regular audits, and collaborating with suppliers on quality improvement initiatives can enhance product reliability and performance.
Case Studies: Success Stories in Utilizing Japanese Force Sensors
Examining real-world examples of manufacturers successfully integrating Japanese force sensors can provide valuable insights and inspiration.
Automotive Industry: Enhancing Assembly Precision
A leading automotive manufacturer partnered with a Japanese force sensor supplier to upgrade their assembly line automation. By integrating high-precision force sensors, the manufacturer achieved greater accuracy in component assembly, resulting in a significant reduction in defects and an improvement in overall vehicle quality. The collaboration also enabled real-time monitoring and data analysis, allowing for continuous process optimization.
Electronics Manufacturing: Streamlining Quality Control
An electronics manufacturer implemented Japanese force sensors in their quality control processes to ensure the reliability of delicate components. The sensors provided precise measurements of applied forces during testing, helping to identify potential weaknesses and prevent defects before products reached the market. This initiative not only enhanced product quality but also reduced warranty claims and customer returns.
Medical Devices: Improving Product Safety and Compliance
A medical device company utilized Japanese force sensors to enhance the safety and compliance of their products. The sensors enabled accurate force measurements in the production of surgical instruments, ensuring that each device met stringent regulatory standards. This collaboration helped the company achieve higher compliance rates, reduce production errors, and gain a competitive advantage in the medical device market.
Future Outlook: The Evolution of Force Sensors in Manufacturing
The future of force sensors in manufacturing looks promising, with ongoing advancements and expanding applications.
Integration with Artificial Intelligence and Machine Learning
The integration of force sensors with artificial intelligence (AI) and machine learning (ML) technologies is set to revolutionize manufacturing. AI-driven data analysis can provide deeper insights into production processes, enabling predictive maintenance, real-time optimization, and enhanced decision-making. Machine learning algorithms can leverage force sensor data to identify patterns and anomalies, further improving process efficiency and product quality.
Development of Smart and Connected Sensors
The evolution of smart and connected sensors will enhance the functionality and interoperability of force sensors in automated systems. These sensors will be capable of self-diagnosis, wireless communication, and seamless integration with Internet of Things (IoT) platforms. This connectivity will facilitate more responsive and adaptive manufacturing systems, leading to greater flexibility and scalability.
Advancements in Miniaturization and Energy Efficiency
Advancements in miniaturization and energy efficiency will make force sensors more versatile and cost-effective. Smaller sensors can be integrated into compact and intricate production setups, expanding their applicability across various industries. Improvements in energy efficiency will reduce operational costs and support sustainable manufacturing practices.
Conclusion
Japan’s force sensors are playing a transformative role in the future of global manufacturing. Their unparalleled precision, reliability, and integration capabilities make them invaluable assets in automated production systems. By partnering with Japanese suppliers, manufacturers can leverage advanced technologies to enhance quality, efficiency, and competitiveness. Despite challenges such as cultural differences and higher initial costs, the long-term benefits of collaborating with Japanese force sensor suppliers are substantial. As technology continues to advance, these sensors will become even more integral to the evolving landscape of automation, driving innovation and excellence in manufacturing worldwide.
資料ダウンロード
QCD調達購買管理クラウド「newji」は、調達購買部門で必要なQCD管理全てを備えた、現場特化型兼クラウド型の今世紀最高の購買管理システムとなります。
ユーザー登録
調達購買業務の効率化だけでなく、システムを導入することで、コスト削減や製品・資材のステータス可視化のほか、属人化していた購買情報の共有化による内部不正防止や統制にも役立ちます。
NEWJI DX
製造業に特化したデジタルトランスフォーメーション(DX)の実現を目指す請負開発型のコンサルティングサービスです。AI、iPaaS、および先端の技術を駆使して、製造プロセスの効率化、業務効率化、チームワーク強化、コスト削減、品質向上を実現します。このサービスは、製造業の課題を深く理解し、それに対する最適なデジタルソリューションを提供することで、企業が持続的な成長とイノベーションを達成できるようサポートします。
オンライン講座
製造業、主に購買・調達部門にお勤めの方々に向けた情報を配信しております。
新任の方やベテランの方、管理職を対象とした幅広いコンテンツをご用意しております。
お問い合わせ
コストダウンが利益に直結する術だと理解していても、なかなか前に進めることができない状況。そんな時は、newjiのコストダウン自動化機能で大きく利益貢献しよう!
(Β版非公開)