- お役立ち記事
- How to strengthen cooperation in multi-site supply chains in the manufacturing industry, which is a focus for purchasing departments
How to strengthen cooperation in multi-site supply chains in the manufacturing industry, which is a focus for purchasing departments
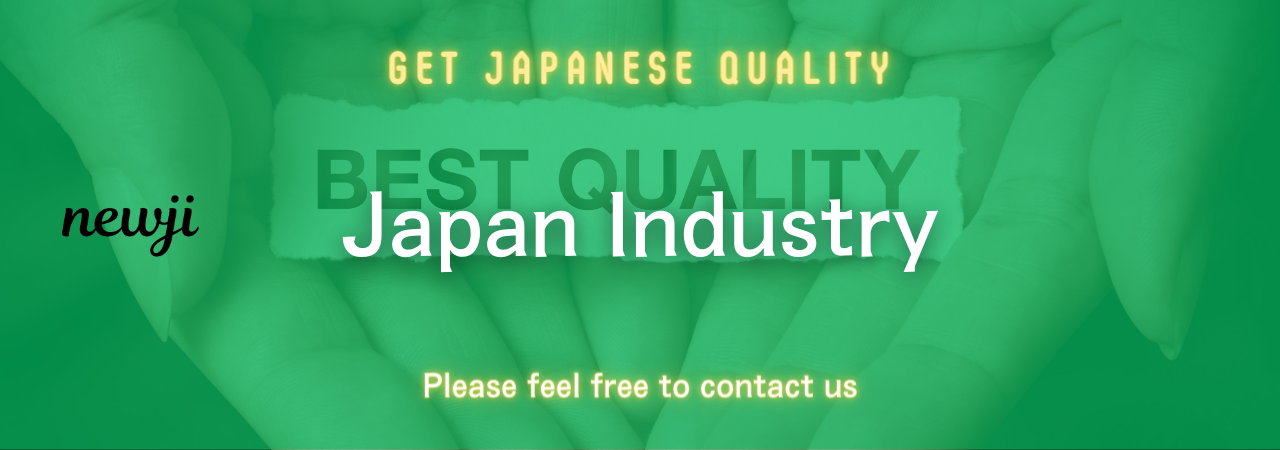
目次
Understanding Multi-Site Supply Chains
Manufacturing industries today often operate with complex multi-site supply chains.
These involve multiple facilities, sometimes spread across different regions or countries, working in sync to produce and deliver products.
The coordination between these various sites requires careful planning and management.
It is crucial that companies understand the intricacies of these supply chains to improve efficiency and collaboration.
The Role of Purchasing Departments
The purchasing department in any manufacturing setup plays a pivotal role in ensuring smooth operations within the supply chain.
They are responsible for sourcing materials, negotiating with suppliers, and ensuring timely delivery of goods.
In multi-site scenarios, the challenges multiply as they need to coordinate with suppliers for each location.
Effective purchasing strategies can significantly impact the overall performance of the supply chain.
Challenges in Multi-Site Collaboration
Managing multi-site supply chains poses several challenges that need addressing to enhance cooperation.
Complex Logistics
When dealing with multiple locations, logistics become increasingly complex.
Coordinating shipments and deliveries among various factories, warehouses, and distribution centers requires meticulous planning.
Any errors or delays can disrupt the supply chain and lead to increased costs and diminished productivity.
Communication Barriers
Another significant challenge is communication.
Different sites might operate in different time zones, speak different languages, or use distinct systems for tracking orders and inventory.
Ensuring that all teams stay on the same page and have access to the same information is crucial for smooth operations.
Supplier Management
Multi-site supply chains often involve dealing with numerous suppliers.
Purchasing departments need to develop robust relationships with suppliers to ensure that they can deliver the required materials on time and at the right quality.
Balancing between local and global suppliers can also be challenging, as it involves managing different lead times and cost structures.
Strategies for Strengthening Cooperation
To enhance collaboration within multi-site supply chains, companies can adopt several strategies.
Implementing Advanced Technology
Technological advancements can dramatically improve cooperation among sites.
Investing in integrated supply chain management software enables real-time visibility across the supply chain.
These systems can help synchronize operations, making it easier to track inventory, orders, and shipments across multiple locations.
Moreover, technologies such as artificial intelligence and machine learning can be leveraged for predictive analytics, helping anticipate and mitigate potential disruptions.
Standardizing Processes
Standardizing processes across different sites can lead to more streamlined operations.
By having uniform procedures for inventory management, order processing, and quality checks, companies can reduce inconsistencies and improve efficiency.
Standardization also facilitates easier training and onboarding of employees at different locations, which can enhance productivity and cooperation.
Enhancing Communication
Communication is key to successful multi-site operations.
Implementing effective communication tools like collaborative platforms and instant messaging systems can bridge gaps between different locations.
Regularly scheduled meetings and updates can ensure that all teams are aligned with the company’s objectives and strategies.
Additionally, fostering a culture of transparency within the organization encourages teams to share insights and best practices across sites.
Developing Strong Supplier Relationships
Building and maintaining strong relationships with suppliers is essential for a well-functioning supply chain.
Companies should consider implementing supplier relationship management programs that focus on communication, performance evaluation, and long-term collaboration.
These programs can help identify reliable suppliers and foster partnerships that benefit both parties.
Conclusion
Enhancing cooperation in multi-site supply chains in the manufacturing industry is a critical priority for purchasing departments.
By understanding the challenges and implementing strategic solutions, companies can improve efficiency and productivity.
Leveraging technology, standardizing processes, enhancing communication, and fostering strong supplier relationships are key strategies for success.
With these efforts, manufacturing companies can ensure a robust and resilient supply chain capable of meeting the demands of the modern market.
資料ダウンロード
QCD調達購買管理クラウド「newji」は、調達購買部門で必要なQCD管理全てを備えた、現場特化型兼クラウド型の今世紀最高の購買管理システムとなります。
ユーザー登録
調達購買業務の効率化だけでなく、システムを導入することで、コスト削減や製品・資材のステータス可視化のほか、属人化していた購買情報の共有化による内部不正防止や統制にも役立ちます。
NEWJI DX
製造業に特化したデジタルトランスフォーメーション(DX)の実現を目指す請負開発型のコンサルティングサービスです。AI、iPaaS、および先端の技術を駆使して、製造プロセスの効率化、業務効率化、チームワーク強化、コスト削減、品質向上を実現します。このサービスは、製造業の課題を深く理解し、それに対する最適なデジタルソリューションを提供することで、企業が持続的な成長とイノベーションを達成できるようサポートします。
オンライン講座
製造業、主に購買・調達部門にお勤めの方々に向けた情報を配信しております。
新任の方やベテランの方、管理職を対象とした幅広いコンテンツをご用意しております。
お問い合わせ
コストダウンが利益に直結する術だと理解していても、なかなか前に進めることができない状況。そんな時は、newjiのコストダウン自動化機能で大きく利益貢献しよう!
(Β版非公開)