- お役立ち記事
- Key points to review the procurement process led by the purchasing department in the manufacturing industry
Key points to review the procurement process led by the purchasing department in the manufacturing industry
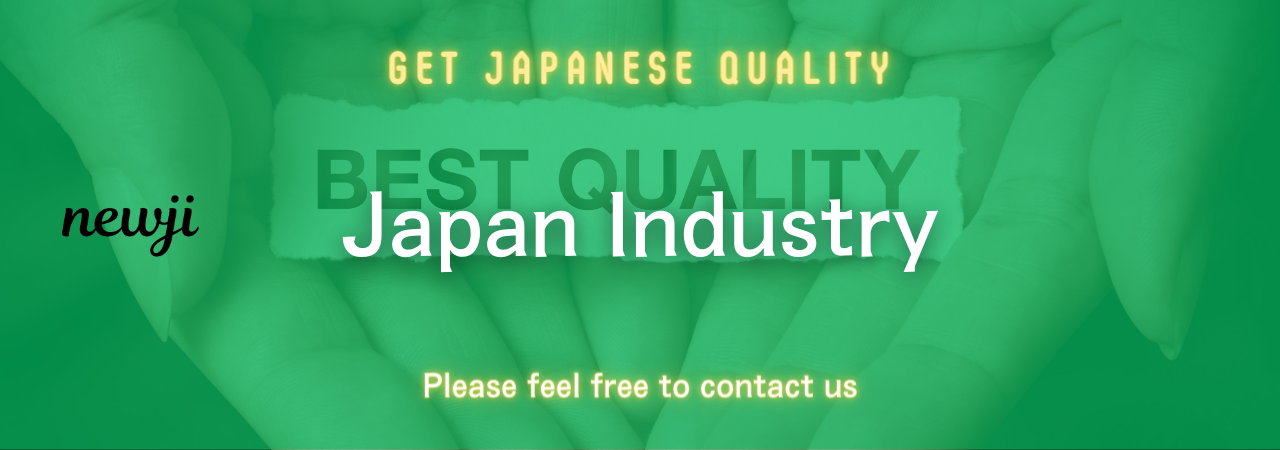
目次
Understanding the Procurement Process
In the manufacturing industry, the procurement process is a crucial component that directly impacts the efficiency and profitability of a company.
This process is typically led by the purchasing department, which is responsible for sourcing, negotiating, and acquiring goods and services that meet the needs of the organization.
A well-structured procurement process ensures that manufacturing operations receive the materials they require in a timely manner, at an acceptable quality, and at the most favorable cost.
Key Objectives of Procurement
The primary objectives of procurement are to ensure the availability of materials, achieve cost savings, maintain quality, and mitigate risks.
By achieving these objectives, the purchasing department supports the manufacturing process by ensuring that production is not interrupted due to lack of materials or defective supplies.
Furthermore, effective procurement can substantially reduce costs, contributing to the overall profitability of the company.
Steps in the Procurement Process
The procurement process generally consists of several key steps, which are crucial for the purchasing department to execute in a systematic manner:
1. Requirement Identification
The first step in the procurement process is identifying what goods or services are needed.
This involves determining the quantity and specification of the materials required for manufacturing.
Effective communication between departments is necessary to ensure that the purchasing department is aware of the needs of the production team.
2. Supplier Research and Selection
Once the requirements are identified, the next step is to research and select potential suppliers.
The purchasing department must evaluate suppliers based on their ability to deliver quality materials on time, their reliability, and their pricing.
It’s essential to consider whether suppliers can comply with any specific requirements, such as sustainable sourcing practices.
3. Request for Proposal (RFP) and Tender Evaluation
The purchasing department prepares a Request for Proposal (RFP) and invites selected suppliers to submit bids.
The RFP clearly outlines the company’s requirements, deadlines, and evaluation criteria.
Once the proposals are received, they are evaluated against these criteria to determine the best possible supplier.
4. Negotiation and Contracting
Negotiating with suppliers is a critical step in ensuring favorable terms and conditions for the company.
The purchasing department must be skilled in negotiation tactics, aiming to secure the best prices, delivery schedules, and payment terms.
Once these have been agreed upon, a formal contract is drafted and signed to solidify the arrangement.
5. Ordering and Expediting
After the contract is in place, orders are placed with the selected supplier.
The purchasing department must monitor the progress of these orders, ensuring that the supplier adheres to the agreed-upon timelines.
Expediting involves proactive tracking and communication to prevent any delays in delivery.
6. Receiving and Quality Assurance
The receipt of goods or services is followed by a quality check to ensure that they meet the specified standards.
The purchasing department works closely with the quality assurance team to inspect the materials or services for defects or non-conformance.
Any issues discovered at this stage must be promptly addressed with the supplier.
7. Payment and Record Keeping
Once materials are received and verified, the purchasing department processes the payment in accordance with the contract terms.
This step includes verifying invoices, ensuring that they match the purchase order and goods received.
Maintaining accurate records of all transactions is essential for financial reporting and audit purposes.
Challenges in the Procurement Process
Despite its structured nature, the procurement process can encounter various challenges, particularly in the manufacturing industry.
Common challenges include fluctuating material prices, supply chain disruptions, quality issues, and the need for sustainable practices.
The purchasing department must remain agile and responsive to overcome these obstacles, implementing strategies such as diversifying the supplier base or securing long-term contracts.
Improving the Procurement Process
Continuous improvement in the procurement process is vital for maintaining competitive advantage.
Here are some strategies to enhance procurement efficiency:
1. Leveraging Technology
Utilizing procurement software and digital platforms can streamline operations and improve accuracy.
These tools offer capabilities such as automated purchase orders, supplier management, and real-time tracking, allowing the purchasing department to operate more efficiently.
2. Fostering Supplier Relationships
Developing strong relationships with suppliers can lead to better negotiations, enhanced collaboration, and more reliable supply chains.
Regular communication and performance reviews help build trust and ensure alignment with business goals.
3. Implementing Sustainability Practices
Sustainable procurement practices not only protect the environment but also reduce risks and enhance brand reputation.
Consider supplier sustainability credentials when making procurement decisions to align with industry and consumer expectations.
Conclusion
Reviewing and refining the procurement process in the manufacturing industry is critical for ensuring seamless production and maximizing profitability.
By understanding the key steps, overcoming challenges, and embracing continuous improvement, the purchasing department can build a procurement strategy that supports the success of the entire organization.
資料ダウンロード
QCD調達購買管理クラウド「newji」は、調達購買部門で必要なQCD管理全てを備えた、現場特化型兼クラウド型の今世紀最高の購買管理システムとなります。
ユーザー登録
調達購買業務の効率化だけでなく、システムを導入することで、コスト削減や製品・資材のステータス可視化のほか、属人化していた購買情報の共有化による内部不正防止や統制にも役立ちます。
NEWJI DX
製造業に特化したデジタルトランスフォーメーション(DX)の実現を目指す請負開発型のコンサルティングサービスです。AI、iPaaS、および先端の技術を駆使して、製造プロセスの効率化、業務効率化、チームワーク強化、コスト削減、品質向上を実現します。このサービスは、製造業の課題を深く理解し、それに対する最適なデジタルソリューションを提供することで、企業が持続的な成長とイノベーションを達成できるようサポートします。
オンライン講座
製造業、主に購買・調達部門にお勤めの方々に向けた情報を配信しております。
新任の方やベテランの方、管理職を対象とした幅広いコンテンツをご用意しております。
お問い合わせ
コストダウンが利益に直結する術だと理解していても、なかなか前に進めることができない状況。そんな時は、newjiのコストダウン自動化機能で大きく利益貢献しよう!
(Β版非公開)