- お役立ち記事
- Practical methods for strengthening coordination between procurement and production in the manufacturing industry for the purchasing department
Practical methods for strengthening coordination between procurement and production in the manufacturing industry for the purchasing department
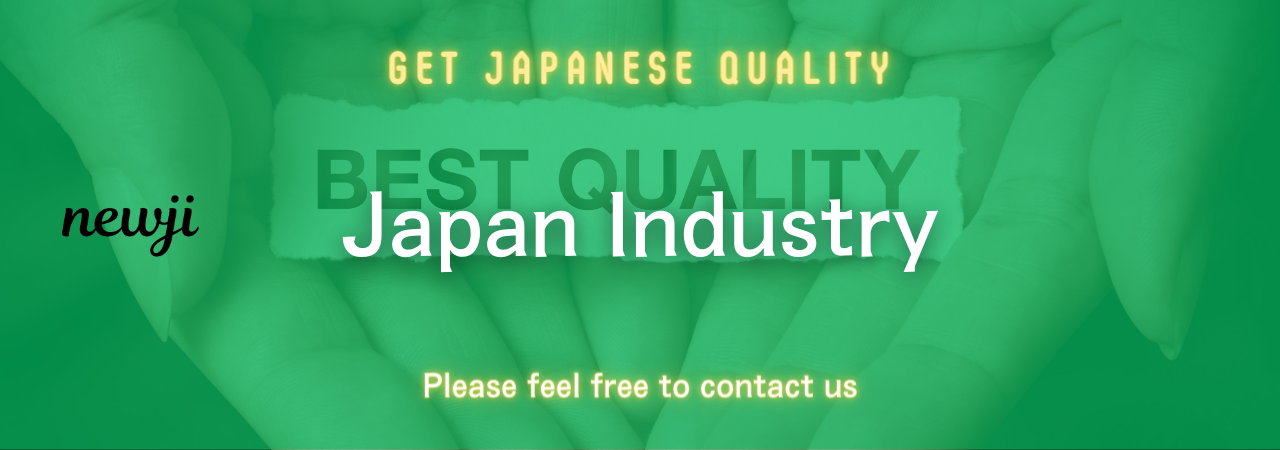
目次
Understanding the Importance of Coordination
Coordination between procurement and production is crucial in the manufacturing industry.
Effective collaboration ensures that resources are used optimally, costs are minimized, and production runs smoothly without interruptions.
In the fast-paced world of manufacturing, timing is everything.
A small delay or miscommunication can ripple through the production line, causing delays and financial losses.
The purchasing department plays a significant role in ensuring that procurement activities are aligned with production needs.
By understanding the demand from production, procurement can source materials efficiently and maintain an uninterrupted workflow.
Challenges in Procurement and Production Coordination
Despite its importance, coordination between procurement and production can be challenging.
Misalignments often occur due to poor communication, lack of information, and misunderstanding of each department’s needs.
In many cases, procurement teams may focus on minimizing costs and securing the best deals.
This can sometimes lead to purchasing decisions that do not align perfectly with the immediate production needs or quality standards required.
On the other hand, the production team might have tight schedules and specific requirements that, if not clearly communicated, can lead to procurement inconsistencies or bottlenecks.
Impact of Poor Coordination
Poor coordination can result in overstocking or stockouts, both of which are undesirable situations.
Overstocking ties up capital in inventory, while stockouts halt production, affecting delivery timelines and customer satisfaction.
Additionally, last-minute urgent orders to address stockouts often result in higher costs and reduced bargaining power.
Practical Strategies for Stronger Coordination
To improve coordination between procurement and production, it’s essential to implement practical strategies that encourage information sharing, communication, and strategic planning.
1. Implement Integrated Systems
One of the first steps toward improving coordination is implementing integrated systems that provide transparency and easy access to real-time data.
Using a robust ERP (Enterprise Resource Planning) system can centralize information, allowing procurement and production teams to monitor supply levels, track orders, and align their activities efficiently.
Integrated systems reduce the risk of miscommunication and ensure both teams have a comprehensive view of the current situation.
2. Regular Cross-Department Meetings
Facilitate regular cross-department meetings to discuss upcoming production schedules and procurement needs.
These meetings can serve as a platform for both teams to share their plans, align priorities, and discuss any potential challenges.
Regular communication fosters a culture of collaboration and ensures that both procurement and production teams are working towards shared goals.
3. Demand Forecasting and Planning
Demand forecasting is a critical tool for both procurement and production.
By predicting future demand accurately, procurement can source materials in alignment with production schedules, reducing unexpected orders and emergency purchases.
Invest in advanced analytics tools that leverage historical data and market trends to forecast demand with greater accuracy.
This allows the purchasing department to plan ahead, negotiate better contracts, and align their procurement strategies with production needs.
4. Establishing Clear Communication Channels
Establishing clear communication channels is essential for ensuring timely and accurate information flow between departments.
Consider using collaborative tools that facilitate instant messaging, document sharing, and task management.
Clear communication helps teams stay updated with the latest developments and swiftly address any issues, preventing them from escalating.
5. Aligning Key Performance Indicators (KPIs)
Aligning KPIs for both procurement and production departments can drive collaboration.
Rather than working in silos with separate goals, align KPIs that reflect shared objectives such as reducing lead times, minimizing inventory costs, and improving quality standards.
Shared KPIs encourage both departments to work together to achieve common goals, ultimately benefiting the entire organization.
Building Long-Term Supplier Relationships
Strong, long-term relationships with suppliers can significantly enhance coordination between procurement and production.
Suppliers who understand your production needs are more likely to provide consistent quality, flexible terms, and timely deliveries.
1. Collaborative Supplier Management
Engage in collaborative supplier management by involving key suppliers in your planning process.
When suppliers are aware of your production schedules and forecasts, they can better prepare to meet your demands.
Collaborative relationships foster trust and open lines of communication, allowing for more flexible and responsive procurement.
2. Supplier Performance Reviews
Conduct regular performance reviews with your suppliers to ensure they meet your standards and expectations.
These reviews provide an opportunity to address any issues, negotiate better terms, and strengthen the relationship through continuous improvement.
Strong partnerships with suppliers contribute to smoother operations and reduce the risk of supply chain disruptions.
Conclusion
Strengthening coordination between procurement and production in the manufacturing industry is pivotal for maintaining efficiency and competitiveness.
By implementing practical strategies, investing in technology, and fostering a culture of communication and collaboration, companies can overcome the challenges of misalignment.
A well-coordinated approach ensures that resources are used efficiently, production schedules are met, and customer demands are satisfied.
In a dynamic manufacturing environment, successful coordination can make the difference between thriving and merely surviving.
資料ダウンロード
QCD調達購買管理クラウド「newji」は、調達購買部門で必要なQCD管理全てを備えた、現場特化型兼クラウド型の今世紀最高の購買管理システムとなります。
ユーザー登録
調達購買業務の効率化だけでなく、システムを導入することで、コスト削減や製品・資材のステータス可視化のほか、属人化していた購買情報の共有化による内部不正防止や統制にも役立ちます。
NEWJI DX
製造業に特化したデジタルトランスフォーメーション(DX)の実現を目指す請負開発型のコンサルティングサービスです。AI、iPaaS、および先端の技術を駆使して、製造プロセスの効率化、業務効率化、チームワーク強化、コスト削減、品質向上を実現します。このサービスは、製造業の課題を深く理解し、それに対する最適なデジタルソリューションを提供することで、企業が持続的な成長とイノベーションを達成できるようサポートします。
オンライン講座
製造業、主に購買・調達部門にお勤めの方々に向けた情報を配信しております。
新任の方やベテランの方、管理職を対象とした幅広いコンテンツをご用意しております。
お問い合わせ
コストダウンが利益に直結する術だと理解していても、なかなか前に進めることができない状況。そんな時は、newjiのコストダウン自動化機能で大きく利益貢献しよう!
(Β版非公開)