- お役立ち記事
- How to balance cost reduction and quality maintenance for manufacturing purchasing departments
How to balance cost reduction and quality maintenance for manufacturing purchasing departments
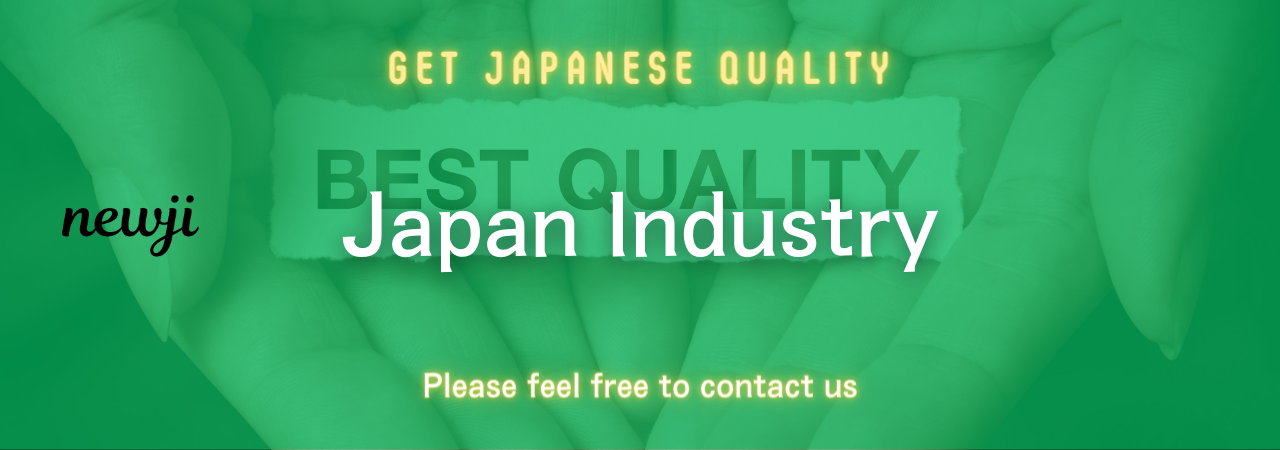
目次
Understanding the Challenge
Manufacturing purchasing departments face a constant challenge: how to balance cost reduction with maintaining product quality.
This balancing act is crucial for sustaining profitability while ensuring customer satisfaction.
The difficulty lies in reducing costs without compromising the standards of the products being delivered.
Achieving this balance requires strategic planning, effective supplier relationships, and sometimes innovative solutions.
Identifying Cost Reduction Opportunities
The first step in balancing cost and quality is to identify areas where costs can be reduced without impacting the quality of the final product.
This involves a thorough analysis of the current purchasing process.
Look at everything from raw material costs to shipping and handling fees.
Evaluate current suppliers: assess if there might be better options that offer the same or better quality at lower prices.
Consider bulk purchasing: often, buying in larger quantities can lead to significant discounts.
However, be mindful of storage and potential wastage.
Examine energy usage: energy-efficient practices can lead to cost savings, particularly in large manufacturing settings.
Optimize inventory management: ensure that inventory levels match demand, as excess inventory can increase storage costs and wastage.
Cost-Benefit Analysis
Before implementing any cost-saving measures, it’s crucial to conduct a cost-benefit analysis.
Weigh the potential savings against the risks of compromising quality.
This analysis helps in making informed decisions that align with the company’s long-term goals.
Maintaining Quality Standards
While it’s important to reduce costs, maintaining quality standards is non-negotiable.
Ensure robust quality assurance processes are in place.
Develop a clear understanding of what quality means for your products.
This often involves working closely with the production and quality control teams.
Supplier Relationships
Strong relationships with suppliers can significantly affect both cost and quality.
Communicate regularly and openly with your suppliers about cost-saving goals and quality expectations.
Consider forming strategic partnerships where both parties benefit from long-term cooperation.
These relationships can lead to negotiated discounts without sacrificing quality.
Supplier Audits and Performance Reviews
Conduct regular audits and performance reviews of your suppliers.
This practice ensures they meet the agreed-upon quality standards.
If suppliers fail to meet expectations, it’s essential to discuss the issues and work towards improving them.
If improvements aren’t made, consider exploring alternative suppliers.
Innovation and Technology
Innovation can play a vital role in achieving cost reductions while maintaining quality.
Investing in technology can streamline purchasing processes and improve efficiency.
Explore automation: automating repetitive tasks can reduce labor costs and decrease errors.
It allows employees to focus on more strategic tasks.
Implement data analytics: use data to make informed purchasing decisions.
Analytics can identify trends and suggest more cost-effective purchasing strategies.
Lean Manufacturing
Lean manufacturing is a production method focused on reducing waste without sacrificing productivity.
Its principles can be applied to purchasing by eliminating non-value-adding activities.
Identify processes in purchasing that do not contribute to the end value of the product and find ways to streamline them.
Employee Training and Involvement
A well-informed purchasing team is better equipped to manage costs while maintaining quality.
Regular training sessions can keep employees updated on the latest cost-saving strategies and quality assurance techniques.
Encourage involvement: involve your purchasing team in decision-making processes.
They often have valuable insights into where savings can be made without affecting quality.
Monitoring and Evaluation
After implementing cost-saving measures, continuous monitoring and evaluation are crucial.
Regularly assess the impact of changes on both cost and quality.
Maintain flexibility to adjust strategies as needed.
Seek feedback from customers to ensure product quality meets their expectations.
Using Key Performance Indicators (KPIs)
Implement KPIs to measure the success of purchasing strategies.
These might include cost per unit, supplier defect rates, and return rates.
KPIs provide a clear picture of whether the balance between cost reduction and quality maintenance is being maintained effectively.
Conclusion
Balancing cost reduction with quality maintenance is a multifaceted challenge that requires a combination of strategic planning, strong supplier relationships, and innovative approaches.
By understanding areas for cost savings, maintaining strict quality standards, leveraging technology, and continuously evaluating processes, manufacturing purchasing departments can achieve this balance.
Ultimately, the goal is to ensure profitability while delivering products that satisfy customer expectations.
資料ダウンロード
QCD調達購買管理クラウド「newji」は、調達購買部門で必要なQCD管理全てを備えた、現場特化型兼クラウド型の今世紀最高の購買管理システムとなります。
ユーザー登録
調達購買業務の効率化だけでなく、システムを導入することで、コスト削減や製品・資材のステータス可視化のほか、属人化していた購買情報の共有化による内部不正防止や統制にも役立ちます。
NEWJI DX
製造業に特化したデジタルトランスフォーメーション(DX)の実現を目指す請負開発型のコンサルティングサービスです。AI、iPaaS、および先端の技術を駆使して、製造プロセスの効率化、業務効率化、チームワーク強化、コスト削減、品質向上を実現します。このサービスは、製造業の課題を深く理解し、それに対する最適なデジタルソリューションを提供することで、企業が持続的な成長とイノベーションを達成できるようサポートします。
オンライン講座
製造業、主に購買・調達部門にお勤めの方々に向けた情報を配信しております。
新任の方やベテランの方、管理職を対象とした幅広いコンテンツをご用意しております。
お問い合わせ
コストダウンが利益に直結する術だと理解していても、なかなか前に進めることができない状況。そんな時は、newjiのコストダウン自動化機能で大きく利益貢献しよう!
(Β版非公開)