- お役立ち記事
- What is the purchasing department’s crisis response plan to overcome supply chain disruptions?
What is the purchasing department’s crisis response plan to overcome supply chain disruptions?
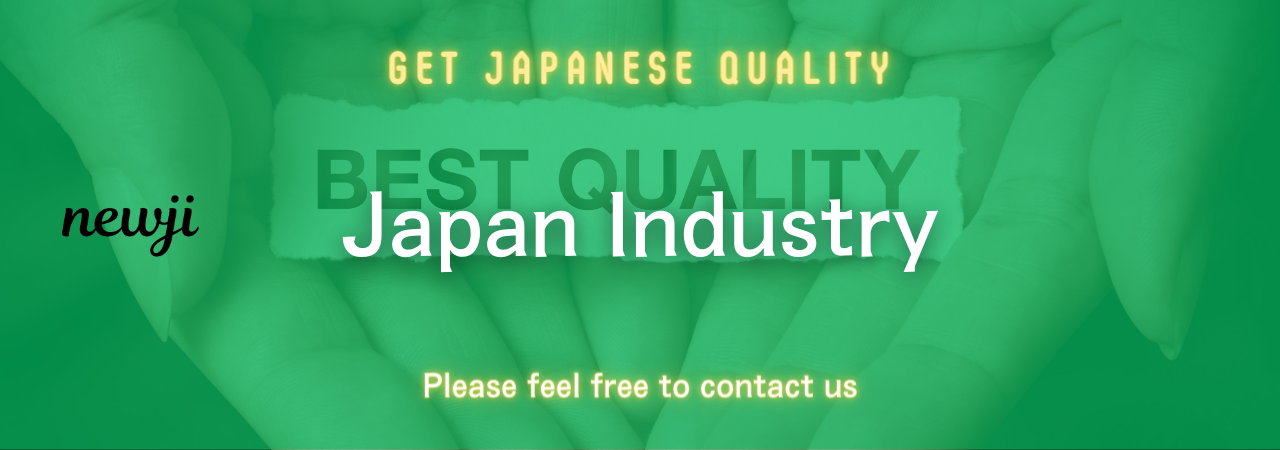
目次
Understanding Supply Chain Disruptions
Supply chain disruptions are unexpected events that interfere with the normal flow of goods and materials within a supply chain.
These disruptions can arise from a variety of sources, including natural disasters, geopolitical tensions, transportation blockages, and even pandemics.
Understanding these factors is crucial for the purchasing department as it plays a significant role in maintaining the continuity and efficiency of supply chains.
A supply chain disruption can lead to delays in production schedules, increased costs, and a decline in customer satisfaction.
To mitigate these potential threats, the purchasing department should have a well-articulated crisis response plan in place.
This plan acts as a roadmap to guide actions during unexpected events, ensuring that risks are minimized and operations return to normal as swiftly as possible.
The Role of the Purchasing Department in Crisis Management
The purchasing department is responsible for procuring goods and services that a company needs to operate.
Its role in crisis management is critical because disruptions can affect the procurement process, thereby hindering the entire supply chain.
Having a proactive approach helps the department respond swiftly to crises and ensure a steady flow of materials.
Creating a comprehensive crisis response plan involves anticipating potential disruptions and establishing protocols to address them.
This includes maintaining strong relationships with suppliers, diversifying the supplier base, and regularly reviewing and updating risk management strategies.
Effective communication, agile decision-making, and strategic thinking are essential qualities for a purchasing department to navigate through a crisis successfully.
Developing a Crisis Response Plan
1. Risk Assessment and Identification
The first step in developing a crisis response plan is to conduct a thorough risk assessment.
This involves identifying possible threats to the supply chain and assessing their potential impact on operations.
Understanding the severity and likelihood of these risks allows the purchasing department to prioritize issues and allocate resources effectively.
Risk identification should include both internal and external factors.
Internal factors might involve production capabilities, technology issues, or workforce challenges, while external factors could include market volatility, supplier reliability, or geopolitical events.
2. Building Supplier Relationships
Strong supplier relationships are fundamental to overcoming supply chain disruptions.
Regular communication with suppliers ensures the purchasing department is aware of any issues that might arise on the supplier’s end.
Establishing contracts with alternative suppliers can provide a safety net if the primary supplier cannot deliver as expected.
Collaborative relationships with suppliers can lead to better visibility into their operations, which helps in identifying early warning signs of potential disruptions.
This proactive approach allows the purchasing department to make informed decisions and negotiate favorable terms during disruptions.
3. Inventory Management
Effective inventory management is essential in minimizing the impact of supply chain disruptions.
By maintaining an optimal level of inventory, the purchasing department can counteract short-term delays without significantly affecting production or delivery schedules.
The use of inventory management software can provide real-time data and forecasts, allowing for better planning and adjustments as needed.
Safety stock levels should be regularly reviewed and adjusted based on the nature and frequency of supply chain disruptions.
4. Communication Strategies
During a crisis, communication becomes even more critical.
The purchasing department must ensure clear and consistent communication with all stakeholders, including suppliers, internal teams, and customers.
Establishing a communication protocol ensures that all parties are kept informed and aligned on the steps being taken to mitigate the disruption.
Regular updates not only help in managing expectations but also build trust and credibility with stakeholders.
In some cases, transparent communication can lead to collaborative solutions that benefit all parties involved.
5. Continuity Planning and Contingency Measures
Business continuity planning involves developing a set of procedures that ensures critical business operations can continue during a crisis.
Contingency measures should include plans for alternative procurement methods, logistics, and resource allocation.
By simulating different disruption scenarios, the purchasing department can test the effectiveness of their crisis response plans and make necessary adjustments.
Having flexible contingency plans in place means the department can swiftly activate these measures as needed, minimizing downtime and maintaining operational integrity.
Technological Solutions in Crisis Responses
In recent years, technological advancements have become integral to managing supply chain disruptions.
Automation, data analytics, and artificial intelligence help the purchasing department to predict potential disruptions and react in a timely manner.
Digital solutions can enhance visibility across the supply chain, providing better insights into supplier performance and potential risks.
Furthermore, implementing technologies like blockchain can improve traceability and security, making the supply chain more resilient to disruptions.
By leveraging technology, the purchasing department can build a more agile and responsive supply chain.
This not only helps in reacting to current disruptions but also prepares the organization for future challenges.
Conclusion
A well-developed crisis response plan is essential for the purchasing department to manage supply chain disruptions effectively.
Through risk assessment, building strong supplier relationships, efficient inventory management, and effective communication, the purchasing department can mitigate risks and maintain operational continuity.
Additionally, embracing technological advancements provides a competitive edge, enabling quicker response times and better decision-making.
As the global business environment continues to evolve, the purchasing department’s ability to adapt and respond to disruptions will play a pivotal role in an organization’s success.
By continuously refining their strategies and processes, purchasing departments can not only overcome current supply chain challenges but also build resilience for the future.
資料ダウンロード
QCD調達購買管理クラウド「newji」は、調達購買部門で必要なQCD管理全てを備えた、現場特化型兼クラウド型の今世紀最高の購買管理システムとなります。
ユーザー登録
調達購買業務の効率化だけでなく、システムを導入することで、コスト削減や製品・資材のステータス可視化のほか、属人化していた購買情報の共有化による内部不正防止や統制にも役立ちます。
NEWJI DX
製造業に特化したデジタルトランスフォーメーション(DX)の実現を目指す請負開発型のコンサルティングサービスです。AI、iPaaS、および先端の技術を駆使して、製造プロセスの効率化、業務効率化、チームワーク強化、コスト削減、品質向上を実現します。このサービスは、製造業の課題を深く理解し、それに対する最適なデジタルソリューションを提供することで、企業が持続的な成長とイノベーションを達成できるようサポートします。
オンライン講座
製造業、主に購買・調達部門にお勤めの方々に向けた情報を配信しております。
新任の方やベテランの方、管理職を対象とした幅広いコンテンツをご用意しております。
お問い合わせ
コストダウンが利益に直結する術だと理解していても、なかなか前に進めることができない状況。そんな時は、newjiのコストダウン自動化機能で大きく利益貢献しよう!
(Β版非公開)