- お役立ち記事
- Mastering FMEA in Japanese Manufacturing: Enhancing Quality and Efficiency
Mastering FMEA in Japanese Manufacturing: Enhancing Quality and Efficiency
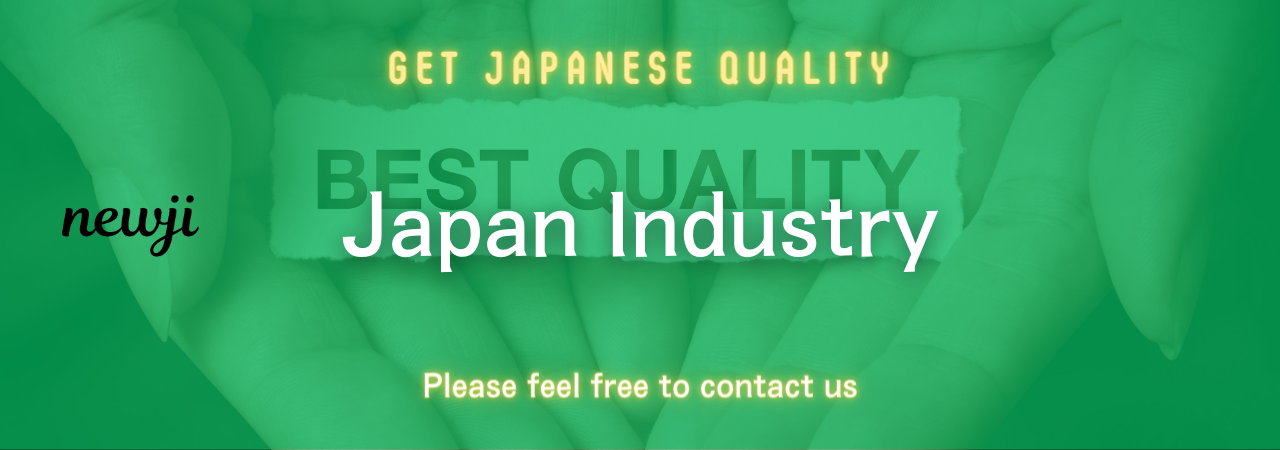
目次
Introduction to FMEA in Japanese Manufacturing
Failure Modes and Effects Analysis (FMEA) is a systematic method for identifying potential failure modes within a system, process, or product and assessing their impact on overall performance. In Japanese manufacturing, FMEA plays a crucial role in ensuring high quality and efficiency. By proactively addressing potential issues, companies can enhance product reliability, reduce costs, and maintain a competitive edge in the global market.
The Importance of FMEA in Enhancing Quality
Quality is a cornerstone of Japanese manufacturing, known for its precision and reliability. FMEA contributes significantly to this reputation by enabling manufacturers to anticipate and mitigate potential defects before they occur.
Proactive Quality Management
Unlike reactive quality control methods, FMEA emphasizes prevention. By analyzing potential failure points during the design and planning stages, manufacturers can implement corrective actions early, reducing the likelihood of defects reaching the customer.
Continuous Improvement
FMEA aligns with the Japanese philosophy of Kaizen, which focuses on continuous improvement. Regularly conducting FMEA allows companies to refine their processes, enhance product quality, and adapt to changing market demands efficiently.
FMEA’s Role in Boosting Manufacturing Efficiency
Efficiency is paramount in manufacturing, impacting production costs, delivery times, and overall profitability. FMEA contributes to efficiency by streamlining processes and minimizing disruptions.
Optimizing Processes
Through FMEA, manufacturers can identify and eliminate inefficiencies in their production processes. By addressing potential bottlenecks and failure points, companies can ensure smoother operations and faster turnaround times.
Reducing Waste
FMEA helps in identifying areas where waste can be minimized, whether it’s material waste, time, or labor. By implementing corrective measures based on FMEA findings, companies can achieve more sustainable and cost-effective production methods.
FMEA in Procurement and Purchasing
Procurement and purchasing are critical functions in manufacturing, directly influencing product quality and cost. FMEA integrates seamlessly into these areas, ensuring that suppliers and materials meet stringent standards.
Supplier Selection and Evaluation
Using FMEA in the supplier selection process allows companies to assess potential risks associated with different suppliers. By evaluating the failure modes of suppliers’ products or processes, manufacturers can choose partners who meet their quality and reliability standards.
Risk Management in Purchasing
FMEA aids in identifying and mitigating risks related to material quality, delivery schedules, and supply chain disruptions. By anticipating potential issues, procurement teams can develop contingency plans, ensuring a steady supply of high-quality materials.
Advantages of Implementing FMEA in Japanese Manufacturing
Adopting FMEA offers numerous benefits that enhance both quality and efficiency in manufacturing operations.
Early Detection of Potential Issues
FMEA facilitates the early identification of potential failures, allowing companies to address them before they escalate into significant problems. This proactive approach reduces downtime and prevents costly recalls or repairs.
Enhanced Communication and Collaboration
FMEA encourages cross-functional collaboration, bringing together teams from different departments to discuss and resolve potential issues. This collaborative environment fosters better understanding and teamwork, leading to more effective problem-solving.
Improved Customer Satisfaction
By ensuring higher quality and more reliable products, FMEA contributes to increased customer satisfaction. Satisfied customers are more likely to become repeat buyers and recommend the company’s products to others, driving business growth.
Disadvantages and Challenges of FMEA
While FMEA offers significant benefits, it also presents certain challenges that companies must address to maximize its effectiveness.
Time-Consuming Process
Conducting a thorough FMEA can be time-consuming, requiring detailed analysis and extensive collaboration. This can be a challenge for companies with tight production schedules or limited resources.
Requires Expertise
Effective FMEA implementation demands a deep understanding of the processes and potential failure modes. Companies may need to invest in training or hire experienced personnel to carry out meaningful analyses.
Potential for Over-Analysis
There’s a risk of over-analyzing every possible failure mode, which can lead to analysis paralysis. Balancing thoroughness with practicality is essential to ensure that FMEA remains a productive tool rather than a bureaucratic hurdle.
Supplier Negotiation Techniques Incorporating FMEA Insights
FMEA provides valuable insights that can enhance supplier negotiations, leading to better terms and stronger partnerships.
Data-Driven Negotiations
Using FMEA data, procurement teams can present concrete evidence of potential risks and the necessity for higher quality standards. This data-driven approach strengthens negotiation positions, enabling companies to secure better terms.
Collaborative Problem-Solving
FMEA fosters a collaborative mindset, encouraging suppliers to work together in identifying and mitigating risks. By presenting FMEA findings as a basis for joint problem-solving, companies can build more cooperative and long-term relationships with their suppliers.
Incentivizing Quality Improvements
FMEA can be used to highlight specific areas where suppliers need to enhance their processes. Companies can negotiate incentives for suppliers who implement these improvements, ensuring that quality standards are met consistently.
Market Conditions Influencing FMEA Implementation
External market factors can significantly impact how FMEA is implemented and prioritized within manufacturing companies.
Competitive Pressure
In highly competitive markets, the demand for high-quality and reliable products is intense. Implementing FMEA helps companies differentiate themselves by ensuring superior product quality, thus gaining a competitive advantage.
Regulatory Requirements
Industries with strict regulatory standards often require robust quality management systems. FMEA helps companies comply with these regulations by systematically identifying and addressing potential failures.
Technological Advancements
As manufacturing technologies advance, new failure modes may emerge. FMEA must evolve accordingly, incorporating the latest technological developments to remain effective in identifying and mitigating risks.
Best Practices for Effective FMEA Implementation
To maximize the benefits of FMEA, companies should adhere to best practices that ensure thorough and effective analyses.
Comprehensive Team Involvement
Involving cross-functional teams in the FMEA process ensures that diverse perspectives are considered. This comprehensive approach leads to a more accurate identification of potential failure modes and their impacts.
Consistent Documentation
Maintaining detailed and consistent documentation of FMEA processes and findings is crucial. This not only facilitates ongoing improvement but also ensures that knowledge is retained and accessible for future reference.
Regular Reviews and Updates
FMEA should not be a one-time activity. Regularly reviewing and updating FMEA analyses ensures that they remain relevant and effective in addressing new challenges and changes in the manufacturing environment.
Integration with Other Quality Tools
FMEA is most effective when integrated with other quality management tools such as Six Sigma, Total Quality Management (TQM), and Lean manufacturing. This integration creates a robust framework for continuous quality improvement.
FMEA and Automation in Japanese Manufacturing
Automation is a key component of modern manufacturing, and FMEA plays a vital role in ensuring that automated processes are reliable and efficient.
Identifying Automation Risks
FMEA helps in identifying potential failure modes associated with automated systems, such as software glitches, mechanical failures, and cybersecurity threats. By addressing these risks proactively, companies can ensure the smooth operation of automated processes.
Enhancing Robot Reliability
In factories where robots and automated machinery are prevalent, FMEA can assess the reliability and performance of these systems. This leads to improved uptime, reduced maintenance costs, and higher overall efficiency.
Integrating FMEA with Industrial Internet of Things (IIoT)
The integration of FMEA with IIoT technologies allows for real-time monitoring and analysis of potential failures. This synergy enhances predictive maintenance capabilities, further boosting manufacturing efficiency and quality.
Case Studies: Successful FMEA Implementation in Japanese Companies
Examining real-world examples of FMEA implementation provides valuable insights into its practical benefits and applications.
Toyota’s Use of FMEA in Quality Management
Toyota, a global leader in manufacturing, has successfully integrated FMEA into its quality management system. By systematically analyzing potential failure modes in its production processes, Toyota has maintained its reputation for producing reliable and high-quality vehicles, consistently meeting customer expectations.
Panasonic’s Supplier Collaboration through FMEA
Panasonic employs FMEA in its supplier selection and evaluation processes. By working closely with suppliers to identify and mitigate potential risks, Panasonic ensures that only reliable and high-quality materials are used in its products, enhancing overall product performance and customer satisfaction.
Canon’s FMEA for Innovation and Efficiency
Canon utilizes FMEA not only for quality control but also to drive innovation and efficiency in its manufacturing processes. By identifying potential areas for improvement, Canon continuously refines its operations, leading to cost savings and enhanced product features.
Training and Developing FMEA Expertise
Effective implementation of FMEA requires skilled personnel who understand both the methodology and the specific manufacturing processes involved.
Comprehensive Training Programs
Developing structured training programs ensures that employees are well-versed in FMEA principles and techniques. Training should cover the basics of FMEA, data analysis, risk assessment, and the use of relevant software tools.
Certification and Continuous Learning
Encouraging employees to obtain certification in FMEA and related quality management systems promotes a high level of expertise within the organization. Continuous learning opportunities keep the team updated on the latest developments and best practices in FMEA.
Practical Application and Mentorship
Providing opportunities for hands-on application of FMEA through real projects and mentorship programs helps employees develop practical skills. Experienced mentors can guide less experienced team members, fostering a culture of knowledge sharing and continuous improvement.
Integrating FMEA with Lean Manufacturing
Lean manufacturing focuses on eliminating waste and optimizing processes, making it a natural complement to FMEA.
Identifying and Eliminating Waste
FMEA assists in pinpointing areas where waste occurs, whether it’s in materials, time, or processes. By addressing these areas, companies can streamline operations and enhance efficiency.
Enhancing Process Reliability
Combining FMEA with Lean principles ensures that processes are not only efficient but also reliable. This dual focus minimizes the risk of disruptions and ensures consistent product quality.
Facilitating Just-In-Time (JIT) Production
FMEA supports JIT production by identifying potential risks that could disrupt the delicate balance of production schedules. By mitigating these risks, companies can maintain the flow of materials and avoid delays in the production process.
Leveraging Technology in FMEA
Advanced technologies can significantly enhance the effectiveness and efficiency of FMEA processes.
FMEA Software Tools
Specialized FMEA software tools streamline the analysis process, enabling more accurate and efficient identification of failure modes. These tools facilitate data collection, risk assessment, and documentation, making the FMEA process more manageable and effective.
Data Analytics and FMEA
Integrating data analytics with FMEA allows for the analysis of large datasets to identify patterns and trends related to potential failures. This data-driven approach enhances the accuracy of FMEA and supports more informed decision-making.
Artificial Intelligence and Machine Learning
AI and machine learning technologies can predict potential failure modes based on historical data and trends. By leveraging these technologies, companies can conduct more proactive and precise FMEA analyses, further enhancing quality and efficiency.
FMEA in the Global Supply Chain
In today’s globalized economy, manufacturing companies often rely on a complex supply chain involving multiple suppliers across different regions. FMEA plays a critical role in managing risks within this intricate network.
Assessing Global Supplier Risks
FMEA helps in evaluating potential risks associated with global suppliers, such as geopolitical instability, variations in quality standards, and logistical challenges. By identifying these risks, companies can develop strategies to mitigate them, ensuring a stable and reliable supply chain.
Enhancing Supply Chain Resilience
Through FMEA, companies can identify vulnerabilities in their supply chain and implement measures to strengthen resilience. This includes diversifying suppliers, establishing buffer stocks, and developing contingency plans for potential disruptions.
Ensuring Consistent Quality Across Borders
FMEA ensures that quality standards are maintained consistently across all suppliers, regardless of their geographical location. By setting clear quality criteria and regularly assessing supplier performance through FMEA, companies can uphold their quality standards globally.
FMEA and Sustainability in Manufacturing
Sustainability is increasingly important in manufacturing, and FMEA can contribute to creating more sustainable practices.
Identifying Environmental Impact Risks
FMEA allows companies to assess the environmental impact of their processes and products. By identifying potential environmental hazards, companies can implement measures to reduce their ecological footprint and comply with environmental regulations.
Promoting Sustainable Materials and Processes
Through FMEA, manufacturers can evaluate the sustainability of materials and processes, choosing options that are both reliable and environmentally friendly. This proactive approach supports long-term sustainability goals and enhances corporate social responsibility.
Enhancing Energy Efficiency
FMEA helps in identifying areas where energy consumption can be reduced without compromising quality or efficiency. By optimizing energy use, companies can lower operational costs and contribute to environmental sustainability.
FMEA in the Product Development Lifecycle
Integrating FMEA into the product development process ensures that quality and reliability are built into products from the outset.
Design Phase Analysis
During the design phase, FMEA identifies potential failure modes related to product design. This allows designers to modify the design to eliminate or mitigate these risks, resulting in more robust and reliable products.
Prototype Testing and Validation
FMEA is used during prototype testing to assess the performance and reliability of new products. By identifying and addressing issues early, companies can refine their prototypes and enhance the final product’s quality.
Post-Launch Evaluation
After product launch, FMEA continues to be valuable for monitoring product performance and identifying any emerging failure modes. This ongoing evaluation supports continuous improvement and helps maintain product reliability over time.
FMEA and Regulatory Compliance
Adhering to regulatory standards is essential in many industries, and FMEA assists in ensuring compliance.
Meeting Industry Standards
FMEA helps companies meet various industry standards by systematically identifying and addressing potential failures. This ensures that products and processes comply with the required regulations, avoiding legal issues and penalties.
Documentation for Audits
FMEA provides comprehensive documentation of risk assessments and mitigation strategies. This documentation is valuable during regulatory audits, demonstrating the company’s commitment to quality and compliance.
Adapting to Regulatory Changes
As regulations evolve, FMEA enables companies to adapt by reassessing and updating their risk management strategies. This proactive approach ensures ongoing compliance with changing standards.
Conclusion
Mastering FMEA in Japanese manufacturing is essential for enhancing quality and efficiency. By systematically identifying and addressing potential failure modes, companies can achieve higher product reliability, optimize processes, and maintain a competitive edge in the global market. Integrating FMEA into procurement, purchasing, supplier negotiations, and various other aspects of the manufacturing process ensures a comprehensive approach to risk management and continuous improvement. Despite its challenges, the benefits of FMEA make it an indispensable tool for manufacturers aiming to excel in quality and efficiency.
資料ダウンロード
QCD調達購買管理クラウド「newji」は、調達購買部門で必要なQCD管理全てを備えた、現場特化型兼クラウド型の今世紀最高の購買管理システムとなります。
ユーザー登録
調達購買業務の効率化だけでなく、システムを導入することで、コスト削減や製品・資材のステータス可視化のほか、属人化していた購買情報の共有化による内部不正防止や統制にも役立ちます。
NEWJI DX
製造業に特化したデジタルトランスフォーメーション(DX)の実現を目指す請負開発型のコンサルティングサービスです。AI、iPaaS、および先端の技術を駆使して、製造プロセスの効率化、業務効率化、チームワーク強化、コスト削減、品質向上を実現します。このサービスは、製造業の課題を深く理解し、それに対する最適なデジタルソリューションを提供することで、企業が持続的な成長とイノベーションを達成できるようサポートします。
オンライン講座
製造業、主に購買・調達部門にお勤めの方々に向けた情報を配信しております。
新任の方やベテランの方、管理職を対象とした幅広いコンテンツをご用意しております。
お問い合わせ
コストダウンが利益に直結する術だと理解していても、なかなか前に進めることができない状況。そんな時は、newjiのコストダウン自動化機能で大きく利益貢献しよう!
(Β版非公開)